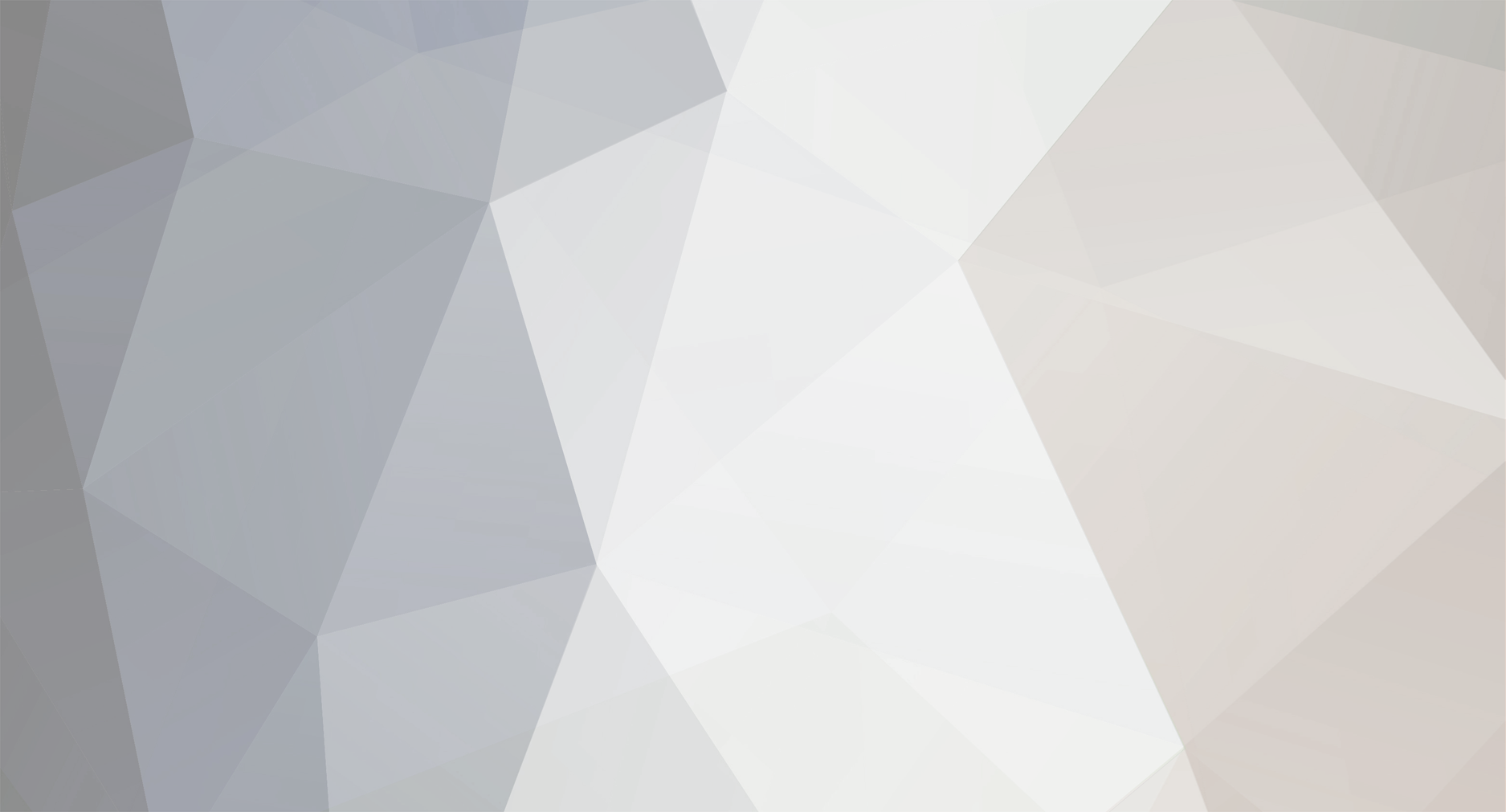
jeffp
Members-
Posts
595 -
Joined
-
Last visited
Content Type
Profiles
Forums
Blogs
Events
Gallery
Downloads
Store
Everything posted by jeffp
-
Is it alright to have my alternator wired like this?
jeffp replied to CamH's topic in Ignition and Electrical
What I ended up doing was to run a #4 wire from the battery terminal of the alternator to the starter log connected to the battery. The black/white wire nissan used was good for a stock application, but if you draw excessive current from the battery the wire and connectors cant handle the current draw. So I left the stock wire connected and added the large wire to effectively bypass the stock part of the system, but it is still functional. A good standard nissan relay, if used will work just fine, or a simple wire from the ignition switch will work also. -
Is it alright to have my alternator wired like this?
jeffp replied to CamH's topic in Ignition and Electrical
The way you have the field wire unswitched will not work. The car will charge like you said, but when you turn the car off the field of the alternator will still be hot. You will drain your battery down over time and may burn out the regulator. The field wire does need to be a switched connection. -
What is the fuel management? When you unplug the AFM the car should go very rich. Also the cylinder head temp sensor will also make the car very rich if it is not connected, and when you loose the AFM input I just may make the car run. Does the car get up to any rpm's? You need a good O2 sensor to see what the fuel ratio really is. The stock O2 sensor for the turbo car will work, but you will need to get it hot first. You mentioned the injectors, are the plastic caps to the injector nozzle intact? That will make the engine run like crap if the tips are missing.
-
I ran the TO4E turbo I think it was a .50 trim. I had the stage 5 exhaust turbine wheel. The cam 266 duration, 112 lobe centers 480 lift intake open 21 BTDC clises 66 AABDC and the same on the exhaust (strait up grind) overlap of 48 I believe. Stock exhaust manifold and waste gate. 8.5 : 1 compression. I wouold be fully spooled by 3K and boy what a change from no turbo boost to boosted, almost uncontrolable. I ran the car to 7K and I was doing about 475Hp with that setup. Go for the TO4E a good 3" exhaust and stock wastegate with boost controller. That is a very good setup. You guys mention stage cams like that is supose to mean anything to anyone. List the cam specifications and that will be much better. Realistically, you could run a STOCK cam and get very good results to 450-500Hp or so.
-
Has anyone ever tested their turbo AFM?
jeffp replied to thetremendoustim's topic in Nissan L6 Forum
I tested my AFM, and what I did was to remove the cover and manually connect the ohm meter to the wafer and wiper. You should have a smooth transistion from one part of the wafer to the other. The theory being that as the door opens the resistnce will scale linear throughout the total travel of the resistor sections. I also disconnected the air temp sensor (the two black wires with the spade lug connectors) and measured the resistance. Then I got a blow dryer and heated the sensor to make sure it started changing resistance. I let it cool and watched the resistance change again. That was a good sensor. You should not have any jittery readings as you open the flap, and if you hit the next block on the wafer it again should be a smooth transition across that part of the resistor. That is about all there is to it. -
Anyone know where i can pick up a Cannon intake manifold?!?!
jeffp replied to Rimal310's topic in Nissan L6 Forum
I bought the manifold a few years back and it has been sitting ever since. Give me a call @ (714) 907-6318 and lets talk. REGARDS: Jeff Priddy -
Now that I am strait on the pumps. The turbo pump is the 40mm rotor assembly. This pump is no different then the turbo automatic pump as well. I bought a millings M111 pump, it is the 40mm rotor assembly. I blue printed the pump and tightened up the rotor assembly tolerances by setting the end play to about .002 @ 270 degrees F I could go tighter to about .001 and get better idle pressure. Remember all of my measurements were with the pump housing pre heated to 270 degrees, and then I took my measurements. So Milling is the pump to get, they also have the M105 pump that has the 35mm rotor assembly. I was thinking about adding another 5mm to the housing and rotor assembly, but that will take some welding on the rotors and an additional spacer at the base of the pump. I just have not had the time to play around with that test. I like the millings pump much better as it is cast iron and not aluminum.
-
What do you guys think about a knockoff of the EURO exhaust manifold casted in 316L? I have a manifold I have been working on for my car. I had the manifold welded in the areas that I needed to remove material to get the flow better. So I have finished up the manifold, it is ported well, and should have no problem supporting at least 650Hp. The second header you don't pictured is on my car. I bought that boat anchor from South Flordia Performance. I could not keep it flat and have reworked it three times. I ended up sectioning the manifold in three pieces very similar to the EURO manifold. The unit works good now, but I want to run the Nissan part, as it is a bigger tube header then the SFP part I bought. So if oyu think a good casting of a fully ported EURO header is good then let me know. I was waiting to show the part to TonyD and make sure it can be copied in its ported shape, so if it is casted there will be no work to do on the part other then attaching an external waste gate if needed.
-
How to make autometer fuel gauge read properly
jeffp replied to smoorenc's topic in Ignition & Electrical
I am not totally sure how the gauge is wired, but if is wired this way: One side of the gauge is wired to 12 switched with ignition switch. second side of meter is wired through your resistors to the sender. The sender then makes the variable part of the resistor make the gauge move as the fuel level repositions the sender to a different resistance. So if you took one of the resistors you have in parallel and sub in a variable resistor, say a 500 OHM resistor (ten turn) then you can vary the resistance of the variable resistor to move the gauge needle perfectly over the full tick on the gauge. Then you connect say a 10 OHM resistor in series with the two resistors (one fixed the other the variable resistor) you can by adjusting the resistor in series and the resistor in parallel get the gauge to read exactly on the gauge at what level the tank is. You get accurate detent of no fuel level, to full level. The sender is the trim, or variable resistance based on the resistor on the sender. The parallel resistors will set the span of the gauge, in other words how much the gauge will swing when the sender is moved from empty to full, and the second variable resistor will determine where the gauge needle will rest when either full and empty. This setup will calibrate the gauge to the sender exactly. You don't need big resistors, a 1/4 watt resistor will do the trick. Remember this is very low current we are talking about here. The current must be very low so that there is no way if the contacts in the sender become disconnected that there will not be a spark of any kind. Sparks in the fuel tank are not good as you may already know LOL. So if the sender resistor is linear throughout ist range, you should have a very accurate fuel gauge reading. Myself I went with a DEFI temp gauge, and tach in my stock dash assembly. Both units work excellent and look as good. Now for the fuel gauge LOL. -
I did a whole gob of research on the topic because I was having that problem with my car. I ran the MSD 6A with the HVC coil and the coil kept going bad in short order. I experimented with the Mallory Volt Master II coil, nice part to this day one of the best coils I have ever worked with. (well Pre 1983 coild) I bought a Heathkit analyxer, and I built a resistor network to plug into my oscope. I used the oscope as the heathkit display was to small for me and was lacking in resolution at least for me. I ran the car with the scope going, and that is when I found the first problem to deal with, the injecton, Z31 boxes are very hard to control @ 600 hp due to the electronics and how it calculates injector duty cycle. Not to get to deep into it LOL. So I got the injection fixed at least well enough to work, not ideal, but very workable. Then came the problems with the misfires. That was the hardest thing to troubleshoot. That is when I decided the Z31 box was just to much pain in the butt to make work. The duty cycle was a minimum of 2 milli seconds charge time on the primary of the coil @ idle. The coil was fully saturated by .8 milli seconds, so the coil was getting hot, the power transistor was getting hot all at idle! The other problem was that when the ECU was spinning @ 8000 RPM's (I did this testing on the bench) the duty cycle to the primary of the coil was about 500 micro seconds. That was to short to charge the coil. So the spark was getting blown out. Yes I did try all of the standard stuff with plug gap not help. The last thing I found were the plug wire boots. I was running the blue NGK wires at the time. I tested the setup, or wires, on a test fixture the simulated cylinder pressure and the boots were shorting to ground in stead of jumping the spark at the plug. I had a number of problems going at the same time, and it wastough to troubleshoot, in fact it cost me a set of pistons. So you could say I did an indebth study on the topic. I have an additional page for everyone to take a look at if it is still there, well I just tried the link and cant get to the Article. Here is the basic link maybe you will have better luck, the article is Anatomy of a Waveform by Bill Bill Fulton good read. anyway like you said, this is not magic and proper attention is really required.
-
I have run a .7 A/R a .82 A/R and the .63 A/R turbine housing. For the street you are better off running a .63 A/R housing hands down. I was getting spool with the .70 and .82 housings at 3400-3500 rpm's. With the .63 I get spool at 3100-3200 rpm's. Dont worry to much about the smaller A/R as it will support up to 650Hp with a good 3" exhaust system installed. The big problem in most cases is the external wastegate. Now that can be a problem for a stock mnaifold, but there have been a few people who have welded a good wastegate on a stock turbo manifold. So there you have it. The divided housing in my opinion is a waste of time and effort. I would not recommend using a 1.06 A/R housing except in race applications ONLY like out on the salt flats. You go that high and your spool will be for S#it. I never even ran a 1.06 housing, totally out of my engine specifications, so if you want more then 650Hp run the bigger housing, but you will run into many more critical problems like engine cooling I can attest to that.
-
The heater circuit is not hard to wire into the harness. Ask Clark which wire to run. I just pulled the harness and put an additional wire to the MAF, no problem. But if you have a JWT system, don't they sell a cobra MAF and a Ford Lightning MAF for their systems? Also, since you are looking at the heater wire, ask about the check sum operation of the ECU and how that is connected. One of the things about the 88-89 ECU is that they wil stay powered up 5 seconds after you shut the car down. The ECU will CHKSUM the program and store it, so if you go to the store and get something and are in and out, the ECU will keep the same program and run it in stead of learning the setup all over again. Anyway, Clark can help you out.
-
Question: If all coils are the same, then why are there so many different coils on the market? First off to be able to read high voltage you need a good probe, and meter that will read into the KV range, or you can build a resistor network so that your oscope can read the HV or use a sun machine for ignitions. Running a N/A car and a turbo car are much different. It all has to do with cylinder pressure. So if you are N/A the cylinder pressure will be fixed, regardless of what cam you run, but determined by the compression. When the cylinder pressure is increased you will need a strong coil to spark the plug. Example: I was running a turbo car, my car, and for some reason I could not get the car to run correctly over 17psi of boost. In this case the coil was up to the task, but the plug wires were not. The coil would jump a 1" spark to ground before it would jump a spark across at the time .025 thousands gap at the plug. WHY? Pressure in the cylinder that is why. As you increase the pressure in a chamber/cell the amount of voltage will have to increase, and the power to make the plug spark. I for instance built a pressure chamber to test not only plugs, but the wires as well. I can take the pressure in the cell to about 30 BAR to simulate what the engine cylinder is being pressurized to under boost. You will see or find that some coils have 1-2 ohms across the primary of the coil and others muck lower like .75 OHMS the lower ohm unit will produce a much higher voltage out put then the 2 OHM unit. Basic electronuics guys. Then you have to take into consideration the time it takes to fully saturate the primary of the coil, and what the spark duration is on the secondary of the coil. For a good coil you are looking at 1 milli second discharge time to give you a 1 millisecond spark duration time. That should work for just about every turbo application out there. You look at top fuel drag cars. They have big mags that fire the plugs, now they run two mags and two plugs. I can tell you each mag will produce about 45 Amps, each to two plugs just to get the engine to run. Mallory made some of the best coils out there, and I have found that there was a period of time that you really could not get a performance coil because they were built so cheap, they would burn out. Take a look at this link and it may be helpful : http://www.impulsengine.com/kits/coil_direct_hits.shtml hope that helps
-
The resistors are used for the low impedance injectors (peek-hold type). Dropping resistors as you mentioned ar installed to lower the CURRENT to the injector, not so much for the injector, but to protect the driver transistors in the ECU. The resistors do not control the duty cycle of the ECU, the Latency, fuel map, and the K value control the duty cycle. < The lower ohm is to control the duty cycle of the injectors as an initial starting point in tuning the ecu, are they the stock injectors? I would assume you are running the car in sequential operation, if so, you can back the duty cycle down with the Nistune.> The Z31 box does not operate in sequential mode of operation, but rather batch fire ONLY. Also for the L28 and wire harness, you need to swap injector #2 wire @ the ECU with injector #5 to seperate each bank to their proper injectors. The Z31 box have ONLY two drivers, so three injectors are connected to each transistor in the ECU. Since you have gotten some information that is not correct, the resistors you need can not be WIREWOUND components. The wire wound parts add an inductive component to the driver circuit and they will affect how the injector behaves. You need AUDIO resistors. Digikey sells exactly what you need resistor part # MRA12-resistor value-ND so the part number will be MRA12-5.0-ND resistor values available: 2.0,2.5,3.0,3.5,4.0,5.0,6.0,7.0,8.0,10.0, and higher, but you don't need them. digikey telephone # (800) 344-4539 And since you mention it, I have done some work with Clark at JWT and we found we could drive the injectors harder with the lower resistors more along 3.0 OHMS. What you get with the higher current is a faster response time regarding the LATENCY (or time from off to a fully open injector) this becomes important as you increase the size of the injectors. Larger injectors are generally a slower responding injector then the smaller injectors. You will need to rescale the fuel maps, the timing map, the cold start, warmstart, first time start. Don't play with the dwell time and dwell duty unless you need to as a last resort. I also have setup a bench and I can tell you if you start messing with them you will get to a point that the power transistor is working to hard (for the coil) and will burn out. So unless you have an ocsope to probe the coil primary side to determine when and what time it takes to saturate the coil you are better off not messing with them. GUYS> if you are going to give information out about this stuff, make DAMN sure you know what you are talking about! The poster asked a question because he did not know the answers, that is why it was asked. He got information that was incorrect and very easily have caused him some serious problems with his steup, was that helpful? I think not.
-
Doing any engine performance build is going to cost money. I don't think the RB engine is any cheaper, thats if you want all the good parts like adjustable cam sprockets, chain adjusters, to name two upgrades that will end up costing about $600-650 just to be able to degree the cam correctly and tension the chain correctly. I had my bottom end built to my specs for about 6K That was new rods, pistons, crank, bearings, everything assembled and ready to go. The head was about 800.00 at the time. I did do a fully punched out Gerolomy head that was 2500.00 So total for the engine it was about 10K complete rebuild with performance parts. The turbo, well 1300 for the 35R, 1100 for the exhaust manifold, 1K for the exhaust. a few hundered for the intercooler pipes, 450 for the intercooler. So what do you get for your time and effort, well I have gotten 650Hp myself. I have heard it said by a VERY good authority that these little L28 turbo engine have put out 1100Hp @ 900 foot pounds of torque. So how much did you want to run the engine at? I would also have an RB engine, IF at the time I could have picked up the hacked fromt clip before I had already invested a large dollar amount in the stock engine/equipment, for the 6K the guy was asking, then I would have a 4 wheel drive 280zxt now, but it was to late to make changes to my setup at the time. The L28 will give you all the power you want, so will the RB engine, but you will be making significant mods to install the RB correctly not just installed and it runs.
-
I have been down this reoad before, but I cant remember what the length of the Turbo unit is. Could you measure the rotor length. I thought it was 45mm, but I believe I am incorrect, and the rotor is 40mm.
-
Just oput of curiosity, what is the part number to that FelPro gasket you have the picture of? I got a FelPro and it was a different gasket all together. The stock gasket looks closer to the FelPro part I bought. Do you think there is a difference between the N/A say 77-78 car and the turbo cars? I would like to try the gasket you have pictured.
-
Dump the FelPro gaskets. they are not going to seal for you. I used one one time and it was leaking in short order. I went to the Nissan gasket, NO MORE PROBLEMS! Also it is in you best interest to surface the manifold if it is pitted, rusted, and more then likely it is warped. You do that and I can assure you many happy days motoring.
-
Ran Outta Luck - Blown HG and Ring(s) - Photos inside
jeffp replied to ktm's topic in Nissan L6 Forum
I have run the car on that dyno, not bad. I liked the idea that I could see the whole running gear in action. I don't however like stressing the rest of the dive assembly if I don't need to. The cooling will be much better on the engine dyno. That is what I am really working the cooling for high hp sustained operation. I like the idea of continious drag on the engine, very similar to what a boat engine is subject to. That is the very best way to tune, because now you have the ability to increase, decrease fuel and timing without the "car" getting hot. I need to keep the engine cool and the higher the hp the increased heat is becoming an issue, so much so that I am working on some changes that I think just may be helpful before I try for high hp levels. I have blown a forged 3.0 block, and I think like Bo a stock bottem end block. The car sits a while until I get the cylinder head completed. This is what I worked on tonight. The EURO manifold. -
Ran Outta Luck - Blown HG and Ring(s) - Photos inside
jeffp replied to ktm's topic in Nissan L6 Forum
Brian, I am running about 1mm clearance. The piston is 0 deck heigth, well on the 3.0 engine. I have the stock bottom end in the car currently. Boost, yes 12 psi is 410 hp with methanol injection. The dyno chart you looked at MSA was correct, very nice graph. I am working on some stuff to change with the build and we will see how that affects how the engine runs. You know Brian, I am beginning to think the engine dyno is the best to do the tuning. You can load the engine well and come up with what should be just about a perfect tune. No worries about the differances in the weight of the car and all of that mess. I would love to have a land and sea unit to do some testing with. I need to figure something out, using the car is just not as good and leaves flat spots in the tune. anyway, 3mm I will keep that in mind. I still have not decided to go forward with the bad block. I have gotten caught up on the cyl head currently. That is going set me back a little. -
Ran Outta Luck - Blown HG and Ring(s) - Photos inside
jeffp replied to ktm's topic in Nissan L6 Forum
No Tony, you just make little suggestions that end up costing lots of money LOL. -
Ran Outta Luck - Blown HG and Ring(s) - Photos inside
jeffp replied to ktm's topic in Nissan L6 Forum
The stroker bottom end did make significant improvements in torque over the stock bottom end. I also lost 175Hp for the same boost levels with the stroker rotating asembly. My first test was with a FelPro gasket 65foot pounds of torqueon the head gasket. Same head, yada yada yada. I was running 1800CC's of meth at the time. @ 12 psi of boost it ran 410Hp. The dyno graph you looked at the show was daed nuts on I found out later. I blew every cylinder, and flashed across 2&3. Second test: Stock Turbo head gasket, torqued the head to 70 foot pounds. Back at the dyno, running C16 the car made 475 Hp @ 22 psi. The car was doing good, but Bernard and I did not have time to tune under 3K so we ran it on the dyno 3K-7K and it was tuned well. The low rpm needed some help, and I knew that. I let Frank drive the car and it ran well, but turning the car around down Tonyies street, literally gassing it out of the turn, the car went lean knocked, and blew #5 out the side, no water, no oil. I knew what happened, but at the time my wife was a little upset, so I drove the car home 50 miles or so. The car has been sitting in the garage. I will take it down, but it also appears I also took out some rings, as it was puffing smoke out the oil filler cap, that on my car means only one thing, bad rings. The mod to #5 and #6 did not help me with a traffic jam on the 91 with the A/C on. The car still got hot, ao I knew the heating issue realistically was not solved. I jave since gotten some parts and blocks. I am building another Greolomy head with Nathan, just like the current head. I am going to test some improvements to the stock block, but the N42 block I got has to be o-ringed because some yoyo decided a few center punch marks in the deck would be beneficial for some reason. I have some work to do, but at the end of the day I am hoping to put this heating issue to bed once and for all! 650Hp is no good to me or anyone else if it can not be sustained longer then it takes to do a pull on a dyno! So that is what I am doing presently, along with some work on a modified EURO exhaust manifold. Tony has been making suggestions again, and you know they always are expensive LOL but I think it just may be the ticket for a good deal many turbo cars, but we will see, hell who knows, maybe, just maybe I may offer a complete system that will very effectively support 650Hp as a bolt on LOL now that would be to SWEET. So in short, I don"t recommend anything over 350Hp and keep a stock head to boot for those levels. You can push higher hp in the 400 range, but it also would appear that running methanol can be problematic, when the power reaches the point that the injection of the methanol is not sufficient to provide any additional power. I believe it is at that point when you start increasing the gas (fuel) that the timing becomes critical, as now the engine will run entirely differently from a methanol mix, back to a strait fuel for the engine. It is better to run one or the other for max HP but not both, remember I was injecting 1800cc's @ 400Hp @ 12 psi of boost. Or use the methanol to trim up the fuel map and provide more for cooling of the intake charge. Tuning and compensating timing for a constant changing fuel burn time can be tricky, and in my opinion, doing pulls on the dyno in the car is very difficult. I am beginning to believe the best tuning is completed on an engine dyno. Anyway sorry to hear it went bad with the rings, but I think I am in the same boat as well. -
How Much HP Does A Custom 3.5in Exhaust Add..Dyno Run Today
jeffp replied to slownrusty's topic in Nissan L6 Forum
The cast part of the DP is not 3" the outlet of the turrbo and inlet to the DP is about 2 1/4" I tried to use the stock DP when I went to a stage 5 exhaust side, 2.448" outlet. I could have opened the cast part of the DP, but it would have been thin in places. Now from the flange at the DP and pipe connection is 3" the pipe is 3" and the stock flange for the cat was 2.600" or a little bigger. But by that same token, if you are running a stock stage 3 exhaust turbine, then the 2.5" pipe is fine, you will still get good flow, but the trouble will begin for you if you try to push 400-450hp + with that setup. That is why I went to 3" in the first place. Also after testing the car and system, once I got past 600hp, well 650hp, it appeared that I was not making any more power if I turned up the boost higher then 22psi. I am running a gt35R unit and I am running the .63 A/R exhaust turbine housing. I can get more power I believe with the .82 A/R turbine housing. but I have not tested the system @ 650hp, only 500 hp, and at that point I had not reached crossover on the inlet to the turbo. anyway, Yasin, go with the stage 5 exhaust turbine housing 2.448" minor on the wheel, port match the flange, and neck up to 3" pipe as soon as you can and you should be just fine to 500hp. -
I don't have fitment issues with the part after I installed the feed lines from the head. I used a 1" spacer, but I think to just install the unit, a 1/2" piece of plate as a spacer will work just fine. I want to get one of these units installed before I do any additional changes to the engine, except maybe installing and outlet feed line between 2&3 cylinders. I have been told that some heads have had all 6 outlets from the head. My problem is I am not to sure how to go about 3 & 4 as the long head/cam tower stud is directly in the path of where I would like to install the outlet fittings in the head. I will have to look more closly into this as the hardware will have to change again to accomidate all of the tee-offs from the main return line. The hardware I am currently using, and it is damn expensive, requires to much space to connect. I am starting to think along the lines of a weld on tee type configuration with the flare type connection to the head. I will research this in more detail to see if I can cut some of the costs with the parts. I guess I could even like Tony suggested utilize a copper line if I have to, but I like the stainless steel line much better.
-
I wasn't aware of this change a few weeks ago until I got both blocks together to compare. The coolant holes that are missing in the F54 block effectively created stagnant water flow to that combustion chamber, or at best slower flow in the combustion area of the chamber. I am trying to stop the flow from one end of the block to the other and out, but rather flow through all combustion chambers and out at the same rate, and time. This way, you get better cooling over the entire surface area of the head and block, and less "hot spots" because of the restricted coolant flow. Keep in mind the goal is to increase the total coolant flow through the engine. Well after some investigation, there are only a few ways to increase the coolant flow through the block and head. Also, the bypass in 5&6 are good, but 3 requires a bypass also. Looking at the block and the head, making note of the holes that are functional for water flow from the block to the head, it becomes very clear the flow of the water will be slowed because of where the water holes are placed in the block. The head has been designed very well in regards to flow, so my thinking is to mate the block to the head water passages more closly then they are stock to increase the total flow through the block. The more water that can get to the radiator to be cooled and back out to the engine the better.