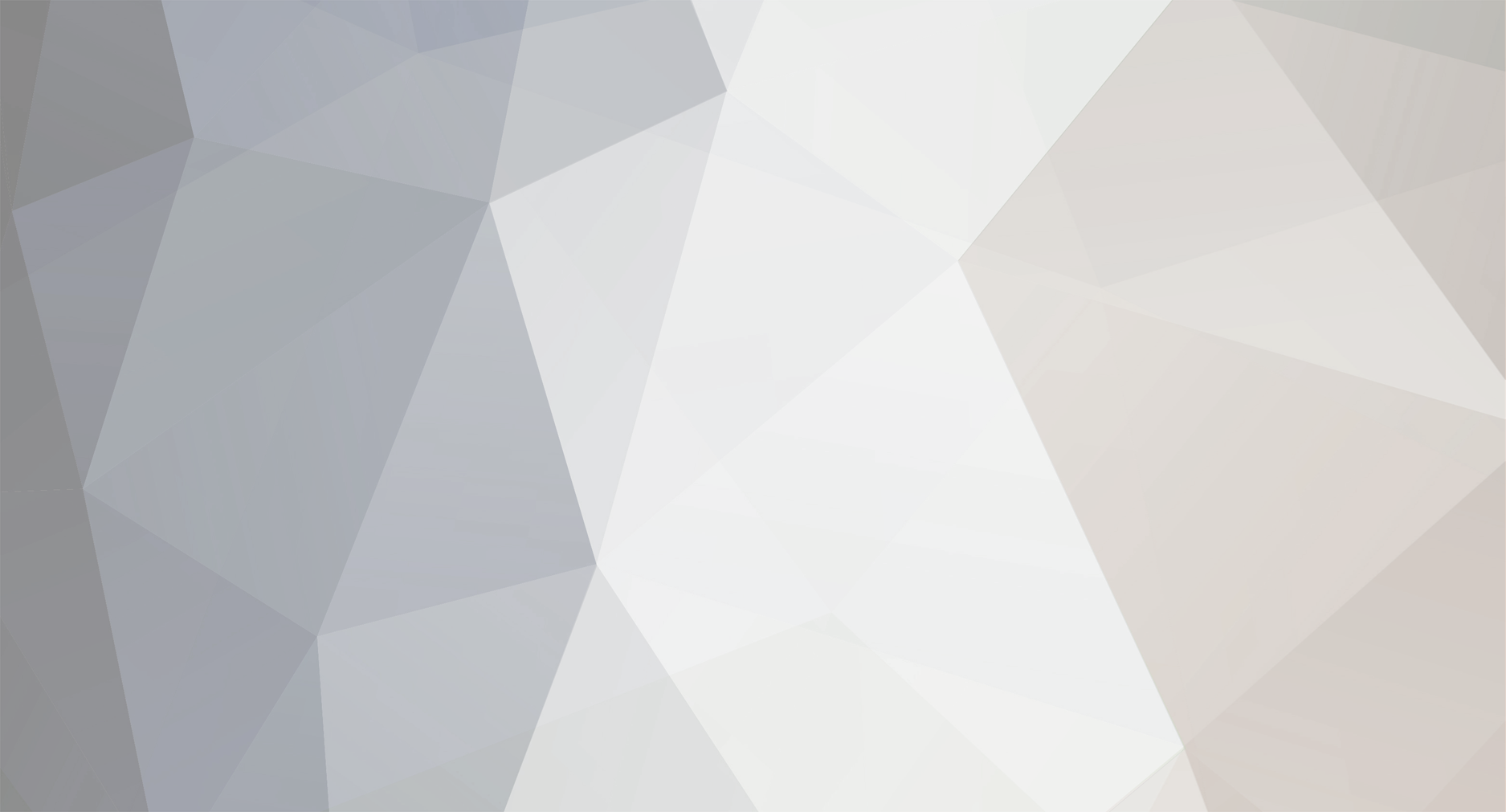
rsicard
Members-
Posts
889 -
Joined
-
Last visited
Content Type
Profiles
Forums
Blogs
Events
Gallery
Downloads
Store
Everything posted by rsicard
-
Mikelly: What type T56 main shaft was put on order? Ford, Dodge, GM etc.
-
Mikelly: What are the Aston Martin/Cobra bits in the T56 transmission?
-
KEITH: Should be able to find a dual left and right kickouts oil pan with 6 trap doors and integral crank scraper welded to the side of the pan versus mounting same to oil pan rail. I purchased one for my SBC for less that $100.00. Also using a big block oil pump on this small block engine. Plenty of oil flow. Also adding a pressure sensor switch to report and record pressure on my EFI system besides and alarm light. I will likely go with the electric switch and warning light for accusump kickin. Won't leave anything to human factors distractions.
-
Kudos to New-Zed. That was a VERY CLEAR explanation concerning converter stall speeds!
-
Eric JB: It appears that some of the posts were LOST when Hybridz.org went DOWN. Perhaps I did not see it before, but your statement stuck out: "...I just went with the steering wheel". That came as an unknown to me as to what THAT switch is for. With the clutch line lock engaged and the clutch pedal pushed in, it seems that the clutch pedal needs to be released, to launch, and to cause the clutch hydraulic line pressure to bleed through the valve and somewhat soften clutch engage. Once that has happened, the clutch line-lock switch can be released for shifting into the next gear. Does that sound like what is happening?
-
Eric JB: Just guessing, once the clutch pedal is let up on launch, is the clutch line lock switch held engaged and the fluid from the slave flows through the bleed clutch engage softening adjustable valve back to the clutch master cylinder in the allowable one way direction. The adjustable valve will not allow flow from clutch master cylinder to the slave but will in the other direction with the clutch line lock engaged blocking flow through the line lock? Maybe I have figured it out?? Once out of first gear, let the clutch line lock switch relax to the not-engaged position. I talk it that switch is momentary action type push to close and actuate line lock?
-
Eric JB: Thanks very much for your response. I am trying to visualize in my head what is happening to the clutch fluid along with the sequence of clutch pedal all the way in, all the way out, the one-way valve and its orientation in regard to the master and slave cylinders also with regard to the line lock valve etc etc. Trying to understand the mechanics, hydraulics and sequence of events in usage of the system.
-
Eric JB: You have spurred a lot of thought from your post. Thanks much for the part number. Already have one on order. Please post an explanation of the sequence of using the system at the drag strip. Start at neutral on the transmission. Push in to disengage the clutch. Select first gear, which toggles the switch to engage the electric shutoff valve in the hydraulic clutch line. " Push the shifter forward (first gear), mat (mash) the (gas) pedal and let it go (of what? the clutch pedal?)". Don't know what is next in the sequence nor what is exactly happening or supposed to happen.
-
Thanks for this post as it is extremely valuable. Could you please share the McMaster Carr part number for the bypass valve. Thanks.
-
I agree with NewZed. Allowing the control arm structure to buckle and shorten under certain conditions of assembly and usage is not a good design. As for the other design, I contend that it is better to sacrifice a little articulation than a lot of strength. If I am to change the rear LCA's, it will be the TTT/MM type design.
-
Hawks Third Gen Swap Parts
rsicard replied to str8pipez's topic in Gen III & IV Chevy V8Z Tech Board
Looks like the crank damper may clear the steering rack. The original location of the steering shaft appears to be blocked by the drivers side headers. -
Same question, are they from Chequered Flag or MM. I have the latter and would like to know also. Don't want my axles to SNAP.
-
Controlling ls2 coil with ground signal?
rsicard replied to nimeton's topic in Ignition and Electrical
Further to this discussion, after having looked at the AEM EMS install manual, the AEM ignition coils have (3) three terminals as likely opposed to (2) two terminals for the GM ignition coils. The AEM coils have the high current driver embedded within the coil package and the driver is fed with a +5 vdc pulse to fire the individual coils as timed by the AEM EMS computer. Therefore the GM coils cannot be used as a replacement for the AEM coils. Maybe this is what you are after. -
Controlling ls2 coil with ground signal?
rsicard replied to nimeton's topic in Ignition and Electrical
The description about the AEM EMS is rather VAGUE. The EMS system likely applies a ground to the ignition coils to fire each. Don't know what you are trying to accomplish. What are you trying to TRIGGER? If you are talking about the Crankshaft sensor, it needs input from a variable reluctance (VR or “mag”) or hall-effect (+5 to +12 vdc signal) sensor. Don't know which coils are being talked about. -
280Z Body Harness (Mod OEM or Painless)
rsicard replied to xellos65's topic in Ignition and Electrical
Unlikely that a guide for wiring will be found. To use the original body harness, download the wiring diagram. Then get someone that is familiar with electrical/electronics to identify and mark the loose ends of the body harness in the engine compartment and instrument panel areas. Then have that person form an interface wiring diagram between the two new and old areas of body harness. Then it is a matter of interfacing the old and new wiring with splices. The headlight harness should be modified to add relays for the heavy current to be controlled by the headlight stalk. -
Pushbutton ignition/toggle switches
rsicard replied to Dudeboy's topic in Gen III & IV Chevy V8Z Tech Board
Dudeboy, if using Option 2, the "F" terminal on the alternator should be at 12-14 volts when the alternator is operational. When the alternator is not charging, terminal "F" should be near the same electrical potential as the negative side of the battery. With the charge light in the circuit, it will be lit as one side should have 12-14 volts (supplied through a small amperage fuse) and terminal "F" will essentially be at battery negative. When the alternator is CHARGING, the charge light will have 12-14 volts on both sides of the lamp having the same electrical potential on both sides of the lamp there will be no current flow through the lamp and thus will NOT be LIT. -
Pushbutton ignition/toggle switches
rsicard replied to Dudeboy's topic in Gen III & IV Chevy V8Z Tech Board
On the subject of the Alternator, two fuse are needed for it. One is a 20 amp for the field excitation from the ignition switch post along with the LSx PCM pink wire. The other needs to be 100 amp inline with the alternator heavy post output to the battery or battery connection at the starter your choice. Have a LOT of experience in wiring Aircraft and Cars. -
Pushbutton ignition/toggle switches
rsicard replied to Dudeboy's topic in Gen III & IV Chevy V8Z Tech Board
The red guarded toggle switch is for ignition on and off. The brown wire must go from the heavy post on the starter up to the ignition switch and also jumpers to the push button start switch. The other side of the ignition switch likely goes to the pink wire on the LSx harness. The other side of the push button switch goes to the solenoid on the starter. The yellow wires connect to the opposite side of the ignition toggle switch where the pink wire is connected to. When the ignition switch is thrown to the on position, it supplies power to the LSx PCM and also to the other two switches on the panel. There needs to be an inline fuse, near the starter, (40 amp) on the smaller wire, going back to the switch panel, connected to the large starter post. The fuse protects the small wire coming from the starter going to the switch panel and also the accessories. There is one hell of a lot of energy at the heavy post on the starter. Should the small wire short to frame or body, the small wire without a fuse could cause a FIRE. -
If the fuse is the appropriate value, it sounds as though all coils are being powered all at one time and blowing the fuse. The hot side of the coil wiring should be connected to the fuse output. The megasquirt output to the coils should be a MOMENTARY ground to fire one coil at a time.
-
l98 tpi vs lt1 swap in 280zx
rsicard replied to 280zxSheik's topic in Gen I & II Chevy V8 Tech Board
The L98 TPI might be the better choice. The real difficulties will be the TPI and 280ZX wiring and the interfacing of these. The mechanical stuff is pretty much a no-brainer. The TPI EFI ECM will need a harness to operate. The 4L60 from the V6 F-bodies may be on the WEAK side. If you want to be done by the end of summer, you better REALLY HUSTLE or not start at all. -
SBC reverse rotation coolant line help
rsicard replied to Grog's topic in Gen I & II Chevy V8 Tech Board
The Small Block Chevrolet engine has the least cooling of the rear (#7 & #8 cylinders) with the least water flow. For most effective heating of the heater core, highly recommend taking hot water from the front of the intake manifold nearest the thermostat housing. For summer operation, a 1/4 turn ball type valve can be installed in this hot water line. In the summer just turn the ball valve closed and this keeps the heater core COOL allowing use of fan operated venting of the cabin. Also very effective for Air Conditioning purposes. -
SBC reverse rotation coolant line help
rsicard replied to Grog's topic in Gen I & II Chevy V8 Tech Board
The front nipple by the thermostat is the hot water out to the heater core. For a cooler water return from the heater core, install a "T", with a 5/8" or 3/4" stub, into the lower radiator hose for the cooler water return that will get sucked into the water pump which then goes onto the block and cylinder heads for engine cooling. Jags that Run has these "Ts" for sale. See their Internet Site.