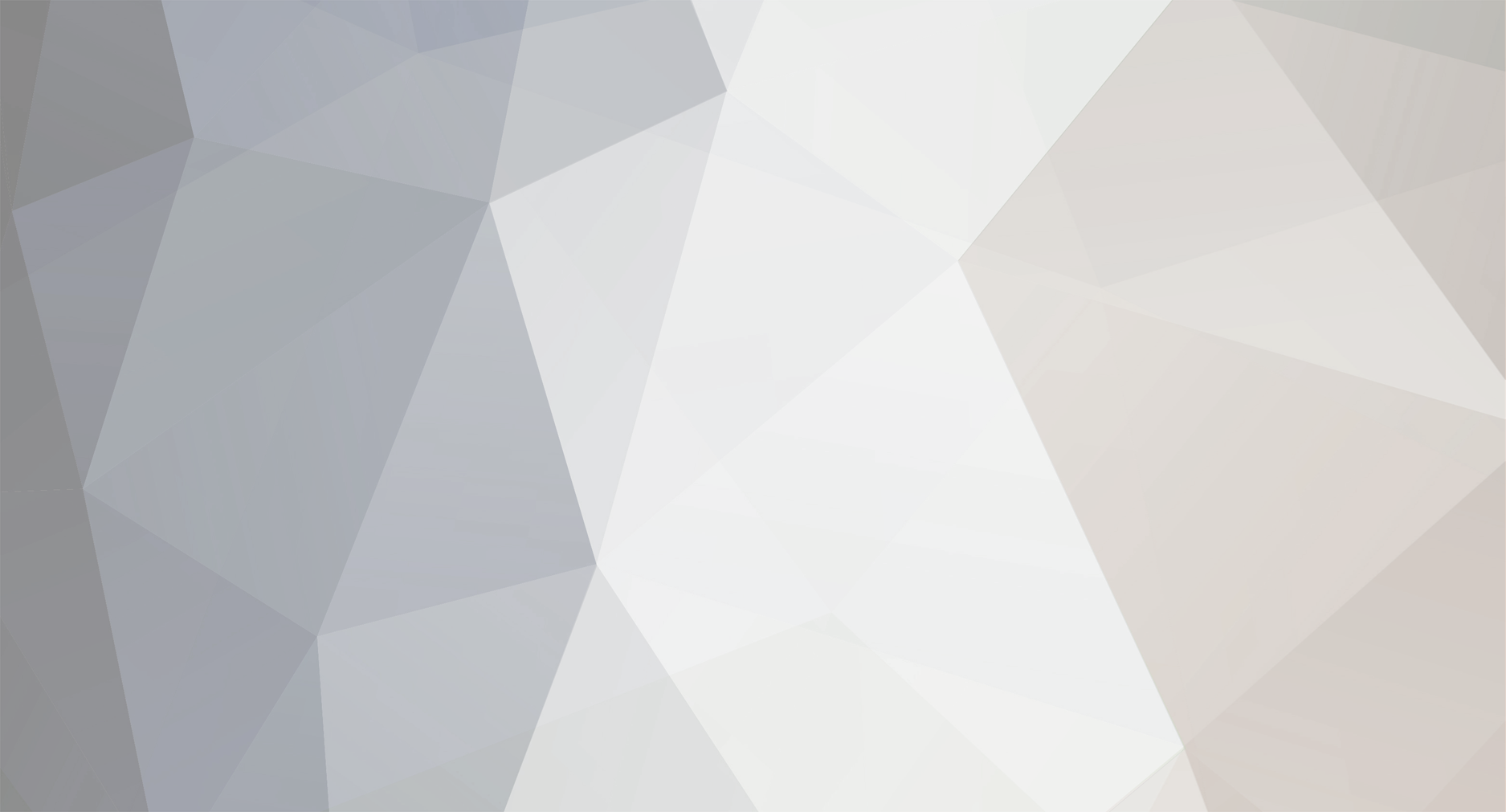
Dat73z
Members-
Posts
840 -
Joined
-
Last visited
-
Days Won
8
Content Type
Profiles
Forums
Blogs
Events
Gallery
Downloads
Store
Everything posted by Dat73z
-
@Zetsaz there is no baffling inside the VTS tank other than the formed center area. However, the formed center area fully blocks off the fuel towards the rear of the tank which perhaps has some benefit under acceleration/cornering but overall I'd say it's comparable to the OE tank. The main benefit (other than being poly) is the formed recessed component mounting area. I think earlier in the thread I showed some pictures of the modifications on my OE steel tank which required quite a bit of cutting/welding/waterjet custom tank ring for the fuel cell plate. I also sealed off the stamped center baffle and added one way valves. Either way nowadays there are a lot of options for fuel slosh control such as Holley Hydramat, Aeromotive Stealth System, in-tank passive/active surge tanks, fuel pump trays, etc. Each has their pros and cons but that's a separate topic 😅
-
@calZ if you are referring to the adapter ring there are no links as it is a custom one-off piece in design. What you see in the pics are the developmental 3d prints before machining and finishing. There are a couple of minor things to sort out I didn't show such as an integrated fuel sender with roughly the same ohms sweep as the s30 gauge. If you're interested in getting an assembly let me know and I'll get some pricing for you when the time gets closer to production. Lots of irons in the fire right now, but I'll dedicate a post to the updated fuel system later like the custom cnc intake manifold.
-
Haven't posted in a while as I've been busy blowing the car apart to a bare metal shell along with welding and rebuilding a bunch of stuff in preparation for the spring bodyshop dropoff date. For the turbo build I started prepping the tank for the in-tank FPG surge tank with integral Pierburg lift pump. I'll be running a single walbro 450 to start, with the option to run twins (3 pumps total including the lift pump) within the surge tank feeding through -8 and returning -10 directly back into the surge tank. Every fuel system I've ever ran in a s30 has been a compromise, so hopefully this will be the last fuel system I ever put together (for this car at least).
-
A busy start to the weekend due to the holidays but the plan is to get the mounting locations for the water/meth tank set and finish stripping out the interior. For the water/meth tank, I think the cubby area on the pass rear works well and it'll basically blend into the black interior when it's all back together.
-
@calZ I'm working to import the Mizukami Auto one and yes the exchange rate has been phenomenal 😁. Nils at JDMJunkies is running one on his Swiss s30 build and when I messaged him he had nothing but great things to say about the build quality, fitment, and how complete the kit was down to the weld-in floor plates. I also went down the rabbit hole of investigating other available option(s)/what is historically accurate/made some friends along the way lol and settled on the Mizukami bar as the most viable option for my needs. @A to Z The manifold is a novel clean sheet design from a very talented designer and friend. I'll dedicate a post to discuss the design philosophy and aspects when it's time to refocus on the driveline.
-
Thanks for the discussion guys, and no offense taken @A to Z. In terms of the scope, chassis modification such as full length frame rails will be carried out for strengthening among other aspects I'll cover later. I see 50k being repeated a lot not sure where that's coming from but this will be done to a high standard regardless. I don't think I've really posted much about the car itself or what it means to me but it'll remain frozen in appearance as a clean narrowbody car, without bodykits, big wheels, etc. It's more nostalgic for me that way and I've already shown early in the build thread, tucking 245rcomps under the factory arches. Not much to update here as I'm recovering from the rona but a lot of irons in the fire. Cnc intake manifold is in production, got some updates and very excited for that. Waiting for my water meth tank to get in and determined the location. Waiting for news on getting a Nissan Comp OEM style rollbar imported so I can weld the floor plates in for that. Also met with the bodyshop guys today to look over the car and the target date to get it in is May. Basically do all the remaining cutting, welding, and drilling before the shell goes on rotisserie.
-
Still feeling terrible but I'm trying to get all the parts back onto the engine to make space for shell tear down. Today I put the hot side parts onto the engine, and like most custom setups clearances are exceptionally tight so assembly order and angles all matter. I think if I'm feeling better next week some buddies will come over to help strip the rest of the shell. I should probably also find some roller suspension for traveling to and around the bodyshop.
-
Got super busy and had to take a break, but this week I got covid so I get to catch up on some unboxing and setup. Unboxed my shielded vband special PTZ and hot side components. Also my custom cnc intake manifold is in production so I should have that in soon. I'm changing directions a bit on the build. After years of keeping it a clean patina driver, I've decided to rotisserie restore the car at a local shop that does a lot of high end work for GTRs and other really sick JDMs. The target date to get it in is this spring so I'm going to finish all the bespoke fabrication work so everything goes together like Legos when I get the shell back in.
-
My plan is to eventually put a couple gallon anti detonant tank in the spare tire well area for volute or direct port injection. For my setup it hasn't been needed at 10psi on 91 CA pump gas and 8.5:1 CR but I want to double that with the new G series turbo. I measured everything out and few years ago for likely candidates around the engine bay area in front of the rad support would be taken up by the oil cooler and AC...which is the case now. The other area I evaluated was the washer bottle/clutch master area which could work but I really wanted at least 2-3 gallons of volume for convenience. Yesterday turned into a nice all day date with my wife so I didn't get much done. After soliciting some opinions from FB groups I decided to leave the lower condenser mount as-is to force air through the coolers. Doing nothing at all is less work and eventually I may redo the air ducting when I do a v3 cooler packaging update in another 5 or 10 years 😆 I considered serviceability when fabricating all of this, with good access to the rad hardware. The easiest location for a top soft mount without making new holes in the chassis seems to be bracketing off the top and/or bottom rad bolt(s), especially if I want the top intercooler air plate to remain independent but this would affect serviceability. Not sure what the best path forward is but I'll think about it over the week.
-
Thanks it feels good to be working on it semi-consistently again. I still haven't had my half day this weekend, but I had an hour tonight so I started final shaping the lower condenser mount. I drew what I had conceptualized on a piece of cardboard a few weeks ago but decided to freestyle it as I was filing things down. I could do a lot more but I think I'm going to punch some speed/air bypass holes on the bottom of the mount and call it. The mounting is Setrab sandwich style soft mounts with high temp silicone sheet. I'm going to try to wrap this tomorrow and weld in the top soft mounts to the intercooler air plate.
-
Things got super busy again but this evening I went ahead and hardlined the oil cooler. I'm a bit out of practice on stainless so I accidentally put a couple of tooling marks in the tubes. The line sections are short so I'll work them out with a hardened rod when I wash everything out and rebrush the finish for final assembly. It's one of those things where I need to remind myself to slow down and think things through otherwise I end up making more work for myself or waste material. I also hit the AC Hardlines with some steel wool and wd40 to get a uniform finish but it's is a bit bright for me. I may go back and redo those in brushed as well. I realize I keep getting busy so this weekend I'm going to try and dedicate a solid half day to wrapping up the turbo cooler packaging updates.
-
@calZ I actually got the fresh air duct idea from the v8 subforum here a few years back when brainstorming the AC setup. I don't recall the thread but it was a super clean silver Z and they ran the lines across the rad support to the pass side. HybridZ is an absolute goldmine of info so maybe someone will stumble across our discussion too and get some inspiration. There's a lot more going on with the AC install on this build I've been working in the background including inside the cabin (I'll update that ongoing thread in the Interiors sub sometime) but I've been trying to keep this thread mostly dedicated to the turbo aspects. For the cooler packaging I intentionally wanted to keep all the AC componentry all on the DS and the oil cooler all on the PS with the intercooler in front of and crossing between the two instead of single sided. So that's why I went through all the fabrication work so far...it would have been a heck of a lot easier to mount the oil cooler in front of the intercooler, run the AC lines much longer onto the other side of the car, etc. but that wasn't the vision
-
My workspace is a mess so this evening I started cleaning up before proceeding so I threw the intercooler back on to check clearances for the AC and oil cooler sections. I think everything looks good to continue fabrication. My welding station is currently set up for AL which it never is so I've been contemplating also hard piping the intercooler with aerospace wiggins clamps. Not sure if it's worth it for this ebay special as the clamps and separate weld ferrules are eye bleeding expensive but I'll simmer on it over weekend projects.
-
It's actually AL tubing but I was using stainless instrument benders to bend them. That's a good point on the sweating, I actually had the same question and emailed Vintage Air tech last year here was their response: "The only line that should sweat would the #10 suction hose/line, make sure this branch is insulated on the hardlines or metal sections of the hoses that are inside the cabin." So it doesn't sound like any of them should sweat but I'm not AC expert. I'm sure some insulation on the appropriate branches would increase efficiency so I may consider it at some point but I'm just trying to get the car back on the road first.
-
Life was getting crazy and I had to take a break from the project for a while but I'm hoping to get back into things this weekend. Where I left off I was mostly wrapped up the AC hardlines for the tucked AC setup. I have a workable solution which clears the intercooler/hood hinges + springs now but have some alternate routing in my mind for a cleaner aesthetic. The most limiting factor was minimum bend radii using my stainless hardline tools and basically I had to rely on changing directions to make the angles work in such a compact area. I think most people just say screw it and run softlines all the way around the engine bay 😂 I left fabricating the condenser soft mount brackets for last as I wasn't sure how much things would need to move to accommodate the hardline tool limitations so I'll focus on that next along with hardlining the oil cooler. Once that's all sorted, the intercooler can go back on and the turbo cooler packaging updates for this service will be complete.
-
Today ran away but I had an hour in the garage so I continued on the AC condensor situation. I sectioned and welded the no6 hardline from the condensor to the dryer. Due to the SS hardline tool minimum bend radii I need to rethink the routing a bit. Everything just barely clears the intercooler though which is the most important thing.
-
Just got back from a nice end of year vacation to some boxes of parts so I started back in on the build. I mostly finished cleaning up the turbo castings in preparation for welding, which to be honest I didn't realize just how bad the castings were internally until I started really blending things out. I also started bending up the AC hardlines in preparation for sectioning and welding. AL lines are super easy to work with compared to SS but all of my tools are set up for SS hardline fab so some of the bend radii are slightly larger than what I could probably achieve on the AL. -10 AN fittings also came in for fuel hardline, so tomorrow I'm going to drop the tank and start back in on the tunnel.
-
Some quick updates, still waiting for parts so tonight I matched the turbo compressor discharge to a cast 90 elbow in preparation for welding. I also picked up some 4943 tig wire which I'm excited to try out on a few components I need to weld. Next week, I have a few days off so I'm hoping to knock out the rest of the fuel hardlines and get caught up on some other fabrication work.
-
A musician's therapist (The $300 Z)
Dat73z replied to Zetsaz's topic in S30 Series - 240z, 260z, 280z
Personally I have almost solely used Hondabond moving onto 2 decades now and I always use an OEM oil pan gasket, rear main, and side seals. For the pan make sure it is absolutely straight all the way around verified on a flat surface, otherwise any slight bend or wave and you'll start leaking again. This includes the bolt holes which can get dimpled and ovalled. I got frustrated enough with the OE pan that I eventually went AL pan with a machined flat surface. -
A musician's therapist (The $300 Z)
Dat73z replied to Zetsaz's topic in S30 Series - 240z, 260z, 280z
Take a really close look at those side seals as well. I did a rear main once on an L then got to do the job all over again along with the pan when I got the car back together realized the side seals were also leaking, masked by all the oil and years of grime on the rear of the block. -
Now that the year is finally winding down I'm actually able to spend more than 30min blocks at a time working on the car. Tonight I measured things up for the condenser hardlines and bent up some tig wire as templates. I also ran the AC softlines into the DS fresh air duct as the intercooler takes that up on the rad support. Basically it'll be a tucked AC setup. I could probably have most of the AC system invisible in the engine bay actually, if I was willing to exit the softlines into the fenderwell. I'm also contemplating fabricating a AC line bulkhead using the OE rad support holes like I did for the oil cooler. It'll add complexity and parts cost to the project but like the oil cool I think it'll be a cleaner solution. With the holidays I probably won't get any materials I order until the new year anyways so I guess I'll sleep on it and decide next week.
-
I wrapped up the fuel system mounting in the engine bay and realized I was missing a couple of AN fittings so while those are on order, I moved back to the cooler packaging. While the AC drier can really be mounted anywhere, including the cabin I wanted to keep everything tight in front of the radiator support. After some further mockup and measurement I realize I'll need to hardline most of the condenser packaging, as the packing including the trinary switch is just too tight for soft lines. What I found interesting about AC hardlines is there are no handheld tools that I could find to produce AC oring flares. Everyone I called who produced hardlines mentions they have some large proprietary hydraulic machine. So this limits me to purchasing pre-flared lines in varying lengths, such as those from Vintage Air, to bend myself and/or section and tig weld back together as necessary.
-
A musician's therapist (The $300 Z)
Dat73z replied to Zetsaz's topic in S30 Series - 240z, 260z, 280z
I'm also going to Vintage Air hardlines to clear all of the cooler packaging, and running everything else tucked on the DS reduce bulk. Another option are the EZ Clip style lines and hoses from Eaton, Vintage Air, etc. I'm running those in the cabin and they're much smaller in diameter with much tighter bend radius than traditional AC softline. They can also be disassembled for service or re-clocking unlike the crimped soft lines. -
Last night I mostly re-laid out everything on the firewall, close enough to finish fabricating the rest of the lines at least. Sort of tempted to start welding up the unused holes in the engine bay and shave things a bit, but I know that will turn into a major project so saving it for when I repaint the entire car someday. It'll also be interesting to see how the bulkhead heater fittings I put in for the vintage air will look with the OE hoses, but won't get that full view until the engine is back in.
-
Last weekend my buddy came over and we pulled the motor as it made sense with all of the work going on. Everything only took about an hour and honestly I think we spent more time eating at a buffet and catching up afterwards 😂 Everything is easily accessible now so the plan is to finish up the hardline work on the chassis + setting up all of the new turbo and manifold(s) on the engine stand. This past couple of evenings I've been bouncing between projects, but for the turbo rebuild redoing the fuel system to -8AN feed and -10AN return SS hardlines. The physical dimensions of all the components are much larger, but through careful fabrication I'm able to mostly reuse the mounting locations from the prior setup limiting any new holes. Earlier on the fall I also had new -8AN and -10AN hardline clamps machined for the tunnel so later this week I'll start fabricating up the new lines into the previous mounting locations with the new clamps and around the new CD00A transmission which occupies a lot more tunnel space. SS hardlines, especially in large diameters are always challenging for me but I think the end result is worth it. This will also likely be the last fuel system I put into the car because I can't see a scenario where I'll need larger than -10AN and -8AN with 450 pump(s) on a L series.