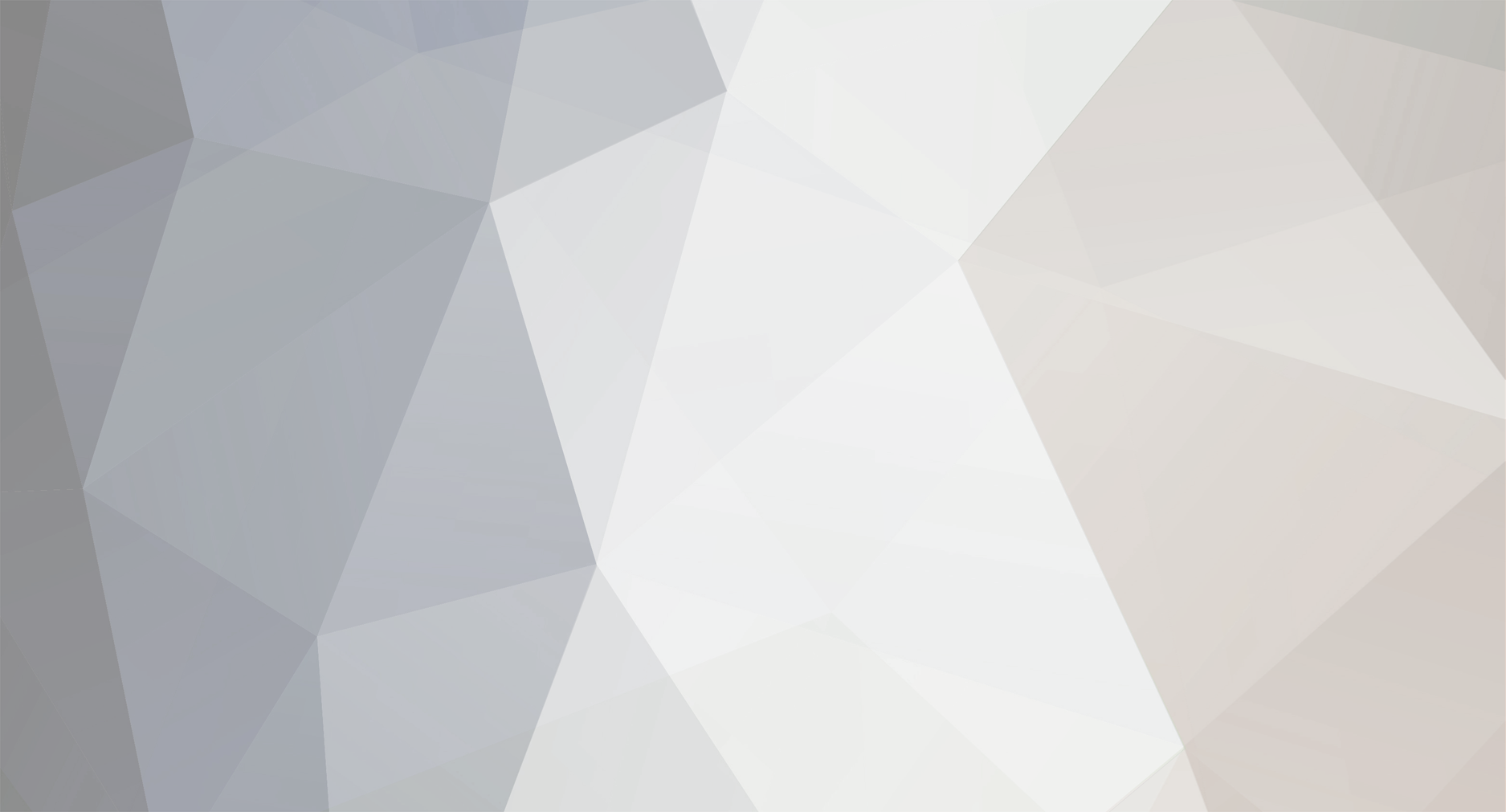
boodlefoof
Members-
Posts
401 -
Joined
-
Last visited
-
Days Won
1
Content Type
Profiles
Forums
Blogs
Events
Gallery
Downloads
Store
Everything posted by boodlefoof
-
Looks like a really good foundation! Congrats on the purchase and welcome aboard!
-
spaceframe 240-Z update
boodlefoof replied to boodlefoof's topic in Brakes, Wheels, Suspension and Chassis
It does look like a good article... although much of the math is over my head. They also seem to spend very little time on some of the more important topics in my opinion. For example, I'm kind of surprised that out of 153 pages, they only spend about a page and a half on roll center and roll axis. The tire and spring tech sections are pretty useful though! Again, I highly recommend getting Chassis Engineering if you don't already have it. It covers almost all of the same information as in the .pdf, but does so in a brief and easy to understand way. At any place that Chassis Engineering isn't in-depth enough, take a look at Milliken's books "Race Car Vehicle Dynamics" and "Chassis Design: Principles and Dynamics." Very good references. -
spaceframe 240-Z update
boodlefoof replied to boodlefoof's topic in Brakes, Wheels, Suspension and Chassis
I would recommend Herb Adams' book, Chassis Engineering. There are others out there as well that discuss frame design, but this one is very straight forward. For the most part though, I just looked at what others were doing when building spaceframes and began designing by integrating some of their ideas. I looked at kit car frames, circle track frames... everything I could find. I modeled some on the computer and I discovered that some frames are just horribly over-engineered with lots of useless weight. By running various iterations of the frame, I came to one that I thought was the best compromise of weight and torsional rigidity. Here are a couple of links I found useful. The first link shows a Mustang, the owner of which was very helpful in answering some of my questions regarding computer modeling though he is a very busy man. http://www.carter-engineering.com/preston67compcoupe.htm http://www.beardmorebros.co.uk/website%20pages/new_project.htm http://www.grabercars.com/Mambosite/index.php http://www.kimini.com/ -
13" rotors and Outlaw 4000 calipers
boodlefoof replied to blueovalz's topic in Brakes, Wheels, Suspension and Chassis
Lookin' good Terry! I'll be using C5 front brakes on mine as well. -
Can I use this for shaving bodywork???
boodlefoof replied to jacob300zx's topic in Fabrication / Welding
Jake, If you're going to use this for bodywork, I recommend getting some strips of copper plate to hold behind the sheetmetal you are working on. When held against the back of the sheetmetal, the copper will act as a heat sink, helping to reduce blow-through. Also, your welding wire shouldn't stick to it. -
spaceframe 240-Z update
boodlefoof replied to boodlefoof's topic in Brakes, Wheels, Suspension and Chassis
Yeah, I really need to start paying for a site so I have higher data transfer capacity... -
The Mustang uses kind of the inverse design, yes. The upper arms are the angled arms, but they converge at the axle housing rather than at the frame. This gives less axle support in lateral motion. Having the upper arms angled also results in a roll center height above the axle centerline. By angling the lower arms, your roll center height will be below the axle centerline. By having the arms connect at the ends of the axle and point in towards the center of the frame, you get better lateral support. Yeah, the lower arms are doing double duty as both the lateral location device and helping control axle windup tendencies. On accelleration the lower links will actually be in compression (pushing on the frame). I haven't built it yet, but the lower frame mounts will tie into the structural transmission tunnel for added strength. I should have mentioned that before... without extra bracing those mounts do look a little flimsy!
-
Have you seen this Japan 240z taking off? FAST,
boodlefoof replied to big-phil's topic in Non Tech Board
I believe the sound you're hearing is the sound from the transmission. That is what a sequential shift transmission with straight cut gears sounds like. It is music to my ears personally. -
Here are some pictures of the Satchell link for those who are interested... http://www.geocities.com/boodlefoof/Project_Racer-Zsuspension6.html
-
spaceframe 240-Z update
boodlefoof replied to boodlefoof's topic in Brakes, Wheels, Suspension and Chassis
Another update... rear suspension is basically built! Pics and a writeup are on my website beginning at: http://www.geocities.com/boodlefoof/Project_Racer-Zsuspension4.html -
My thoughts on uerethane bushings:
boodlefoof replied to veritech-z's topic in Brakes, Wheels, Suspension and Chassis
Always the best time to work on the car. -
My thoughts on uerethane bushings:
boodlefoof replied to veritech-z's topic in Brakes, Wheels, Suspension and Chassis
When I bought poly bushings for my '68 Camaro, they came with "white lithium grease." -
Thinking about building a custom go cart...
boodlefoof replied to 280zwitha383's topic in Non Tech Board
I built a go-kart once with a mower engine like you're describing. I actually ended up using some parts from a roto-tiller to make it work. The roto-tiller bellhousing bolts to the bottom of the engine... crank attaches to a friction disk clutch. When you release the lever on the roto-tiller, the clutch engages the other friction disk on the roto tiller... it had a driveshaft that then went straight down into a differential with a pair of axles. So, the engine sits right over the drive wheels. Only problem I had was that the gear ratio in the roto-tiller was insanely low (probably around 10:1). So, I put some taller tires on the thing to try and compensate. Even so,... it probably couldn't get up over 15 mph. -
PICS: Custom rollcage fabrication/install
boodlefoof replied to mull's topic in Brakes, Wheels, Suspension and Chassis
bjhines, I've been contemplating this problem as well. You could try to recess the A-pillar/window rail bar into the existing body. Cut a channel out of the A-pillar and window rail and move the bar into it as far as possible... might pick you up 3/4''? Only problem is that you probably don't want to mess up the window lip for your weatherstripping. -
My thoughts on uerethane bushings:
boodlefoof replied to veritech-z's topic in Brakes, Wheels, Suspension and Chassis
I agree on the lube. The higher amount of friction between the bushing and bushing housing due to the poly bushings will reduce the suspension's ability to rotate freely around that mount point. If the suspension can't move freely, a bump in the road is transferred to the chassis rather than absorbed by the spring and shock. -
Q about control arm design (non Z related)
boodlefoof replied to J__'s topic in Brakes, Wheels, Suspension and Chassis
It sounds like you're talking about an unequal length A-arm setup, and that the car uses an independent rear suspension as well, is that right? If so, there is no real "best" length for the control arms... jmortensen is right that you typically should make the lowers as long as you can fit. The upper arms should usually be slightly shorter (around 2/3 the length of the lowers) to get the best results. Your friend should really invest in a computer modeling program before cutting and welding anything. I used Suspension Analyzer from Performance Trends to model my suspension (front and rear). They actually have a free 10 day demo you can use to try it out. The demo allows full functionality. With an unequal length A-arm setup, there are a lot of variables you want to keep in mind... and sometimes getting them all within the acceptable range simultaneously isn't easy. You will want to at least: - maintain a low roll center height (RCH) - minimize lateral movement of the roll center in roll - design the RCH to move up and down relatively the same amount as the car body in bump and lift to keep your roll axis constant - keep the swing arm length acceptable (not too short) - build in anti-dive/anti-squat appropriate to the car's weight, spring rate and wheelbase - consider how bumpsteer will be affected by your control arm design - consider the caster appropriate for the car's purpose - consider the camber curve appropriate for the car's purpose Really, you should design from your steering knuckle/hub inward. Once you have the wheel/tire/knuckle combo set, you will know what your A-arm mounting points are at the knuckle. From there, work back to where your frame mounts should be. What kind of kit is this? Most kits I've seen have a suspension setup already designed to sell with the car. -
Hah! Nifty bar stools!
-
Drag/Track Car Cage
boodlefoof replied to JustinOlson's topic in Brakes, Wheels, Suspension and Chassis
Justin, If I remember correctly, the NHRA .118'' requirement requires that all parts of all tubes meet this wall thickness. When you begin bending the tubing (particularly the tight bends at the roof), the outer edge of the bend will stretch and become thinner. Most people use .134'' tubing to maintain a .118'' minimum wall thickness all around. -
PICS: Custom rollcage fabrication/install
boodlefoof replied to mull's topic in Brakes, Wheels, Suspension and Chassis
That guy in the link should probably be wearing more eye protection than just sun glasses while he is welding... -
Isn't it nice to work with a bare frame? Looks good!
-
Getting closer... I got the rear axle housing in yesterday and fabricated all of the frame mounts for the trailing arms. Today, I fab up the axle mounts!
-
Lason, Regarding trailing arm length, you have the option of moving the axle mount rearwards (actually behind the axle) to make your links longer. This gives you the same benefits of having your frame link mount further forward. So, for example a link that is 18'' long that connects to the axle directly above the axle centerline and 18'' ahead of the axle CL (assuming a link with no slope) will act the same as a link that connects to the axle 3'' behind the axle CL and only 15'' forward of the axle. Another option (which probably won't work without using big fender flares and moving the wheels outboard slightly) is to run the links outboard of the seats. To accommodate my links, I'm actually going to run my upper links outboard of the passengers... so basically my upper links' upper mounts will be next to me while I sit in the car. With my frame design, I could theoretically acommodate as long as 60'' upper links... but that is a little absurd. I've been modeling hundreds of iterations of my rear suspension design on the computer to try and optimize it. For anyone attempting to design a suspension from scratch, I would suggest downloading the free demo (10 days free with complete function) of Suspension Analyzer from Performance Trends (google will find it). Plug in your coordinates and it will spit out all the outputs you can think of and show you how they react in bump and roll.
-
I live in Northern Virginia and I've never seen one of those either. Most of what I see around here are the black rat snakes and a little medium green colored guy every once in awhile.
-
I really like the looks of that one Veritech-Z! Almost makes me want to get a Miata just to re-body it!
-
Amen to that! I see it all the time as well.