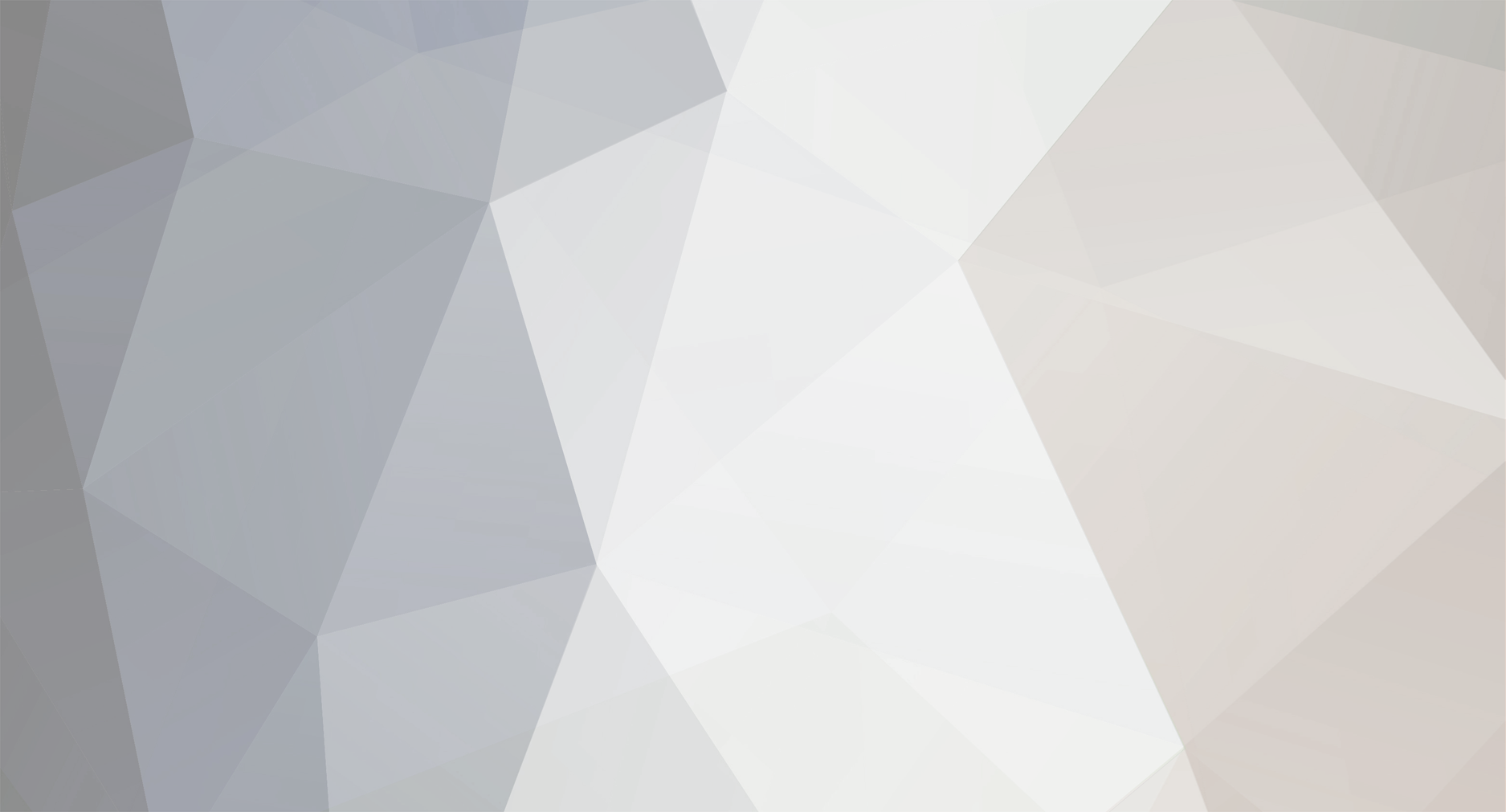
SH4DY
Members-
Posts
136 -
Joined
-
Last visited
-
Days Won
5
SH4DY last won the day on June 17 2019
SH4DY had the most liked content!
Profile Information
-
Gender
Male
-
Location
Richmond, VA
Recent Profile Visitors
3553 profile views
SH4DY's Achievements
-
Funny, I actually just got an '08 Explorer diff heading my way courtesy of ebay. I need to reach out to DSS about a custom set of axles and see what that damage is compared to the Apex kit. Does your car not squat? I'm stock fenders and with 245 dr2 Hoosiers you can see where they touch, presumably on the launch. That was with the stock cxracing springs though (240lb). I've got 500lb springs in there now but never got back to the track to try them.
-
The 8.8 IRS may not be cost prohibitive if I fabbed everything up on my own, but I'd still be limited by the IRS suspension geometry and wheel/ tire size. Also, it's not the strength of the R200 that I'm concerned about. There are cars using them going way faster than I am. If I went with an SLA I could easily fit the 275/60r15 drag radial I want to run in the stock wheel wells. Right now I'm limited to a 245 (currently running a 245/45r17 Hoosier DR2). I'm also not talking about a production 9" - I'd be looking at a Currie/ Moser 3rd member and possibly a Tin Soldier or Moser housing. After axles, that's close to the TechnoToys 8.8 swap cost (~$6k) but can handle 2,500+hp. Another alternative is finding someone to make a custom ring and pinion? I'm sure that won't be cheap though. Or find an old Kameari gear set? I'll look into the 8.8 IRS some more. Maybe if I can find someone to buy my current setup I could offset the cost.
-
I currently have a 3.7 R200 with an MFactory LSD, WHP 300M stub and CV axles. On motor, the car made 465rwhp and trapped 128mph in the 1/4 which was about 6k rpms in 4th and was pretty much ideal. Well, that was almost 300hp ago. I twin turbo'ed it and now it makes 745rwhp (at only 7psi - plenty of room to grow) which should get it to trap in the mid 140's. With the current gearing, that would require a shift to 5th since I don't wind to wind this motor out more than 6,500. So here are my dilemmas: The 3.36 Ring and pinion for the long lose R200 seems to be unobtainium at this point and the 3.54 isn't enough to get the mph I need in 4th. WHP has closed up shop so even though these axles are rated for 800hp, if I break them, I have no recourse. The R200 pinion flange only has M8 bolts (this is a T56 car so there is a lot of driveline shock). So what do I do now? There's 3 options as I see it: Leave everything as-is and just lift before the end of the 1/4, and hope the axles and diff stay together. Buy a sequential shifter and shift to 5th, and hope the axles and diff stay together. Sell all of the IRS stuff and go with a proper SLA (4 link, Ford 9").
-
LS1 street cam recommendations
SH4DY replied to nick-james's topic in Gen III & IV Chevy V8Z Tech Board
If you want lots of bottom/ mid-range power, avoid a lot of overlap. The tighter the LSA the more "chop" you'll get at idle which will give a novice tuner fits. Upgraded springs are required for pretty much every cam out there and you'll also want to upgrade to LS7 (Delphi) lifters and you will need a custom tune. Summit actually has some good budget friendly LS cams (I think they hired someone that worked for Comp to design them). -
I can vouch for Chip and the MFactory unit. My car makes ~450rwtq and this unit has had no issues handling it, even on drag radials. No one wheel peels here or dealing with clunking/ popping from a welded diff.
-
Looking for Ring and pinion for a longnose R200 with either a 3.08 or 3.36 ratio. Thanks PM me if you have something for sale
-
I know there are some Z's putting up some crazy fast times but I wanted to share my results from my first drag racing event with the Z this weekend at Street Car Takeover at Virginia Motorsports Car. The build list is pretty extensive: but the short of it is: LS1 based 383 w/ ITB's makes ~465rwhp, GTO T56, WHP CV axles and stubs, factory long nose R200 with Mfactory Helical LSD, Hoosier DR2 245/45R17, CX racing coilovers. First pass (ever in this car) it went 11.6 @ 124. I launched around 3k slipping the clutch and shifted pretty easily. The car had also gotten really hot in the staging lanes and wasn't super happy. Let the car cool down for a good hour or so and got back in the lanes. Second pass netted a 11.4 @ 126 with no changes to the car. Actually slipped the clutch harder and it slowed down the to 60' (1.9 vs 1.8). Loaded the car up after that to look over logs (forgot my laptop) and get it ready for the race the next day. Logs showed it was a little rich (ethanol content was slightly down) and videos showed the car squatting a lot on the launch and shifts. I added a full turn of preload to the rear springs and went from 10 to 3 click from full hard on the dampening. Left the fronts at 16 out of 32 on the dampening. Only pass I got to make on race day was during eliminations and I brought a spit ball to a gun fight - I got gaptized by an AWD k-swapped civic. Anyway, I couldn't be happier with the way the car ran. I launched around 4k barely slipping the clutch and netted the following: A couple pictures of the car: (Yes - I hand laid the carbon fiber for the stack and the air boxes) Not sure where to go with the car from here. I think the 10.8 was one of those moments when all the stars aligned - I'd be lucky to get it to 60' like that ever again. It has a weld in 4 point roll bar right now but if I put any kind of power adder on there, she'll need more cage for sure. She weighed in at 2,935 lbs with me in it which is ~200lbs heavier than I was expecting (I'm 170lbs), but makes sense considering the gauge metal I used when replacing the floors/ tunnel, adding the tubular frame rails, roll bar, etc. Don't really want to hack it up at this point though. This is the last time I'll get to race it this year but the wheels are definitely turning about what to do this off season.
-
Just a few more pictures of the defrost vent and the fuse box situation. The defroster works really well - needed it on Saturday going to Cars and Coffee (temps in the 40's in the morning). The center console is also installed (finally have cup holders again!!) but it's going to need some massaging and maybe some extra padding under the carpet in some spots to make it look like it really belongs in there.
-
Little more complete picture. For the heater/ defrost I'm using a Vintage Air unit (gen II heater). You can see in the picture the aluminum piece where the dash meets the window gasket. I used the little ducts that come with the heater and notched the dash for them to fit, then secured them to the trim piece and drilled some holes. The ducts are pretty small - maybe a 6" opening, .5" wide or so. Fuse panel is now mounted behind the glove box and I'm still working on getting the center console installed (had to cut out the factory mounting points for it to sit flush with the tunnel). I also tore down and cleaned up the factory turn and headlight switches and they seem to be working fine. I'll get some more pictures but overall, I'm really pleased with it. Looks a lot better than what I had in there and the gauge visibility is significantly better.
-
Inspired by @clocker thread, and a $50 dash I found on Craigslist, I decided to try and tackle the NB ('98-'05) Miata dash and center console swap. Width size, it's pretty much perfect although as he points out, if the dash is centered in the car, the gauge cluster winds up being right of center. Not the end of the world though. I also had to trim the back of the dash to fit the contour of the Z firewall. Maybe .5" or in the center and closer to 1"-1.5" at the ends. Even the center console fits almost perfectly. After I was happy with where the dash was, I then modified the Miata dash support to mount to the factory Z pick up points. That involved a good bit of cutting and then adding mounting points to the ends and the plate that gets sandwiched by the steering column like the factory dash. I had Speedhut gauges already that were sized for the Z dash but unfortunately the Miata cluster is very small and wouldn't accommodate them. So, I fashioned and mounted an aluminum plate in the hood. The speedo is going to wind up going in the center of the dash a la Mini Cooper - because speedometers are just a distraction on the track. (Gauges are centered with the steering wheel) Currently I'm working on a panel for the rear of the dash to cover the defroster ducts (and some boogered cuts I made cutting the dash). (It'll be painted black) Eventually the lower portions will be painted black and the entire thing will be flocked.
-
Advice on radiator and fan for LS3 swap
SH4DY replied to 280Z-LS3's topic in Gen III & IV Chevy V8Z Tech Board
Fan is off and it's that cold. Has nothing to do with the fan. Stopping the coolant from flowing through the heater core via the heater controls seems to keep it in the 160-170 range which I'm OK with. -
Advice on radiator and fan for LS3 swap
SH4DY replied to 280Z-LS3's topic in Gen III & IV Chevy V8Z Tech Board
You guys are missing what I'm saying - the cooling system is cooling too well. It's getting too cold. I'm not worried about the temps during stop and go traffic - I'm more concerned about the coolant temps not getting above 150 on a cool night. -
Advice on radiator and fan for LS3 swap
SH4DY replied to 280Z-LS3's topic in Gen III & IV Chevy V8Z Tech Board
Standard practice for the last few LS swaps I've done to help maximize cooling with less than ideal radiator setups. When not using a heater core (more full race oriented), the absence of the additional coolant volume becomes apparent pretty quickly at low speeds. Drilling holes is the step between a stock t-stat or just running a disc to slightly restrict the flow. This setup has an unshrouded fan. 5/8" coolant hoses to a Vintage Air heater/defrost unit. Originally I just had the t-stat housing looped but adding the heater core dropped coolant temps 10-15 degrees when sitting in traffic (blower motor off). Inside the car is a sauna, but the motor is happier. -
99-02 LS plastic fuel tank install
SH4DY replied to ukcats07's topic in Gen III & IV Chevy V8Z Tech Board
...again though, all of that goes out the window (the venturi primarily) when running an aftermarket pump/ external fuel pressure regulator (which most people run when doing swaps) because the internal regulator gets bypassed. On a stock F-body, sure, I'm sure it works great. But we are flipping the tank 180 degrees making fuel more prone to move away from the basket and in my case (or anyone with a different pump and external FPR) modifying the basket. Feel free to keep it all stock, I'm just telling you that with high power/ high grip, you're going to have issues unless you modify it. This is from real-world experience. -
99-02 LS plastic fuel tank install
SH4DY replied to ukcats07's topic in Gen III & IV Chevy V8Z Tech Board
You are right in that the pump sits in an enclosure but it's not a sealed "bucket" - there are passages to let fuel in from the bottom and unfortunately if running one of the bigger Walbro units, there is trimming needed that can do away with the check valve (its just a small rubber flap) so fuel can drain from the bottom if not submerged. You could probably seal it if you wanted but then you'd be only relying on the return fuel to fill it. Not ideal on a thirsty motor depending on the racing you're doing. There's always the option of running a surge tank as well. Also, my issues with the level dropping weren't even cornering - just straight line acceleration.