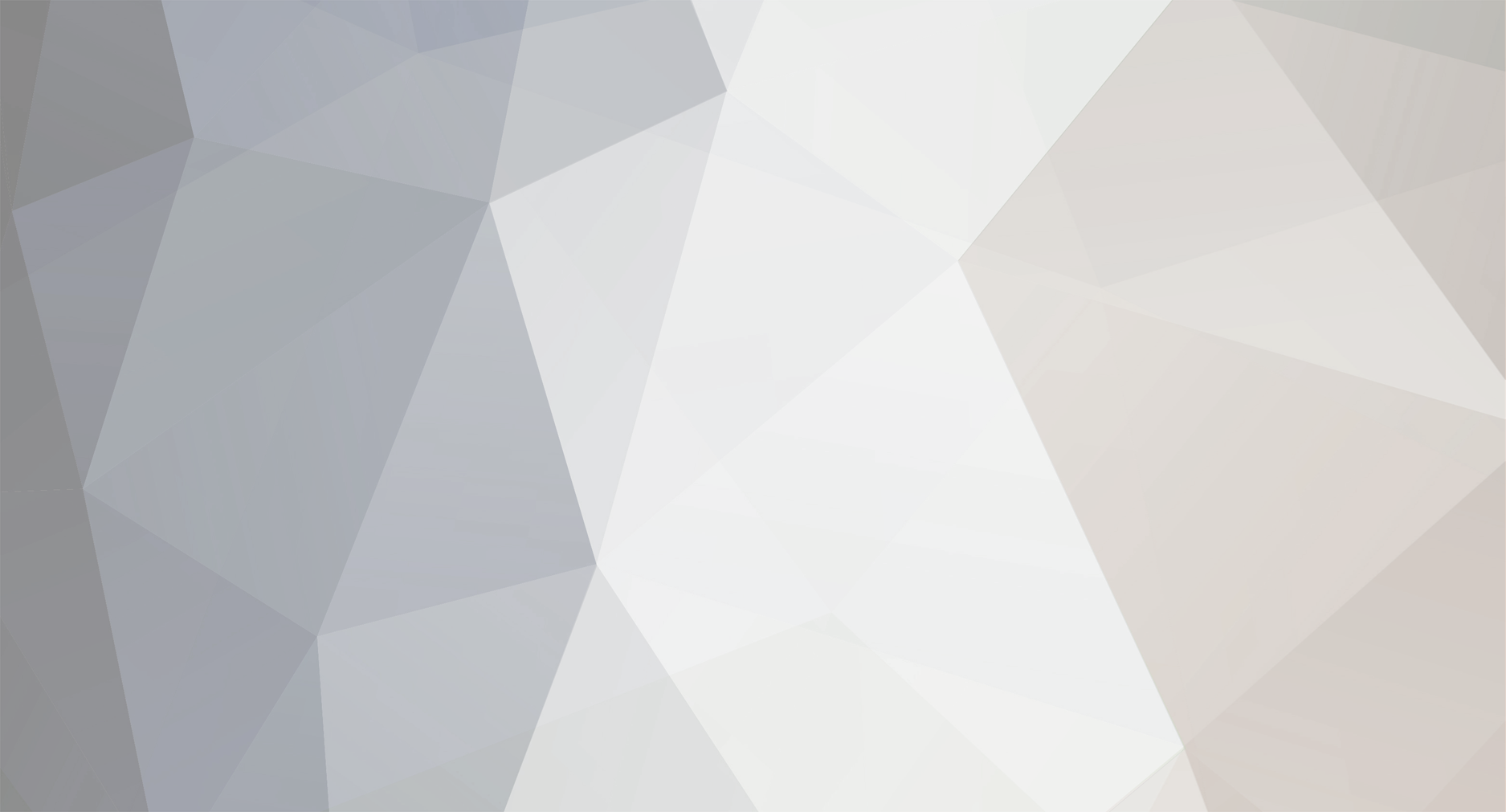
rejracer
Donating Members-
Posts
422 -
Joined
-
Last visited
-
Days Won
2
Content Type
Profiles
Forums
Blogs
Events
Gallery
Downloads
Store
Everything posted by rejracer
-
How bad can it be? Thinking of taking this 72 240z.
rejracer replied to estrada42's topic in Non Tech Board
Free? Take it! Your budget of getting it running is about right. Don't think free car means cheap car. -
I pulled the speedo cog, it was black. I did not bother pulling the rear cover. I might go back out and check. 37:11 is the lucky number.
-
Leon, One point to consider: All L6 intake manifolds have the air entering from front to rear of the vehicle. Since this is the case, making that 90* turn over the largest arc a will consume the least amount of energy. Velocity change should be made over the longest distance (within reason). Velocity change could be the air speeding up / slowing down, or changing direction. The question remains, is this more efficient than a straight runner. Why does it make sense designing runners after a plenum? Is there some math behind it, or does it just seem logical? Thanks, Robert
-
Here is the latest, I did not like the angles so I split the runners into two pieces, it's much more compact so far. I'm still playing with the runners, but I think the geometry is there, now I just need to tweak diameters. from the front: Current runner diameters are 60mm inlet and 38.1mm outlet. I don't yet know how to calculate the ideal, but then again, with the theory I am taking with this, I don't know if established guidelines apply. If anyone has any advice, I'm all ears.
-
I was at the Antelope, CA pic and pull today and found a 72 240z. Build date: 1/72. They had it listed as a 72 280. I guess that's why it's so complete. It had hood, doors, drivers fender and bucket, all lower valence pieces, rear bumper w/bumperetts no over bar, longblock (E88 head), trans, diff, full suspension. Hood was on top of car next to it. Color was white on red. Dash still has speedo and ammeter / fuel gauge. I pulled the front bumper, center console, tach and rear parking brake mechanism. It was rough, and I actually found some of the parts I needed in neighboring cars. There was also a 78 2+2 with a P79 engine and from what I could tell a 4 speed.
-
I decided the stubby concept is not the most ideal design. It's doable, but it's not turning out like I had hoped. The biggest problem is the volume in the plenum, I thought it would slow the buildup of pressure, and thus response. So here is the new concept. It uses a splayed runner layout to get the runner diameters where I want them. I have yet to design the plenum, but it will be a log design with ports going out to each runner. I am splaying the runners so they will clear one another. Both the forward slant and the cone/velocity stack design aspects cause interference between the runners. The purpose of this exercise is to come up with designs that will mitigate the efficiency lost as a result of the different velocities between the plenum and runners. If it's possible to lower the rate of change in velocity between the plenum and runner, then I believe the overall design will be more efficient. The my current understanding is the different velocities are caused by 2 design parameters. 1. The diameter difference between the runner entry and the plenum. 2. The near 90 degree angle between the runner and plenum. I've not had the time to work on it as much as I would like, but I think it's a solid concept. Build-able? Probably not. Once I get the "ideal" design down, I can start breaking this thing down to individual components to determine feasibility of construction.
-
ZX distributor upgrade questions
rejracer replied to 4.6StangRage's topic in S30 Series - 240z, 260z, 280z
regardless of the distributor you get, tear it down and check to see how much advance the distributor has. I would pull the dist base with it, not knowing what car this is going on. The distributor bases are different between 72 and 83 Z's. I don't know what year the change happened, if it was with 280z or 280zx, or somewhere in between. While in the yard, Check the bushings, Inspect the magnet, coil and stator, points plate, and the vacuum module. If 2 or more things above are bad it may be cheaper to buy a refurb unit from Rock Auto. as tony said, Ensure you are running a E-12-80 control module. If it has 2 connectors there is a circuit that can be built to eliminate the ignition retard portion of the module. I personally would just get the E12-80 module. Hope that helps. -
Pull the spark coil wire from the coil and see how far it will arc to the plug wire. check the basics: 1. Check to see that the distributor mechanical and vacuum advance is working tip top. 2. Set your timing to factory spec, or advanced if you know what engine you have (open or closed chamber) and how much mechanical distributor advance you have. 3. Check to see if the carbs are getting heat from the cooling system. This in my experience it the biggest factor when it comes to hesitation on these cars. If the outlet on the rear carb is not warm, it's not getting enough heat. 4. Fix any vacuum leaks you may have. 5. Set your Fuel Mixtures if they need it. From your description, it sounds like the carbs are running out of fuel if that's the case, here is what I would do: 6. Check your fuel pressure at the carbs while the engine is under a load. If pressure is not good then: 7. It could be rusty fuel lines from the tank to the fuel filter, or between the fuel filter and the carbs. Corrosion can be removed with products like evapo rust. Once fuel pressure issue is fixed: 8. I cant remember if the SU's have the built in perforated brass filter on the carb inlet. Pull it and check to see if it does, and that the inlet is free of obstruction. 9. Pull the lower jet and give it and the line connecting it a good cleaning. 10. Pull the bowls and check the needle and seat. as well as the port going from the bowl to the jet.
-
Shaft swapping between long and short tail FS5W51x
rejracer replied to will_drift_4_food's topic in Drivetrain
I would not weld on the shaft, rather swap components assuming they are compatible. Once you get into teardown, it's not that bad. I am assuming that when welding the shaft, you would have it torn down anyway. Shafts are not just like welding normal steel if you want them to be strong. -
I tightened mine while the diff was installed. I just used an open ended wrench between the body and the RT mount. With the poly mount attached to the diff, there was no problem with it twisting. Yes there is room once installed. As far as torque, I just snugged it up real well.
-
I also found a link which has the instructions from the FSM: http://www.zcar.com/70-83_tech_discussion_forum/adjusting_clutch_slave_cylinder_240z_654914.0.html Lastly, you NEED to get your hands on a factory service manual. Download the service manual from Xenon s30 Get the 1972 manual, the clutch system did not change between 71 and 72. I would agree with Dexter, it's most likely a hydraulic issue.
-
Bonjour Monsieur, There is no booster in the clutch system. There is a clutch master cylinder, and a clutch slave cylinder, with a metal line in between. To check out the system: 1. check the fluid level in the system. Bleed it as necessary. 2. Check the adjustments on the pedal per: Atlantic Z Clutch freeplay page. 3. Adjust the slave cylinder if necessary. The system can leak at either the master cylinder or the slave cylinder ends. Inspect the clutch master cylinder by looking up where the rod from the clutch pedal goes into the clutch master cylinder. If you see signs of leakage, the clutch master is leaking. Check the clutch slave cylinder by pulling back the dust boot and looking for signs of excessive leaking. Note that during normal operation (over the years) some fluid will seep past and form small amounts of sledge at the end of the piston travel. do not be concerned with small amounts of sledge. Do be concerned with fresh fluid, which is a result of a large leak. J'espère que vous le faire réparer,
-
Fidanza flywheel, ACT clutch install and pedal mods
rejracer replied to rejracer's topic in Drivetrain
Good to know, I recall mine were tapped all the way down, I checked fitment in every hole. I never did check into it, but it might be possible to drill the hole all the way, and make it a through hole. It looks like it might interfere with the ring gear: it could be done, but would require a good machinist. Im thinking use flathead counter sunk bolts to go through. If it interferes with the ring gear, it will secure the ring gear better, but it would be a pain if you ever had to replace it. Steel is looking better all the time... -
Hey there Hybrid, I never created a post on my flywheel and clutch install. I did this about 2 years ago. I searched for many options available and I decided the best bang for the buck is the Fidanza aluminum flywheel with ACT clutch. By "best" I mean that it is: 1. Improvement over the stock flywheel. 2. Reliable. 3. Serviceable 4. In an emergency off the shelf parts can get me up and running Concerning why I chose the above, I started a rev-happy-flywheel-clutch-choices-for-street-use thread. Had I to do this again, I might have chosen different parts, regardless, lots of info in the other thread. Just an FYI, if I were to scratch requirement 4 off the list, I would have went with the clutch masters setup like monzter is running. If I were to scratch 3 off the list, I would have went with a kamari or similar steel flywheel. It all depends on what your priorities are. Now back to the topic! To start off with I wanted maximum thread engagement for the clutch/pressure plate mounting. Some have reported that these strip out upon fastening them down because the holes in the flywheel are blind, and this forces us to use shorter bolts. To get around this I decided it was best to use a stud. The hardware I chose for this is: Class 14.9 M8.1.25x25mm socket hex screws (used Class 14.9 because 10.9 was not available from McMaster Carr) Class 10.9 M8 washers Class 10.9 M8 1.25 nuts A visual of the problem, because the holes in the flywheel are blind, it's not possible to use longer bolts. When tightening the bolts down some have reported the aluminum threads are pulling out. To get around this I thought a stud would be better for this application. It all assembled: For the final assembly, I used locktight green for the setting the dowels and studs in the flywheel. I measured the depth of the hole, and threads in the crank, the thickness of the flywheel where it mates with the crank, and the thickness of the ring I was planning on using for installation. I then called up ARP and purchased longer 12 point bolts. These bolts were a 1 off design that ARP custom made for another customer, who did not buy them all. I ended up picking them up for a really good rate, but I had to buy a set of 7 as part of the deal. I cannot remember the specifics of the length, but I had a very helpful sales rep that did the research and was able to find these. As I recall they have 20mm of thread engagement. I want to say stock was 10-12 mm when you consider the increased flywheel thickness and spacer I had read of someone milling the top of the bolts to gain clearance when you run the spacer, and these bolts have a shorter head on them, so this will not be necessary. Here is the crank side of the flywheel, I did not have the spacer at the time the picture was taken, so they are protruding 3mm's or so more than they are installed. When I installed it I thoroughly cleaned the mating surface, and thread bores on the crank. Then ran a thread chaser down them to ensure the threads are in good shape. Finally cleaned everything with brake clean and compressed air. The flywheel bolts were installed using blue locktight. The pressure plate nuts were installed using locktight blue. I then measured and confirmed I was using the right collar and after I was confident, I installed the new throwout bearing, greased the shift fork, and installed it. My clutch pedal was worn quite badly, so I opted to fix it! I increased the clevis pin to 10mm instead of 8mm. I also wanted to give the clutch pedal a bit more throw, so I wanted to bias the hole further away from the clutch pedal pivot point. I would say I lowered it perhaps 1mm. I also wanted to use a hardened steel sleeve, which I had handy. I took the outside diameter of the sleeve and drilled a hole the same size in the clutch pedal. To drill the larger hole in the right spot, I used a thick washer(approx 3/8" thick) to guide the drill bit. I had predrilled the hole to the right diameter in the washer before hand. I then tack welded the washer to the clutch pedal where I wanted to hole to be. As you can see I positioned the washer with an 8mm bolt. The bolt was in the original hole. This enabled me to bias the hole down and forward as I wanted to do. When I got the washer in the right place, I tightened up the bolt, then tack welded it. Using the washer as a guide, I was able to drill the hole off the center line of the old hole. With the hole drilled I ground off the tack welds and inserted the steel bushing, and tack welded it in place The bushing I used was a bit longer than the width of the clutch pedal lever, which gave a bit wider (better) contact area and would hopefully be more durable. Not that a 40 year service life is bad, but why not go for 100? I was able to drill the clutch adjustment clevis to the right diameter for connecting to the clutch pedal. For a clevis pin a Class 10.9 10mm bolt was used. It was necessary to cut it to length and drill a small hole in it for a cotter pin. Due to the additional width of the bushing, it was a tight fit. With a hardened steel bushing and the class 10.9 bolt, I don't see it wearing out anytime soon. I should probably take it apart and inspect for wear to satisfy my curiosity. Lastly, the clevis did not seem to have enough thread engagement, maybe 2 full threads when adjusted. So I removed it again, and welded a nut to the end of it to add another 5mm's worth of threads. It solved the problem, although I really want to make a new clevis, I have stainless steel stock to make it from. For final adjustment I followed Atlantic Z's Clutch Free Play guide. I finished the install in the summer of 09, and it's been a big improvement. WRCBONK drove the car in the spring of 2010, and he liked the feel of the clutch. I can't believe how much of a difference the clutch pedal mod made. No more squeaks, rattles or play, just quiet and smooth. The clutch drives well on the street, and I noticed a big difference in the way the engine responds. In the rev happy flywheel thread, someone pointed out that they can feel every pulse of the engine, an that is certainly true at lower RPM's. So far no problems! I will give it a good inspection when I do my trans swap. I will be putting in a FS5W71C, hope to do that swap soon. happy wrenching
-
My suggestion is to pull the compressor and drain the oil. Flush all the components using denatured alcohol, and blow dry. Then evac the system. The reason for draining the compressor and flushing with denatured alcohol is to ensure the oil is out of the system before charging. It's not necessary to replace the receiver drier every time the system is open, only if it's been contaminated. Just make sure you hold the system at vacuum for 45+ minutes to ensure it's dry. Concerning the receiver driers, they can be stored indefinitely uncharged. Leaving the system open to atmosphere is what you should avoid. At a minimum, store them with vacuum caps to prevent it from absorbing unnecessary moisture. If the system has been left open, or it's old, I personally would replace the receiver drier.
-
Check the basics. 1. Is it getting spark? 2. Is it getting fuel? 3. Check all electrical connections, fusible links and relevant fuses. Chances are you removed or unplugged something during the prep work.
-
Clutch masters and ACT are good. Stock is not bad either, although I don't know the HP rating. Both of their websites are straight forward.
-
Oz, It depends on what regulator you have in it as far as what wires you need for alternator operation. At a minimum, you need the excite wire and the main wire. It is strongly suggested that you install the alternator using heavier gauge wire (at least 4ga) for both positive and negative. The alternator is capable of burning up the existing wiring. I have a post on this, check it out, I created a wiring diagram, and included pics of the install. There are other posts as well, that document various aspects of the upgrade. rejracers charging system upgrade
-
Download the FSM from http://www.xenons130.com/ . The system is described in Detail. If you are running the stock turbo system, it's called the ECCS.
-
I got the chance to pull the 300zx VSS. The lineup from left to right. 1. 240z w/manual 3.364 2. 240z w/auto 3.54 3. Early 5spd 3.54 4. I am assuming 280zx 2+2 or GL model. 3.70 5. 87 300zx NA 3.70 I disassembled the 300zx VSS and I was able to reassemble it with the 240z gear, based on that, I assume any of the gears will work with it. The VSS will also screw onto any of the the Cog bodies. If one were to have the right adapter, it would be possible to run this sensor behind the dash. Regardless, this sensor is nice, as it can be used with any L series transmission. I think it's exactly what you need, it's certainly the part I am going to use when I do my gauges. One question: does the Maxima speedo have blinker indicators on the speedo face? I did not see them in the pics. Thanks for the writeup, hope this sensor solves the problem you are facing. PS... I need a red and a white cog(more interested in the white), you up for a trade? I have 1 black and 1 blue to trade. No big deal, I can source one from the jy here if you don't.
-
Valve cover paint? Regular or engine paint
rejracer replied to voltron_boi's topic in Body Kits & Paint
I painted the inlay parts of this valve cover in 1995. The photo was taken about 3 weeks ago. It's held up fine, and still looks good (the paint). I even use my valve cover as a place to set tools, fastners, parts when working on it. I just did the proper prep work and painted it with engine paint. I too like the duplicolor engine paints, please note there is a difference between engine paint and high heat paint. For an engine, use engine paint, not the high heat. For black parts I now use duplicolor low gloss black. It dries much faster, and I believe it adheres much better than the gloss varieties. Because it's low gloss, you don't notice the scratches that inevitably appear on real world parts. -
The L28ET only uses the throttle closed switch of the "TPS". This turns on the idle control circuit of the L28ET. If the S13 TPS has a throttle closed switch in it then it will work just fine, assuming you wire it up.
-
You could use epoxy to put the gear on, just rough up the gear hole and shaft surfaces, assuming you can get it on concentric. If your circuit works, I would not fiddle with the gears, that's a fairly slick setup. FYI.. GM ECU's take the VSS signal, and have programed into them the gear ratio and tire size to calculate the VSS output which goes to the Speedo, Cruise control, and body control modules. You are achieving the same thing. I'll get pics of the VSS from the 87 300zx. The VSS has a gear for 3.70's, and I will test fit it for my spare 280zx 5spd.
-
John M, Yes preload as you described is what I was referring to. I don't like fiddling with lowering the car slowly to seat the springs. Preload ensures they stay on both perches. I have my car set up in front with preload in the front, and I am using 12" hypercoils, Beta motorsports upper and lower spring perches. Preload is determined by spring rate and ride height, assuming you are not sectioning the tubes. I am currently at stock ride height, which is 6.5" for a 72. When I said I wanted to get a 50% increase on spring rate, I looked up the spring rates for an S30, and found the rates listed for a 280z, which are higher. I did not think to check to see the specific year. When the deal came up for the 3 pair of hypercoils, they were 175, 200, and 225 rates, which was exactly what I had calculated I needed. My reason for not wanting higher rates is that the higher rates on rougher roads are uncomfortable, plus more unpredictable in cornering on rough roads. After buying the springs, I learned the right spring rate and discovered the slight issues of preload in the rear using the 225lb springs. I will swap rears out for the 200's and see if I will have preload using them. I tried calculating the rate, and was a bit off on my calcs. Daz, I hope you find this helpful, I think it's relevant info to consider, but I still don't know what your intended use is. If it's a track car, my concerns about preload are not that important, but a minor annoyance on a street car.
-
The FS5w71B and FS5W71C I thought had the same offset between the tail housing and output shaft. I am assuming the 240sx you pulled the sensor from is using a FS5W71C, which should just be a drop in affair, at most grinding a flat spot on it. I have setting in my storage shed a FS5W71C out of a 1987 300zx NA and speed sensor, a FS5W71B with a variety of speedo cogs. I can check to see if the 300zx sensor fits in the 71B transmission. My understanding is that the speedo cogs are interchangeable, assuming you change the cog, it should fit. I was planning on following Nigels writeup when I install the 71C into my 72. the hole for the shaft (which the gear is connected to) is not concentric, in other words, as you rotate it, it gets closer or further away from the gear. I think you just need to clock it correctly? I think that's what you were saying above?