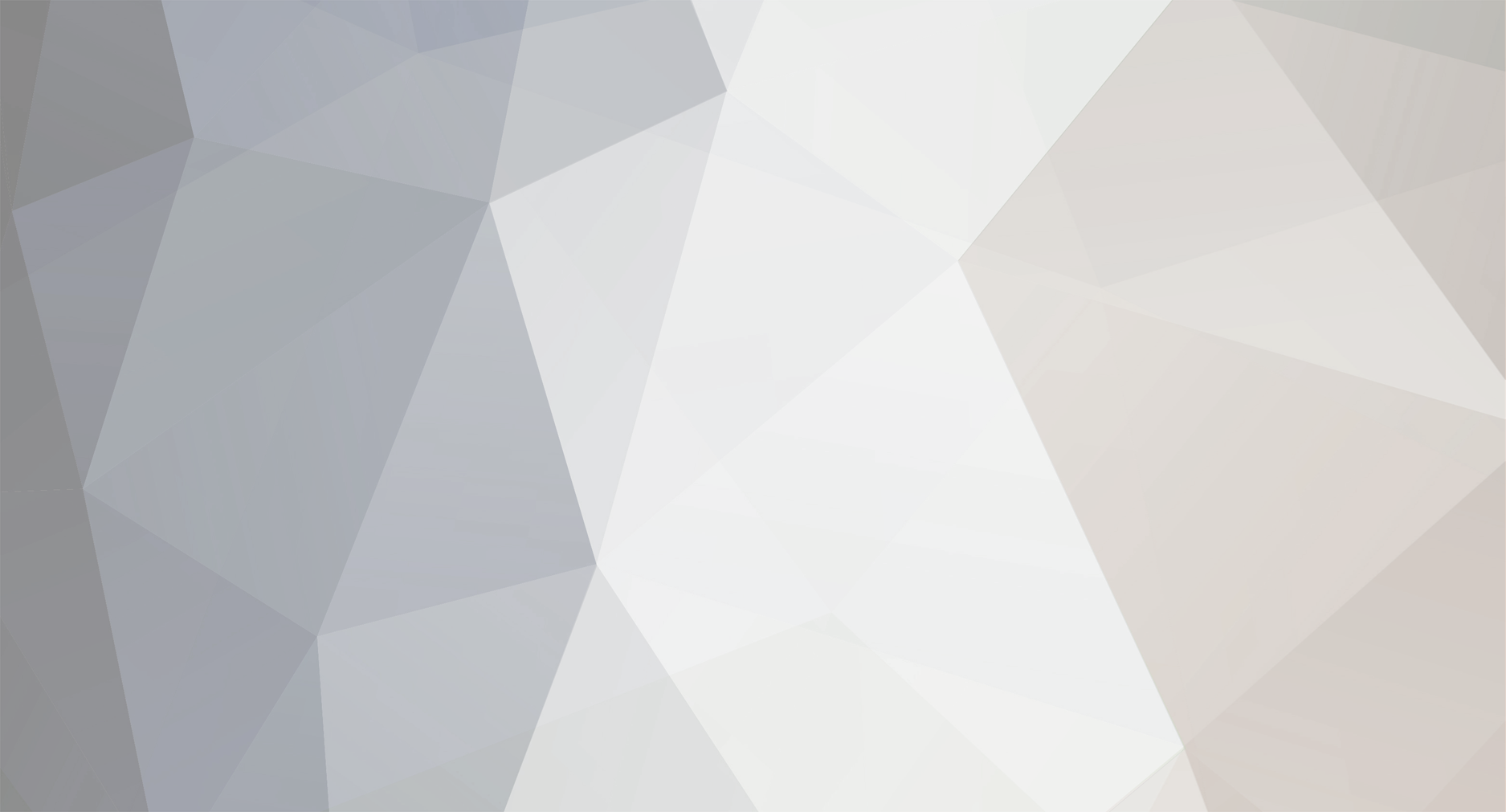
Dat73z
Members-
Posts
840 -
Joined
-
Last visited
-
Days Won
8
Content Type
Profiles
Forums
Blogs
Events
Gallery
Downloads
Store
Everything posted by Dat73z
-
A musician's therapist (The $300 Z)
Dat73z replied to Zetsaz's topic in S30 Series - 240z, 260z, 280z
Your car looks really straight but was it ever in an accident or are the moustache bar studs off on the chassis? That spacing to the spare tire well looks really tight. I would think others with the same setup would be complaining about that. Did you ask T3 about what's going on? -
Also before I forget huge shoutout to Harold Burroughs @ https://www.stuffharrydoes.com/ He fabricated me some reinforced engine mount brackets which will allow me to fine tune the angle and tilt of the engine. In my case I want to optimize the balance between the required carb angles and height/tilt of the engine to get more clearance for a strut bar or whatever bracing will eventually go in the front.
-
Just some quick updates, the build has been going on in the background. Life has been busy so I've only been able to put a couple hrs here and there. Still waiting for parts, mainly the ZCG stoptech brakes. I'm also getting a tubular manifold and DP set up for a Garrett G30-660 0.83a/r turbo and Tial MVR 44 wastgate. Originally when I went with the t3/t4oe hybrid I thought I was going to be doing a l25/l28, but then life resulted in the 3.2 instead. Once that gets in I'll check clearances then off for inconel shielding again. The new turbo tech should provide better response/spool even with the larger sizing and it is also all vband in/out so hopefully the hardware stretch issues I had before won't be an issue anymore.
-
@Tank did you ever get the T3 micro kit on? I'm curious how the clearances look. On the large t3 BBK the largest issue I found running small 15" wheels and lower clearance barrels like the R types was the calipers depth in relation to the rotor top hats. Wheels like the 15" Rota RKRs with good inner barrel clearance fit fine even with the large t3 BBK front and rear with the ebrake. The ZCG stoptech kit I thought was better all around in terms of size and packaging but it's a long wait for the kits.
-
Awesome build. Looking forward to your updates on the sound system and interior 👍
-
It's crazy how quickly time flies when you're busy but this weekend I'm getting back into the build again. I've been pretty on/off due to personal commitments but things have been moving forward. I have some buddies coming by this weekend to swap parts which will be nice to clear out my space then it'll be a few days of prepping and bolting on new parts. I feel like I've rebuilt the car a few times at this point, but the nice thing is you can basically shell swap a s30 over a weekend if you had everything prepared.
-
Based on your driving style it sounds like you'll be fine with sticky 245s. Fwiw I'm probably putting down half of what you are and on 225 r comps I can easily spin at speed if I don't roll into it when boost comes on so I've been eyeing 245 45 16.
-
Depends on your humidity. Where I am, things stored in the garage don't rust for years. If you're in an area where flash rust occurs quickly I'd oil it for storage and acetone wipe it all down before reassembly.
-
What tire compounds are you running and how do you drive the car? At those pwr and trq levels, I can imagine doing rolling burnouts on 245 R comps when the boost comes on
-
I was curious so I took a look at Godzilla Raceworks site and it looks like they sell a 24x12x3 intercooler with their kit which has the bent bracket above the rad support. My IC which is mounted below the rad support is 27x12x3, and I can actually fit a 4" core with both a large oil cooler + small ac condenser and retain the hood springs. If you remove the hood springs you can fit an even larger IC if you need it, but you'd likely need to angle it a bit. This is on a 240z so on a 280 with the taller support you can probably fit an even larger IC. The brackets are easy to make (couple bends and holes). Fwiw
-
I had the same thought years ago and decided to keep mine. The thought being that it would help channel more air through the coolers. You can still mount the intercooler below that lip and there is plenty of room for a large core, moreso with the 280 rad support. On the 240s I think they may have been 73 only and you can also put a rubber strip across the top to seal the area more. Curious what others think
-
A quick update, life has been crazy, parts are still trickling in and hopefully I'll have everything within this next month. Apparently OE Nissan s30 MCs are ridiculously expensive now and 50mm carbs are going onto the build. Hopefully I'll have more time to post updates soon as a lot has changed
-
Got some more wiring done while I'm waiting on other parts which have been trickling in. Not sure why but the shorter KA/SR trans yoke dust covers were NLA for years then they came back in stock recently so I ordered a few and they just came in from Japan. My current JDM SR trans is missing this so I'll tap it on later this spring.
-
I had a few mins after lunch so I went ahead and swapped the gauge housings and rear mount brackets to test fit. So now the early 280z voltmeter bolts into where the ammeter used to go. Now that I've verified the fit I'll tear it apart for restoration and rewire it all to mate with the OE 240z harness.
-
Realized I haven't updated for a while but the build has been going on in the background. This past few weeks I was waiting on electrical parts so I fully stripped down the suspension as I have a new set of coilovers and brakes going on. Today my voltmeter finally showed up so I'll start gauge swapping later this weekend.
-
http://www.vintageconnections.com/
-
After some research, I saw a lot of Z forum questions on how to get charge indicator lamps to work without many clear answers although it is a simple circuit and universal for many vehicles. I recall wiring in a few on motorcycles many years ago. I found a schematic I believe from a 280zx off atlanticz which shows the circuit. It seems the charge lamp will be between the L terminal (switched ground) on the alternator and 12v switched ignition. So if my understanding is correct, when the engine is off or a charging fault occurs, L will approach 0 providing the ground for the charging light to go on. Next I will need to research if it's better to have ring and/or spade terminals or if the set screw type terminals are acceptable for all of the stranded 12v ign wires I want to consolidate on the car. The set screw type power distribution solutions are generally more compact, but seeing as my car vibrates its fasteners loose regularly I'd be concerned wires can vibrate loose or fatigue and shear over time.
-
This AM I assessed what needs to happen. I ordered 10AWG gxl wire for the fuel pump dedicated power and ground circuits, and 12-14AWG txl wire for the harness repair/uprating. For the walbro 255 I think the final 2 foot pigtail to the pump is like 14 or 16 AWG, so it's questionable what a 10 AWG dedicated feed/ground gets me, but at least there will be limited voltage drop and headroom to upgrade the pump later. Since I have this all torn apart and my 12v ign and a ground wire melted I have decided to pull all accessories off the harness and into a dedicated distribution panel to avoid this in the future. I currently have: (1) fuel pump trigger, (2) boost controller, (3) o2 sensor, (4) tachometer, (5)msd 6ald. There are several fused/relayed compact powersports solutions I'm eyeing for this. I'm also planning to swap in an early 280z voltmeter and built the charge light off of the alternator L circuit as my amp meter doesn't do much with the internally regulated alternator. This will also be an ideal time to fabricate the AC system but I also want to drive my car this spring so perhaps it'll have to wait until winter again. Hopefully I can get everything ordered today then as is usual it'll be a couple week wait for the parts.
-
Next week my schedule looks terrible again so I decided to press forward and get to a good stopping point. I finished unlooming the dash harness and found the extent of the ground and 12v ign wire melting stopped where they respectively tied into larger branches. I noticed also some damage in the harness where the previous owner had spliced into some areas back when the car was drawthrough turbo in the 80s for the boost gauge, water/meth injection, etc. Generally, this harness is actually one of the nicests 50 year old s30 harnesses I've worked on, not far gone enough to warrant replacing everything. So I think the strategy here will be to uprate and replace all of the ground and 12v ignition wires, along with the entire fuel pump circuit (green wire + ground is about it) on the body harness. I'll order some rolls of factory colored wires today and clean up the harness while I wait for materials to arrive.
-
This morning I started back in on unlooming the harness. So far I see 2 toasted wires. A black wire (ground?) And a black with white stripe (12v ign?). No smoking gun yet maybe they contacted at an exposed branch somewhere upstream.
-
And the main dash harness is out. If anyone knows how to swap to a 280z volt gauge from the 240z amp meter let me know. Tomorrow I'll start unlooming everything and hopefully not get too confused.
-
Today I got the dash pulled. I started tracing the damaged wire back from the fuel pump circuit. It looks like the black/white stripe which if I recall correctly is 12v switched ignition. I was using this wire to feed the 12v ignition leg of the oil pressure sensor to trigger the 12v relay to the fuel pump once that circuit closed under pressure. Now that I'm thinking about it, I had one oil pressure sensor start failing almost new but it was due to an oil leak due to a manufacturing issue earlier in the build thread and not an electrical issue. Hopefully I can get the harness out and decide what to do from there.
-
It's been a hectic few weeks but I've been inspired to get back on the build this weekend. Yesterday I had the opportunity to go for a ride along with a skilled driver then test drive a 3.2 NA stroker car with triples and the brakes I'm waiting on. I must say I miss being able to rap the throttles NA but the 3.2 turbo just sucks you into the seat in boost. The plan this spring has changed a bit as I've been inspired to revamp the s30s suspension a bit more but this weekend I'm going to focus on getting the main harness out.