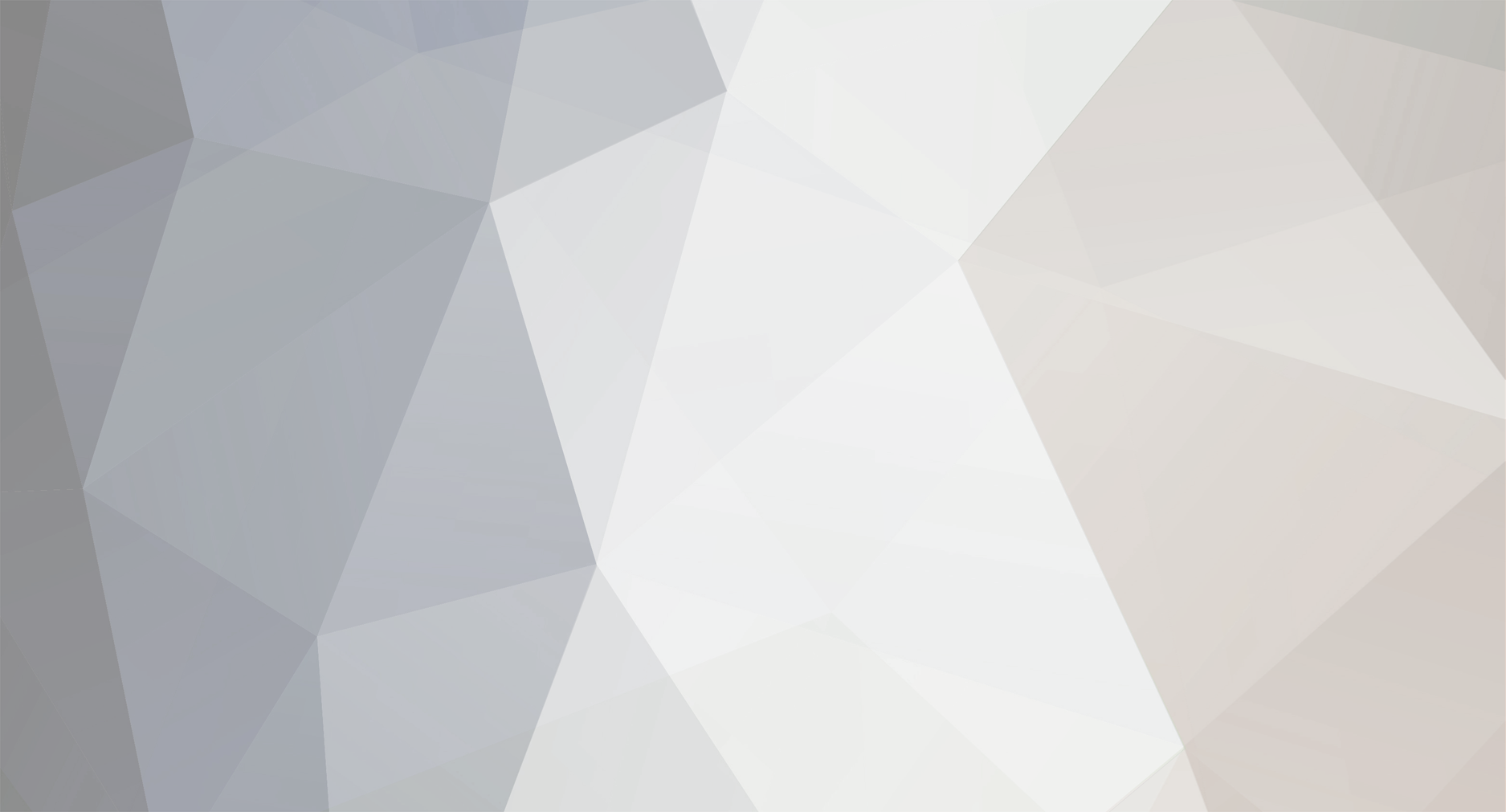
Dan_Austin
Members-
Posts
223 -
Joined
-
Last visited
-
Days Won
2
Content Type
Profiles
Forums
Blogs
Events
Gallery
Downloads
Store
Everything posted by Dan_Austin
-
5 lug front drag wheels
Dan_Austin replied to stock600's topic in Brakes, Wheels, Suspension and Chassis
The second gen Camaro (and many others) used the same A2/A6 bearings as the S30. If you measure the stock hub to get the distance between the outer edges of the bearings you can then spend time on the Wilwood web site checking out their aluminum hubs to find one with the correct bearing spacing using the A2/A6 combo. Many are drilled in both 5x4.5 and 5x4.75 You would need to then figure out the rotor hat height and caliper bracket, but if you've back-halved the Z already you can likely handle that part. -
Another Vela Rossa install
Dan_Austin replied to Dan_Austin's topic in S30 Series - 240z, 260z, 280z
Great info. I had learned the vin tag tip from your thread. How did you tackle the dash tag? Long flat head screwdriver and a bit'o violence? I can throw a cordless drill in the trunk for the door jamb. Did they also take the bolt on plate in the engine bay? I actually planned my headlights fairly well. The main bucket is bolted to the rear of the pocket and the floating bucket is in front with notches in the fiberglass for the adjusters. I was between 5 and 10 degrees off from vertical, so I tweaked the adjustable bucket to allow for a bit more leeway in the bulb placement. A quick check in the driveway looks like I will be fine. -
Another Vela Rossa install
Dan_Austin replied to Dan_Austin's topic in S30 Series - 240z, 260z, 280z
She is a young '76 so she still has to pass sniffer and visual. Sniffer no prob, visual now way no how. I thought to use the other loop hole for vintage/classic cars, but I do not own a second qualifying vehicle, so no carrier would issue the appropriate insurance. Not one of them cared that my weekly commute was only 12.5 miles. So a VR kit and the SB100 route keeps her on the road without resorting to tracking down 35+ year old parts to meet the visual requirement. I may be too naïve and optimistic, but since I've owned the car and major parts for years as a registered vehicle I do not expect major issues with the DMV or CHP. The brakes were rebuilt earlier this year, so that should be an easy pass. Which leaves lights, and the one check that gives me pause. If the shop checking is particular, the housings are ECE and not DOT. I also did not plan to install marker lights, which I have read can be an issue for some shops. -
Another Vela Rossa install
Dan_Austin replied to Dan_Austin's topic in S30 Series - 240z, 260z, 280z
Started at 8:00 since my extra hands for the big day had to leave early. I had laid out the tub and had already prepared the body. Neither I nor my buddy had worked with body filler before, so we did not recognize that the cream hardener had separated sitting on the shelf at the parts store. After 40 minutes we guessed the problem, pulled the tub and mixed a second batch. That one setup very fast, but after the 'dry' run we had plenty of time. With the tub on my buddy departed, and I started looking at the door skins. I figured I would start the passenger side, so if I screwed it up I would not be looking at it on a daily basis. Well I did not screw it up, but after the bonding set I realized plan to not cut the handle pocket was not a good on. The handle fit perfect, and even the mount bolts just slipped right in, but were not long enough to put a nut on. So I ended up pulling the window and regulator to make enough room to reach in with a 4" angle grinder and cut off wheel to cut the pocket. It worked, and was drama free, but boy did it suck putting the window back in my self. This is what I should have done and what I did on the drivers side- With the doors on she is basically complete. I need front turn signals and to mount the license plate, then I can start the DMV process. I have one panel left to bond, and that is the spoiler, which has to wait until I can pickup a bit of strapping long enough to span the deck for clamping- One bit that does not show up well in a photo but I am pleased with is the door edges. I was able to feather and smooth out the filler to dress the 3/8" gap on the rear and smaller gap on the front- -
Another Vela Rossa install
Dan_Austin replied to Dan_Austin's topic in S30 Series - 240z, 260z, 280z
A few more small items knocked off the list. I borrowed a welder and finished tacking the trimmed rear wheel arches. I also welded in the hood stop. The welds look better than the photo, and I really did not care to make them pretty. While I have the front end apart I finished mounting the idle valve and plumbing it and the valve cover breather into the cold air intake track. I found my headlights were canted a bit, despite trying to ensure the buckets went in level. Instead of cutting up the fiberglass I opened up the notches the buckets. Not that I have the lights in I can see that I did have the relay wire up correctly, so that is another item crossed off. The one other item handled so far is cutting in the Quik Latch Minis. I ran a 1/4-20 tap down the original hood bumper mounts and used a 3"4 hole saw (very slowly to avoid splintering) The nut for the latch did not feel right when tightened on the fiberglass, so I cut out a couple of 1.5"X3" tin strips and drilled those to be large washers. The latches are nice and tight, and if they do not hold well enough, I can also step up to the full size Quick Latch, I just wish they have a size in between the mini and full. I picked up a gallon of Kevlar reinforced body putty and will be bonding the tub tomorrow morning. If that goes well I may do the doors too. I am debating removing the doors and laying them flat to make the panel easier to install, although that will make it harder to tweak the panel alignment, so maybe they will be bonded on the car... -
Another Vela Rossa install
Dan_Austin replied to Dan_Austin's topic in S30 Series - 240z, 260z, 280z
The hood is mounted and the headlight buckets installed, mostly. I need to pick up some specialty bolts to finish, but the cutting and sanding is done. I also finished rerouting my cold air intake since the tilt nose hit it hard in the original location. Need to install a pair of Quik Latch mini hood pins and cut in the washer nozzles, and start bonding panels. Next weekend maybe... -
Another Vela Rossa install
Dan_Austin replied to Dan_Austin's topic in S30 Series - 240z, 260z, 280z
The hinge arrived on Thursday, but I have not even opened the box yet. I moved our corporate HQ last weekend and the local Telco managed to bork my WAN and internet deliveries., so no free time to play. Those problems were resolved yesterday, so the hood goes on tomorrow and bonding is likely next weekend. I am fairly happy with the pods. If the local TAP Plastics is done remodeling I will pick up some 3oz fabric and try my hand at covering them, otherwise I plan to see if a local custom stereo shop that makes enclosures will accept a non-stereo job. -
Another Vela Rossa install
Dan_Austin replied to Dan_Austin's topic in S30 Series - 240z, 260z, 280z
Still waiting for my hood bracket, so I spent the week shaping the tail light pods. Mid-week I placed the shaped, but not sealed/glassed pods and marked out my cuts, last night I took a deep breath and made my initial cuts. The good news is that the pods will completely solve my clearance issues on the passenger side. The bad news is driver side has seen repairs in the past, and is not quite square. I needed to trim the lower valance to make room for the right side turn signal. I have not bonded the tub yet and can remove it to make adjustments for clearance, so this is actually working out nicely. The tub looks intimidating, but I can easily place it and remove it by myself. My first attempt at glassing my pods was just short of a disaster. The shop I bought my epoxy resin from was remodeling and could not cut my desired 3oz woven e-glass, and offered a 'comperable' tape. It did not want to hold a curve and kept pulling away from my carefully carved pods. The 'just short of' was achieved by removing the misbehaving glass before the resin fully hardened. I am now attempting to just resin coat the foam so it is not fragile, and revisit the need to glass it later. Not wanting to end the day on a downer, I finished soldering the tail light harnesses and mounted the lights without the pods- Once I figure out how to finish the pods I can be confident in bonding the tub. -
Utter refusal to run at reasonable AFR's, noise problems
Dan_Austin replied to Xnke's topic in MegaSquirt
Which wideband are you using, and do you have a separate gauge for it? Your descriptions sounds like you have a calibrated sensor, but TS is using the wrong calibration curve. I have no experience with the Extra code, so I may be talking out my lower orifice. On the B&G code I know I needed to identify the sensor in the project properties, calibrate it in the sensor tools and I seem to recall needing to tweak something in VEAL, but I do not have my tuning PC handy so I am not sure about the third location. -
Another Vela Rossa install
Dan_Austin replied to Dan_Austin's topic in S30 Series - 240z, 260z, 280z
Headlight relay harness complete. The high density foam cuts easy with a fine tooth hacksaw blade and I was able to make curved cuts to follow the lens housing shape. Not as nice as a coping saw, but close enough, and the foam sands nicely. I started by mocking up a full valance to see what it would look like: I like, but do not want to completely fill the void in the valance, so I cut up a couple more 8" high panels, copied the lens holes to the smaller pieces and started shaping the pod curves. I may end up removing a bit of the outer edge to make the pods symmetrical, or maybe not. Once I decide that I need to tackle my first glassing project and cover the foam pods. The pods will solve, or at least greatly improve the clearance issue. Edit- I just notice the tape on the left pod sagged before I got around to taking the picture. That will be corrected before I make any cuts on the tub. -
Another Vela Rossa install
Dan_Austin replied to Dan_Austin's topic in S30 Series - 240z, 260z, 280z
Still waiting on a bracket and a few lights, so not much progress to be made. So I picked up some 2'X2'X1" high density foam panels to sculpt the taillight pods. That project starts tomorrow, after I finish building the headlight relay harness. It has been on my list for a long time, and it made sense to tackle with the front end apart. -
Another Vela Rossa install
Dan_Austin replied to Dan_Austin's topic in S30 Series - 240z, 260z, 280z
My clear euro tail lights arrived yesterday so last night I cut the sockets off one of the factory stub harness and wired up the tail/turn/backup lights and confirmed the wiring scheme. I need to hit the junk yard again for two more tail/brake light pigtails to wire up the second set. -
Another Vela Rossa install
Dan_Austin replied to Dan_Austin's topic in S30 Series - 240z, 260z, 280z
The rear tub is requiring some trimming at the rear to get the front to set down and align with the rocker and door jamb. I just about have it where I think it needs to be, although the arch is covering part of the quarter window trim. I also mocked up a couple more light options- Staggered: Angled out: I really like the staggered, but clearance will be hard, the angled out arrangement is growing on me. I also like it with a slightly shallower angle on the outer lenses, say 30~35 degrees on the outer and 45 degrees on the inner. Finally I placed the lights inside the valance in the angled out setting: This was interesting, although hard to see in the photo, the lights are sitting about 3" too high. The lenses are curved and the peak is about 1/2" to 5/8" from the mount surface, combined with the steep curve in the reflector and the 1/8" thick pocket suggests I will be much close to getting the inside clearance I want. If notching the valance does not yield enough space, I can then move on to relatively short pedestals. -
Another Vela Rossa install
Dan_Austin replied to Dan_Austin's topic in S30 Series - 240z, 260z, 280z
The first delivery of the C5 lights arrived. I found a used set at quite a savings, cheap enough that I only planned to use 2, with 2 spares or two to sell. I have ordered two more with a clear insert that will be my backup lights, which have not been delivered yet I need to decide if I want the secondary lenses on the bottom, top, facing each other or apart. I am thinking that I am on the right track with the angled install. I chopped up a box with the basic shape of the lens, and taped them in place. The missus was calling for dinner, so this was just an eye-balled spacing and tilt. The lenses do not separate from the housing, otherwise I would tape them in place to test the visual appeal. I do tend to think that the angle works better with the tops leaning in, accentuating the wide hips. -
That is a little more aggressive than I planned, but it is an option. The housings are fairly shallow, with the central socket 3.5" deep from the mount surface. I had another layout in mind ( _ -- plate --_ ), but that would definitely cause a depth issue. Since I have not bonded my tub yet, I will pick the style I like, install the lights and check the fit. At that point I can decide if I want to do more cutting or make small pedestals.
-
Another one with missing nub-ins and springs. Pharaohabq has a thread about 3D printing bits we need for these old cars, http://forums.hybridz.org/topic/113544-240z-horn-button-refab/ If that does not work, I may need to study up on plastic casting, there is clearly demand. Not sure where to find the itty-bitty springs, maybe a hobby shop that has a R/C focus.
-
The lights are scheduled to arrive tomorrow, and I will be checking that very closely. The lights are between 2.5" and 4" deep from memory. I'm playing with a couple designs, the lights a slightly oval, so am thinking to mount them on an angle, which would move their center up ( / / Plate \ \ ) or the basic ( - - plate - - ). A big goal is to maintain access to the bulb sockets from inside, but that seems more and more unlikely.
-
Another Vela Rossa install
Dan_Austin replied to Dan_Austin's topic in S30 Series - 240z, 260z, 280z
The quarter windows stay. This is to be my daily driver, and with the way the locals drive, I want to see them coming... The kit does have optional panels to cover them, so I can always change my mind. -
I ordered a coupe kit from Reaction Research 10 days ago and lucked out that John had business in the area yesterday, so I saved I pile on the delivery. Since I knew it was coming, I stripped her down last weekend I could only take a couple of hours for the delivery, so we had to rush the pointers, but I still felt OK to jump in today. John pointed I needed to trim a few brackets, so I had to call a buddy to borrow his angle grinder. He showed up at 2:00 and we shot the breeze for 45 minutes when another friend stopped by unexpected to show the project to his kids. Once every one was gone I got the cheek panels mounted. I managed to get the drivers side right on the first try, but had the passenger set back 5/16" of an inch, which was easy enough to fix. The rear tub was a adventure by my self, but I have it in place as a dry fit, and the door skins taped in place to get a look at the end game. I have just less than four hours in the assembly, which is not a bad start. I need to pick up some duraglass next week and work on wiring harnesses. The bonnet is just resting in place since the hinge did not make it on the truck., so that is a task for after labor day
-
My ECU limits my choices to multiples of 80. I found suggestions of 300 to 320 HZ. I tried 160 to 960 and found that 320 seemed to be the best balance between noise (too much when the HZ was too low) and response/resolution (40 RPM at temp per 1~2% duty cycle) One addition thing to watch with the Bosch/VW IAC is that the ports are large. The in port my is about 17mm and the out port about 25mm, making hose connections an adventure.
-
Zip tied to the remnants of the AFM bracket. I need to make a better mount, but before that I want to get a 16mm hose nipple on the cold air pipe so I can connect the IAC to it and ditch the small filter I put on the IAC.
-
I've had the Z for about 5 years, after purchasing it to be my daily driver. All the mechanicals have been refreshed or updated- 83 ZX Turbo w/large ebay intercooler and 3" mandrel bent exhaust 81 Wide ratio 5 speed Obx helical diff w/3.90 gearing & RT diff mount Wilwood Forged superlights in front and Silvermine Stage 4 in the back, 1" Wilwood master Full urethane bushings swap Eibach springs and Tokico blue strut inserts CS130 alternator swap The cosmetics have always been the least of my concerns, but the missus finds it ugly. The turbo swap happened after having major issues with the stock 76 setup passing, not for numbers but the visual, so I decided to go whole hog with the SB100. The wife surprised me by liking the VR kit, so the project went from fantasy to real very quickly. I stripped the front end and all lights last weekend. I choose the bolt on cheek panels, and hope that I can have the nose mounted this weekend, with the doors and rear tub to follow the following weekend (but may drag out). I've ordered a set C5 euro spec tail lights and collected the pigtails to build the proper harness, which might happen after work next week. I cut the rear fenders two weeks back in anticipation of starting (look honey, I cannot change my mind now, it is even uglier....) I am hoping to remember to take photos, but I often get engrossed in the work and forget to eat or drink, much less record the progress. Before, mid-way and after happens to be my typical build log.
-
That is an excellent read, thanks for that. It is also great to know that sequence numbers are still available. I have an aggressive install schedule, but I can relax a bit about starting the paperwork.
-
He is making the delivery which saved me enough for the tail lights and other small bits. I've never worked with glass before either, so I'm glad you documented your challenges. It was part inspiration and motivation for me jump in. BTW, would you object to sharing where your SPCN fell in the range of 1 to 500? I'm trying to decide if I go into the DMV next week or if I need to wait until January.
-
So Cal Wiring Guru Needed! L28ET Wiring
Dan_Austin replied to ~KnuckleDuster~'s topic in S30 Series - 240z, 260z, 280z
Everyone has to start somewhere, but this is really basic stuff. You only have one battery ground, which is the first photo, provided it connects to the battery's negative terminal. The cable on the smaller cylinder (solenoid) should be connected to your positive terminal. As long as both are connected to the correct terminal, then the main connections are correct. There are smaller (10~12 guage) wires from the battery, one from the positive terminal to the chassis harness and one from the negative to a chassis ground, which would normally be only a few inches from the battery itself.