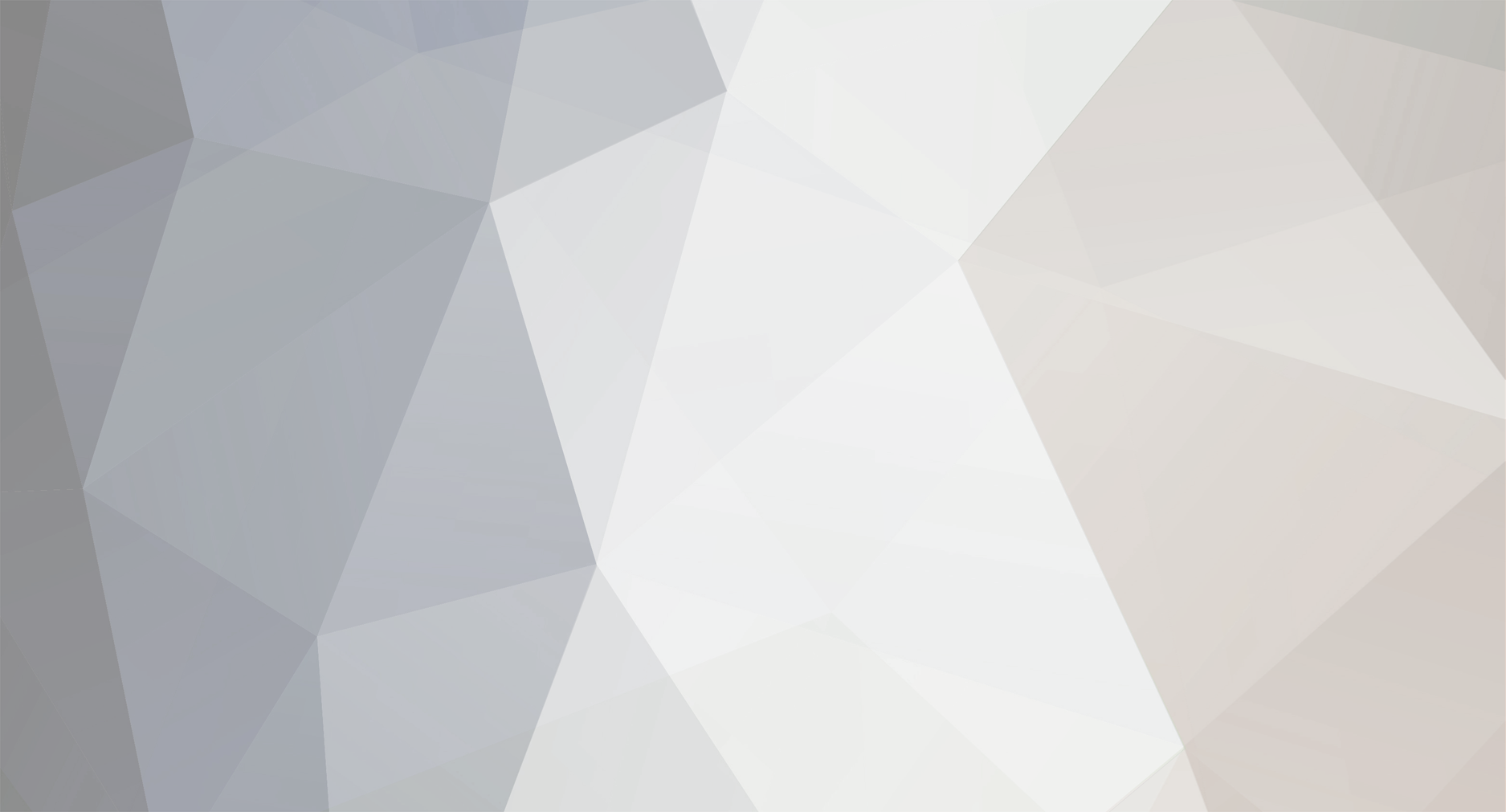
5foot2
Members-
Posts
83 -
Joined
-
Last visited
Content Type
Profiles
Forums
Blogs
Events
Gallery
Downloads
Store
Everything posted by 5foot2
-
I've always felt the 2+2 cars were the red headed step child of the Z world. This car should have been sold before it's expiration date, I'd say some time before 1984. Maybe he'll get lucky and someone is doing a remake of corvette summer and they're looking cars.
-
looks like he welded on the shock tabs so he could add the bitchin air shocks to the car.
-
Anyone watch Pinks Last night ?
5foot2 replied to jnjdragracing's topic in Gen I & II Chevy V8 Tech Board
After seeing the 240sx/mustang show I was left thinking at this point in the pinks game, everyone should know that if you don't show up with a car that is atleast reliable your going to look like a huge boob on national T.V. It was stated at the begining of the show that the guys with the mustang had been at the track for two days working on the car and trying to catch a race on the show. The other thing that gets me is all the untested cars or cars just finished the night before. You must get some notice before your called into race. -
I'd say you came out of that very well. I'm a fire fighter in a small town and the water alone just saturates everything, then you add on the smoke and heat and most people are left with very little to salvage even after a small fire in a single room. A while back we were called to assist at an apartment fire (our town is 99% single family homes). It was an eight unit building, two story with a large open stairway that ran up the middle. In a top floor apartment some knuckle head had setup a small growing opperation in a closet. The lights fell over or overheated (or something) and lit off the bedroom. 20 minutes later the apartment was gutted, the one next door was fully of smoke and very hot. The unit below was like a smokey wading pool.
-
Now there is some dedication, cutting the roof of to get some quality welds.
-
One thing that's nice about welding thick to thin is the ability to linger on the thick material dipping down (or up, sideways, etc) quickly onto the thinner material with a looping motion (or whatever pattern you prefer). I find it easier to control heat this way sometimes. You could also just spot stitch the parts together but I'd do this as the last resort. It's not the best weld.
-
The 2004r is a fine trans when built correctly. It's also a nice trans choice for a Z car swap in that it's a smaller trans than the 700r4 (it fits better). The gear ratio spread is also better in my opinion, with a higher over drive ratio (.68-1 if I remember correctly) allowing for a steper rear end gear ratio (3:90 or 4:10) but reasonable engine RPM at freeway speeds. It's my intention to run one behind a 454 BBC in my Z.
-
Base it all on weight of what your likely to tow. A tractor or small dozer on a 10,000 lbs cap trailer and you should look into a 3/4 or 1 ton. 2500lbs car on the avg car trailer and a light duty 1/2 or full size import truck is suitable.
-
A full size 1/2 ton with a v6 will tow a Z well enough. MPG will be no where close to the Scion, but hey, it's a truck.
-
My LT1 rebuild, the risk of buying a used engine
5foot2 replied to deja's topic in Gen I & II Chevy V8 Tech Board
The lt1 motors run roller cams. -
Need opinions from our resident welding experts!
5foot2 replied to Z-Dreamer's topic in Fabrication / Welding
I own a Henrob. It's a great setup. I mostly used it for fine cutting and welding thin steel sheet. I gave alum a try with it and never got the hang of it. I have a tig and mig machine that do most of the welding in the shop so the Henrob is not used much anymore. It does do really clean fine cuts on material, but I'm going to be ordering a plasma cutter soon, so that's one more thing the Henrob will not be doing much anymore. The O/A rig is mostly just used as a heat source in my shop. -
Another vote for the Remington 700. Even the entry level 700's have an action like butter.
-
Now let be honest everyone. The second you viewed the side shots of the finished sculpture, you were wondering about the money shot. I'm just the only one that's willing to admit he spent some time searching for the pictures. Being the father of two, and having been forced to witness the train wreck.... er miracle of child birth. This is pretty tame.
-
because I think it's important to look at every side of an issue, I offer this....... http://cache.gawker.com/images/2006/04/20060406britcrowning.jpg
-
Had some fun today welding, but had a little problem...
5foot2 replied to CruxGNZ's topic in Fabrication / Welding
1/4" is beyond your WP100's practical limit. The welds may look sounds but penetration well not be all that deep. Are these welds structural? -
If it's a real race car, I'd say go solid rear, a four link and a spool. You might also check with the sanctioning body. Some don't allow welded diffs.
-
If by cast your talking about cast aluminum, I'd not recommend it. I have the SP 175+ Lincoln and it's a fine machine, but not well suited to aluminum work. It's at the bottom end of the heat range for aluminum mig work with a practical thickness limit of 3/16", in a perfect world. The other problem (the biggest I think) is feeding wire. The common feed wire I've found is 5356 and 4043. The latter works really nice with many types of aluminum but is as soft as butter in .30 so feeding it through the push feed of the small Lincolns is a huge headache, even with the aluminum liner and rollers. The 5356 feeds much better, but I was not able to produce a quaility weld with my machine and this wire. If you need to mig a lot of aluminum, I'd recommend starting with a 210 amp machine and a spool gun. My solution, since I do little aluminum work, was to get a Lincoln PT185 tig machine.
-
My breif perspective on union shops. I worked on the Kenworth assembly line in south Seattle in the early 90's. It of course was a union shop. I worked towards the start of the line installing air lines and sub systems for the brakes. some of the trucks required a threaded stud to be spot welded in a few places to secure various clams and gromets for the air lines. Every now and then I would forget to weld on the stud and the next station on the line would notice. Instead of the guys at the next station simply welding on a stud, fastening the clamp then throwing a nut at me and telling me to stop missing the studs, I had to gather a portable stud gun and run up to the next station and do the work. I had to do this because the people standing 50 feet away from me were in a different union than I was and it was not thier job. They had no interest in building a truck, they simply wanted to attach part A to part B and not have to think or deviate from the norm. Working there and at a few other union job in my early 20's soured me on unions. The basic ideas of a union is a good one (collective barganing, worker protection, insurance, pentions, etc, etc), but I've found they are counter productive to getting work done, they promote lazyness with the seniority systems, they make the shop a hostile place to work with all the tention between the union and managemnet, and the top level union management is far from seeming on the up and up. They're just as bad as corp. management or politicians. All that said, filing for protection through a bankruptcy is a good thing for the company and the workers. It keeps the place in business.
-
So on3go, if you opt to go with a IFS and an open drive shaft rear diff let me know. I'd be interested in the parts that come off the Ford. It seems to me "Rat Rod" has become it's own type of car, mostly a hack job that just barley runs and is very questionable when it comes to safety. Eight or ten years ago the cars that carried the rat rod label were mostly cars in progress being driven, on the way to looking nice, not the **** being hacked together today. But I guess that's the way it works when something gets a label. It's a race to the lowest common denominator.
-
rat rod....... the most over used term of the last 5 years. I think the 41-42 cars are in the same family as the 46-48 years. The latter years have a nicer front end imho. These Fords look great with a 3-4 inch chop if your at all thinking of that route. Be careful just cutting off the roof, it just doesn't look right on some cars. Sometime the diffs between the convertable and the coupe are pretty significant making the conversion tough. If you don't know about them, look into Carson tops. Basically they're removable hard tops. They look sweet. I'm collecting parts for a '30 Model A tub. I'm trying for a '55-'62 period hotrod, so I've picked up an old offy tri power intake and a bunch of rochester 2g carbs, an early 60's 283, most of the A front end part, '53 f100 front brakes, etc. This summer I'll be prowling the swap meets for sheet metal. Should be fun. I have a buildable L24 and I've thought it would look nice in an open early style hotrod. In fact I have a cowl and roof off a very rusty 240 I picked up for parts and I was thinking of maybe using that sheet metal as the basis for a custom bodied rod. Using the L24. I assume you know about the HAMB? http://www.jalopyjournal.com.
-
Right, 8k for a motor is not the norm, and laying it out like that kind of makes you sound like an *******. Hell I just build a 40x38 shop, maybe I'll start making fun of people bolting together their stuff in a one car garage. I also just picked up a nice tig welder. All you fools using mig or O/A are stupid and should really step up to the better welding proccess. High dollar parts are nice, but plenty of people can make good long lasting power with much less cash.
-
wacky swap: 240z parts on a 280 chassis
5foot2 replied to zeiss150's topic in Brakes, Wheels, Suspension and Chassis
I'm going with the 240 front and rear bumpers, front valance and turn signals, but the stock tail lights on a 77 280. the 240/early260 is a much cleaner looking car IMHO. As for the dash, I'd only goto the trouble if I had a perfect 240 dash. You'd have to swap the dash and center console, plus the likely changes in heater vents, electrical, etc. -
evenly spaced tacks all along the seam, space the tacks out and move around along the seam. the goal is to minimize localized heat. by tack I mean just enough heat to melt the spot in front of your gun with full penetration. do not leave an open seam. weld it all, it will take some time. when you dress down the weld seam use a light touch. Flap disks in a 4.5" grinder work well. you can get them in grits from 36 to 120. if your not careful, the grinder will warp the panel just as badly as the welding.
-
Did you get that 275 from Sears? About a year ago on this or another forum someone posted a super, super deal on the 275. It was a close out deal through Sears. I waited half a day to run the purchase past the wife before I spent the $$, and missed out. The extra heat of the 275 would be nice once in a while, but I think I'll be happy with the 185. Between my Lincoln sp175+ mig and thie pt185 tig, I feel I have all my bases covered.
-
tabco makes replacement rockers. if it's rotted there it's likely rotted elsewhere. get a weak fridge magnet and a screw driver and start poking around. use the magnet in areas that are prone to rust and place it on the body. if it's loaded with bondo the magnet will not stick. any paint bubbles should be probbed with the pick/screw driver any rot you find will need to be cut out and replaced with raw sheet metal formed to fit or replacement panels from tabco or another supplier.