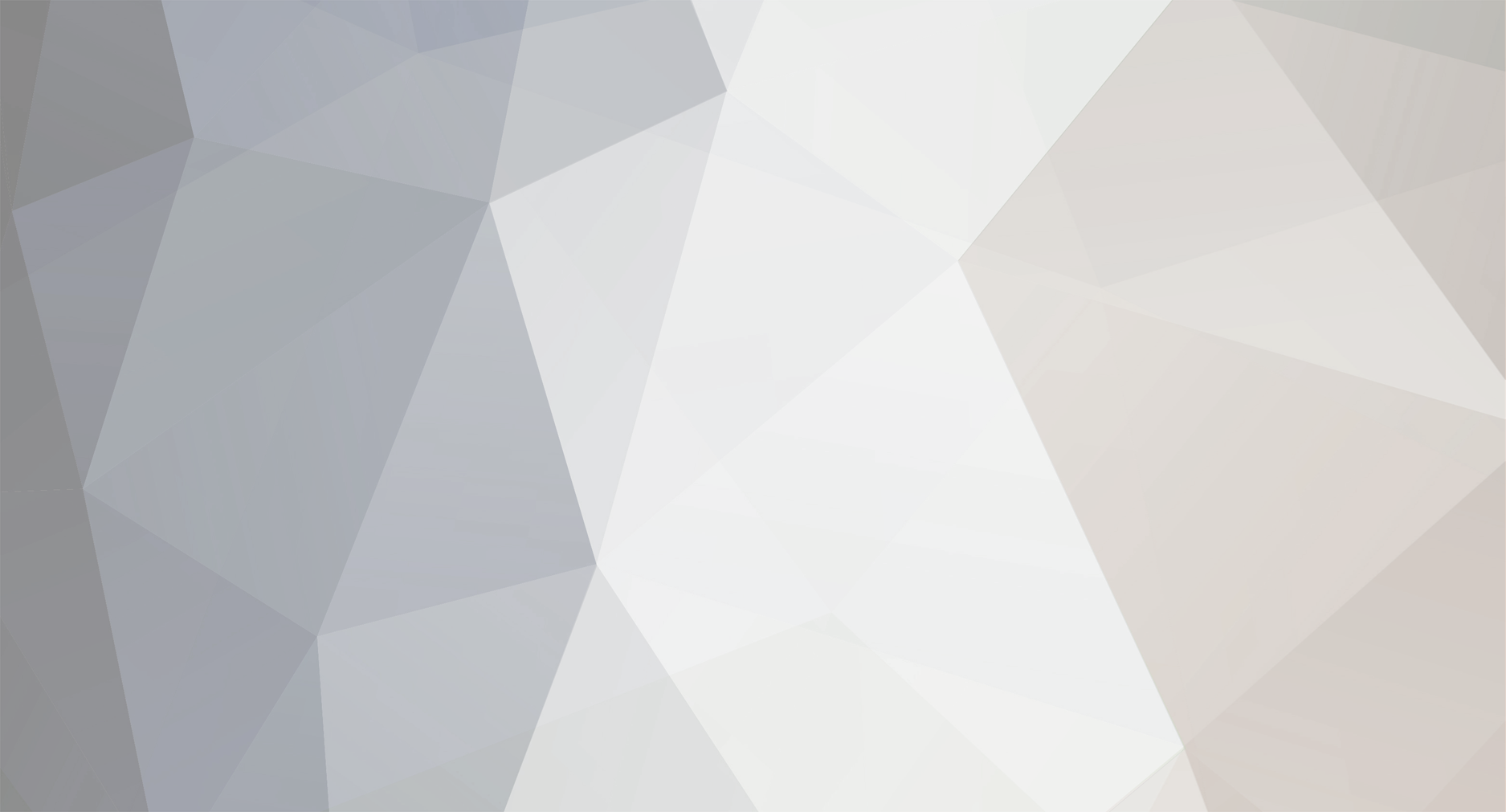
jeffp
Members-
Posts
595 -
Joined
-
Last visited
Content Type
Profiles
Forums
Blogs
Events
Gallery
Downloads
Store
Everything posted by jeffp
-
The yellow/white wire goes to the (igniter) power transistor. The wire comes from the ECU and is the trigger wire for the power transistor and coil. The voltage you have mentioned is along the lines of what you should be seeing. However, the voltage is a pulsed trigger, so the voltage will not be constant, your meter should flutter up and down as the pulse happens. The best way to troubleshoot it is with an oscope, that way you will be sure you are getting a pulsed trigger, and not a dc voltage that does not change. The power transistor is a robust component, and the only way you will blow it up is to wire the transistor incorrectly. I dont have the harness in front of me, but if memory serves me correctly, the black/white wire is the switched 12 volt feed wire and it goes to the top of the connector, the yellow/white wire is the second wire to the transistor. Check the black/white wire, to make sure that when the ignition key is in the ON position, you have 12 volts on the wire.
-
You need to get the comp pan if you want to save your engine. That was one of the first things I noticed with my car when it was under heavy acceleration. The oil pressure would fluxiate, not good at all.
-
Try Rebello raing, I think dave has a supply, and if not then MSA will have on I believe.
-
Unfortunately, while testing the engine, and tuning it, the engine started surging under power. I waved the opertator off to shuit the engine down, and he did, the bad part is that just ats the engine was coming back down to idle, the cam let go. Not a good sound to hear, and I verified that the cam sprocket bolt came lose. I have no one to blame but myself on this. The screw up took out no less then five valves when it happened. The lower rotating assembly is fine, but I have to fix the head now. That is in the works, and provided the valves can be sourced quick enough, I expect to be up and running here in a few days. So some advice on building your engines, when you start on a part of the engine finish it completly, and as Tony mentioned that we did in the military, the bolt marking goop is a good idea to ensure you have secured every required bolt. Again, I have no one to blame but myself on the matter. I built the engine so it was my screw up. I had to start and stop start and stop due to problems with my daily drivers, and just to much going on at the time. I could not dedicate the time I needed to ensure I had all of my ducks in a row. Fortunetly, the lower rotating assembly is good, and I am quite sure it will not pose any problems. I did the bottom end at one time, no start and stop in between, and I did the cylinder head the same way. When it came time to assemble the engine, I had very little time to do so, and I did it in parts, seems I had a little difficulty keeping track of the work completed. There were three errors I found, the cam being the damaging one, but the turbo outlet was not tightened, Tony found that, I readjusted the rockers, and one had excessive lash, and finally to round it all of the cam bolt came lose. Expensive lessons for anyone, so we will see if I can get it back together by the 24Th. Some of the data I did get before I destroyed my valves, was looking very promicing for the heat control of the engine. The testing is not complete, but I think the overall improvements are very impressive.
-
I am not obsessed with EGT's really. What I was concerned with at the time, was the temp gauge in the car, and the glowing exhaust turbine housing. That was my indicator my EGT's were getting to high. The thing is that the engine, EVERY ENGINE, has the sweet spot where it likes to run the best. That is what you are tuning for at the end of the day. To simply setup a fuel map based on what others have done and calling that good is just plain STUPID. As Tony mentioned that may be a good place to start, or it may not, every engine is different, and to be technical, you could tune perfectly one day and the VERY NEXT day have to dial the tune again because of the external variables like humidity, temp, to name two. The fact of the matter is that when you build power you are going to create heat, no matter what you do. True you can run differently with the various fuels that are available, but for the most part, you will run hot. I don't really care about the EGT's if the engine can sustain that temp long term, and as most of us know the stock high hp L28 can not accomplish this requirement. That is precisely what I have been doing all of my R&D on, to get the heat to a manageable level that I don't melt down my engine in the process of having some fun. The other thing I am going to try is to use an engine dyno, NOT the car dyno. I am wearing out all of my running gear components on the dyno and that isn't good either. I will have the ability to control the engine much better and get a very good tune to run on the dyno, and then check how it has changed in the car. I am really hoping that there will be little difference once in the car. So this is my first go around on the engine dyno, so if it turns out like I believe it will than I will never put my car on the dyno again for tuning purposes. I will have my results here in a few weeks.
-
To dispel all the confusion regarding the stock turbo, turbo automatic, and standard pumps. The standard pump is a 35mm pump gear. The turbo, turbo automatic pumps have the 40mm pump gear. I have never looked into the KA pump personally, but it is suppose to be the same as the turbo pump. The other differences are the springs, no problem; you don't need to go to all of the trouble of sourcing new springs, just shim the current springs in the pump with a spacer to compress the spring more. A piece of sheet stock cut to fit in the spring cap works out very well. I think I used about a .100 thick piece of steel to shim the springs. Now if you have exhausted all of your options, there is one other source for pumps. Millings oil pumps are an excellent replacement with benefits. The standard pump is the M105 pump (35mm gear) The turbo/auto pump is the M111 pump (40mm gear) The housings are cast iron, so they can be easily blue printed to improve the idle oil pressure. Either way, the oil pressure @ idle will be low, typically 10psi. I blue printed the pump and was able to increase the pressure to 15psi @ idle. Good enough for me. The millings part is about $75-80 USD and are readily available here in the US. I would suppose with this global market you should be able to source them in your country as well. So that is just one step in the quest for good oiling for the L28, now to the oil pan improvements for cornering and road race conditions right Tony? It suffices to say you would really work an accusump setup on a bone stock oil delivery system for the L28.
-
I just got done with this install. I neded to get a new manifold, as the SFP part rused very badly, and it would NOT stay flat. I started in on a stock manifold and worked the part extensively. The wastegate was changed to a TIAL 44mm part. I was able to get a 1 3/4" pipe in the bottom of the manifold, just under the turbo flange. I then routed directly to the downpipe. The install was not easy, but the pipe welded very well, and I was using 316L for the waste gate pipe. I was even able to get a 1 3/4" flex joint in the inlet side of the gate. I will have to post some pictures to my web page of the install. The manifold is out for JET-HOT 2000 (Black) and will be ready fo install after I get it ground flat. hat appears to be the weak point of the header, and I believe that is why they came up with the EURO header in three pieces.
-
I haven't talked to Derek about this part. I think TonyD did speak o him regarding this part and he gave Tony a reference to a company that could do the work. I called one compant and they wanted WAY TO MUCH to make the part. I would really like the part to be made in SS but I am not going to pony up 8-15K to have the molds built. That is what I was quoted, so the header sits in the garage in the hopes that I can find a place that will do the job for a reasonable price. I am not a cast/mold guy, but what they wanted wqould pay my salary for a few months. Regardless, that is to much money for me to spend. So if there is a company/person that can do the work without me paying for their kids private school, and for their mercedes, I will go for it. I am QUITE sure this part will run at least 650Hp. I have run that much with the SFP header and the tubes are smaller then the EURO part. I think this would be one of the best options any turbo application could run for the cars. Anything more would require a custom setup exhaust, but how many people are in the 600-700hp ranges? I don't think to many are that high in hp. So any help would be appreciated.
-
I have looked into the Evans glycol and the thing that bothers me about it is the heat transfer coff. Water has a cofficient of 1 Evans is about .78 or so, and standard 50/50 antifreeze about .82 so water is the best coolant. I don't really know of anyone that has data on a high hp engine with this stuff, and @ 25.00 or so a gallon, I am not confident it will help my engine all that much.
-
I had the stock single piece manifold on my car and it ran 500hp. I needed a external wastegate with the GT35R turbo, and that at the time was a problem for me. NOTE: I was not aware of the fact that the stock turbo manifold was CAST STEEL! I bought the south flordia performance manifold and it looks very much like the one in the pictures. So first thing, mild steel will not work! I reworked my manifold THREE times and still got warping. I made the manifold three pieces, like the EURO manifold, and it still warped. The center section that picks up the 3 & 4 had to many pipes attached in to small of space, so it continued to warp, and the turbo flange warped as well. This happened THREE times to me. I ran the part, and since it was high temp coated in SILVER, the max temp was about 1200 degrees. Well the first thing that happened was the silver coating started coming off the manifold, not good, but workable. The problem that made me trash the part was that in the process of coating the outside of the part, they decided to coat the turbo outlet area as well to cover up the bad welding. Well, it worked for a time, then I blew up the car and that really cinced it. But, what was happening is the coating on the inside of the manifold started chipping away,,,,,, RIGHT TO MY EXHAUST TURBINE WHEEL! NOT GOOD! So I started in on the Euro manifold, and BTW it has a larger tub section then the SFP manifold did in the first place. I worked the manifold, welded it up, ported it out and was trying to get it cast in 316L or so. That did not work, as the quote was to the tune of 8000.00-13000.00 to do the molding. No go on that one for me, unless you know of a shop that will cast the part cheap. Now, I am back to the stock manifold again. I think the tube of the part is just about the same size as the EURO manifold, which is bigger then the aftermarket part I spent, all total about 3K on purchase and rework. I did all my port work on the stock manifold, welded the sides of each outlet(except the center ports) and was able to cut a 1 3/4" hole in the bottom of the manifold under the turbo inlet flange. I am running a TIAL 44mm unit now. So as far as the manifold is concerned. I am thinking I am going to get better flow then the SFP part, and about the same flow as the EURO manifold. I know I was able to do 658hp with the SFP part, so I am thiking the stock ported manifold really is a better part then the SFP part, and not as good as the EURO manifold because it is a single piece part, and is subject to warping more easily then the thre piece EURO manifold. The EURO three piece part was designed spicifically to stop the warping. So if you know a shop that cast parts at a good price then let me know. I will run the EURO part and have an excellent part for all to use. Whatever the case is, the part has to be standardized and built from the stock part locations, or most downpipes that have been built will not work.
-
AC Delco/GM Alternator Swap Part 2 - CS144 Installation
jeffp replied to ktm's topic in Ignition and Electrical
I have since decided to go with yet another upgrade for the alternator. This unit is made by Penntex out od Texas. The alternator is mede her in the US. I think this just may be what I was looking for in the first place. The differences in the alternators are for one date of manufacture. The other is the r4ectifier set for each unit, and as you mentioned the rotor. Also the 244 unit has two cooling fans, one in the front and back. Realistically, you are correct 140Amps should be sufficient for welding LOL, or to power your car easily. The problem with the Alternators are the CURRENT OUTPUT @ idle, and that is where you run into problems. Ecah alternator is rated at X amount of rotor speed for that unit. You will note the differences in the rotor speed of each unit for the specified output current. The smaller units "generally speaking" will require a faster rotor speed to get the unit into the higher current ranges that we would like to see at idle. Easier said then done. The other thing you will notice is that the larger the alternator current output, "Generally speaking" the more current it is able to provide ast a lower rotor speed. So that was my criteria for the 244 unit "and it is fully upgraded with the stator, brushes, Diode rectifier, and finally the external regulator I installed. So I started with a 200.00 part that was stated to provide me with 95 amps at idle, it did not do that. So I called and it was mentioned there was a larger stator, and better diode block for the unit. I bought those, again the alternator did not fit my needs. I changed to a 2 " pulley to spin the alternator faster. Still not quite where I wanted it. I was seeing the line voltage drop off after the alternator got hot. So then it was the internal regulator that was the problem. I bought that for 145.00 (external unit) and installed that. Still not what I wanted and it did not improve the line voltage drop when the unit was hot. So in a nut shell, the unit would not do what I wanted it to do after spending 500-600 total on the install and upgrades, for this one unit it still was not quite good enough. So what to do now, lower my line voltage to 13.8 that seemed to work, but again I am where I started. Total waste of money in my opinion. True, I have somewhat of a unique situation with my car, so like I mentioned somewhere else, a 200 amp unit is not required, however if you are looking at idle current, the the only things you can do are spin the rotor faster, and that helps. The second thing you can do is get more robust, higher current devices in the unit that will not get so hot, and finally increase the windings of the stator. I did all of those "upgrades" and still could not maintain 14.2 volts @ idle when the car was fully warmed up. So for me this was a total waste of money, and my time. Take a look at the new unit and see what you think. I built the bracket and I think that part is about strong enough to lift the whole car LOL. Do you have any ideas that would make the page links better? I do have the mouse-over funstion on the page links. So if you leave the mouse on the small picture the title of the page will show, and you get the page title on the explorer lower tool bar. Anyway. I really am interested in the performance of this new unit. My goal is to maintain 14.2 volts under any condition, well within reason, so if I can run the car, turn the lights on, and at that time an electric fan, and electric water pump. I have since went away from the electric water pump for some heat testing of the cooling modifications I have made. This alternator was NOT cheap, but if it does all that it says then worth every penny. This has been an ongoing modificaton for me, very costly to test all of the different parts and all the upgrades, will it never end LOL. -
I wish I could have gotten to this post earlier. The 2mm HG can be modified to the thinner head gasket. You will notice that the gasket is a makeup of multiple layers. You could have removed the eye-lits from the gasket and gotten the thickness you wanted. The issue of a 91mm cylinder hole. First off the sealing ring is 90.5mm plenty of room to seal the water, oil and combustion chamber. Not a problem. Second, 15psi of boost is alot of boost, so depending on your turbo charger it may be to much or ok. I was able to run on 15psi of boost on the MSA gasket. The felpro gasket died the first time I went to 15psi. The whole gasket, every cylinder let go, and tracked across 2&3. I run a gt35R turbo. The metal gasket will do the job, but the thing to keep in mind now, is that the damage to the engine with detonation will be the piston skirts first (for stock pistons) and the rings next, then the bearings. So what I am saying is that the metal head gasket will not blow, but everything else will now.
-
So you are looking for a "they said" answer. What you really should be doing is running your system to make that determination. You will get a number of answers, but at the end of the day you will need to test your specific application. Fuel edlivery is not an area that is left up to guess work. Install the pump and test the flow of the system. You should be able to check the low pressure and the high pressure, and more importantly, will the system provide the fuel you need at your boost level. You can calculate the required flow at the required pressure you will run. Anything other then testing the system is in my opinion just guess work and you get what you get.
-
Aeromotive 13101 EFI Bypass Fuel Pressure Regulator This is a rising rate fuel pressure regulator. I have used this part and it has worked very well to 650hp.
-
Yes the 11:2-3 AFR did make my turbo exhaust turbine very hot. As for the engine, it seemed to run about the same water temps. I was reasonibly sure the excess fuel was igniting in the turbine housing. I concluded this when I started tuning for 12:2-3 AFR's the turgine was not as hot as before. The power was up and the engine sounded better, smoother through the RPM range. A quick test is to look at the exhaust turbine itself. If the wheel is a white/crusty look then the engine was lean. If the wheel was a sooty black, then it was rich. The brown crust, like rust is a good burn. Flow will follow the path of least resistance, so if your exhaust back pressure is 1 Lb less then the intake, guess where it goes. So that being said, it sufices to say this is the ideal condition for the engine, exhaust back pressure less then the intake pressure. Another thing you can check, I was walking behind the car once on the dyno at JWT. The car was running around 11:1 and when the exhaust hit my face and my eyes, I imediately started sneezing like crazy and my eyes were burning a good amount, but the one thing that let me know exactly what it was is when the exhaust hit my face, it started to burn. That was nothing less then fuel dense enough to make me notice it on my face, and it really smelled like gas as well. The car was hotter then hell and had to cool down that time. I think it is enough fuel getting ignited in the scroll of the housing to create the additional heat, and the turbine housing was glowing. I have also seen a lean condition, and that appears to happen, or have more effect in the engine, and not so much in the turbine housing. Lean just overheats the pistons, and you can see that by looking at the color/texture of the pistons in the quiench area of the part. You wont see near the heat in the exhaust turbine housing with a lean condition, you destroy the engine, and the water temp will be the indicator of that. The O2 readings, well raw fuel will not trigger an O2 sensor, what the sensor reads is the PPM O2 of the sample taken, the sensor then makes a calcuated measurement of the O2 and compares that to "free air" or normal breathing air, unless you live in OC then you get to become a human air filter, to make the calculation. Convert that into what we know as AFR's or in reality it is a PPM measurement. anyway
-
From all of the information I have been able to get, there is still some reasonable doubt as to WHAT EXACTLT is happening in the cylinder head with a high hp engine. I guess it is a situaton of I have not personally observed the occurance. I know that Electramotive when they were running the car did X and that seemed to take of the heat issues with their builds, so it would also stand to reason that they did discouver the problem, but I have yet to see any REAL imperical data on the subject. So if I was REALLY wanting to SEE the problem, I vould work a head and install some optical windows in specific parts of the cylinder head and physically SEE what is happening. I don't think I am going to go that far with this. I am going to follow what electramotive did with their engines and see what happens. IF I am required to do additional testing then that is what will be done. So for now here is what I am working on: 1) I have looked at the cylinder head, and YES there are points of interest that I will monitor for data. One of the big ones is what is happening to the water/coolant @ the exhaust ports of the head? When you look at the cylinder head, you can see that there is little coolant flow in that portion of the head, and thus the reason/rationale for the bypass flow external to the cylinder head back to the radiator. I have noted an improvement with the #5 & # 6 bypass on my last build. Did this help with high HP? Yes it did, the engine took longer to get hot, and it cooled down much faster. On the road though, on a hot April day in traffic on the freeway, the engine would stay cool, but again as soon as I introduced a load to the engine (A/C turned on) the engine would over heat if I let it. So my first change made improvements but did not solve my problems all together. You need your A/C LOL, it is a good basic test to check the cooling abilities of the engine. I have not reached the point that I can run the A/C in start and stop traffic. 2) the cylinder heads and blocks were designed by different people! If you look at the head you see very good water paths for the spark plugs, not so good water paths for the exhaust ports, and that is where all of the heat is being produced, less the combustion chamber. Improvements in this area of the head has been addressed by me and I am in the process of testing this change I have made. I just need to get the engine back together, but I have gotten side tracked with a few other areas that have bothered me like fuel delivery. I have upgraded that system as well to 1/2" line and a new magnaflow external fuel pump. I am almos done with the setup, but I was getting a vibration that ran the whole length of the fuel lines. I have to change the pump mounting configuration and change some lines from SS to rubber to insulate the pump vibrations. That will be completed next week. 3) I took a look at the engine blocks, N42 and F54 blocks and noted some SIGNIFICANT changes in the number, placing, and size of the holes in the block. I have had information from electramotive, and from my eaxperience with the HKS laminate gasket. I compared these gaskest to the stock gaskets, and I can tell you the stock gaskets , and the felpro gasket SUCK! the gaskets cover a number of the water cooling paths to the spark plugs, and more importantly the exhaust ports. I have made changes to the F54 block I am going to test, and if all works out well my mods will be the winning ticket along with some of the other mods mentioned here. 4) I am going to run the LD pump, and a higher system pressure as well. My testing will be with water and water wetter to stop the coorosion of the steel in the negine. Also as a NOTE: check your rust in the block, if you have more then a light rusted coating in the block, I would highly recommend a good hot tank to remove the rust buildup on the cylinders specifically, and then the block itself. Rust is NOT a good heat conductor, and it will cause problems with heating. I have always thought this may be some of the problems with a stock engine that will not stay cool. Also, if you hot tank your block, make sure their tank has the ability to remove the rust, seems now days here in CA, gwetting a REAL hot tank that works is not to easy because of the chemicals used to remove said rust are noe outlawed to use without, you guessed it a costly permit and most shops wont deal with the state in that respect, so what we get now is a fufu hot tank. I found a place in Santa Ana that will do it for ??? $200.00 that is correct 200 dollars because of the chemicals used to remove the rust. Hell the last tank job I got did not remove the rust, and it did not even remove the pain on the block, total waste of time and money for that one, and so goes again my education of the way things are now. You use to get a hot tank fo 40.00 and the block was clean, not anymore. 5) I am going to run a better flowing thermostat, there is a flow restriction with the aftermarket thermostats from MSA and others, you are much better off getting a stock Nissan part at you desired temp if they still sell them that way. The flow through hole is bigger on a stock thermostat then the aftermarket parts. I tested this part, it is a 160 degree part and it can come with the bypass or without the bypass. 6) mods to the block along with a good deck flycut. I will use the laminate HKS gasket as it has more of the cooling holes then the stock gasket. I also milled the gasket in specific areas to flow better. I drilled two more holes in the block for flow around # 3 & # 4 along with some other mods that I don't care to discuss at this juncture. 7) in the future I have been working on a new head gasket that I will be testing later this year to verify a new type configured gasket as a replacement to the HKS part. That is still in the works, so that has been yet another diversion to getting my engine built again quickly. So that is where I am with this issue. I have a number of changes that I think will be nothing but beneficial, but I need to complete my testing before I outline any changes or recommendations on the matter. I think I have this problem fixed, but I need to get my proto engine completed and give it total hell to get the results of all my changes. Good info guys, all of which I seem to have directly addresed for this next build and some of my own non disclosed changes. I don't want to feel responsible in any way if someones engine goes south because of XXXXX I will not get involved with that. On a sideline topic, the CSR water pump: I had this designed to stabelize the water flow in the system, regardless of the engine RPM, the pump will operate and pump 24 gallons a minute @ 4psi pressure from the pump outlet. Pumping contained within the engine can then be bumped to a much higher overall system pressure, yet still maintain the overall flow rate of 24 gallons per minute at any engine RPM. The pump has worked well for me, but with all of the mods I am doing I am going to run the LD pump for comparison to see what I get. I like the pump, it has many things that can be done like circulate the water after the engine is dhut down, very beneficial on the dyno. In fact that was the ONLY way I could run so many times in one day on the dyno. I had the engine cooled down in about 5 minutes and was ready to go again. The one thing to KEEP in mind is the current draw of the pump @ idle, most of the stock alternators will heat soak over time and lower the system voltage. That is bad also, you can never set the tune where you want it effectively unless you have a good stable voltage potiental to the injectors, and the larger you go on the injectors the more critical the line voltage becomes. TOTAL PITA! and costly for me at this point with 4 setups tested on the car, well three with the last setup also being tested for this next buld. I just need to get all of the ground work completed and do the testing. Testing will be quick and I wll know if I wasted my time and money for all of these new changes, they aint cheap.
-
I guess I should have worded it differently "I Mis spoke LOL LOL" What I was trying to get across was thyat the rich mixtures are just as damaging to the engine long term on the dyno. The 11:1-5 AFR's are really bad in my opinion. The excess fuel going out the exhaust, on a turbo car has one more chance to be ignited, WHERE YOU ASK? In the exhaust turbine housing! That is BAD! Take a look at the picture I have on my webpage, the turbine housing got VERY hot and in my opinion the engine started going into thermal run-away. In fact, I will say that if you run the engine to 110 degrees C on a pull like I did ONE time, you just may find yourself with a bad valve seat around #4 in that area. I put that car through FRICKIN hell that day, at least 25 pulls with full power. So it cost me a little, but I was able to figure out along with Tony that the richer AFR's in the 11 range up to peek torque only to serve to make the engine hotter then it would run with a leaner mixrture. On the N/A car, the AFR's can be much richer then they need to be, and the waste is in the exhaust, no big deal, just bad fuel economy, but you take that same exhaust and run it through a very hot exhaust turbine housing and you start to run another somewhat of a second engine (the exhaust turbine housing) and that IS BAD.So the excessive heat is bad for the engine (cylinder head) and the pistons, depending on how they were honed to fit the cylinders. I have pictures of one build that the engine got very hot, and the pistons expanded about .0005 with the heat that left a nice 1/2" wide scrape mark in every cylinder. Was it enough to make a difference, in reality no, but none the less that is what happened to that build. The car got to 270 on the gauge and stayed there, the oil went to 130 degrees C and stayed there as well. I was out in the middle of the desert and really had not other alternative but to continue on and hope for the best. The next build the pistons were a little looser in the cylinders to provide the space for the pistons to expand and not cause problems running that hot for short periods of time. Anyway, I'm all over it, I must find the correct solution to keep the engine cool, and I think I have, but testing will tell all. If the temp gets under control to my satisfaction with the modifications to the head and block I have made, then it will be a goal of 800 Hp, and guys (the nay sayers) I will run the rpm's to at least 9000 rpm's in that process. So think about that, I don't think the honda boys will be able to compete if I can get the car to hook. anyway
-
I was running C16 race fuel at the time. I have only tried to run (in CA) 91 octane pump gas with methanol, I have to say the methanol and pump gas got me some really impressive dyno numbers, and theengine stayed cool. Back to the race fuel. I like Tony mentioned was tuning for the mid 11 AFR's and that was to rich for the car. The EGT's went out the roof, in fact I took a picture of my turbo and the whole exhaust turbine housing was glowing bright PINK (the jethot blue turns pink when the base metal gets that hot) So with some additional tuning, we realized the engine ran cooler and made more power in the 12.2-4 AFR range. Also, as Tony mentioned we were able to lean out the engine some more AFTER PEEK TORQUE! That is the key, when you are coming up on peek torque, make sure you have enough fuel or it will ping, well KINOCK loudly. Also, the dyno testing will be little help to you in the car, but rather get you close, and even then it is schetchy. I have not completed ONE dyno run or tune time that I did not have to readjust after the dyno tuning. So my last attempt to do dyno tuning will be on an engine dyno, no car, no distractions, just engine tuning. We will see how that goes after the engine is installed. You do seem low in power for your boost levels, but that is dependant on the turbo and the engine. So check out your application to make sure there is not something hindering the power output. Also, the comment was made that you would pick up the power with a better tune. Well even if you are rich like you are, you will only pick up about 20hp total from what you have now. Check the cam timing and make sure that is correct.
-
I realize that there are a few people who advocate removal od the air purge setup on the cars. The 280zx car really should have the system in place and working. The purge canister not only removes the raw fuel smell, but more importantly it pressurizes the fuel tank. Not such a big deal, except for the fact that the zx system has a gravity feed to the inlet of the fuel pump. The positive pressure helps to force the fuel into the fuel line and puts a slight pressure on the pump inlet. The system aides the pump fuel delivery along with the emissions stuff. My recommendation is to keep the system and work around its location with your intercooler setup. The delivery may work good or it may not, but you will never know unless you have the ability to monitor the pump output, not just the fuel pressure, but also the air that could be pumped along with the fuel, that is bad, you will never be able to tune the car and it will not run consistantly if that happens. I am all for pressurizing the fuel tank, removing the slight emissions the system provides. Run -4 steel braided lines to and from the tank and it will look really good. I did this upgrade on my car and have never had to mess with it again.
-
I don't recommend the 84 box, but rather the 88-89 ox for your conversion. The 84 box doesn't have the features the newer unit does, and the 88-89 box uses the same connectors as the turbo harness.
-
That is the book.
-
I took a look at the calculator and it to was not quite right for my known engine output power. The thing that surprised me was that the line for my power and compressor map were off as well. I did not have to run 45psi of boost to get 650 crank hp, more in the line of 22psi. I did all of my calculations from John Lawlors book and that got me to where I wanted to go. You will have to use a number of different calculations, but for the most part it is very accurate. The thing about a turbo size question: 1) what is the static compression ratio. 2) what is the swept volume of the cylinder. 3) what total compression ratio do you need to make that cylinder reach you hp goals. hp/6 cylinders= power of one cylinder. 4) once you have the compression ratio, then you need to calculate the total air required. 5)with total air required, static compression ratio, final compression ratio calculated, you then need to calculate the pressure ratio you will need to make the cylinder produce X amount of power to get to the target compression ratio to make the desired power per cylinder. 6) with total AIR required, and pressure ratio required, then go to your compressor maps and select the best fit turbo. Then comes the give and take of how well the turbo will spool, when it will spool, what is the efficiency of the turbo at your desired hp and rpm range, and go for it. If the turbo manufacturers can do this and build turbo's all day, why cant we do the same thing? I mean required air, based on the cylinder size and swept volume of a cylinder based on all the required givens to calculate hp per cylinder is all you need to make a very informed decision for turbo size. Guys this stuff is not magic, it is calculated and you would be very surprised how accurate it is. Play with the formulas that are available to you and figure it out. Sure a quick calculator is nice, when they work, but it is not required. anyway, I think I would be WAY over 650 crank HP with 45psi of boost.
-
I was looking at the picture of the intercooler and noted that the flow through the core is 90 degrees of the end tanks. Did you choose this type of cooler so that you could run the inlet and outlet on the same side? I took an all together different flow path for my setup. I also had spearco do my cooler, and I have to say it looks like their quality has gone down since they have been bought. So I got the SP-209 core to start and had the tanks welded to the ends. I did send them a drawing of how I wanted the tanks made. The core tubes run horizontal instead of vertical with the end tanks on each end. So air goes into one end of the tank, through all of the core passages, and out the other end. I did have to run a longer discharge tube to get back to the intake inlet, but it is in front of the radiator and is not subject to heat soak from the engine. To me that seems like the better option for the intercooler. I think there is a better cooling effect with the longer core tubes, and flow is less turbulent in and out of the core. anyway.
-
I have never seen one of those dampers break like your part did. I did have the first damper made and I did end up replacing that part with the steel part mentioned. I had that damper installed and removed at least 5 times. I noticed how loose the damper was and started checking cranks out. I measured 5 cranks and came up with an Id for the part. I had the part made in steel. I havent installed the damper yet, but we will see how it goes. The crack on your part, if you look is right at the 90 degree angle in the slot. Notice there is no relief radious. The strength of the aluminum part was compromised because of the sharp corner. Then when the damper moved it cracked. How do you install all of the components on the snout? Do you use the oil flinger washer? I have had nothing but trouble with one installed. Like Tony said, I use a standard Volvo washer. I turn down the OD and use the KA bolt, or the 81 Turbo bolt. You do have to shorten the bolt 6mm or so. sorry to see that happen to your bottom end.