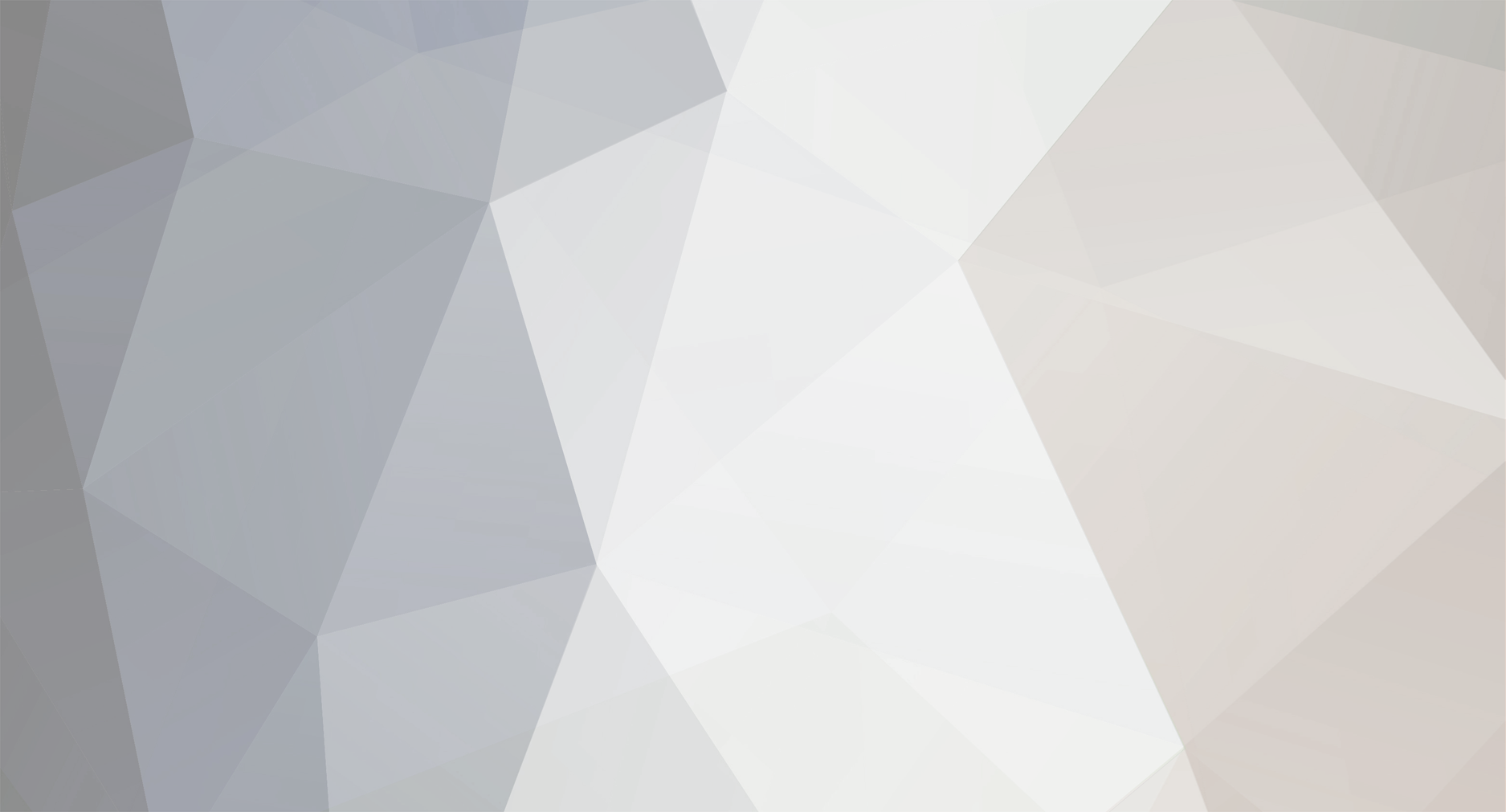
Dat73z
Members-
Posts
840 -
Joined
-
Last visited
-
Days Won
8
Content Type
Profiles
Forums
Blogs
Events
Gallery
Downloads
Store
Everything posted by Dat73z
-
This winter I've been making good progress on various aspects the build, but most importantly getting back into the groove of one mini project per day. Tonight I diassembled the frontend of the car to revisit the cooler packaging. In the last iteration of the build I had intentionally left enough room to mount a half-size AC condenser, which are popular for other turbo cars such as evo's running large forward facing turbos. The packaging is extremely tight as I wanted to retain the hood springs while running a large oil cooler and condenser behind the fmic. I also left enough room for the option to run a 2" thicker core fmic in the future. I did have to mount some new PIAA horns as the OEM units would not fit. After some measuring, the plan this week is to SS hardline the oil cooler from the bulkhead fittings as although everything is functional I've never been quite happy with the SS braided hose. At the time I also didn't have the 10AN SS hardline bending tools and materials which I now have. Perhaps this will allow me to bring the oil cooler further to the pass side and give the condenser a bit more room as well.
-
Poly tank from Vintage Tank Solutions install discussion.
Dat73z replied to Derek's topic in Fuel Delivery
Look forward to your updates @Derek. I'm hoping to get to my VTS install early next year once I get some adapters machined for my in-tank surge tank. I agree all of the vents on the later 240z tanks makes a difference. I recall when I was deleting vents many years ago on my 1973, I ran into issues where I actually could not pump more than 1/2-2/3rds of a tank due to trapped air which was a major nuisance. So I went back to all OEM vents and the issue went away. -
Trust me when I say the heat from the turbo hot side effectively into your brake master cylinder and reservoirs even with a heat shield is not a good idea. Cruiser or not, it is dangerously close just from a heat perspective let alone movement of the driveline and even firewall/bmc from actually using the brakes making all of this worse. I'm not sure why you are opposed to simply cutting a flange you have already modified before and rewelding it to properly clear everything when you are willing to cut open the shock tower and elaborately plate it back in. Good luck
-
This winter I've been rebuilding the interior of my car. One item I could not find any information on at all were the mounting dimensions of the RS Mach Steering wheel. I believe in period this was a competition option, with the thicker wheel material and 380mm diameter often seen on the s30 and Hako Skylines. It seems the RS Mach wheel mounts more like the JDM s30 wheel compared to the deeper dish of the USDM wheel. Potentially I may machine a spacer to move the wheel further out but will see when I get everything back together. I know for the JDM s30 wheels it is popular to modify the turn signal stalk to account for the difference in wheel depth. I am also around 6' tall so also likely dimensionally different than the typical JDM person in period. Hopefully this helps someone. There is plenty of information out there for Checkman, Nardi, JDM s30 types, etc. types but nothing on this item. Edit: someone sent me some information and perhaps the Nissan comp part # was 48400-E4110. Apparently there were a few types of this wheel available, it would be good to know all of the variations but that'll be future research.
-
Poly tank from Vintage Tank Solutions install discussion.
Dat73z replied to Derek's topic in Fuel Delivery
@Derek I'm planning to run 2 vents. The fuel filler vent to the evap tank near the rear shock tower, which then goes to a one way valve and vents back into the rear fenderwell (I'll likely plumb in a charcoal canister for fumes). The second vent is on top of the tank on the fuel pump plate, also feeding back into the evap tank. Are you still having fuel tank backpressure issues? -
Not knocking your work, but what was the rationale behind cutting your shock tower in half which is a major structural component of your car versus reworking the Jpipe which can easily be modified or re-fabricated? It looks like even after severing the shock tower, your Jpipe still puts your turbine hot side into the brake master cylinder which has already been ground down? After looking through your build thread I see you modified the bolt-on jpipe from an old turbo kit. The chassis has already been cut but I would advise you remake or modify the jpipe to fit the turbo properly away from your brake system. You may be able to reuse your modified jpipe by simply changing the angle on either flange.
-
Thanks @calZ. Big fan of your work.
-
Reserving post 2 Also have a bunch more pictures and videos to upload. Not sure why but I keep getting upload errors so perhaps I'll focus on the written aspects first.
-
Reserving post
-
Misc.: Triple carb idle up solution Set a bunch of placeholders going to keep this post as a catch all. Open to any suggestions on what else I should add as I am working on this through the winter.
-
Wiring: Write this up later out of time today.
-
Refrigerant Charge and Service: Write this up later out of time today.
-
Line Branches: Write this up later out of time today.
-
Condenser and Dryer: Writeup in progress For the condenser I went with a half size parallel flow unit, which are popular with modified imports such as evos with space constraints due to large forward facing turbos: 12 X 14 Superflow R-134a Condenser On my s30, I have a large Setrab oil cooler mounted next to the condenser and a large intercooler in front which dictated the size and configuration. Similar to my oil cooler I found that due to space constraints routing softline would be borderline kinking even with looping the hoses around due to how tight things are in the cowl section. Looping the hoses and/or running them across the engine bay would have worked but that configuration did not look good to me. I also wanted to run the dryer off the condenser, retain the factory hood hinges, springs, front grille so basically all of this just made things even tighter. I concluded the cleanest approach for the most compact form factor would be to hardline the condenser No8 and No6 lines to the dryer along with bulkheading the connections at the radiator support. I used the following parts from Vintage Air: 07323-VUC Standard Painted Drier with Trinary Switch and Mounting Hardware x1 Vintage Air 366100 - Vintage Air ProLine TiteFit Fittings x1 Vintage Air 366101 - Vintage Air ProLine TiteFit Fittings x1 Vintage Air 382680-MBA - Vintage Air Streamline x1 Vintage Air 12513-VCD - Vintage Air U-Bend-Em Refrigerant Lines x2 Vintage Air 125741 - Vintage Air Replacement Air Conditioning Hard Lines x1 Note for the No8 lines you can probably get away with one but I ordered 2 as I couldn't find the PN for Female/Female ends. Also as with all hardline work make sure you measure what you actually need and make wire templates before ordering material. I typically always order more length of hardline than I need as it sucks to be short mid-project. For the bulkhead fitting I retained the Vintage Air connectors but fabricated my own bulkhead plate to bolt into the existing s30 radiator support holes. I also swapped the position of the No6 and No8 lines to meet the angular requirements of the hardlines and also the softlines seemed to have better angles on the other side of the bulkhead as well. For the condensor mounting, I opted to soft mount with my usual choice of scrap AL and 1/8" high temp silicone sheet. I basically copied the Setrab factory soft mount arrangement which I had also fabricated for my oil cooler. Adding more detail and pics here shortly... For the hardlines I typically work with stainless so my tools are mostly stainless instrument benders. What this means is for the tools I have on hand and materials, is the minimum bend radii for SS in the wall thicknesses I use is larger than what is achievable for the AL tube I used which isn't ideal for such a tight area. I didn't want to go out and buy a bunch of new hardline tools just for marginally tighter AL bends so to work around this, I had to rely on changing directions with minimal bends to make the angles required to fit the space. Note: If you have the AC line flaring tools disregard below. When working with stainless I typically do AN style flares, although I have done bubble and others as well. The typical workflow for hardlining is to create the bends, then slip on the tube sleeve/nuts, then flare the connections. However, for the AL AC line apparently the flares are done on some large proprietary hydraulic machines. I did find what looked like a similar style of flare from Mastercool (not 100% on this and it was only the female side of some fuel push lock fitting) but the tool was like $500. So I decided to use the pre-flared straight Vintage Air AL lines, bent them to shape, sectioned to length, then tig welded them back together. This is typical practice for AC lines esp for field repairs, and pre-flared tubing end sections are also sold for this. I think you can also braze or solder them but I've never tried that. Tig welding them was interesting as it was like welding around the circumference of a pencil but they welded really clean/easy unlike old oily castings. I also used 1/16 4943 filler which flowed really nicely. Machine settings were 70amps, pedal control, max freq, min cleaning action, 1/16 e3 sharp tip, #6 gas lens, 12cfh argon, 0.5s pre flow, 5s post flow.
-
-
Heater Lines: For the heater lines I evaluated several options including AN, HS-79, and other fitting types. Ultimately I wanted more of an OE spec aesthetic so I purchased the following bulkhead fittings from Vintage Air: O-Ring Bulkhead Heater Fittings For 5/8 Inch Hose - Straight NO 10 Hose Fitting (34215-VUG) 90-Degree O-Ring Heater Fitting for 5/8-Inch Hose (121018) I decided to run the OEM 240z heater hoses cut at the firewall and found that the bulkhead fittings were just slightly too long. So I cut them back to the base of the second hose rib from the top and bead rolled the tube right below the 3rd hose rib from the top to securely grip the hose. When installed on the firewall it really gives an OE aesthetic, especially running the trimmed OEM hoses. More details to follow.
-
Compressor: For the compressor I'm using a Sanden SD 508 Compressor Double V-groove pulley Standard Finish (04808-VUA). Nowadays you can also get an electric compressor and mount it anywhere, but I decided to stay mechanical. There are dozens of Sanden SD 508 compressor configurations you can order, including rear fitting exits, and even custom machined rear caps. I especially liked the version where the charge ports for the high and low side were directly on the back plate but could not use that on my setup. I chose the standard top exit for packaging considerations as the turbo sits behind the compressor and I wanted to have the space directly behind to run a 4-5inch pipe from the turbo inlet turning down to the steering rack/front swaybar area of the splash pan to pick up cooler filtered air from under the engine bay. The compressor itself can be clocked, and the rear plate can be removed and clocked as well if needed so long as the centerline of the oil fill bolt does not exceed the 9:00 or 3:00 positions. I chose to clock around 9:00 to clear my intercooler charge piping and new ignition coil location. The mounting bracket is a ZSM Custom unit (a very quality piece, thanks to Zach) which I modified by milling the slots further to push the compressor back to clear my dual spals and engage the first row of the compressor dual row pulley (mating to Rebello spec BHJ dual row damper on F54 block). I have conveyed this information to ZSM Custom as well for future brackets. There are also several other bracket and fabrication options available but I decided not to go with any of those. I'll get some updated photos up of the final configuration later.
-
Center Vent: Nowadays you can 3d print anything, but I wanted to use what I had on hand. And what I had on hand was scrap AL plate and 2.5" intercooler tubing. I tig welded the two components together and flattened the flange with a sanding block due to minor warpage from welding. Note that I found it's better to weld the plate to the tubing first before cutting the hole due to warpage.
-
Fan Switch: I've mapped out the wiring and what I found was the vintage air switch has 5 terminals: 12v power, Fan L, Fan M, Fan H, and 12v switched only with Fan on to AC thermostat switch then onto the compressor clutch. The OE blower switch for my 73 at least has 6 terminals: Black (probably former ground) which is switched with Fan L, Fan M, Fan H, and a Red (formerly Blower 12v) + Blue wire (I believe unused in OE harness but for AC power) which is switched only with Fan on. So to go from 5 wire vintage air to 6 wire OE, I would split the vintage air 12v relayed switch power between the OE switch Black and Red wires (to power the fan and kick on the compressor clutch only when Fan on). Will update with better wiring drawing later unless someone else wants to help out.
-
Starting a Vintage Air Gen II Mini install thread. Specifically this is going into my HybridZ, a 1973 240z which is a triple carb blowthrough turbocharged L running a FMIC, oil cooler, and retaining the stock hood springs and front valence. Factory dash, radio, and gauge mounting. Nissan Versa EPS. Wizard cooling AL rad with dual Spal fans. The same concepts would apply for any Z install, but packaging considerations may differ. Each post will focus on a specific aspect so hopefully it'll be easier to digest for the DIYer. I'll attempt to edit and add more details over time. Controls: What I found researching is most either discard their OEM controls, or perform a partial retrofit where some OE levers are used, OE lever throws may be incorrect, and it seems everyone modifies their OE housing to accept an aftermarket blower switch. I wanted retain the full look and feel of the OEM HVAC controls including the OE blower switch and levers + lever throws. It's important to note that the Vintage Air unit I selected uses 4 switches. I also included the Vintage Air part #'s used as applicable: 1. Fan (Off, Low, Med, High) - Rotary (OEM Switch Used) 2. AC Thermostat (Off -> Cold) - Linear (11088-VUT) 3. Heater Temp (Off -> Hot) - Linear (11212-SUA) 4. Mode (Defrost, Upper Vents, Lower Vents, Upper/Lower Bi-Level) - Linear (11430-VUS) For functionality and less to remember in the car what I'm going for is when all levers are to the right AC Thermostat is Off, heater is Hot, Vents are Upper/Lower Bi-Level. When all levers are to the left AC Thermostat is On, heater is Off, Vents are Defrost. So basically all left Cold, all right Hot. Note that the wires on the Mode switch can easily be moved around for any custom order of control, but it's important to get the mounting orientation of the AC Thermostat (bimetal thermostat) and Heater (potentiometer) correct to where you want them. I used 1/16" AL and SS tig wire for the linkage rods. For the Mode select I added 2 detent positions for a total of 4 including the factory 2 (chamfer the new holes a bit where the bearing rides for positive engagement and smooth disengagement). For the AC Thermostat I added an overtravel stop on the left/off position as I noticed even the OE lever would overtravel and crack the hvac control panel on almost every panel I've inspected so consider that an improvement over stock 50 years later 😆. For the bracketry I used some Home Depot scrap AL L stock I had left over from my wife's garden. I'll get those dimensions later. In the videos everything is dry with no grease so while things are already smooth with no binding they will get much better on final assembly. My plan is to black zinc coat everything but the issue I am having now is finding someone local in the Bay Area CA who will do zinc black chromate for larger parts. So perhaps I will run it patina as I'd rather not paint and have the sliding/friction areas gum up the grease. Pictures attached detail the arrangement, clearances, and function. 20241109_092059.mp4 Controls.mp4
-
Replying to FAQ's - Dat73z
Dat73z replied to NewZed's topic in Brakes, Wheels, Suspension and Chassis
I am using tig as that is all I currently have available but mig would work as well with small wire. The key with the tig is to focus the arc on the cast yoke, a light dab of filler, wash the bead onto the cap then immediately get out of it and force cool. Another option could be to plate in like below and perhaps there are already washers of the correct 15mm size out there. Welding caps is apparently very common for the 4x4 guys, and they do it on high speed applications like driveshafts/axles. Worst case I already know it's easily serviceable as I had to get the poor quality joint out. I'm really hoping this bearing will last another 50 years like the original 😂 but we will see. -
Replying to FAQ's - Dat73z
Dat73z replied to NewZed's topic in Brakes, Wheels, Suspension and Chassis
Thanks @NewZed. Didn't realize that was a thing. Updated my post per your suggestion. -
Like many other Zs my 50+yr old staked ujoints were making some clicky play and of course there is not much good information out there. After some research online, the staked ujoints can be replaced but restaking them properly requires a special tool which is quite expensive (500$ to a few thousand). Also many shops will not touch these components for liability reasons. So what I did was I carefully ground down the stakes with a dremel tool and pressed out the old ujoints. For the new ujoints I actually had to do the job twice as I initially purchased some ujoints recommended by the classic zcar forums. What I found was the caps were so soft that they ovalled out when pressing in and caused binding in the joint. The country of manufacture were not specified on the boxes, and when I cut the joints out to redo the crosses were also soft. After many years of dealing with poor quality aftermarket parts, I should have known better and the solution I found was to purchase high quality Made in Japan Toyo joints PN ST-1540 (15mmx40mm), and when pressing these in the caps do not distort or cause binding. I believe this is an OEM part and OE supplier. Pressing the new joints in, you need to be careful and press the caps to the appropriate depth to achieve 40mm cap-to-cap, centered in the yokes on either end of the cross. Similar to what is done in the 4x4 communities I decided to tack weld where the old stakes were, 4 per joint and air cool after each tack as to not overheat the parts. I know this is much stronger than the factory arrangement as I was able to press the OEM caps past the OE stakes whereas I could not actually press out my first install attempt (before I realized the poor quality bearing issue) with a 20 ton press without exactly grinding down the spot welds for fear of bending the yoke ears (the poor quality soft caps were all kinds of mushrooming out and distorting unlike the OE hardened caps). Hopefully this helps someone. This has been on my to do list for the better part of a decade and I know from inspecting many columns and steering shafts over the years that there are a lot of worn joints out there. Edit: per suggestion from @NewZed the joints which did not work are as follows: https://www.driveshaftparts.com/index.php?route=product/product&product_id=1100 From this thread at classic Z cars: https://www.classiczcars.com/forums/topic/63434-steer-column-u-joints/?do=findComment&comment=629099 When I was researching the above joint, it seems many of the same appearance above are sold under different name brands are coming out of China, probably from the same or similar factories. Also some tips: I practiced the tacks on a few spare caps I had laying around and they blow through super easy compared to thicker driveshaft ujoint caps. So focus your torch on the cast yoke, one small dab of filler, and lightly wash the filler down onto the cap. Work quick so you put the minimum heat into the parts. I used tig as that is what I currently have available but mig with small wire may work as well. Consolidating comments to FAQ from discussion thread: Another option could be to plate in like below- I did check and 15mm washers are available. Due to the construction of the s30 steering yokes, I'd recommend washers sunk into the holes versus plating above the recessed bearing surface so the bearing is fully captive and cannot move. This will make sense if you are servicing the joints and have the parts in your hands. See picture of washers welded to yoke ears. This way per @NewZed comments the metallurgical properties of the bearing caps are not affected.
-
A minor point on the larger EPS systems as this information wasn't readily out there when I was researching. For the Versa unit, I clearanced the brake pedal then plated it back in for reinforcement to achieve the OE pedal position as a starting point, otherwise the pedal would need to be adjusted downwards to clear the EPS gearbox assembly. This allows a full range of adjustment and is not necessarily a negative as ime getting the stock s30 pedals closer helps me in heel toe but def something to consider in EPS options if you have a preference for pedal position.
-
A musician's therapist (The $300 Z)
Dat73z replied to Zetsaz's topic in S30 Series - 240z, 260z, 280z
Yes the regular kit will fit under RKRs 15x8 +0. Here is a pic from like 10yrs ago when I was still daily driving my Z, you can see the T3 big wilwoods peeking out under the rkrs I took a bunch of pictures and measurements with rkrs and watanabe/several other wheels a couple yrs back when I decided to go ZCG due to the limitations on the t3 kit. I also ran a 1" wilwood MC but would not recommend it today as the unit leaked internally and externally so I went new OEM. Will DM you those later when I get some time to dig them up.