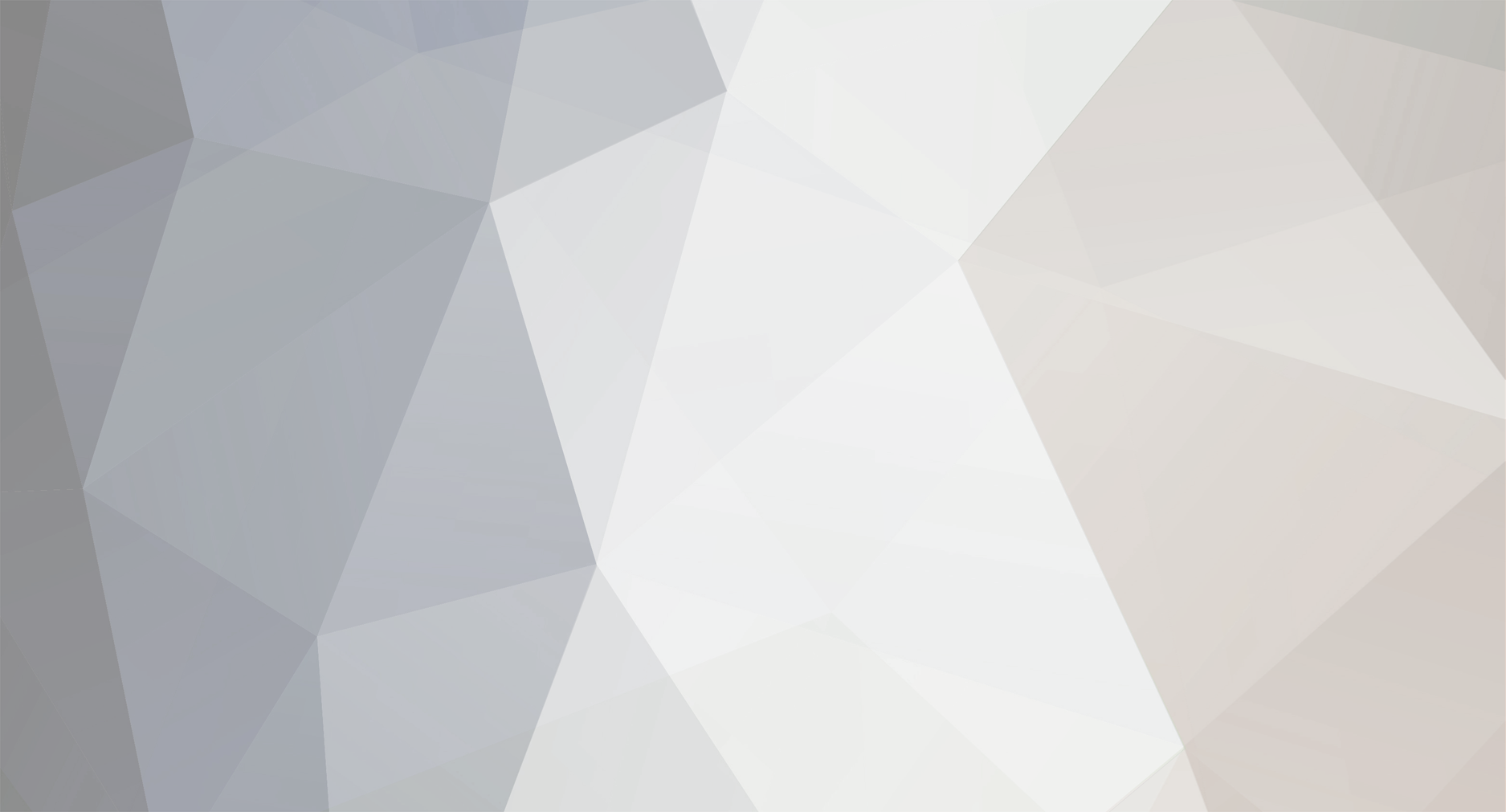
WizardBlack
Donating Members-
Posts
1444 -
Joined
-
Last visited
-
Days Won
2
Content Type
Profiles
Forums
Blogs
Events
Gallery
Downloads
Store
Everything posted by WizardBlack
-
ES Bushing problem???
WizardBlack replied to WizardBlack's topic in Brakes, Wheels, Suspension and Chassis
Well, as I said, Subaru does the exact same thing. It is metal to metal pivoting which is how most of the factory bushings are. Metal on metal is gonna last better than metal on poly I should think. Bugger, I guess I will reinstall them. I used POR15 on all my suspension pieces and some got down in the locking pin holes. It's a real SOB to get it out. -
The best? Hmm... since they are unsprung rotational mass how about these: http://www.racebolts.com/Titanium-Hex-Flange-Bolts-M5-C11.aspx Mark
-
ES Bushing problem???
WizardBlack replied to WizardBlack's topic in Brakes, Wheels, Suspension and Chassis
Another update... I just put the outer bushings on and had to do the same thing to all four (on each side) for them as well. I found that one of those little metal polishing disks that are about 2" in diameter and have the little quarter turn twist-lok type deal (they look like scotch brite) works very well for a fairly non-accurate method of getting them honed down right. I did all four instead of just the middle two to make sure I don't end up with the same problem. Also, I looked at the rear clamshell mount; the sheet metal one. It is indeed angled rearward to accomodate the additional length of the pivoting axis due to the bushings. Also, my stock bushings (which were almost 100% intact) are very clearly designed NOT to spin in the clamshell as they aren't round. They have 'ears' on them that stick in to the little crevice on each side of the mating surface on the clamshells. On a critical side note; do I REALLY need to install new spindle pin locking pins? Why not just leave them to spin; it only makes for a freer moving suspension. Subaru does the same thing (no locking pin). -
Lifting an Inside Front Wheel
WizardBlack replied to johnc's topic in Brakes, Wheels, Suspension and Chassis
Yep, Subies are cool but they still get eaten up by EVO's. Owned both and tracked both. That is, until they break. LOL. BACK on track: Isn't a wheel lift a sign of slightly too soft suspension for the compound and the specific track? Mark -
front and rearend for sale.
WizardBlack replied to stony's topic in Brakes, Wheels, Suspension and Chassis
Very beautiful car; sorry to see you having to backtrack a bit. BTW, who is tuning your F-CON V PRO? Or did you somehow hijack the software? -
Strengthening Front Anti Sway Bar Mounts
WizardBlack replied to 260DET's topic in Brakes, Wheels, Suspension and Chassis
It can't disappear as heat. Work or energy can turn into heat (different form of energy) but a force cannot. The original measuring method was the correct one. If you have X lbs of force on one end of the bar, you have the exact same thing on the other end assuming the bar is free to pivot with respect to the chassis (which your test replicates of course). OTOH, you can consider that your 100 lbs/in. correlates to 100 pounds of force per inch of total bar travel and not just the travel of one side. So, it depends on what exactly you are defining as your swaybar 'rate'. That may be where your intuition is trying to tell you it should be doubled. It will take 100 to 160 pounds of force to get EACH SIDE of the rear sway bar to move 1 inch for example; or two inches of total travel. I am sure you get what I'm saying. EDIT: VERY cool thread by the way. Thanks for posting updated info. Perhaps some completed pics of the frame braces and swaybar mounting? Half the pics in the thread went into the internet black hole. Mark -
ES Bushing problem???
WizardBlack replied to WizardBlack's topic in Brakes, Wheels, Suspension and Chassis
What did you shave them with to get an accurate cut? I am looking at this problem next... -
ES Bushing problem???
WizardBlack replied to WizardBlack's topic in Brakes, Wheels, Suspension and Chassis
UPDATE: I measured them and they show precisely what they said they should be. I reassembled everything; this time sanding the clamshells on the chassis that hold the bushings to make sure they are smooth. I also lubed the outside better now that I know they are going to have to be a moving surface. They move quite a bit better and no longer squeak, but they will still (barely) stay up in the air. I think they'll be fine. I looked at the parts again and I think my description was in error. To better (and more correctly) describe the situation. We have the following pieces from outer to inner: 1. clamshell on the chassis that holds it together 2. poly bushing provided by ES 3. metal sleeve provided by ES 4. tube on the LCA that has internal threads 5. LCA bolts (those big bolts on the front and rear of the inner pivot axis) Before, I thought that the total installed length of the poly bushing (#2) was longer than the sleeve (#3) that was supplied with it. This would cause it to mushroom a bit when bolted down and essentially rub very hard on the LCA because the compression of the LCA bolts would act through the poly bushing to the surface of the LCA. In actuality, the sleeves are longer than the poly like they should be; or at least they are now. Regardless that doesn't seem to be the problem. Upon looking at it very carefully, it seems that the tubes that the bolts thread through (#4) are TOO SHORT. As I understand it (or at least by intuition and experience with other cars), the LCA bolt (#5) should screw in and the head of the bolt should bottom out on the tube (#4). That way, none of the compression of the big bolts are acting through the poly bushing or it's metal sleeve (3 and 2). Additionally, the bushing components will therefore stay stationary with the chassis and the LCA tube and LCA bolts will pivot with the suspension and nothing else would. The LCA tube versus the bushing sleeve would be the wearing point as it is metal to metal and can be lubed by antiseize, etc. The way it works as it is (with the LCA tubes being too short) the LCA bolts bottom out on the bushing sleeve which then bottoms out on the LCA. Since the sleeves are very tight in the poly bushing, when the LCA pivots, the LCA bolts pivot with it (as it should), but the poly and sleeve do as well! The entire assembly essentially moves as one. The wear point is the outer diameter of the poly bushing versus the clamshell on the chassis. I think this is a poor design. Polyurethane was NEVER designed to be a moving/rubbing part. It isn't that hard to design the length of the LCA tubes so that the flange of the bolt head bottoms out on them just before it snugs up the poly/sleeve bushing. This would leave the bushing sleeve's ID as the wear point with the LCA tube inside of them; much like the LCA outer bushings versus the hub with the spindle pins pivoting in the metal sleeves. I think some of the problem may be ES's since they have the "flange" on all their bushings for "thrust" support which the original parts weren't designed to do IIRC. This adds effective length to the total bushing system and causes part of the problem. The LCA tubes are no longer the correct length to span the increased length of each bushing system. Maybe the ES bushings need the flanges shaved down or removed altogether like the above poster did with the outer LCA? You'd have to shorten the metal sleeves the proper amount as well of course. The only way that ES got away with this (if this is the case) is because the rear mounting point (clamshell) is mounted to a flimsy vertical sheet metal bracket that is about 10" tall and therefore it can bend away from the front clamshell (which acts as the front diff mount as well) to increase the total length from the rear of the rear bushing to the front of the front bushing. Any thoughts on this? Am I nuts? Should we cut/trim/machine to get this right or leave it as is? Maybe the speed shops could comment again on this. What would you do if you had an aftermarket moustache bar and all that? No more bending with that to allow it to accomodate the increased length... -
Wow, no doubt. I haven't heard of that before but that one sounded like a horrible experience.
-
ES Bushing problem???
WizardBlack replied to WizardBlack's topic in Brakes, Wheels, Suspension and Chassis
What was wrong with the moustache bar bushings? Mine seemed like the pin that is mounted to the chassis could wobble inside the bushing a bit. The massive washers that go above and below the poly had holes that allowed for a lot of slop, too. -
ES Bushing problem???
WizardBlack replied to WizardBlack's topic in Brakes, Wheels, Suspension and Chassis
Bugger. Where I am going to get such a precise and odd OD and ID sleeve? Should they essentially be the same length as the two halves of the poly bushings? UPDATE: ES has been really cool to give me precise specs on the sleeves so I can measure them (which I am doing right now). They did say there is a tad bit of compression ( 0.030" initial load that lessens over a few weeks). I went and measured the bushings and they fall into spec. If anyone else needs to measure theirs, they are thus: Inner front bushing: 2.450" +/- 0.010" Inner rear bushing: 2.065" +/- 0.010" Outer bushings: 1.830" +/- 0.010" They also noted that these are designed to pivot on both the outer and the inner surface of the poly bushings. I dunno, I guess it could've been done otherwise (ID of poly) but it isn't. The one control arm can be pivoted into a position and it will stay there just by the stiction of the bushings. Perhaps that's just a cost for very low compliance in real world manufacturing. It may loosen up some with a few weeks as they said, but I don't like their lube; it seems way too sticky to me. -
OK, I did a search and found other issues, but not this one. Maybe it isn't a problem. I dunno, you tell me. I have the Energy Suspension Master Bushing kit for my 280Z. Everything on the front fit up just fine, but the rear has me confused. I have everything laid out as to what fits where so I am sure I have everything lined up for the right spot; it's pretty hard to mix it up. Anyways, the rear lower control arm inner bushings don't seem right. As I understand it, once you remove the OE bushings (including the outer metal lining by using a saw), the polyurethane slides in and then the metal sleeve pushes in. When the lower control arm is all bolted up to the chassis and the big bolts on each end of the inner side are tightened down, they should snug up on the sleeves which are snugged up to the control arm itself. By this method, it takes all of the fore-aft slack out of the bushings without actually placing the poly bushing in compression. Well, when I installed everything, the sleeves looked about 1/8" too short on both the front end and the rear. I know the front and rear require a matched set of bushings and one end is a tad shorter than the other, but I am sure I have it right. BOTH sides are too short by the same amount anyways. I thought maybe they just need to compress or something and went ahead and bolted the control arms to the chassis, but when I bolt it all up and snug them down, they do indeed compress the poly bushings and the lower control arms are tight. Swiveling them up and down causes the bushing to pivot with the control arm and squeak and they will stay where I move them albeit it doesn't require a lot of muscle to move them. Every setup I've seen allows for the polyurethane portion to stay stationary with the chassis and only the bolt inside the metal sleeve actually pivots. What gives? Did ES send me metal sleeves that aren't long enough? It seems like the poly bushings are compressed a lot before the big control arm bolts actually bottom out on the metal sleeves. Anyone that can share info would be appreciated. I know I cannot just shorten the two halves of the poly bushings as they are the right length to span the clamshells on the chassis (if anything I think they could've been a tad longer too, but pushing the sleeve in them while they are off the control arms showed the sleeves were still too short). TIA, Mark
-
Lifting an Inside Front Wheel
WizardBlack replied to johnc's topic in Brakes, Wheels, Suspension and Chassis
AWD cars do, too. But then I am sure with all the wierd drivetrain setups on AWD some do it like RWD as well. -
The A1000 is not a big hunk of aluminum crap. Comparing it to a Walbro NVH-wise is definitely not it's strong suit, but it supports about TWICE what a walbro will. It's a big and nasty race pump for the most part; thus the noise and vibration issues aren't much of a problem for it's primary application. Walbros will only go to about 500. I've used them on 'street' cars before. Yeah, they are noisy and they vibrate, but I've driven too many very loud and very fast turbo cars before for it to bother me. It's more of a comforting sound because I know my fuel supply is still working. Dual walbros is a good solution but some worry that you could have one fuel pump fail and still be able to start and drive without knowing you don't have enough fuel for boost. I've heard of only one or two cars have that issue but they both ended up damaging the motor.
-
That is slip in style and will only slip into the intake pipe (pre turbo). If you need one for a boosted car it should be threaded to go after the turbo and intercooler.
-
Hmm, I think you'll have to wait for one of the seasoned L28 guys to answer for the specific motor. I could see a blockoff of the head limiting the oil pressure to some degree but you should still get it flowing through to your main and rod bearings. I would hazard a guess (sorry it isn't going to be anything to go on) that if the head was blocked off, you wouldn't have enough open discharge for the oil pump to push the air out and start picking up oil. One thing you could feasibly try is to remove the oil pressure sensor and try priming it with someone watching the hole to see if it starts pouring out with that hole.
-
Just to throw it out there, Big Phil mentioned in another current thread that if the head gasket is installed the wrong way it could block oil passages to the head. How are you determining there is no oil? Via the filler cap and peering down into the top end or by using an oil pressure gauge on the block itself? Also, what is "quite a while"? I have seen some engines take 10~20 seconds or more to start priming.
-
Sorry to see those problems. I have had a few ppl I know go through the same issues in the past on other motors. I will say this: flush every single route of oil. Those metal particles get everywhere and if any one of them isn't flushed it will circulate back through the motor again and take the bearings out. I've seen it multiple times. IMHO, flush the block's oil passages, replace the oil pump, have the head flushed, etc. Hope everything works out for ya.
-
Spindle-Pin-Puller Loaner program
WizardBlack replied to Dave's topic in Brakes, Wheels, Suspension, and Chassis
Thanks for the info. I ended up getting to the suspension and went ahead and knocked them out without it. I believe mine had recently been replaced; otherwise I'd have never gotten them out. Why, oh why, don't ppl use antiseize?!? LOL Thanks, Mark -
I know earlier you mentioned displacement to manifold volumetric ratio. Can you comment on what it affects when using a manifold that is too small or too large?
-
This Holset battle station is armed and fully operational!
WizardBlack replied to nish's topic in Turbo / Supercharger
Hmm, thank you I will indeed search some more. The dude that sold me the Z (on here) really had some incorrect information. -
There is no mention of the Aeromotive pump in that discussion. The root issue is that some aftermarket pumps WILL prime themselves and some won't. The ones that won't MUST always be below fuel level so that fuel will naturally fall via gravity to the inlet. They can't deal with air. Some of the other aftermarket pumps have a different displacement method that will also displace air and therefor siphon the fuel up to themselves at start (ie., self priming). I was pretty sure the A1000 was a self priming even if they don't tell you that for their own safety reasons. It's always a good idea to gravity feed if packaging allows. Honestly, seeing the way an S30 is built, the 044 Bosch pump looks like the way to go. Mark
-
Who told you it had to be lower? I was pretty sure that the A1000 will suck the fuel up... BTW, make sure you RUBBER MOUNT it. It is loud and vibrates a lot. If you hard mount it it only makes it worse. Also, your car MUST be set up to have the fuel pump running while you are cranking as the pump won't hold fuel pressure while it is off. I know some cars prime the pump when key is turned on and then it shuts off and doesn't come back on until the car is started. The A1000 must be running while the car is cranking or you have zero fuel pressure.
-
Would you be interested in testing a Mitsubishi Evolution VIII injector? They are a readily available injector and flow 560 cc/min.
-
Most cars I have seen end up with a hysteresis of about 10 degrees F which hovers around the thermostat temp. Much lower than that is pointless (may as well rig the fan to stay on all the time) and higher than that isn't really wise. As far as fuel pressure, it really varies from setup to setup. I have seen aftermarket pumps that allow the pressure to back up through it as soon as it shuts off (ie., no pressure when off; priming is pointless) and stock cars that hang on to part of the pressure overnight. I wouldn't worry about it. EDIT: BTW, I watched the video. Looking good!