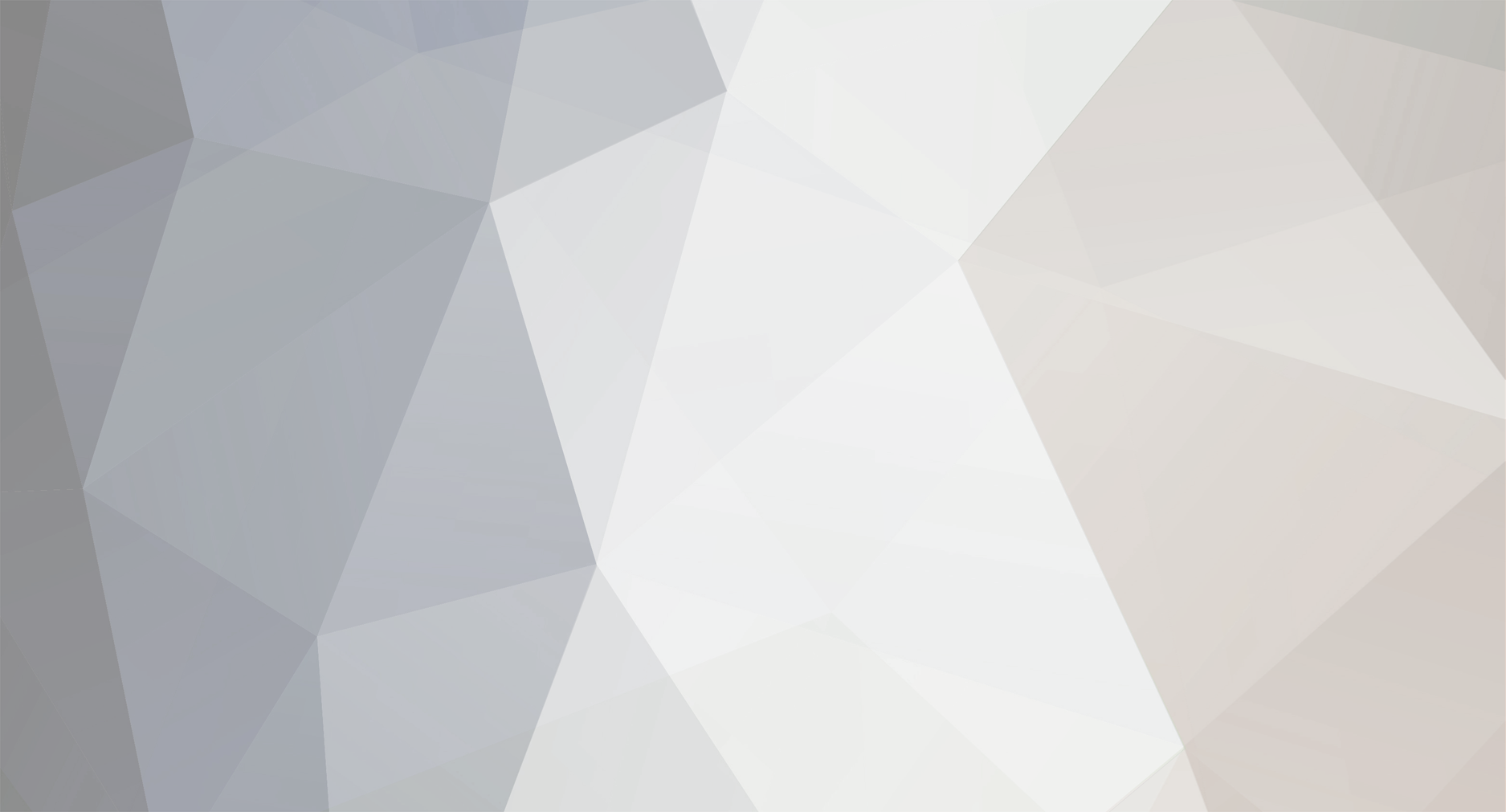
jeffp
Members-
Posts
595 -
Joined
-
Last visited
Content Type
Profiles
Forums
Blogs
Events
Gallery
Downloads
Store
Everything posted by jeffp
-
1) The chain tensioner, (including the Kameari) takes up the tension on the “slack†side of the chain which has no effect on the length of the chain on the tension side between the crank and cam. 2) In shaving the head .080â€, the cam is now .080†closer to the crank and with the tension of the timing chain still taught, that effectively causes the cam to roll, retarding the cam timing, which the chain tensioner will NOT take out because it is on the slack side of the chain, not the tension side. This is correct, however, I also mentioned the cam sprocket fro 140.00 to do the cam timing. Adding head bolt washers and the like is a way of doing the job, but I don't recommend it. I realize alot of you have done this modification and I really don't agree with it completed this way. You guys come up with the fastest cheapest way of doing things for your beloved vehicles, why not make modifications correctly that promote reliability and longevity. I built my engine, and I could have done a number of things to save money, and they may work. I needed a topend that I was sure would stay on the block. My cylinder pressures before firing are in the 450-500 psi range under boost. I did not want to depend on a head that has a significant amount of surface contact area removed from the head. I did not want to try to compensate for cam timing with cam tower shims either. I bought a tensioner, that does work very well to 13,000 rpm's. I also bought the adjustable timing gear to correct for ANY offset in cam timing. You guys always talk about performance, and do this or do that, but I NEVER, except in a few cases hear of some guy taking the time to get the actual cam timing dialed in with a DEGREE WHEEL! Performance, yea right! Shade tree mechanic type work being done all the time. Then when things go to ♥♥♥♥, you wonder what you could have done to stop the problem, bitch about how it is this or that yada yada yada. Fact is that you short-cut proper design because of the cost. So you can give me all the reasons and excuses in the world, my answer is I don't have ANY of those challenges, and I know EXACTLY where my cam is timed because I made DAMN sure it was correct with a DEGREE WHEEL to begin with. I completed WOT tuning of my engine last week, care to guess what power it made? I will tell you, the calculated HP at the crank is 658HP and the dyno torque figures are 509 foot pounds. In fact, if I wanted to sacrafice my 3200 RPM spool of the turbo with a .63 A/R exhaust turbin housing and went back to the standard .82 A/R exhaust turbine housing I am quite confident I could pick up another 20-25 Horse Power. That puts the engine in the 680-700 hp range! WHO ELSE HAS BONE THIS? I will tell you, Electromotive, and a couple others that I will not mention. So you guys can debate, discuss, and theorize all you like, but the fact of the matter is, I can take most of you with 8psi of boost @ 300-350 horse power. Not bad figures I say, I doubled the hp output of the stock boost levels with my engine, and you know I did that with a STOCK TURBO INTAKE! I NEVER heard of ANY performance builders that did not have a degree wheel handy for every build. I use to grind cams, and make valve train components back in the day of Super Shops and Sig Erson, so you could say I know a LITTLE about what is going on with these things (to quote Arnie) have fun, and if we do happen to meet on the street, I am QUITE sure I could take the majority of you with my A/C running. Anyway, sorry if I am a little maen about the whole thing, but this is so agravating to read time and time again.
-
You need to take a look at the EURO turbo header. Nissan did a very good job on that part, and I will guarantee you it will make at least 600hp from that part. I have looked at a number of headers for the L28, all of them are costly, and various configurations, all very costly. I don't recommend moving the turbo flange. You will have problems created in the steering and other things like the pcv valve to mane two. Sure the setup is not ideal, and I am not all together convienced you can make much improvement, but it is the most efficient use of the header. Going custom is cool, but in this case not necessary. I am running a log style header from South Flordia Performance and what a nightmare that has turned out to be. I had to rework the part three times to get it to work. Get a EURO header and you will not be sorry you did, but if you want to go custom, then copy the design and incorporate a waste gate flange for the Tial 44mm wastegate. The bigger the better on the wastegate I say. You want to be able to vent enough exhaust to maintain stock boost. The Tial 44mm will flow a bit better then the Tial 46mm (porsch gate) I can almost run stock boost levels with the 46mm gate, but I do get a little creep from 5K to 7K because the gate is a little small.
-
if you did that damage punching out the freeze plugs, my recommendation is to get another block. Damaging the cylinder like that is not a reliable block, and that looks like just about the place the rinds end up at TDC. One of the things about doing repairs and building aomething to begin with is that YOU DON"T CREATE DAMAGE IN THE PROCESS OF THE REPAIR! You would be surprised how many times you see someone assembling new parts and create damage in the process, not good at all. Myself, if I realized I nailed the cylinder wall that hard to create that much damage, I would not hesitate to replace the block.
-
I have read time and time again about doing this setup for the P90 head and the 280 engine. Head shims are not the correct method to compensate for the chain slop created when the head is milled this extensively. The correct way to fix the problem is to go with the chain adjuster from Kamalari (if I spelled that right) then all of your cam spacing is not an issue any longer. You will not have to bother with shimming the towers. Also, can you even shim the cam towers that much without hitting the top of the valve cover? I don't know because I would never do this to my engine. The L series cam is long, it needs a good foundation to secure to and that many shims just is not a good way to go. Remember, the head bolts go through the cam tower, so if you shim the towers with that many shims you are losing threads in the block for the head bolts. Spend the extra money and get the right part for the job. Also I would recommend the TOMEI adjustable cam sprocket. You can have that part in hand for about 150.00 shipped from Japan to your door. Worth every penny in my opinion. this is the very best way to go, and you can feel confident the cam timing is not going to change after you make the adjustment.
-
I was looking at your intake manifold and realized you are not running the heat shield under the manifold. I think it would be worth you time and effort to install the shield. You are taking all of the heat from the turbo hitting the intake runners and the part may be subject to heat soak in short order. Seems to me the heat is one of the most important factors to try to get control of. The pipes look good to go.
-
I did the fuel delivery tests of my system, and the fuel pump is not as good now then when it was new. I really started dropping flow after I went to 80psi of fuel pressure, and 10 seconds into the test I could hear the fuel pump going into bypass. NOT GOOD AT ALL. But the good news, is that YES the plug wires started breaking down, specifically the boots over the plugs. I also did the test under extreme pressure conditions. Lance has a test jig that has windows, and can be pressurized. I installed the new plugs and the wires and powered the coils from a test ECU. Sure enough, when we got to about 275psi of pressure in the test jig the wires started arching on the plug end. So there really was a misfire of the ignition, and since the fuel was about up, it was a good thing this time that it was misfiring. I bought magnacore wire and MSD 3301 plug boots and terminals to build the new wires. I also bought a second fuel pump that is good to 90psi of fuel pressure, and I am going to install that in series with the Nissan twin turbo pump. The ECU will be programmed to turn the pump on at about 10psi so it is not running all of the time, well sometimes it will not be running LOL. So the question now is, what am I going to get with the additional 5psi of boost? Here is the last dyno and the car got one good pull at about 18-20psi of boost. I think this engine is going to make some good power @ 25psi of boost.
-
I agree Scottie, pushing a single pump that hard will not be the best option. The voltage booster is an option, and MSD sells one of those boxes. Realistically if I get a flow rate of 4400 cc's a minute then I should have the flow I am looking for. So here is the plan, I spoke to a number of people and the common fix was a second pump, we will see about that. In the mean time I am going to see what I get with the single pump at 69psi and thatwill tell me which way I really need to go. that is 3 BAR 43.5 plus 25psi of boost. That is where the rubber meets the road. I have all my test bottles ready to do the test today, so I will post the results tonight.
-
As Tony said that is where my brain was going. 96Lbs/min injectors. That will set my static fuel pressure to 43.5psi at idle then the boost of 25psi. The Nissan pump should be up to thattask, but I am going to check it. I think if memory serves me correctly, the nissan pump is delivering excellent fuel flow quantities. I have a big cc flask at work that will do the trick for the test. The fuel pump relay, I agree, it just may be time to get a better part. Scottie, I ran down that road a number of years ago with the dual pump setup. The thing that stopped me from doing it was the fuel delivery at pressure levels higher then 75-80psi of line pressure. All of the pumps I looked at had a top of about the 75-80 psi and the flow rate would go off a cliff and die. I will look into the 96lbs/min injectors. I m not sure what idle will be like though. That would solve my problem. Greedy, I don't think so Tony, I have the air available, and from my sensors, when the car is heat soaked the mat is telling me the air is 67 degreesC not to bad for an intercooler that is sized on the small size for this build. I want to run the boost to the limit. so with an additional 5psi of boost, the engine will be very close to 700hp at the crank. The 537 figure was at the wheel, so that puts me right at 617hp with the 15% drive train loss figure. Not to bad, for a street car. If you got it, use it. Hooking up the tires is an all together different story, but we will see what the wrinklewalls do for traction. Anyway, I have pugs on order, and I will speak to Lance today about the larger injectors, and try to complete the flow testing. 4500cc's should do the trick, and if not, then I will consider the second pump, what a pain. I thought the fuel delivery was good enough, and last time it took some engineering to get that system correct. Anyway lets see what happens.
-
I am running the fuel pump with the stock fuel pump relay. I may be losing some power there, I will have to test the relay. I don't want to mask a problem with the methanol, but I really th8ink the engine is running out of fuel not spark. The give away is when the power curve starts coming up quickly in the 4K range I get a little misfire but it is short. That tells me it is not an air flow problem. I have completed the fuel delivery charactorization a while back, so here is that data. Using the Nissan twin turbo pump, the pump will go into bypass at about 90psi. I also tested the drop in pressure from the pump outlet to the fuel rail and there is about a 4psi loss through the stock fuel line (feed side) so that would make my maximum fuel pressure at the regulator be 86psi with boost. 58.8-86=27.2 so that would indicate I can run 27psi of boost. So depending on what my brake specific fuel consumption is, I have never put a flow meter on the fuel, I need at least 3300 cc's of euel a minute. I think that number is higher, but I have not worked that formula. So to test the system, supply battery vooltage to the pump @ 13.8 volts. run the system with the return line in a bucket to measure the cc's that return to the tank, this is the fuel the injectors have to use to fuel the engine. I tested the system to 83-85psi with boost added to the static pressure of 58.8psi. I am not all that sure the single pump is going to supply all of the fuel required for 600-650hp so when I put more boost to the engine then 600hp I don't have enough fuel for the engine, hense a "misfire" So I need to work a few formulas and do some fuel edlivery testing to make sure there is enough fuel. But according to the rc injector formula, to run the car to 600 hp with a bsfc of .65 @ 58.8psi static I will need an injector that is 740cc's/min or 70.36 Lbs/Hr fuel injectors. The calculation for flow is if I am correct 740cc's/min X 6 = 4440 a minute. I don't think my system is able to accomplish that task, close but no cigar. I am also going to test the system again to make sure I have the flow I need and I also need a little head room as well. So I have a few choices: 1) get 96Lbs/hr fuel injectors and run 43.5 static fuel pressure and that will get me to almost 700hp 2) use the methanol on the topend to get the fuel required. 3) leave it alone and run to 19psi and be done with it, and be happy knowing I still have at least 5 psi of boost left in the turbo. The lower fuel pressure will save me an additional fuel pump to get the correct flow at the fuel pressure under boost. so that is what I was thinking. What do you think?
-
So I was talking to a friend of mine about what the car was doing and the thought occured to me and him that if it is a fuel problem, no problem, I can start injecting methanol to compensate for the lack of fuel I believe is happening. So if it does turn out to be a fuel problem the methanol will corrcect the problem. I can do this test without changing out the injectors. I will have to think on this a while longer, but if that is the case, then the car will have two power levels, fast and reeeeeelllly fast. Anyway that is what I am thinking.
-
First off, the champion plugs are gone. I did not want to use them in the first place, but that was all that the shop had. I did find a good site to sell plugs http://www.ridegear.com The had every plug I was looking for. I was thinking along the lines of a B8es plug, but the resistor type will work good also. The plugs are cheaper then the newer plugs. I have been told the Nissan engine does do better with the wide electrode. I also have tried the NGK V-power plug and it appears to work well at more cost. Either way, the 8 range plug appears to be the best bet. I was also looking at the injector flow rate requirements and from what I have been able to calculate on the RC engineering site, I have just about run out of injector. so with my fuel pressure set to 58.8psi and using their formula of .65 for the brake specific fuel consumption, 650hp desired, the injector flow rate is indicated to be 740 cc/min with the injector @ 80% duty cycle. Anyone want to verify that figure, I might be missing something. I ran into this problem on the mustang dyno @ 489hp or so with 17psi at the wheel. The dynojet said 508 or so @ 17psi of boost. Not to far off the measuremets. The thing that really sticks out to me is that when the engine comes up on boost about 3200 rpm's I get a misfire at about 4500 and it goes away. Then at about 5500 or so I misfire to 7K Now I could be wrong all together on this, but from the injector flow formula, I am out of injector to pull the power up over 600-625hp I will speak to lance on Monday and get a better idea of what is going on. He did not indicate that there was a problem with injector sizing, and I did not think to ask him what the duty cycle was. The thing is that the wideband did not indicate a lean or rich condition, but we know that when the O2 sensor gets into a pressure state in the exhaust they start acting a little funny. It just could be that the sensor was not reacting fast enough to measure the AFR's at that level. I am running the Honda NTK sensor. Now wouldnt that be a pisser, the injectors are out of juice at 625hp or so. I ordered some plugs from NGK and they will be here Monday, I will also order some of the Br8ES and BR7ES plugs. I think the 8 plug will be best. The 9 heat range is to cold even for my car, and my motocycle when I rode bikes. That plug would foul fast, and looking at the plug out of my car, that plug appears to not be getting hot enough to burn off the carbon on the insulator. So what do you think? bigger injector? maybe this was all that I was seeing last year? Really would be a pisser.
-
I took the spark gap to .025- .028 for this set of runs. The designer of the new system was doing the tuning during the dyno runs. So telling him that the plug gap had to be set down did not wash with him all to well. So I called it a day and paid my money for the dyno and a set of chanpion plugs I don't want. When Lance said he needed to test the wires and plugs in his pressure tester I decided that was the best thing to do for now, and order some plugs. I found a good site that sells the B7es-B9es standard 2.25 a plug NGK parts. I think this may be beneficial. I have also tried the V-power race plug from NGK with little success. So for now, I am going to go with the tests Lance wants to perform. Its cheaper that way LOL. No I really want to find out what the heck is still happening.
-
Well got the car to the dyno again and it is still misfiring at high boost levels. I got one good pull @ 20psi and that was it. The car had a slight misfire @ 4500 rpm's and it would go and about 5500 to 7000 it would misfire again. I did all of the standard stuff with the plug gap and all of that with no improvements. I tried two different type of chanpion plugs (that was all the shop had) and that did not make improvements. I was running a 6 range plug and they glazed and began to misfire. I then went to about a 9 heat range, they did not glaze, but it did appear that they were to cold. I have tried an 8 range irridium plug, and an NGK race V-power plug in the 7 and 8 ranges. The 8 range seems to be about the best but the misfire is still there. I have a new ECU and the spark duration is 3 milli seconds, and we tried 4 milli seconds with no improvement either. any idaes?
-
Meth Injection - PWM Calcs for Injector - Calcs within, request check
jeffp replied to ktm's topic in Turbo / Supercharger
Now that is some calculating! I have the FJO injection kit on my car. I am running two of their 900 cc Injectors. You are going to try standard injectors? You will not be able to pressurize the standard injector to 150psi I do believe you will damage even the bosch sytle injectors with that much pressure. I was running my car on the one 900 cc injector. The car really liked it, but it was not enough methanol. The FJO controller has a standard map 16 X 16 blocks to tune, all based on RPM and engine vacuum. Have fun with it, you will like running methanol. -
Intake Porn! My New 4" piping Cold Air Intake System...Pics!
jeffp replied to a topic in Turbo / Supercharger
I also did the 4" inlet pipe because of my turbo and MAF. I made the pipe in two pieces and used a silicone coupler to install them together. The really cool thing is that after I get my intercooler pipes removed the intake is easy to remove. I remove the aircleaner and 90 degree bend. Then the part that is cool is that I can remove the pipe to the turbo without removing anything from the car. I get it past the A/C lines, the headlight washer bottle and it just fits in the car slick as snot LOL. K&N makes the same filter you have, I got the K&N part and at the time was really glad it was available. Now a good powder coat job will make it perfect, and you wont have to worry about any rust. I just love this stuff LOL -
I just completed a relay and wiring upgrade on my zx. Nissan is switching out the power ground to the lamps. The switch in the car is switching the B+ or 12 volts to the lamps. Now, also they have the head lamp test circuit for the dash indicator. The thing that is different is the high low bean switch in the car. I thought they were switching from 0 to 12 volts with the high beam switch, but they start out with 12 volts to the high bean switch, and when you select high beam, the switch line goes to 0 Well for a relay, that would be hooked up so that the relay was energized in low bean and off in high beam. So for the majority of the time the relay is switched on because we drive most on low beam. I ended up bypassing the lamp test circuit to get the indicator to go off when you run the test from the dash. This is an easy fix, but you will need two relays per light, one for the ground switch and one for the NEW 12 load switch. Use the wires to the light to toggle the new power and ground feed relays. This takes all of the strain off of the stock wire harness and switch. Also check the fuse link in the box, to make sure the connectors in the fuse link box are still good. My car over heated the connector and the lights got dimmer. Use the FSM to determine the correct wires, and the two letters you mentioned I don't know about, but the side of the relay should have some sort of diagram that have the letter and pin location. Hope that helps.
-
A cam will work well provided the application of the cam is realistic. You need to know what your power curve is to be 4K 5K and up. The falicy of a cam with overlap creates problems with the turbo engine is not all together true. My cam for example has 54 degrees of overlap. To much for a turbo engine right? Wrong! my cam is putting my power curve from 4000-past 7K so to say across the board that overlap and duration is bad for a turbo engine is just not correct. Realistically, to get the power inthe higher rpm levels, you are going to need duration and lift. Match the cam to the capabilities of the engine. The stock cam will work for you, but the power will be way down by 5500 rpm's, so if that is what you are looking for then use the stock cam. There really are not a specific application for a particular cam, the head flow is going to determine if you are under cammed or over cammed. A overcammed engine will be doggy at low rpm's, and a under cammed engine will be bad on the top end. just something to think about.
-
L series - Positive crank case pressure, too much.
jeffp replied to proxlamus©'s topic in Nissan L6 Forum
I used a -6 check valve on my car. I made the block plug and it is installed with orings. The plug is tapped for the check valve. I then and this is important, drilled a .060 hole in the bottom of the plug to get the gases, but not fling any or little oil in the air path. from the check valve I then have the hose going to a seperation tank, and from the tank to the bottom of the intake manifold. This setup has worked very well for me. I don't get the smoke on decell anymore and the engine seems like it likes it. not the cheapest way to go, but fixed the problem. -
Odd Misfire Under Boost - Only 2nd and 3rd gear...
jeffp replied to ktm's topic in Turbo / Supercharger
The gap is going to fully dependant on the ytpe of coil you are running. I don't know what system you are running, but you mentioned you set your spark duration to 6 mSec, that is much more then is required to fire a coil. Most coil primaries become fully saturated by 2-3 milli seconds for a not so good coil. You just may want to check to see if the coil is getting hot, that is the sure sign that you are turning the primary windings to the coil into a heating element. The ECU driver transistor must be getting hotter then a pistol at that duty cycle as well. I never liked the idea of adjusting the spark gap at the plug to .022-.027 or so. I have taken a look at the pulse on my oscope and the gap is not sufficient to get a proper discharge of the coil. That is why the car runs poorly at idle. To correct the misfire properly, get a coil that has a sufficient voltage potwential output that will accomidate the higher cylinder pressures. Mallory makes a very good coil for points, and a good unit for a capacitive discharge type ignition. I tried the MSD HVC coil, and it worked well but failed very quickly, two failed quickly in fact. But I was able to run high boost with the car. The output voltage on that part was 48,000 volts, and I did have to adjust the plug gap as well. The mallory coil is a bit better, @ 50,000 and they are oil bath type coils, they can handle much more heat in that configuration. anyway. -
I went through this here resently and went even cheaper. I used the flex plastic conduit coverings. I like that stuff, but heat considerations have to be examined. I went to the junk yard for the clamps to secure the ends of the conduit. I go ends, tee's, and feed through plastic clamps. I think I spent about 25.00 to do the complete harness, terminating all of the ends, clamps for the center sections, and the tee's. All it took was a good paint brush to clean off the parts. I think the harness turned out good, and it is clean. So there is an alternative to spending allot of money on harnessing components.
-
I have run both of the plugs. Seems the non projected plug is a little less prone to detonation under high boost. I cant prove it, but it would appear that the electrode becomes to hot, similar to a glow plug. That ignites the fuel to early and you know whaty happens after that, the engine loses power and knocks. Any other comments or observations on the two from someone?
-
I went through the whole process of the Nissan pumps. First off the turbo pumps I have found from every company is the same stock Nissan unit. The only other pump available is the millings pump. The turbo pump number is M111 it has the 45mm drive assembly, instead of the standard 40mm drive assembly. In fact this is what the difference between the turbo pump and the standard pump. The LD engine has an even smaller drive assembly as I understand it, but I have not disassembled one to make sure. I modified the Millings unit. and blue printed the part and tightened up the tolerances some. The final test was in the oven @ 270 degrees temp and I double checked the tolerance and it was .002 end play. So this helped out my idle pressure. I always thought 10 psi @ idle was a little shy for the engine. I installed the bob sharp springs, and I still had to shim them to the desired full pressure setting. You don't need special springs, just get a flat washer and place that in the tightening nut and that should give you about 55-60 psi @ 7K rpm's that will work well. I say go with the millings pump, because I think I got mine for about $70.00 out the door. That is the cheapest you will find for any l series pump. Then you can if you want tighten up the tolerances for better idle pressure, install the spacer (flat washer) shim and go for it. I will caution you on one thing, USE the STOCK nissan gasket, the after market gaskets are thicker and that will change the tolerances of the drive gear end play. hope that helps.
-
So looking at the cam specifications of the stock Nissan grinds, it is easy to understand why most of the L series engines run about the same for power, rpm ranges and torque curve. I went with an ISKY regrind and that part has turened out to be a really good fit to may application.
-
The 274 cam's Valve Events are as follows: .501/.510 Lift & 110 LDA IVO = 31* BTDC IVC = 63* ABDC EVO = 35* BBDC EVC = 63* ATDC This is a good cam to run in a small block. I would go to say .550 lift on the valves. The opening and closing points are good of the intake valve. The 274 cam's Valve Events are as follows: .501/.510 Lift & 110 LDA IVO = 31* BTDC IVC = 63* ABDC EVO = 35* BBDC EVC = 63* ATDC 274 intake duration 278 exhaust duration 56 degrees overlap lobe center 106 degrees The other thing I would change is to advance the lobe centers to 112-114 degrees. This will give you the lowend, and you should be making good power by 3000 rpm's Here is a suggestion, Call Ron Iskiderian and talk to him about your application. Your cam is very similar to my cam for duration I am not convienced the 106 lobe center is going to be too your best advantage. I am sure Ron can give you a very good direction to go. Myself, I am running my cam on a turbo application. The engine will pull to 7500 rpm's the cam works well for what I wanted. What is your target rpm range?
-
Looks good to me Frank. I never did like the thin blower belts myself, but if they work go for it. You could also go with an electric water pump if the idler becomes an issue to free up some placement locations. I say boost the piss out of it and see how it works.