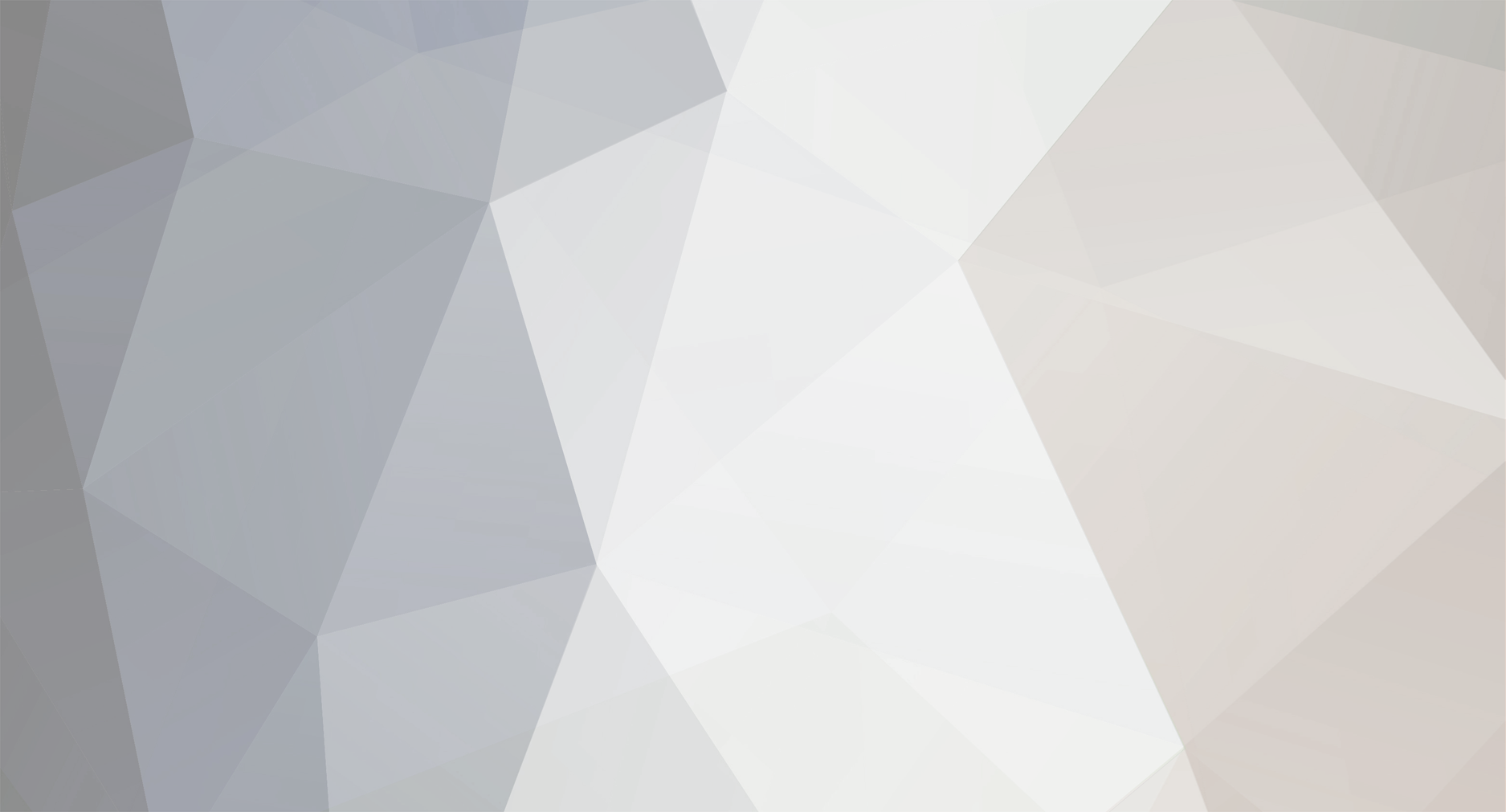
waddiejohn
Donating Members-
Posts
90 -
Joined
-
Last visited
-
Days Won
1
Content Type
Profiles
Forums
Blogs
Events
Gallery
Downloads
Store
Everything posted by waddiejohn
-
Young guy's get to have all the fun!
-
talk to me about milling machines
waddiejohn replied to grumpyvette's topic in Fabrication / Welding
I bought a 9x49 Lagun with DRO and power feed and a lot of tooling for $5000.00 a year ago last May. It is in excellant condition and I love it. Most of the Bridgeports I found were worn out and had 42" tables. I think it is a toss up between good Tiawan and U.S. made stuff. The Accra brand is good equipment in my experience. The Lagun is heavier. The knee is wider and so a bit more stable than the Bridgeport and copies, but for general use there is certainly nothing wrong with either. Before I was laid off last February I worked for a high tech company and they had a second hand Accra 9x42 mill and the guys that ran it abused it. They didn't even clean the cosmoline off of the collets and chips were imbeded in the goo. When I took over the shop I did some good cleaning and maintenance and that machine was a pleasure to use so I bought an Accra lathe too. When it came time to purchase the lathe I called a local machine shop and spoke to the owner about his lathe that was the twin to the one I was buying. He'd used his a lot and was happy with it so I got one for us and I was happy with it as well. The only complaints I had were it was too short in height and it didn't have quik change gear box. At home I have my Lugun mill and a Clausing lathe plus an 8x32 U.S. Burke Millright Mill that needs a rebuild and a cheap little Chinese lathe that was popular back in the 70's. I'd love to have all U.S. made equipment, but we've priced ourselves right out of the market. Before Southbend went under their 10X36 lathe was priced at $13,000 and it was still driven with a flat leather belt. Go figure! -
So, did I understand that you, in effect, created relief around the recoil lug by taping it off? We always wanted a very tight fit in that area. When we did a thread and chamber job for a customer we would guarantee an inch or better group size at 100 yards if we could free float the barrel. We used car wax as a release agent. It was blue and that made it easy to see where you put it. The bedding compond of choice for us was Micro-Bed. It was made by the Micro Sight gun sight company. I think they are gone now but it sounds like Accra-Bed might be the same stuff. It smelled like a Phenolic Resin compond. We would relieve the area around the recoil lug and the tang screw but leave the rest of the wood in order to locate the metal in it's original position. If we were making a stock for the customer we'd usually buy a semi-inlet or take one of ours to a duplicator and have it turned then add any custom touches or use plastic wood on a stock to mold a model for duplication. We'd inlet to proper debth then relieve the areas to be bedded. Once we were down to the final ten percent of inletting we'd apply "Inletting Black" to the action, then using "Inletting Action Screw" as a guide we'd very carefully set the action into the stock and tap it with a rawhide mallet. lift the action out and remove very, very small amount of wood using very, very sharp wood chisels or scappers. The "Black" would be applied with a shaving brush every time the action was removed from the wood. It also had to be thinned with oil so that it was not so thick as to give a false reading. Typically, on a high powered rifle we'd bed the areas mentioned and the chamber area of the barrel. This method was very successful. I served a one year apprenticeship then work for that shop until the owner decided to move to Alaska and only one rifle ever came back. After we verified that it indeed would not group we called Douglas and the asked us to ship the barrel back to them for analysis. It turned out that when they profiled the barrel they got the breech and muzzle ends mixed up. This is turning into a long post. Sorry, but how else do I get there? Adding pressure to the forend is something that Remington used to do on their wood stocks. If you ever pulled one apart you'd see a bump machined into the forend that apllied upward pressure. I was told (I think it was at a Remington seminar, but not absolutely sure) that it was about twenty pounds of upward pressure. The problem is that wood warps, so twenty pounds today might be twenty five or fifteen tomorrow. Guy's would bring in the previously accurate rifle that no longer was all of a sudden and we'd bed and free-float then it would be accurate again. Of course it could be the crown too and there isn't always a way to tell without some fancy equipment. For finishes we used either True Oil, hand rubbed mostly then sanded and polished with automotive white rubbing compound, or we'd use Deft's spray on Urathane if areal "shinny" finish was requested. I didn't look at the youtube thing, so I can't comment, but I use masking tape on the wood just in front of the pad then use twelve inch disk sander and Opti-visors to take it down. If you look closely at most professional jobs you'll see a few thousanths of pad raised around the stock. I'm not saying my way is the only way. My mentor was trained at the Denver School of Trades in the 1960's and I started with him in the 1970's so a lot has changed I'm sure. I haven't done much of this kind of work since about 1980 but I'm currently building two .22-250's for a friend and myself. I apologize for talking too much. Waddie
-
Can I delete the reservoir tank for the gas tank?
waddiejohn replied to dharr67's topic in S30 Series - 240z, 260z, 280z
Why not go to Nisson and see if they are available. A friend who is an import shop owner told me that he just purchased a couple of sets. -
I just built one of my own design that is a bit taller than the one that are available and designed in a "Dutch Key" arrangement to set friction on the shaft that the head is welded to. I can put a 460 Ford engine on it and turn it to any position without having it swing around. Waddie
-
Actually it wasn't a Mr. Gasket, it was a Purolator, model Pro 59SV. The package says it is 6 to 8psi, 32gallons per minute. I didn't use a regulator and have had no problems at all. It has been on the car about one year now. I paid about $70.00 for if I recall correctly. It was in that neighborhood anyway. Good luck with your ride, Waddie
-
CKOLANDER, I think you've spent too many winters in the upper part of the COUNTRY. The rest of you wiseguys are funny too. Thanks for the chuckles. Waddie.
-
I bought a Mr. Gasket pump at Auto Zone and tied in where the old electric pump was at and eliminate the mechanical. I've had zero problems and have done this on two cars now.
-
dual weber 32/36 DGV downdrafts verse SU carbs
waddiejohn replied to zedsn's topic in S30 Series - 240z, 260z, 280z
Hey, me too. I've got the carb's, rebuild kits and manifolds and my S.U.'s are still good as well. Anyone with experience please respond. -
Slown280z, where to heck is lower arizona? Waddie
-
Great tips and good stories. Thanks, Waddie
-
I do this one of course. Dodge Trucks.org , Factory Five Racing and BJ's Tombstone History Forum. So four is all I do right now.
-
I like to keep my shop pretty clean and to that end I mop it once or twice per week. There is always a dull film on it however and it looks dirty. It is a painted concrete floor and I mop it using Simple Green or the Zep purple stuff and sometimes just plan water. Results is always the same after it drys. The film wipes off, but it is a 1200 square foot shop and I'm not going to wipe it by hand. So, I'm just curious how others do it or am I just too picky. Thanks for any replys I might receive. Waddie
-
talk to me about milling machines
waddiejohn replied to grumpyvette's topic in Fabrication / Welding
Maybe I should not be bringing this back to life, but I've not been active lately and saw this thread after tuning in again and trying to catch up. I'm surprized that nobody recommended using IPA for maching Aluminium. It keeps the material from galling and welding itself to the cutter and provides a very nice finish. -
They may be photoshopped, but they resemble the Jag XJS.
-
Amen to that ezzzzzzz. I've seen a couple of those chuck keys go flying and I'm always on a friend of mine about it. When I was in my apprenticeship anyone who did this had to buy everyone in the store a coke. The apprenticeship took place in a gun shop and could get pretty crowded during hunting season. Also keep long hair tied back, long sleeves rolled up. No jewelry, no neck ties and wear snug fitting clothes with shirt tales inside your trousers. I got my shirt tale caught in a lead screw once and was very lucky to reach the off switch before it chewed me up. It did pinch my then much smaller fat roll though. And, don't forget the safety glasses. I know I sound like and old man, but there is a reason for that. Old Waddie
-
John, I think you should write a book. You are a wealth of information. Thanks for sharing. John
-
Thank you John and Monkey. That's good info for me. Modern gun steel as you know is Chrome Moly and I sure don't need to induce fractures. What is HAZ? I've never heard the term. I've been living in the sticks too long I suppose. The 3 1/2% Nickel is suppose to be great for guns and blues nicely. I've not tried bluing it yet but will try that soon. Thanks again, John
-
Well, like I said, In this case at least the 316L worked great on high carbon steel welded to stainless. The guy that put me onto this worked for a big name mechanical contractor locally and said that was about all they used on their stainles plumbing systems and welding dissimilar metals. I'm not saying it's the only thing out there, just that I'm very happy with the results. Happy welding, WJ
-
Geez, it's only 80 degrees in Tucson and that awful sun is bearing down on us out here.
-
Look at my new toy...Drilling Milling Machine
waddiejohn replied to jerryb's topic in Miscellaneous Tech
I would clean it as best as i could with a good solvent, paint brush and wire brush and compressed air. Then I'd dismantle it and clean out what remained. -
A friend of mine wanted me to put half cock notches on a set of Ruger New Model Vaqueros in Stainless Steel for his mounted shooting competition revolvers. To do this one must weld up certain parts and machine or file them to a different configuration. I TIG'd up the hammers using a 3 1/2% Nickel Steel rod. The flow of the weld puddle was not as good as i'd have liked, but I put the parts in the mill and machined them to the configuration I wanted and decided they were acceptable, but could have looked better. Next was the cylinder latch. It would be more difficult for me given the way this rod flowed. I finally got the part to "pretty good" but not what I'd like. I have a day job at a high tech company as a machinist and the plumber there is always welding up S.S. tube and pipe. I notice that he used 316L and asked him about it. He said it was all he used for stainless or welding dissimilar metals and gave me a piece to try. He made a believer out of me. I welded a piece of flat spring raw material to the thinest portion of the cylinder latch. Approximately .050"x.100" and that metal flowed exactly the way I wanted it to flow. There were no hollows where the weld began and ended and the part came out beautiful. I don't know if this will help anyone out there, but it might. give it a try
-
Congrates on the new toy. It's sure cool to be able to play with that stuff and opens doors for extra income too.
-
I like a Corgie mix myself. Corgies legs are so short they look weird, but the purebreds are really nice little dogs too. They are protective. Aren't so hyper that they bark all the time and they're smart. They do like to get out and run though.
-
You all have pretty much convinced me not to buy the thumb actuated amptrol. I appreciate all the feedback. John C., what do you mean by " set the machine into two step ". All best, JD