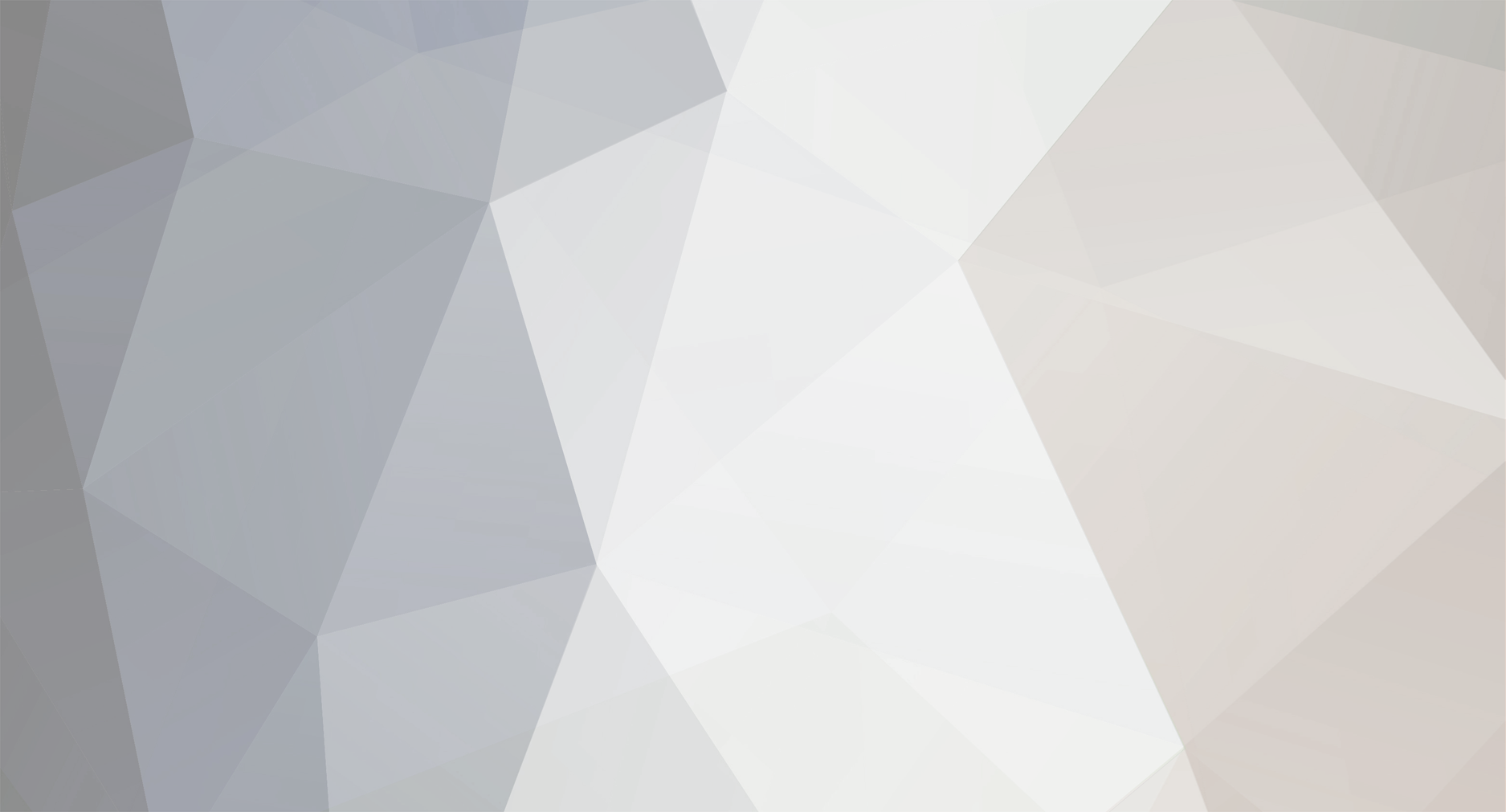
rejracer
Donating Members-
Posts
422 -
Joined
-
Last visited
-
Days Won
2
Content Type
Profiles
Forums
Blogs
Events
Gallery
Downloads
Store
Everything posted by rejracer
-
I picked up 3 sets of 12" blue hypercoils used for 60$, so I'm set at 12" lengths. I think you can use anywhere from around 16" to 8". The stockers are somewhere in the 14 to 15" range. The setup John is selling requires you to weld a section of pipe to your strut tube, depending on where you place this section of pipe, determines the length of spring you need to use. The 8" spring is a good choice. If you are going to be lowering, I strongly suggest you section the strut tubes. With John's setup, you only need to buy the threaded collar, lower spring perches, and springs. You modify the upper spring perch by welding a 2.5" (or is it 2": section of pipe to the upper perch to keep the spring aligned. I will end up running 175 front and 200 rear springs. Much more than that and the springs will not have preload. I don't like having to fiddle with springs to get them to set in their perches every time I pull the car off of jackstands. Regardless, my original goal was to increase spring rate by 50%, which would put the fronts around 125. The shocks I am running are 5 way adjustables, which are limited to about 275lbs max. I could not imagine driving a 240z with that stiff of spring on the street. Maybe in Texas (much nicer roads) but the cobblestone paths we call roads in california would beat you up.
-
Beta Motorsports has one of the best deals considering the quality. Plus John is very knowledgeable, and gives great support. http://www.betamotorsports.com/
-
Tim, The offset of the cog bodies is different between the 70-80 bodies than the 81-83 bodies. The reason for this is the early transmissions the locking tab (flat machined section on the cog body) faces up. On the later transmissions it faces down. It sounds like you have a cog body that is mismatched to the transmission. You can change gear and use the same cog body, or swap it out. I read somewhere of someone machining a secondary flat spot on one of their cogs to make it a "universal" Hope that helps. Edit: The gauge electronics are most likely set up to calibrate between MPH and KPH. This would explain the difference as the gauge face would change, as would the calibration on the Odometer. The other reason for this is the same electronics can be used for different face plates 0-100 versus 0-150. It might be an engineering carryover from when cars were only allowed 85mph speedo's. Anyhow, it makes sense to me. Edit to the Edit: Nigel describes the cog differences in his trans swap guide: http://www.motortopia.com/cars/1973-datsun-240z-11118/car-pictures/240sx-transmission-swap-14041 edit to the edit to the edit: Also stumbled upon this link, which articulates the same differences in the cogs. http://www.geocities.com/inlinestroker/ratio.html
-
I just stumbled across this thread again. The difference between class and grade is like BAR and PSI. It's metric versus imperial. Grade 5 is the same material as a class 8.8. Grade 8 is the same material as class 10.9. Please note they are not the same strength, because the sizes are different. Now for the practical differences: The diameters are not the same. The thread pitches will be different. The markings on the heads are different, Class has the number on the head, Grade has radial lines. 3 lines = grade 5. 5 lines = grade 8 The hex head sizes will be different (as in imperial not metric sizes). The problem is folks are giving advice and they are saying things like, "you need a grade 8 bolt". Then the neophyte goes to the hardware store and buys a class 8.8, because he knows it's metric, and ends up buying a bolt that is "the same" as a grade 5 bolt. If the head is not marked, then it's either grade 2 (which is garbage) or unknown in the metric system. It's not that we are being picky, we are trying to be accurate and to give advice to those that don't know the difference between a metric and an imperial bolt. Fellas chiming in mocking those trying to help out is not doing anyone any favors, especially the guy going to the hardware store buying the wrong fasteners! So in short... 10mm Grade 8 bolts don't exist. Got it? Ever wanted to know what a sex bolt is? Click the link and find out! http://www.boltdepot.com/fastener-information/
-
I did the above upgrade as well, although on a 72, which only has 1 fusible link. I ended up running 3 wires to mine: I am only using 30 amp circuit breakers for the time being. I have 80 amp fuses, but decided to try the circuit breakers for the time being. It's been rock solid so far, run for about 3 weeks. 1. The Alternator wire (White/Red) 2. The fusible link wire (White) 3. Headlight relay harness A fusible link is just a smaller gauge of wire, but with a specific type of insulator. I have seen fusible links at auto parts stores, autozone to be specific. If you are blowing fusible links, find out first why. And whatever you do, DON'T put in a higher rated fusible link than what the circuit was designed for.
-
For the bolts I think they would clear, but if not a stud / nut combo would easily clear. As far as header flange I think it's good as I made the flange based off dims from Ron Tyler. Clearing primary tubes, Good question! Aa far as the steering shaft and motor mount, the Plenum is 10" tall, so it hangs down 5" from perpendicular to flange port centerlines. Plenum base is 9" away from manifold mounting surface on head. but here is some info on it: Plenum outlet ID is 75mm. Flange port ID is 38mm (1.5") All ports have identical offsets. and design. Here is the last version I had made up. I did not like the layout of the previous, so I rearranced them. then I discover I don't like this very much... so back to the drawing board.. I ended up reversing ports 3 and 4 on the Plenum. I also reduced the port entrance diameter to 50mm. I rearranged the ports to make the overall design smaller. Next I will try and increase the offset. I changed the port offset again, Increased the port entrance diameter to 55mm, increased the plenum offset to 10". This latest version the plenum base is 8" tall.
-
I'm trying to come up with a new plenum design on an L6. I have this concept that it's the length of the L motors that makes the plenums hard to design for. As a result I am trying to get the plenum output ports closer together by offsetting the plenum output ports by a set amount for all the ports. I also want all the ports identical. Here is version 1, which has issues with the runners clearing each other, so this particular design is not buildable. I am in the process of moving the ports on the plenum around to make this possible. The port design is intended to be a large velocity stack. The diameter is larger at the plenum side. I think they are 2.5" at the plenum and 1.5" at the flange. When designing a velocity stack, what are the variables and formulas needed to calculate the optimal design for a given application (displacement, VE, RPM...) Any help is appreciated. ..and the eyecandy Clearance is an issue between 1-2 and 5-6. 3-4 cleared, but that was an easy fix by increasing the vertical offset. This gives you a better feel for the diameter difference between the plenum output and the flange input diameters. The design seemed simple, but the offset and diameter differences are shooting holes in this concept. Thanks.
-
location of headlight relay on 71 240z?
rejracer replied to Sugee_S30_Z's topic in Ignition and Electrical
Power runs from fusible link on starter to headlight switch to fuse block to Common terminal on headlights back to dimmer switch then to ground. Yes, 4 passes through the firewall! -
Will aftermarket 240Z springs work in a 280Z?
rejracer replied to Trbulnt's topic in S30 Series - 240z, 260z, 280z
Working and fitting are 2 different things. 240z uses softer spring rates, and rides lower than the 280z. The thickness of the strut tube walls is thinner, and a different inside diameter. There are also differences in the Hub assemblies on the front. I am not certain on the brakes. (yes I am aware you listed some of these things already) If you are changing out the isolators to the 280z type, you are no longer dealing with "the 240Z strut/spring assembly" John gave you a solid answer to the question you asked. In my opinion Turbo HLS30 gave you an incomplete answer, but was indicating there are options concerning using a mix/match of 280z/240z parts. There are a lot of variables and info not known that makes this almost impossible to answer. Such as: Corner weights of 280z (do you have parts removed like bumpers) What do you want the ride height to be? Since you are in wisconsin, I assume your roads are rough due to the thing you call winter back there. Running a car with little or no suspension travel is a recipe for damaging parts, or worse, an accident. Just some food for thought. -
Wire components in for the worst case scenario, rather than what you want it to be. If you have a dead battery, and you start it up, and then increase the rpm, then the alternator will be charging at full tilt for x minutes. The battery will "buffer" power draw once voltage drops below it's stable charge state (roughly 12.5 volts). So it's not stable voltage by any means. Also with the factory wiring harness the voltage at the device using the power will be lower than 12.5 due to the losses in the harness. Everything BJhines is saying I agree with, except I would add the one detail on the buffer bit. I will say that if someone is running old school technology (carb, points distributor) then the voltage is not much of a concern, assuming dimming lights and slow fans don't bother you. If you are running a modern computer controlled fuel / spark system then the stock system is not adequate. I think what is really needed is an accurate diagram, (which I think I created in the below thread) so one can easily track the power path from the alternator to whatever device you are concerned with. BJhines, I just completed my 240z charging system upgrade consisting of a 200 amp alternator, heavy duty battery cable assemblies, Aux Power Posts, circuit breakers, and eventually Volt meter. I can tell you are not a neophyte in the ways of the electron, so would like your input on my setup. I created the diagrams based on the 72 / 73 FSM. So far the FSM is accurate in the engine bay, up to the firewall. When I go for the Voltage gauge install, this will tell me how accurate the FSM diagrams are from the firewall to the Ammeter and fuse block. My plan so far is to cut out as much of the old white / white red going to the ammeter as possible.
-
The original poster is talking about a stockish L26. My comments are within the context of what the original poster was asking for. You are not going to gain ANY volumetric efficiency by "upgrading" a non limiting factor. Change the cam / cam timing, cylinder head, or exhaust and my comments no longer apply. Yes there are improvements to be had on the Stock SU's, but now we are talking about tuning, not bolt ons. Same rule applies to webers. I like my triples (DCOE 40-18's), they make lots of noise, and run well. I also like the stock SU's. My emotional attachment to a piece of hardware does not change my answer to the original poster as how to best benefit him. For what it's worth, I can't tell the difference between the two on the butt dyno, except: The triples are more responsive at tip in, and make more noise. Initial tip in throttle response has nothing to do with WOT power. I hope that clarifies things.
-
So I recrimped the battery cables. The old setup was several individual cables routed to the battery. I now crimped the individual leads into 1 terminal. Crimped terminals are better than soldered as if a serious problem arises and they get hot, they are mechanically attached to the cable, where solder could melt, and cables come apart. Crimping in action, sunny day, forgot my hat, think i got a sunburn up there. Watch out when releasing these crimpers. I relased one and I did not slow it down enough, unfortunately the back of my and and the handle caught my chin. I spent the next 30seconds feeling for broken teeth, fortunately none! I have not had that sensation since high school. Negative crimp done on battery side. I used (3) 2ga cables to the starter, alternator and Aux ground post, plus one 8ga wire to the factory chassis ground. The positive side only had the three main cables. The terminal is a 4/0 the cables fit in very snug, I think perfect for what I was trying to do. The finished negative assembly. They are a lot of work to crimp. 2 crimps on each terminal, and it's everything I can do to get it crimped. The hydraulic hose is going to be the insulator for a bracket I intend on making for it. I'm routing the cables under the motor mount. Below the motor mount will be a bracket to hold the battery cables. The bracket will be bolted to the block using the motor mount bolts. Birds eye view. Looks much better without the old overflow tank mounted on the strut tower. Circuit breakers installed, this eliminates the fusible link. The entire vehicle is powered through this little block. I'm not so sure on the quality of this unit. I consider this a temporary fix until I get the electrical center installed. If I were to run this more than 5 or so years, I would replace the bottom piece as it seems too weak. I may fabricate one out of fiberglass stock from McMaster Carr. Regardless, circuit breakers that auto reset! How cool is that? the 1st breaker is for the "white" wire where the fusible link used to be, I used a 30 amp breaker. The 2nd breaker is for the old alternator White/Red wire, which I used a 30 amp breaker, the last is for the headlights, and used a 20 amp. New coolant bottle, from the turbo doner car. I need to get it mounted somewhere. Not much space with where I have my headlight relays wired up. I plan on ditching the hella fuse blocks in favor of the GM / delphi stuff. I will put the electrical center behind the strut tower. This is why I chose to mount the aux posts where I did. Once that is complete, then I think I will mount the coolant bottle where the hella fuseblocks are now. But I would also like to convert this car to a closed coolant system. Anyone know of a good small bottle to use for that? Only thing left to do as part of this phase of the upgrade is to install the volt meter and tidy up the harness with some wire loom. This is a relief getting this done, previously I was driving it around unfinished (read firehazard).
-
Correct Cogs: teeth Color Ratio 16 yellow 3.364 17 black 3.545 18 Blue 3.70 19 White 3.90 20 Red 4.11 21 Purple 4.38 Sounds like you need the speedo cog to set the odometer and the dip switches to scale the speedo. On the old speedo cogs you could switch the cog itself out from the body. Is that possible on the speed sensors? I like the design with the dip switches. This will enable you to make a new face if you wanted a 200mph speedo without major work. I might end up doing this mod to get an electronic speedo. Hope that helps.
-
Jake, Check out Monstzers fuel tank mods. Also WRCBONK did similar tank mods.
-
I agree it sounds like a ground issue. I would clean up the body ground connector in the engine bay, the one below the battery. Then run jumpers from the Alt case to ground and battery neg to this ground. if that does not help, problem is in harness. Do you have a schematic for the stock headlight circuits? Edit: Here is a diagram I made up, as well as a description of the system. Introduction: The 240z uses “A side†switching to get power to the headlights, and “B side†switching to ground them through the dimmer switch. Description: Power comes from batt/alt to headlight switch. From headlight switch power is routed to fuse block across 2 fuses, one fuse for the left headlight, and one for the right. From the fuseblock the fuses are connected to the left and right headlights common/ ground terminal on each bulb. From the bulb the High beam “ground†is connected to the dimmer switch, as is the low beam. The common side of the dimmer switch is connected to ground. Problems with this System: 1. The headlight switch is NOT fuse protected, and is a single point of failure for the entire system. 2. This setup requires full current be routed from: * Alternator to Fuseblock (fuseblock used as a juncition point, not going through fuses yet ) Fuseblock to headlight switch Headlight switch to fuseblock (this time through 2 10 amp fuses) * Fuseblock to common terminal on headlghts. * Headlights to dimmer switch via high and low beam circuits. * Dimmer switch to ground. Items marked with a * represent a circuit running through the firewall. 3. The long lengths of wire reduce overall performance of the lighting system.
-
Power comes from an ideal mixture being ignited at the correct time. What the mixture comes from, or what ignites the mixture is irrelevant. The stock SU carbs are not a limiting factor to power that can be had out of a mostly stock engine. I say pay attention to the small things, check your distributor is in perfect mechanical order, set to the ideal timing for your engine. Then sync and adjust the carbs. It's virtually free.
-
I finished mounting the power posts today. Originally I was going to mount a square plate. Once I fabbed it up, I decided I did not like it. Unfortunately I had already cut the fender support bracket. So I recut the plate, and tack welded the lower portion of the bracket on to it for looks really. Then finished the holes for the power posts. The finished product. I used masking tape and newspaper to tape it off before spraying the bracket down with duplicolor orange engine paint. And the backside (frontside?) Next up: Recrimp Battery Cables then voltmeter install.
-
I left mine unpainted. I installed it in 97. I intended on painting it, but the look grows on you. The only thing I dislike more than an unfinished look is a chipped and not repaired properly look.
-
If you have not yet purchased the refrigerant, you might check into a product called duracool. It's also called 12-R (not R-12). In a nutshell, it's 1% more efficient than R-12, is compatible with all lubricants, and can be mixed with existing refrigerants. Note, it's not legal to mix them, but it won't do damage to the system if you do. It's also non-toxic. The downside to this is it's flammable, as it's a pure hydrocarbon, but it's auto-ignition temperature is higher than R134. http://www.duracool.com/ As Kunoz pointed out, it's the lubricants that are incompatible. You must ensure you get all of it out. Evaporator/condenser can be easily flushed. They are "compatible" with each other, but the R134A is not as efficient as the R12/12R is, so the system will not cool quite as good. How do these condensers compare to the Vintage Air units? http://www.ackits.com/merchant.mvc?Screen=CTGY&Store_Code=01&Category_Code=Parallel Accumulators are replaced if they have been in service with another refrigerant. One note on the charge levels, I always go by the gauges for the given ambient temp/humidity. Here is an example chart: http://www.ackits.com/aacf/ptchart.cfm If you don't have a vacuum pump, gauges, refrigerant, lubes, dyes, injectors, thermometers, barometer..... then I would take it to a shop. A/C work requires a lot of special tools. Build it with the best parts, then take it to a professional is some good advice!
-
Hi all, Auxiliary Power Posts from Waytek wire. The mounting location. I chose this spot because I plan on moving my fuse box behind the strut tower, this is a good place to tap into power for all the power feeds. I will need to make a new mounting plate. I'm still deciding on keeping the existing and just welding in the circular plate, then redrilling the holes, OR building a new plate, and trimming the existing back, basically making it just an L bracket to mount the new plate. On the lower side I would tack weld in some brackets to bolt it together, making it nice and rigid. The back side. When the power posts are in, I will recrimp the battery cable assemblies into a single connector. I will also ditch the 1/0 cable in favor of 2 ga to the starter. Essentially each cable assembly will be 3 runs of 2 ga wire from battery to Starter, Alternator, Aux Power Post. I decided to test the 240z vs 280z fuel gauge. I set up a simple potentiometer wired in as a rheostat to limit voltage to the 2 gauges. It's not the most accurate test, but I think it's good enough to convince me that they are compatible. I will run the 280z gauge. Both gauges did full sweeps, at the same positions, same rate. I am satisfied the 280z gauge will work with the 240z sender.
-
I Just cleaned up the pod frame/housings and repainted the bezels. here are the pics of how it turned out. I used flat white paint coated with reflective spray. I did not like how the reflective spray turned out. I may strip the bezels down and redo them. Here is how the driver facing side turned out. Believe it or not, there is glass in it in this picture. Duplicolor low gloss engine enamel was used. The low gloss paints dry much faster than the gloss. The gauges mounted up. The somewhat finished assembly. The backside of the assembly. I was not concerned about paint finish on the rear portion. I had a local glass shop cut the glass rounds for me. Anyone know of a good bright white reflective paint? I would like a single stage rattle can paint, that is as reflective as a road sign, or better. As of now, the reflective spray I am using is a clear coating that turned the nice flat white paint to a yellowish color. -Robert
-
You can buy magnecore bulk wire. They sell quality wire, terminals and boots for many applications. http://www.magnecor.com/ I used them in this installation: http://forums.hybridz.org/index.php/topic/69648-chronicals-of-rejracers-l28et-swap/page__p__657547__fromsearch__1#entry657547 -Robert
-
Now for replacing the ammeter with a voltmeter. I sourced a 78 280z volt meter/fuel gauge pod. After reviewing the factory 280z service manual to glean how they intended to wire it up, I decided to tear the gauge pods apart. I noticed some physical differences between the fuel gauges. 240z on the left, 280z on the right. the 240z gauge interferes with the 280z rear housing, it touches the transparent green bubble on the inside of the gauge. I decided I did not want the green tint to the guages, so I removed it. This added enough clearance to mount the 240z gauge in the 280z gauge pod. And another view of the guages themselves: Notice the difference in font between the 240z (left) and 280z faceplates. I will probably keep the 280z faceplate as it's in better shape. Also notice the 280z face plate overlaps OVER the 280z volt meter. The 240z fuel gauge faceplate overlaps UNDER the stock ammeter gauge faceplate. The front bezel design is different. I will need to stick with the 240z bezel (left) to make this work. I am also replacing the factory plastic cover with glass. I had a local glass shop cut them out for me. I will reattach the inner bezel to the outer bezel using #2x.25 wood screws used with 3mm washers. I will drill a hole in the mounting tangs for the inner bezel to ensure all goes well. The steel frames of the 2 gauge pods are similar, same mounting for the fuel gauge, of course it's different mounting for the Volt meter, and the provision for the charge light. The components I think I will end up with is going to be: 280z metal frame 240z fuel gauge 290z fuel faceplate 280z volt meter and faceplate 280z ilumination light 280z charge light 240z inner and outer bezel, with glass insert. I am in the process of stripping the metal frame down to bare metal as it's rusty. I am going to paint the inside of the bucket white, and then give it a coat with reflective paint. I will do the same for the inside of the inner and outer bezels, but refinish the visible portions in flat black. By removing he green illumination light bubble, and refinishing the inside white with reflective paint, I hope to brighten the stock gauge illumination up a bit. If anyone has any insight to this upgrade, please chime in. In particular I would like to know if the 240z and 280z fuel gauges are the same electrically. As far as the wiring goes, I will connect the volt meter to ignition voltage, and to ground. The charge light indicator gets connected to switched ignition voltage, and the other end to the brown/red stripe wire on the CS144 alternator. The fuel gauge gets connected to the stock 240z connection points. I will try and use only the stock 240z connector. To my recollection, there is a position in the stock electrical connector that is not being used. I will use that position to run the wire from the charge light to the alternaor. If it's not available, I will just use a single insulated connector. -Robert
-
Here are the pictures of the install of the CS144 Alternator. There are 4 wires on the pigtail. Only 2 of them are used. The red wire is the voltage sensing wire, it gets connected directly to battery voltage. I suggest a 14ga wire direct from battery to this terminal. It is this wire that will enable the alternator to produce clean stable voltage. One wire alternators have voltage drop across the charge line, thus they will never be capable of producing stable voltage at high loads. The Brown with red stripe gets connected to switched voltage through a resistor. It is this wire that turns the alternator on. When the alternator is charging this alt produces 12v at this terminal. When the alternator is not charging this is grounded. This "switched" ground is what makes the charge light work. Here is a shot of the tidy sealed connector. It's very easy to remove and solidly locks in place. Notice the Alternator brackets. This is a bolt in installation, no hard modifications needed. I used the Alternator parts.com universal mount kit part number A285 Here is a better shot of the alternator mounts. They are simple offset brackets. The positioning of the lower mount could be better, Nigel's modified lower mount would put it in a better location. The downside to this is it limits the range of adjustment the alternator has. The plus side is it's a bolt in installation, somewhat adjustable, and very strong. Here is the upper mount. I used the stock upper mount but had to reduce the offset to have it line up correctly with the alternator. A hammer and vice worked just fine. I also had to slightly increase the inside width where the locking bolt passes through. A file worked fine. Parts used in this installation: CS144 200amp standard voltage regulator alternator (included the harness / plug) A285 dual foot alternator bracket Nissan small diameter pulley. I got this from the failed alternator, one from Z specialties. Napa 25-7350 or equivalent belt. Modified stock upper bracket Custom 2 gauge battery cables, run directly from battery to alternator. 280z volt meter Misc wiring as needed.
-
I just uploaded a new version. Changes: 1. Renamed old "Final drive" column to "Diff Ratio". 2. It now calculates RPM for the given speed in all gears. 3. It now calculates the Final drive ratio for all gears in the trans/diff combo. 4. It's now editable by anyone. Feel free to play, don't be surprised if/when I overwrite your changes with a refresh. I reserve the right to revoke update capability without notice, we will see how it goes. Feel free to ask me to refresh it, if it gets scrambled. -Robert