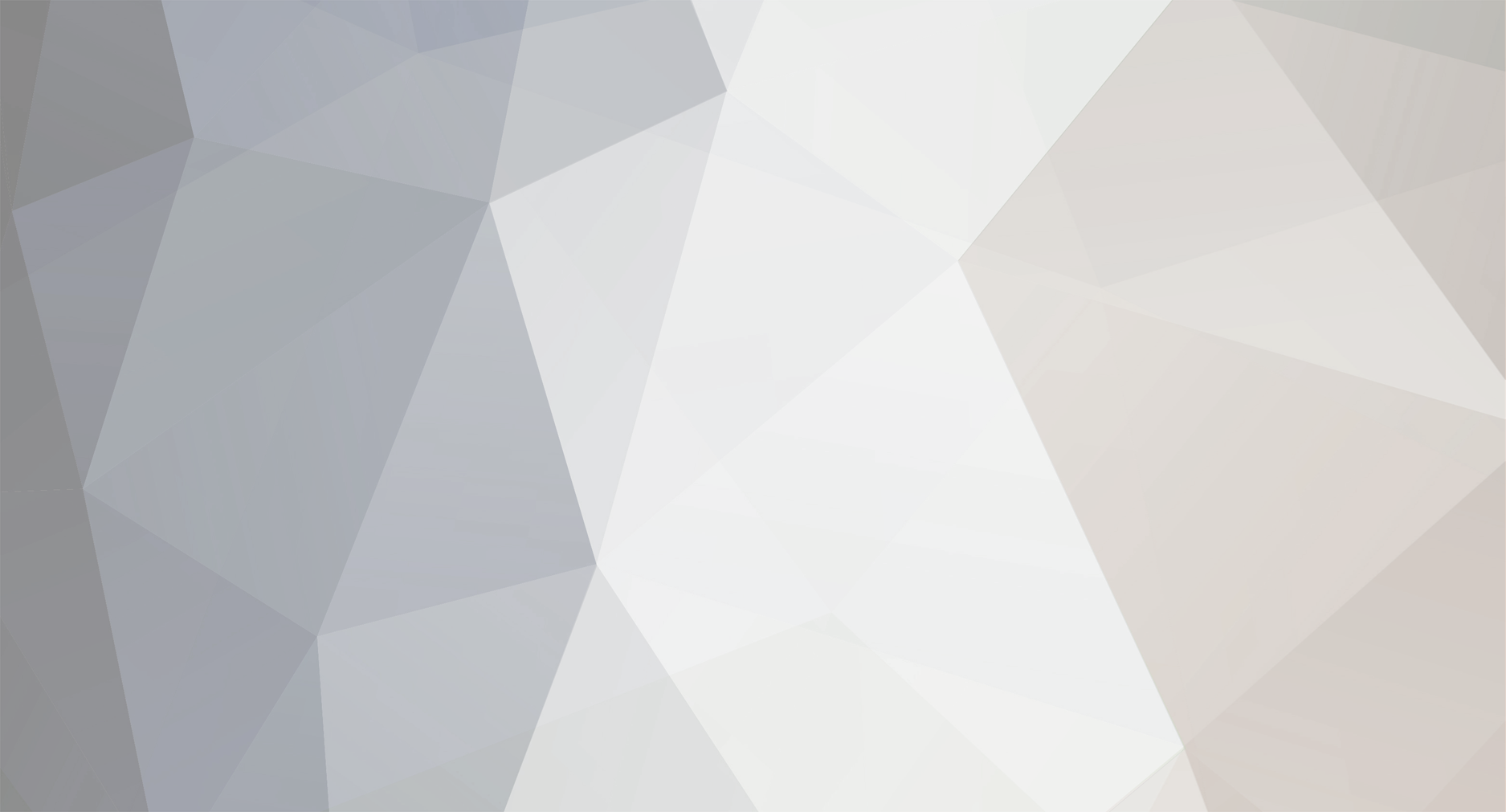
Dat73z
Members-
Posts
838 -
Joined
-
Last visited
-
Days Won
8
Content Type
Profiles
Forums
Blogs
Events
Gallery
Downloads
Store
Everything posted by Dat73z
-
I doubt we'll see a resurgence of forum activity. I agree with @Derek, the trend since 2010 or so has been towards short-form social media, soundbytes, instant gratification scrolling, and now AI. Unfortunately e-commerce has basically all but migrated to other platforms as well so it's near impossible to fully unplug if you're looking for parts. We're a small remaining userbase but I think we can at least keep the HybridZ discussion boards alive. Which are good reminders, just put in my donation to HybridZ operating costs and time to put down the phone 😁
-
A musician's therapist (The $300 Z)
Dat73z replied to Zetsaz's topic in S30 Series - 240z, 260z, 280z
Looking forward to your feedback on the Resurrected Classics seals, I've been meaning considering that or Vintage Rubber. My experience so far with various companies and seals is can be hit or miss depending on the specific seal. Hopefully everything fits up well for you 😁 -
@calZ I agree, the logo location is unfortunate but I'm running with it as I'm working around various clearances and I didn't find great options. Given all of the modifications required of any cover, I had also weighed making my own but PTZ cut me a great deal 😁 I suppose the silver lining and eye opener for me was how much more aftermarket there is now for r200s than when I was looking to build one 10 or 15yrs ago. Just the availability of monolithic chromoly conversion stubs alone versus welded options is huge. @Zetsaz if you run the older r200 style covers you also need to open up the mounting flange bolt holes as they are upsized from m8 to m10 on the more "modern" r200s. Attached are some pics of the machining operations on the cover for a better idea. Unfortunately still delayed for my chassis to get scheduled in so I think I'm going to do some more fabrication and welding on various aspects while I wait so the shop won't need to worry about it. I've been hesitant to get too far into the bodywork at home as our garage is attached and my wife doesn't like the mess and chemicals 😂
-
Quick weekend update. I picked up the diff this morning and it came out great. Some people had asked me to share what it takes to build a r200sn q45 diff as they aren't typically built, and as a result there isn't much info out there on these. So I got to be the guinea pig and put my own money and time down to find out 😂. Most, myself included, tended to run these diffs as cheap junkyard specials over the decades but as they've aged over 30+yrs all of the bearings and viscous LSDs are worn at this point. This one in particular came off of a turbo nitrous v8 drag race s30 and was starting to get noisy and show signs of metal in the oil. The builder, Weir Performance, is local to me and has set up a lot of Formula D cars over this past couple of decades and are very knowledgeable on Nissan R200s among other types. Having been around for a while they also make custom parts for diffs and actually have a full machine shop in-house working on other industrial projects. Basically the formula for this diff is s13/14 240sx OSG LSD, custom equal length stub axles that Weir has made in Italy with the stronger q45 6 bolt pattern, and a 39/11 r34 GT-R ring and pinion. I think the important things to note are OSG, unlike other brands like KAAZ, don't make a LSD that fits the q45 unequal length stub axles. The ring and pinion swap is due to the Nissan street car style diffs running smaller toothed gears, I believe the q45 was a 46/13, and the high performance cars like the GTR came with larger and stronger toothed gears in this case a 39/11. I also had a PTZ rear diff cover custom machined to clear the ring gear, open the bolt holes from Datsun to modern r200 case sizes, and also milled off the logo for more of a low-key look. The PTZ cover was needed to change the bolt pattern to suit the Escort rear end setup so I couldn't just run any r200 cover. I could write a lot more detail but I think those are the key points for anyone wanting to build a q45 diff.
-
It's been a while but I've been getting back into the build this week. Since the last update the chassis is waiting to be scheduled in for restoration hopefully next month and I got busy with house projects, which coincidentally led me to South Florida where I picked up a Nissan competition oil pan from motorsports legend Greg Ira. The oil pan has seen better days with some motorsports style clearancing and a bunch of JB weld slathered over the side which after torching turned out to be covering a large crack. I think it's an interesting piece worth saving, and as the pan needs work it seems fitting to further modify it. The plan is to repair the cracked area and also weld some reinforcement along with a -10AN turbo oil drain. I'll try my best to straighten everything out then have it re-zinc coated. I also received word that my r34 GT-R geared Q45 OSG LSD diff is done so I'll dedicate a post to that when it's back in my garage.
-
The actual ZCD L brackets themselves were not consistently bent. The widest gap I measured was almost 1/4" which I suppose can be filled in with weld, but is absolutely unacceptable for my standards. There's definitely a spectrum of skill and expectations when it comes to metalwork. My buddy had floors and rockers put into his 60s mustang by a mobile welder...sure it had new metal but the fit and welding was terrible. I took the time and massaged the metal to 0 gaps all around on both rails before welding. I shouldn't be surprised at this point tbh, even the door hinge kit from ZCD was garbage. I ended up having custom bushings machined after zinc coating for perfect door actuation. With that said I probably won't learn my lesson and will order more stuff from them to fix in the future 😂.
-
The car is headed off to the bodyshop on Mon so I figured I'd do some final welding and chassis prep to save some labor. What was supposed to be a couple hrs turned into several mostly due to the poorly fitting front sway bar reinforcement plates from ZCarDepot but nothing a bunch of relief cuts, hammer, and brake time couldn't fix. If there's a next time I'll bend the reinforcement plates consistently myself as that may have saved me hours having properly bent brackets from the start. I haven't actually seen any pictures of how others did theirs, so I'll post these up for reference. I have done quite a bit of overhead mig, but never overhead tig and on my back so not my best work but it's under the car 😅
-
Last night I was disassembling the cooler packaging and snapped a quick picture of the frontend. It's interesting how the sheetmetal of the s30/s31 changed over time. On the later s30s a lip at the top of the core support was added (missing the seal in this pic), as an improvement to further force air through the coolers. On some builds I've seen this lip cut out for intercooler or other mounting. The lower support was also changed for the impact bumper, which also affects the valence mounting for the 73 year.
-
I'm not a fan of the bolt-in s30 Autopower roll bar or cages overall but they have their place and purpose. Today got busy but I managed to squeeze an hour in check the final fit of the roll bar and prime the floor in, which gives an idea of what things may look like painted. I'm planning to run full interior and custom carpet so it'll all be hidden anyways. The bodyshop also let me know the rotisserie is ready for my chassis. There are probably a dozen other things I could do on this but I'll leave it to the shop as they're going to paint the entire underside, inside and outside.
-
Yeah the geometry of the s30 is just difficult. I am also tall and every s30 with an off the shelf roll bar or cage (autopower 4 and 6 points come to mind) has put the main hoop at my head or had some combination of factors making the seating position awkward. I would definitely go custom. Last night I was able to mostly stitch weld everything in. Not my best work but I was getting good penetration so I'm confident it's strong. Every weld was done crazily out of position with the foot pedal on the floorboards or contorted sideways with with a leg out the door 😂. I'm really hoping I can wrap this today as I need to move back to welding in the engine bay.
-
@calZ here's some pics and rough measurements. I believe the roll bar is designed to fit around most the interior of the car, with some areas such as the interior quarter panel pieces requiring trimming around the bracketry. Also, to my understanding there were only a few of these roll bars produced and I'm not sure if or when more will be made. A quick mid-weekend update: I finished fabricating the rear deck plates by welding in captive nuts, weld through primer on all surfaces, then tacked the rear plates in. With the main hoop torqued in the plates are in perfect alignment for the fasteners to thread by finger. To be honest it was a huge pita timesink to straighten the floors where possible for tig prep, but I'm glad that's all done. A friend mentioned that in-period the plates would've probably been mig welded in, perhaps poorly with mig wire sticking out so sanitary tig dimes are probably going to look out of place 😂. Now I just need a couple of hours to take my time and stitch weld the plates then finish with some self etching primer.
-
Some quick photos of the Nissan comp OE type roll bar test fit to determine the final position of the trunk floor plates. The roll bar is an absolute work of art made by Romas at DCW Classic. I've definitely learned a lot about the racing history behind the s30 and am grateful to have made many new friends all over the world this past couple of months, exchanging notes with experts in the community such as Romas, Alan T, Kats, Chris, Florian, and many many others. This build definitely would not have been possible without the support of the community. I started flattening the trunk floor for welding yesterday but I think I'm going to take a break for a day to fully prepare the welding areas and work through the interior overall which is covered in old sticky adhesive/tar remnants.
-
Continuing on chassis reinforcements, the Nissan comp OE type rollbar will be delivered later today. The OE type rollbar bolts to the existing m10 captive nuts above the rear tubs and also to the trunk floor straddling the reinforced u-channel between the rear shock towers and rear suspension/driveline mounting points. For the floors I've started fabricating some 6"x6" 1/8" steel doubler plates which I will weld some captive nuts as they do in the JDM then stitch them in with the tig. In preparation for this, I bolted in the Escort 1 piece rear end which will stay in place for fabrication. Given the reinforced structure of the rear suspension points, I don't think things will move around but just for peace of mind that everything bolts up properly before and after welding. I've learned my lessons over the years from welding warpage and fixing my mistakes with blocks of wood and BFHs 😂 I also decided to mock up the PTZ cover one last time to verify dimensions before machining and I'm not sure how I got this so wrong but everything fits. I was under the impression that the Escort geometry was the same as OEM so maybe the T3 geometry is different. Not a big deal either way, as the front diff mount needs a bit of refabrication for the exhaust and shortening the AL driveshaft is straightforward. I also have some spare Q45 diffs I could blow apart and check for fit, but I'm running out of time and need to do some other welding and misc. chassis work before it goes on a bodycart for transport next week.
-
@Zetsaz a lot of my friends have been doing the same 😅...not a bad move imo if you're planning to use the parts. My OSG LSD actually came in a month or so ago before this whole mess but as we've seen things can change by the hour lol. One thing to look out for is some importers have already been upcharging 25%+ for "tariffs" even though they aren't fully in place yet. I was asking around this past few weeks and got similar stories from a lot of 3rd party importers so maybe they were anticipating and charging the 25%+ upfront to be safe, but who knows if they would've pocketed the fees or refunded those extra costs if the tax bill didn'tcome in. I ended up ordering parts direct from JP companies like Escort and they did not charge me the thousands of extra in "tariff" fees, they just let me know if it's stopped in customs I would need to pay the taxes to get it released which has always been my experience prior.
-
Last month blew by but good progress has been made on the chassis. This next few weeks I'll need to finish stripping a few things off the chassis and get it loaded onto a body cart for transport in May. Due to the uncertain tariff situation I procured a few parts I was initially planning to order after the car goes out. I decided to eat the costs now as prices could potentially increase 25%-200%+ on the US consumer tax side and who knows how sticky that will be. For the turbo build refresh I wanted to beef up the chassis and rear end. A few weeks ago I dropped off the Q45 diff for a full rebuild with R34 GT-R 3.54 gears and a OSG Super Lock LSD. My rear end was also already structurally reinforced and plated in, but I decided to take that a step further with a Escort JP single piece rear end. I also received a PTZ rear finned cover, which I will need to perform some machine work to fit. For additional chassis reinforcement, the OE type competition rollbar should arrive soon. It's more of a historic/obscure part but I'll post some mockup pictures for anyone who's interested.
-
@DuffyMahoney the raised aspect of the manifold is for packaging. I think l posted these pics before, but here's what you're working with on high mount turbo setups and surge tank/induction boxes (ignore the cold side charge pipe wonky angles I will fabricate a new one later). Early on I referenced the dimensions between a few other manifolds I had (SK/FET/Mik). The form is really dictated by making everything fit and function properly, and as you can see space is at a premium.
-
@DuffyMahoney yes balance bar with takeoff ports in my case for BOV, timing control, brake booster, etc. The takeoff ports are separate from the 1/8 npt ports you can see on the runners which may be used later for direct port nitrous or other injection. Also modular rod holder. I'll do a proper photodump and full post later but it is a clean sheet design by Larry Asp at Revery Performance so you likely see some similarities to other manifolds he has designed including one I've seen on a SEMA Z. The concept here was the ultimate mid-runner high clearance manifold. The geometry is such that it clears even high mount turbo manifolds such as the ProtunerZ vband custom I am running along with providing adequate clearance to run a surge tank or air box. We went through several design iterations over 2 or 3 years (I took a ~1yr break from my Z to finish building and selling a couple of other cars before starting back on this build late last year 😂) and found the ideal packaging in the s30 chassis. Imo there are a lot of novel design features present here which are missing from any other offering on the market today such as the o-ringed balance bar, ability to isolate individual runners and sync check without pulling the airbox/surge tank, etc. I'll cover the aspects later when I get past paintshop crunch time. I can't say enough good things about Larry but he's an incredibly talented designer and incredible to work with. I'll be showcasing more of his work soon 😁. If anyone is interested in getting one of these manifolds or anything custom made reach out to him.
-
Still going through prep work on the chassis but a quick turbo update. Got the custom cnc intake manifold in and couldn't resist unboxing. I'll dedicate a post to this later when I get it fully set up but I snapped a pic on the dining room table before it goes into storage for a while 😁 Next up will be the cnc fuel system components and there are a couple of concepts I have in mind from OEM performance blowthrough cars such as the Lotus Esprit Turbo I'd like to implement and have parts machined for as well.
-
This afternoon I checked the mid-section of the exhaust. Looking at reference pictures when I had the cd00a in the car I will likely need to section the front of the exhaust right before the twin resonators and build the merge to carefully run around the trans mount and case. This will also allow the exhaust to suck up into the tunnel as the AE trans mount hangs much lower than the OE mounting arrangement. What will be interesting is if I can fit a flange or dual vbands on the resonator end. As with most everything else on this build it'll be crazy tight but I think doable. Something to look forward to when the shell gets back in.
-
Another crazy week but I've been making some progress on the Z in the evenings. Last week I threw the spare rear end setup back on to mockup the NOS Reinhard twin 60mm exhaust and see if the Escort Japan rear end setup will work. My rear end setup is far from stock as everything is structurally reinforced, boxed in/plated and welded out but the geometry to the LCAs/caps is the same. What I found is: 1. There is about 4.75" (4.5" to be safe) from the r200 case rear cover flange to the rear pipe. 2. There is something like 0.5"-1" to the rear caps if I account for adjusting the system fit. 3. I will also need to trim the r200SN front mount a bit to pull the exhaust into the early s30 twin pipe rear crossmember cutouts. 4. I also had to trim the front exhaust mount to clear the r200SN but like my last custom exhaust I'll tig in a new bracket which will turn the mount 90 degrees for clearance. I also left some of the original mount there to triangulate the new mount when I tig it in. Fitting up the system it's pretty evident it is exceptionally high quality, a work of art. It was near impossible for me to actually find any pictures online and I think most people who have posted just purchased the muffler or back boxes with custom piping so I'll photodump a bunch of reference pictures. Maybe in another 10 or 20yrs someone will also be doing the same off these grainy pictures 😂 I'll check the center section as well and upload pics of that later but am most concerned about getting parts on order for the diff rebuild.
-
Thanks @madkaw, I'm checking that out now so I'll see how things look. Quick update on the turbo build I unboxed a heatshield from Datsun Spirit and test fit it up last night with the restored SK50s and Surge Tank. I think it'll work well with some slight modification and perhaps add a secondary layer with an air gap. I'll also need to drop the engine in one last time to double check the turbo cartridge clocking and hot side clearances before welding out the elbow. I have about 2 months left to go before the bodyshop so I'm minimizing the time spent diving into specific aspects of the turbo build unless I need to. Mostly I'm test fitting things to ensure I'm not missing any packaging considerations on the chassis. Any other fabrication work can wait until the shell is at the bodyshop.
-
That's good to know on the Q45/Z32TT wheel bearings. No I am running 280z stubs with the Q45 CVs and custom Moser cut shafts. I looked at the t3 Q45/Z32TT option a couple years ago when swapping out my t3 Konis/GCs and wilwoods and parts availability was definitely a concern. I ended up locking in on the KW and Stoptech setup for the long-term, so my weakest link is still the stubs 😅
-
@calZ sounds good I'll send you a DM when the time gets closer. I agree it's typically about finding the compromises you're willing to live with 😅 I've been continuing the prep process for the bodyshop and realize I need to check some clearances/brackets on the rear end. A few years ago I imported a NOS Reinhard full 60mm twin exhaust for this build. I figure the twin 60mm should be as good for single or twin turbos. My Q45 r200 is getting rebuilt with a OSG LSD and for the rear end I was thinking of upgrading to all Escort Japan pieces including their extended rear diff cover. The problem which may present is how the r200 (and so far as I can tell the vintage Nissan Comp systems) wrap around the rear of the diff. I only have one grainy picture of a full Reinhard exhaust installed so later this week I'll test fit it up with a spare diff to see.
-
@Zetsaz there is no baffling inside the VTS tank other than the formed center area. However, the formed center area fully blocks off the fuel towards the rear of the tank which perhaps has some benefit under acceleration/cornering but overall I'd say it's comparable to the OE tank. The main benefit (other than being poly) is the formed recessed component mounting area. I think earlier in the thread I showed some pictures of the modifications on my OE steel tank which required quite a bit of cutting/welding/waterjet custom tank ring for the fuel cell plate. I also sealed off the stamped center baffle and added one way valves. Either way nowadays there are a lot of options for fuel slosh control such as Holley Hydramat, Aeromotive Stealth System, in-tank passive/active surge tanks, fuel pump trays, etc. Each has their pros and cons but that's a separate topic 😅
-
@calZ if you are referring to the adapter ring there are no links as it is a custom one-off piece in design. What you see in the pics are the developmental 3d prints before machining and finishing. There are a couple of minor things to sort out I didn't show such as an integrated fuel sender with roughly the same ohms sweep as the s30 gauge. If you're interested in getting an assembly let me know and I'll get some pricing for you when the time gets closer to production. Lots of irons in the fire right now, but I'll dedicate a post to the updated fuel system later like the custom cnc intake manifold.