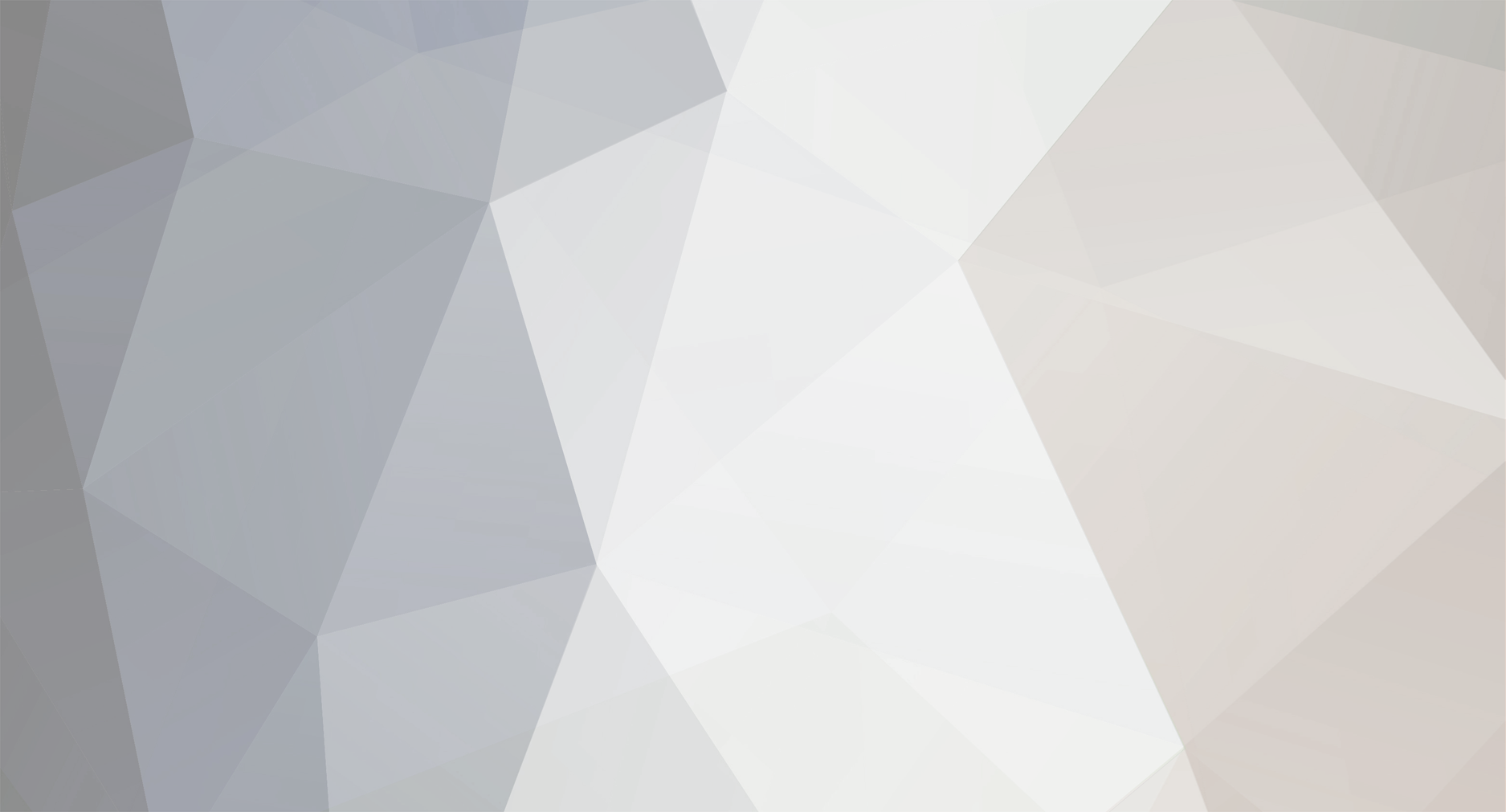
boodlefoof
Members-
Posts
401 -
Joined
-
Last visited
-
Days Won
1
Content Type
Profiles
Forums
Blogs
Events
Gallery
Downloads
Store
Everything posted by boodlefoof
-
I vote for the 'Vette as well, with the Viper as a close second, then the 911.
-
spaceframe 240-Z update
boodlefoof replied to boodlefoof's topic in Brakes, Wheels, Suspension and Chassis
Hey guys, thanks for the words of encouragement. I will certainly keep updates coming as I make progress. I may be a little slower for the next three weeks or so though... I'm taking the bar exam at the end of July so I'll be cramming. However, after the exam I get all of August off before starting my job. I hope to have the front suspension mounted and possibly have the body attached to the frame by the end of September. We'll see if the funds allow purchasing a rear end to stick under there by that time... it may have to wait. As to using the solid axle rear several factors influenced the decision. First, I do plan to have this car run the 1/4 mile on occassion and I wanted more anti-squat than I could feasibly get with the IRS. In addition to that, the solid axle should be better suited for that application for the reasons jmortensen and shift pointed out. Second, the solid axle was simpler to design and will be less expensive to construct. I do plan to take the car to some open road events, and on smooth surfaces there shouldn't really be any appreciable disadvantage over an IRS setup. It will also save quite a bit of frame weight to mount as opposed to the IRS. Shift, nice looking pics! I ended up doing something similar with the wooden braces to locate the frame. As for cutting off the entire firewall, I had to. I've actually moved the firewall back about 8'' and will move back the engine and trans assembly to match. I'm shooting for close to, if not better than, a 50/50 weight distribution. It will make the passenger compartment a little cramped, but this is going to be primarily a race car... and I'm only 5' 10''. In fact, when the body is attached to the new frame... the only part of the original body that will remain (not replaced by fiberglass) will be the roof, the windshield channel and the rear hatch and the doors. Everything else will be fiberglass attached to the frame. As for the front suspension, I've already purchased a complete front suspension assembly from a 2004 Corvette. I managed to snag it for a good price from a 'Vette wrecking yard. I will not be reusing the suspension cradle or the fiberglass monoleaf spring, but will use the control arms, steering rack, spindles, hubs, brakes, and will give the sway bar a try and see if it is adequate. I have only changed the C5 suspension mounting points slightly for less anti-dive (stock is 57%!) and for more consistent caster (less change) during bump. Anybody know if they make delrin bushings for the C5? I've looked and can't find any. I will be using coil-over shocks. Again, I will keep you guys posted as the project progresses. = ) -
spaceframe 240-Z update
boodlefoof replied to boodlefoof's topic in Brakes, Wheels, Suspension and Chassis
OK, put some pics up on the website real quick... hope you can get them. Remember, it isn't done... more bracing to be added as well as the cage. http://www.geocities.com/boodlefoof/Project_Racer-Zframe -
Hey guys! (Sorry this is really long, but hopefully a fun read - pics attached). I've been posting about building this spaceframe chassis for awhile now. Well, I finally had some time over the past two weeks to start the build. Before I began building, I spent quite awhile trying to finalize my suspension design so that I could model the spaceframe around it. To help in this respect, I first did some reading and then began mapping coordinates on the Suspension Analyzer software. It is harder than it seems... I spent quite awhile trying to create an unequal length A-arm front suspension that would maintain a stable roll center laterally. It was pretty tricky. Finally, I serindipitously discovered that my overall car width would be equal to that of a C5 'Vette. So, I decided to use the C5 dimensions as a baseline on the front suspension. For the rear suspension, I will be going with a Satchell link solid axle suspension. After getting the suspension points roughed out, I had to design the frame... Since I had my main dimensions, I first began looking at what other spaceframes looked like. I then began to tinker with a freeware programe called GRAPE and put down the coordinates. When all was said and done I came up with a design that would fit my modified Z body (pretty well anyway) and that would put the suspension where it needed to be, all while maintaining a fair amount of torsional rigidity. As per Herb Adams' suggestions, I kept the concept of load paths in mind when designing. When all is said and done, I anticipate having a chassis with well over 10,000 pounds per degree of deflection. It should weigh around 300 pounds with the full roll cage. So, on to the build... I first ordered some steel tubing from a local metal supply house. I ended up ordering lengths of 2x3x.083, 2x2x.095, 2x2x.065 and some 1.5x1.5x.065. Round tubing will be ordered later to complete the cage. The rockers will use the 2x3 tubing, while most of the other main rails are 2x2x.095. The diagonal reinforcement pieces are mostly 2x2x.065 and the 1.5x1.5 will be used solely to construct the trans tunnel and to support the rear of the body behind the rear axle. Then, I purchased a large 4x8' piece of 3/4'' plywood and marked it with a grid to help keep measurements in line. I tried my best to level the plywood as well since the garage floor has about a 2* slope to it. When I laid the tubing down on the plywood I screwed down pieces of wood around each piece to keep them from moving while welding. I then proceeded to cut... first I cut off the front of the car (forward of the windshield). Then I began cutting pieces of tubing and welding the front snout together! I made sure to tack each side of each connection prior to finishing the welds. I did this to try and minimize any deflection due to heat. The front snout began with the front firewall piece (a rectangle). I then attached the lower frame rails (which attach the lower control arms) and subsequently the upper frame rails (for the upper arms). Once the front snout was completed (aside from some supporting cross sections) I began the rear piece. This was much easier because I decided to go with a solid axle. All the rear needed was the rear firewall and the rails which will mount the anti-roll bar and shocks. It will eventually be further reinforced with a cross brace and will tie into the roll cage overhead. After getting the basics of both the front and rear snouts created, I then proceeded to bridge them with the 2x3 tubing and some 2x2 cross braces. I've attached some pics of the progress below. I haven't had a chance to update my website with a writeup of the progress though. So, attached are a few pictures of the progress too far. I hope they work... I'm not super techno-savvy. Awww nuts!... it says my pictures are too big (around 170KB). I know the thread is worthless without pics! I'll try to get them on my website (which has limited data transfer) and post a follow up, or if somebody knows how to help me out let me know via PM and I'll try to put them up sometime soon. Anyway, happy 4th all!
-
If you go to http://www.corner-carvers.com and perform a search for "grape chassis" you will find some information. In one of the few threads is a link to the program download site as well.
-
lexan windows.. thickness recs and where to purchase?
boodlefoof replied to JaysZ's topic in Fabrication / Welding
Summit Racing sells sheets of some stuff called "Speedglass" that is Lexan supposedly covered with a clear coating of some sort that helps with scratch resistance. That's what I plan to use for my windows. If you want more info on Speedglass, you can google it. The company that makes the stuff is called "Percy's" if I remember right. -
I like 'em!
-
Hey olderthanme, Well, I've been tinkering with it, but time is kind of limited... I'm studying for the bar exam this summer. I'm hoping to break out the chop saw again later this week though. My next step is to cut off the front tub (from the windshield forward) and build the front frame snout. Then I'll cut out the rest of the floor and build the rear and center sections. Will post updates as they come.
-
Yup, that sounds exactly like what I am doing. Thanks for putting up my link Z-tard. I'm not sure yet whether I'm going to rivit or use an adhesive to bond the fiberglass pieces on. Now that I've got the rough dimensions on the fenders, I'm taking a break from bodywork to start work on the space frame and suspension. Then I'll be able to finalize the mounting points for the fiberglass pieces.
-
That's awful...
-
I'm not familiar with Autodesk Inventor, but for others interested in designing a spaceframe and custom suspension, I'm using a freeware program called GRAPE for the suspension and Suspension Analyzer from Performance Trends for the suspension. I'm just about ready to start building the spaceframe! My steel tubing just came in yesterday.
-
Ditto Z-tard's method. Floral foam works great.
-
I have done what you're talking about. Except that I first built up the fenders with some floral foam to make flares. First recommendation... don't lay the fiberglass directly over the metal. It will stick pretty tightly. First, take some duct tape and cover the metal, then lay the glass over that. The tape will peel off the metal more easily than the glass would. Less risk of cracking your new piece. As for what kind of fiberglass to use, using multiple layers will build strength. I used two layers of 7.5 oz. cloth and then topped it off with two layers of 4 oz. cloth. The finer the weave (smaller weight), the less chance that the cloth will "print through" after you paint it. This made a part that is very rigid. Go slowly and use a stiff bristle brush to blot in the resin, trying your best to keep any bubbles out of the cloth. The more bubbles, the more sanding and filling you will have to do. I have to credit Terry (BlueOvalZ) for the tips and tricks I learned about doing this sort of thing. Thanks again! Good luck!
-
Rockland Standard has been putting together durable gearboxes for a long time. They have an excellent reputation.
-
You moving out of Fredericksburg Mike, or just moving into another place locally? If you're interested in moving down closer to Richmond, the property prices down there seem pretty low. My folks just moved down there a few years ago and got a very nice house for very little (relatively speaking).
-
I'm a big fan of black/silver two-tone. I plan to paint my car silver with a black center stripe (or double stripe).
-
mechanical engineers - how would I calculate this? (((long thread)))
boodlefoof replied to 260ZRED's topic in Non Tech Board
I'm not an ME, nor an expert but something strikes me about your engine swap proposition. I may be completely wrong, but it is food for thought. If you're putting in a smaller turbocharged engine into the pickup, and you will be putting a lot of load on the engine (from towing), you're constantly (or very often) going to be in a positive boost scenario. The smaller engine and increased load is also going to require that you give the car much more throttle than an engine with more displacement and torque. Now, at highway speeds perhaps this won't be the case and you will get increased fuel economy. But, in stop and go traffic, it seems like you would probably get worse fuel economy than, say, putting in a larger V6, cammed to make most of its torque down low. If you consider the throttle position and vacuum as your analogs to fuel consumption, it appears that the smaller engine may be detrimental. -
Thanks guys. Haven't had the chance to look too much into the glass. Hopefully I'll have some updates on the project this summer.
-
There are some cars running it, but I think they're mostly fleet ordered vehicles (local gas company's cars are all run on LPG, etc). I've never seen them marketed to commuters... only for farm vehicles and things like that.
-
Yeah, ethanol is higher octane. Problem I've heard with respect to just popping it in your gas tank is the corrosion issue. It eats up rubber lines and such more quickly. Not sure if the E-85 they're selling now alleviates this problem somehow. Another thing to consider is that ethanol will not give you the same mileage per gallon as gasoline. I recall reading a few years back that it will give you about 70-80% the mileage of gas... so a 30mpg gasoline-engined car will be turning 24 on ethanol.
-
Can't wait until my '73 is driveable... right now it is just a shell. It is so nice to get back into an old car after some time off. I went about 6 months without driving my '68 Camaro and once I got back in the driver's seat... it just put a big smile on my face.
-
Hey icesky, Haven't had a chance to work on the car in awhile. Currently finishing up law school, but I hope to get back into it this summer. After doing a little more fiberglass body work, I'm going to finalize my suspension and spaceframe design and start welding up the frame. Then, I'll cut out the floor, firewall, etc and drop the modified body on to the frame. Really hoping to get most of the way through that by the end of the summer. I'll post updates here and on my website when I can.
-
This sound like a good deal for a SBC?
boodlefoof replied to Mycarispurty's topic in Gen I & II Chevy V8 Tech Board
Ahhh the Edelbrock Scorpion intake. Haven't heard that one mentioned in a long time. Was the hot ticket awhile back. I still do think the Vortecs are probably a better deal than most of the older factory castings though. Aside from the flow numbers, the combustion chamber design is better than the older designs, allowing more compression and timing on the same gas. The L98 heads don't flow all that well. I have the flow numbers here from a magazine some time ago... Vortec numbers are from the same magazine. They are as follows. lift/intake/exhaust .100/56/52 .200/120/104 .300/160/133 .400/186/150 .500/196/170 .600/199/175 As opposed to the Vortec L31 heads. lift/intake/exhaust .100/70/49 .200/139/113 .300/190/142 .400/227/159 .500/239/170 .600/241/172 -
You probably don't want to run a continuous bead at all on such thin metal with a MIG. You will warp it. Also, blow through is a problem as you've described. For such thin metal, you would probably be better served to lay a series of spot welds and small (less than 1'' long) beads. It can be done... I've welded 24ga. with my 175 amp welder with no trouble using this method. Just a little time consuming. If you must run a bead, lay a copper backing plate behind it. The copper will act as a heat sink, and your welding wire won't stick to it.