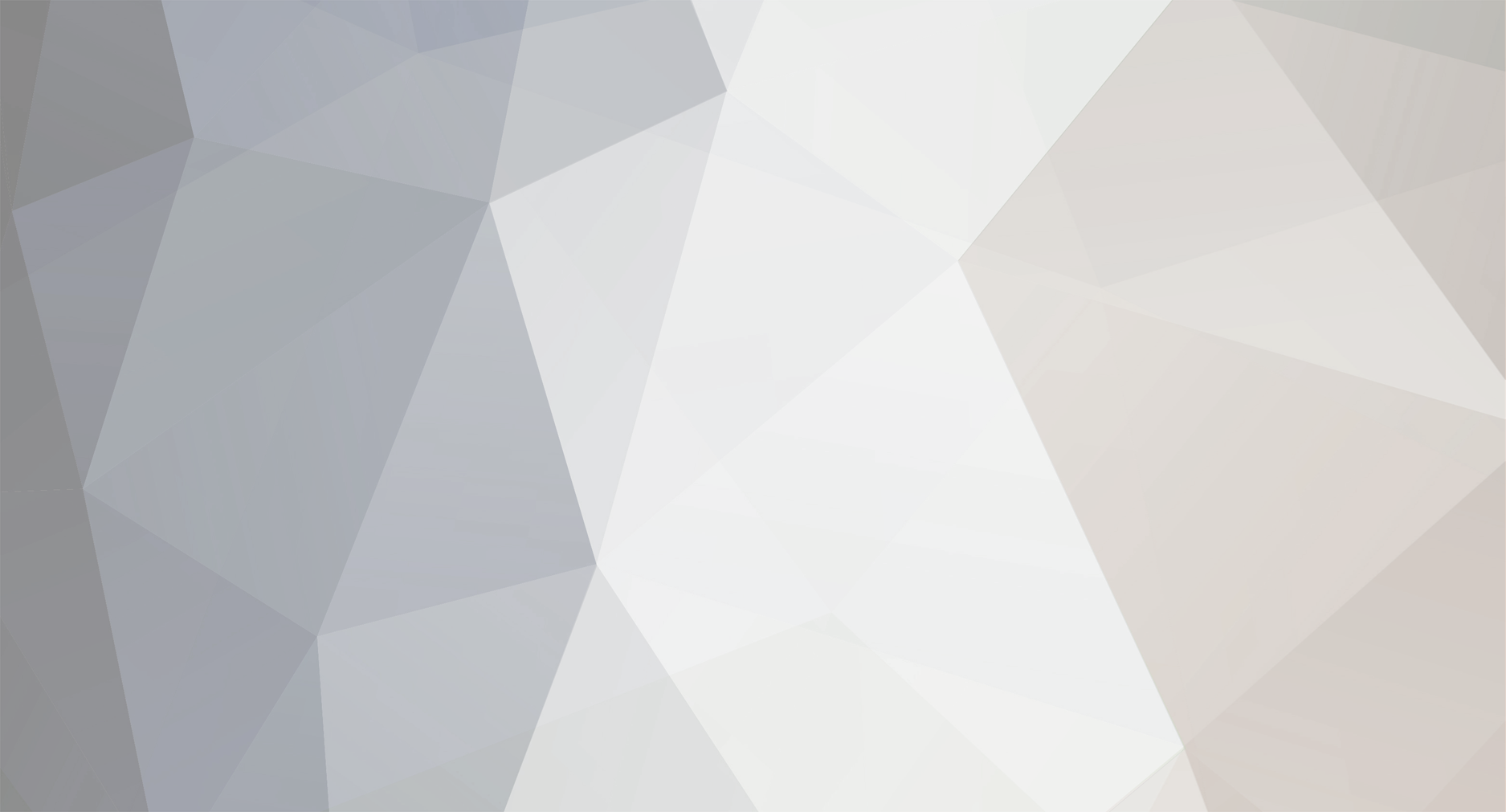
Ironhead
Members-
Posts
529 -
Joined
-
Last visited
-
Days Won
18
Content Type
Profiles
Forums
Blogs
Events
Gallery
Downloads
Store
Everything posted by Ironhead
-
ANOTHER Datsun Z/LS3/T56 Swap Thread
Ironhead replied to Ironhead's topic in S30 Series - 240z, 260z, 280z
After a horrible experience with Carbon Signal: I ordered the 240YZ rear flares from ZTrix, and could not be happier with the fit and quality of them. So that is what I am using in the rear. They fit over the 315 wide tires perfectly (which is to say...just barely...LOL). They were cheaper than Carbon Signal, and came from Arizona instead of Dubai. I am still trying to remember what the hell I was thinking ordering from Carbon Signal... Fronts will be Ztrix parts as well...either IMSA or YZ or some combination. Thanks for the kind words. -
ANOTHER Datsun Z/LS3/T56 Swap Thread
Ironhead replied to Ironhead's topic in S30 Series - 240z, 260z, 280z
I finished the modification to the driver's side rear quarter, for large tires and flares.... I know some variation of this mod has been done to every "Z" car with flares, but I have to say I found it surprisingly difficult. Lots and lots of welding the thin OEM sheet metal in awkward positions. Lots of holes burned through the OEM sheet metal. Lots of repairing these same holes. But I got it done. Now I have to do the passenger side.😆 -
ANOTHER Datsun Z/LS3/T56 Swap Thread
Ironhead replied to Ironhead's topic in S30 Series - 240z, 260z, 280z
I agree Ian, but after perusing the 'net so far I haven't been able to find one that would both fit and be an improvement. Vibrant makes a bell-mouth velocity stack with a 4" flange...what I would need...but the outer edge of the stack is 7" OD and thus far I have not found a filter that large. I could modify the stack down to 6" OD, then weld on 6" tube for the filter...but I haven't really made a final decision yet. Most velocity stack/filter combos I could find are made to be used in downdraft mode on top of a 4-barrel carb...and not only would not work in my application....but they also use a very small filter. Pipercross probably makes a large foam filter that would work, but given a choice I would rather stick with the K&N style filter. As with everything on this build...it is a work in progress. -
ANOTHER Datsun Z/LS3/T56 Swap Thread
Ironhead replied to Ironhead's topic in S30 Series - 240z, 260z, 280z
I see what you mean. Only a very, very small area filter would fit there...but I have no doubt it would indeed flow a bit better. -
ANOTHER Datsun Z/LS3/T56 Swap Thread
Ironhead replied to Ironhead's topic in S30 Series - 240z, 260z, 280z
I have no doubt there are better ways I could have done it....but I am not visualizing exactly what you mean....? -
ANOTHER Datsun Z/LS3/T56 Swap Thread
Ironhead replied to Ironhead's topic in S30 Series - 240z, 260z, 280z
I've started cutting up the rear quarter fenders to make room for the large tires and fender flares. I have to say, cutting up rust free 45 year old OEM bodywork gives me a bit of pause....but that is my path....😯 -
ANOTHER Datsun Z/LS3/T56 Swap Thread
Ironhead replied to Ironhead's topic in S30 Series - 240z, 260z, 280z
https://www.ictbillet.com/ls-truck-alternator-bracket-low-mount-lsx-ls3-lq4-lq9-l33-billet.html IIRC the tensioner is the OEM one from the Pontiac GTO. -
ANOTHER Datsun Z/LS3/T56 Swap Thread
Ironhead replied to Ironhead's topic in S30 Series - 240z, 260z, 280z
With air filter.... -
ANOTHER Datsun Z/LS3/T56 Swap Thread
Ironhead replied to Ironhead's topic in S30 Series - 240z, 260z, 280z
I got the cold air intake done....at least to where it passes through the radiator support. It is done pretty much the same way every LS swapped Z, ever, has been done....but here it is regardless. I just have to decide on an air filter. I will probably just weld a piece of 90 degree aluminum tube to the outer flange, then use a cone filter on it. The same sort of cone filter that adds at least 50 RWHP to any car they are installed on. -
ANOTHER Datsun Z/LS3/T56 Swap Thread
Ironhead replied to Ironhead's topic in S30 Series - 240z, 260z, 280z
Thanks gents! -
ANOTHER Datsun Z/LS3/T56 Swap Thread
Ironhead replied to Ironhead's topic in S30 Series - 240z, 260z, 280z
I got both headers finished. I am reasonably satisfied with the outcome, but I have to say this was a time consuming chore. Enough of a chore, that if I was doing it over again I would plan the build in such a way that off-the shelf headers...like the Hawks...would be compatible. In my case I could tell that my motor mounts and the Apex cross member braces would have prevented the Hawk headers from working. In addition to not hitting or burning anything, I wanted to be able to install/remove the headers with the motor in the car. This was very difficult on the passenger side. As it turned out, I can do it, but I have to remove the Apex brace and the starter in order to do so. I can live with that. As I said before...hell with "equal length"....at the end of the day I was trying to find someplace they would fit...period. The two headers look quite a bit different because the interference issues were different on each side. On the driver's side the primary obstacle was the steering shaft and oil lines. On the passenger side it was the starter, oil lines, and the crossmember brace. Anyway, I am glad it's done. Thanks for looking. -
I could...I'm not saying there is no way these parts could be repaired and/or made usable. I'm just trying to give other potential buyers a heads up....these parts are expensive, fragile, poorly made IMHO, likely to arrive damaged, and unless you live in UAE you will have absolutely no recourse if you order them and wind up agreeing with my assessment. That's all. I'm still trying to remember exactly why I thought ordering these things was a good idea.
-
I thought about that. But honestly, I wouldn't feel right unloading them on someone else. Particularly damaged. I know builds have been completed using this stuff, but I don't understand how. These parts are junk IMHO.
-
I am posting this as a review of the parts I ordered from Carbon Signal, as well as my general experience with the company. I certainly don’t want to write an overly lengthy account, but I want to include enough detail to fairly document my experience, so here goes. In a nutshell, for those who don’t want to read the saga: My advice if you are considering ordering parts from Carbon Signal is Don’t do it! As I was shopping around for a wide body kit for my project Z, I noticed there weren’t a lot of objective reviews or even accounts of anecdotal experience with most of the parts offered on the market. Well, I don’t even recall my reasoning at the time, but in late October of 2018 I wound up ordering the “Moonbeam” kit from Carbon Signal, in “fiberglass reinforced plastic”. I had seen a few photos of builds using these parts, I generally liked the styling, and I couldn’t find any write-ups about negative experiences with the company. So I took a shot in the dark and ordered with some hesitancy, particularly since the parts had to come from Dubai, UAE. The basic kit was “on sale” for $2500, and the total with shipping and Paypal fees came to a bit over $3500. For me, and I assume most people, this was a major expenditure. Carbon Signal required full payment up front, and quoted a six to 10 week lead time for the parts to be made. The parts wound up shipping in mid-late February of 2019, roughly 16 weeks after I ordered and paid in full. The parts were shipped internationally via EMS, and were delivered to my door via USPS. The first “package” that arrived consisted of the bumper/air dam, splitter, and running boards. I use “package” in quotes, because the items weren’t really boxed. They were taped between two large pieces of cardboard, and wrapped in clear plastic and additional tape. There was absolutely no crush protection or padding of any kind. Every part in this first package sustained shipping damage, some minor to moderate, but the splitter received major damage. The fender flares arrived a few days later. These were properly boxed and arrived intact. Thus began a pointless battle with Carbon Signal, Mr. Ali the contact, about the shipping damage. He told me to make a claim for the damage with the shipping company. USPS delivered the items to my door, they were shipped to the USA by EMS. USPS will not even accept a damage claim on an international shipment unless it is initiated by the sender. This was moot anyway, as I knew damn well that no shipping company, certainly not a cut-rate international shipping company like EMS, was going to pay a dime to reimburse shipping damage on such a poorly packaged shipment. It just wasn’t going to happen. In my opinion, Mr. Ali had to know these realities, and was simply acting in bad faith and refusing to accept any responsibility for the damage. We talked in circles for a few emails, after which Mr. Ali stopped responding to my emails and ignored me. By now I had examined all the parts, and I was not the least bit happy with fit and build quality. The splitter, a part always subject to some abuse, was made of extremely thin hollow fiberglass, roughly 1/16” thick. I honestly believe I could crack that splitter with a firmly thrown tennis ball. The fender flares would have required major work to fit my car, and they too were so thin and brittle that I cracked two of them just “mocking them up” over my wheel arches. I knew if I used the parts and fitted them to my car, the build would be “wedded” to them, IMHO they were of poor quality, and I would basically be dependent on Mr. Ali for any replacements. By now I had concluded that Mr. Ali was a bad faith/dishonorable seller. The situation was not viable, and I quickly knew I would not be using the parts. IMHO they would only be viable (after much work) for a “show car”…not a driver. That was not the goal of my project. While it is not really relevant to the review, a Paypal dispute followed and Paypal seized the funds during the dispute. Mr. Ali resumed contact through Paypal, and said the only two possible solutions were: A) He would replace the splitter only after he was reimbursed for his costs by the shipping company. Or, B} I could return the parts for a refund. I knew A) was not going to happen, so I began properly packaging the items to return them to Dubai. This is where the cold realities of international shipping set in. The basic reason the large parts were so poorly packaged, was to keep the package small enough to be accepted by EMS in UAE. But EMS has different size restrictions from Dubai to the USA than they do from the USA to Dubai. Even with the shoddiest most minimalist packaging, it was impossible for me to pack the items in a small enough package to be accepted by EMS USA. The other options, Fed Ex, UPS, DHL, all would have charged me thousands of dollars to return the items to Dubai. Far more than my refund would have been. While the shipping dilemma is not the fault of Carbon Signal or Mr. Ali, I am quite certain Mr. Ali knew returning the items was not financially feasible, and the “refund” offer was a disingenuous gesture. But even if Mr. Ali was an honorable vendor, IMHO the realities of international shipping make buying/shipping parts of this size internationally financially non-viable. Important lesson here. To be fair, during the Paypal dispute period Mr. Ali apparently got a bit nervous about losing his money, and offered to ship me a new splitter if I would cancel the Paypal claim. Once Paypal claims are canceled, they cannot be reopened. I knew full well if I canceled the claim I would never hear from him again, so I ignored him. By this point, there was no way I was going to use the Carbon Signal parts regardless. A new splitter would be of no use to me. While not relevant to the Carbon Signal review, Paypal required me to submit a bunch of documentation, including a written independent review of the damage/quality of the parts, which I did. Paypal said they found in my favor regarding the dispute, and said they would refund my money in full as soon as I returned the parts at my expense. As documented above, there was no way I could do that. I tried to explain the shipping dilemma to Paypal, but with language barriers and canned/non-applicable responses from them, that was like talking to the wall. Ultimately Paypal denied the claim without refunding me a dime. I don’t blame Paypal too much for denying the dispute. I mean, it would be difficult to refund my money while I had the parts in my possession, even in damaged condition. But in terms of customer service and communication, Paypal proved to be one of the worst companies I have ever dealt with. It was maddening. Bottom line, I spent $3500 on parts that most likely are going to wind up in a landfill. This was a painful and expensive lesson. Carbon Signal Review: Parts design/quality: C-/D+ Business Practices: F Side Review: Ordering large, bulky, expensive parts from around the world: Don’t do it! I was just looking on the Carbon Signal website today, and noticed they no longer list/sell the kit I ordered. Maybe mine was the last one they sold. Not sure what that means…. Hope this review proves of use to someone. I wish I could have found something like this before I ordered these parts. All around, it was a big mistake.
-
ANOTHER Datsun Z/LS3/T56 Swap Thread
Ironhead replied to Ironhead's topic in S30 Series - 240z, 260z, 280z
Sorry, I couldn't dig up the specific part number. It is one of the Woodward "heavy duty" manual racks from this page: http://www.woodwardsteering.com/PDF/5. Heavy Duty Manual Steering Racks, types JL, JLR.pdf You just order LHD "Front Steer" rack (assuming your car has LH steering), then tell them the length you want, the ratio, and the threading for the tie rods....the part number is built from that. You can call and talk to them, they are very helpful. You might not want exactly the same part number as mine anyway, depending on what steering ratio you want and other factors. My outer tie rods were made from scratch by Woodward. They do this all the time and it is very inexpensive. You just need to know the thread of your inner tie rods (which come as part of the Woodward rack), and the thread of the Heim joints that thread into the other side. Keep in mind one end will be a LH thread and the other a RH thread, so that you can adjust your toe by turning the outer tie rod. -
ANOTHER Datsun Z/LS3/T56 Swap Thread
Ironhead replied to Ironhead's topic in S30 Series - 240z, 260z, 280z
I ordered the AE crossmember unpainted, then just cut off the bases for the stock rack mounts, and welded on a mount to fit the Woodward rack. There are a few pictures of this on page 4 of this thread. The Woodward rack is very easy to make a mount for, basically all you need is a piece of .25" steel plate. I added braces below to stiffen things up, but this was probably overkill. I ordered the Woodward rack in a significantly quicker ratio than the stock Datsun rack, but I also just wanted another option than my stock rack. It was very tired and loose, most of the parts needed to rebuild it are NLA, and I just wanted an aftermarket option rather than trying to deal with 45 year old parts. This has been the case with most of the build....not too much OEM Datsun stuff is left. -
Sirpents 260Z / C32 AMG Powered RS30 - Australia
Ironhead replied to Sirpent's topic in S30 Series - 240z, 260z, 280z
Fantastic project and work. Every aspect of your metalwork is so impressive. Honestly, it almost looks like you could have just built a new Z from scratch! -
ANOTHER Datsun Z/LS3/T56 Swap Thread
Ironhead replied to Ironhead's topic in S30 Series - 240z, 260z, 280z
I managed to finish the driver's side header. Seems to clear everything well, and I think there is enough clearance around the spark plug wires so I won't need to worry about them melting. It also clears the underside of the car by at least 1" everywhere. I don't plan to wrap it as things stand now, unless heat problems develop somewhere I failed to anticipate. I am going to make some sort of support from the unused tranny brackets that are circled...just to provide support for the ends of the headers and hopefully prevent any cracking down the road. The collector exit diameter is 3", and after a lot of pondering and vacillating and reading contradictory opinions, my current plan is to finish things off with a dual 3" exhaust system. To provide decent ground clearance I will probably have to use oval tubing in the portion where it goes below the rear suspension. Of course, I still have to do the passenger side header, which looks like it will be a bit more tricky as there is less room. Thanks for looking. -
ANOTHER Datsun Z/LS3/T56 Swap Thread
Ironhead replied to Ironhead's topic in S30 Series - 240z, 260z, 280z
Thanks Granny! Just ordered a tin of that flux! Did some work on the collector today. The "spike" is a weld-on part that is supposed to give you about the same benefits of using a true merge collector, but without having to buy one. SPD wanted around $300 each for 4 into 1 merge collectors, just because there is a lot of fab time that goes into making them. I suppose making my own might have been an option, but they are sort of complex and I figured it was beyond my limited skill level. So the budget approach is just to weld in this spike and use a standard formed collector. It was a relief to find that everything still fit in the car as intended after it was all assembled and tacked together. Some of the clearances are so small I was afraid the final welds on the primaries might have caused sufficient distortion to pull things out of whack...but so far so good. -
ANOTHER Datsun Z/LS3/T56 Swap Thread
Ironhead replied to Ironhead's topic in S30 Series - 240z, 260z, 280z
Haven't had much time recently to work on the car, but I did manage to finish the primary tubes for the driver's side header. Again, the goal was less perfect balance/flow than it was to make the headers fit well and not burn anything. I also wanted fairly easy install, in that I wanted to avoid having tubes on both sides of the steering shaft, that sort of thing. The numerous small bends were incorporated in pursuit of that goal...to maintain good clearance from steering shaft, oil lines, clutch hoses, etc. So far this has been easier to do than I expected, just very time consuming. Also argon consuming....with so many welds, and the necessity to back-purge all of them, the argon goes very quickly. Thanks for looking. -
ANOTHER Datsun Z/LS3/T56 Swap Thread
Ironhead replied to Ironhead's topic in S30 Series - 240z, 260z, 280z
Thanks Joe. Honestly, I have the driver's side header completely tacked up now, and have refined using the grinder technique to the point I will probably just finish out with it. I tell you though, I have found that the disc sander with a 36 grit "hard metals" abrasive has been essential to face each cut so I get good fit up. The grinder would not work at all without the sander. -
ANOTHER Datsun Z/LS3/T56 Swap Thread
Ironhead replied to Ironhead's topic in S30 Series - 240z, 260z, 280z
That looks like a great idea. How do you handle different bend radiuses...radiai....however you say it? -
ANOTHER Datsun Z/LS3/T56 Swap Thread
Ironhead replied to Ironhead's topic in S30 Series - 240z, 260z, 280z
I started on the driver's side header. So far no major difficulties, just very tedious and time consuming work. I had planned to pursue the goal of "equal length" headers, but have already lowered my sights to "as equal as possible". There is just too little room to mess around much with tubing placement, which is necessary to make them all the same length. I have found it is a sufficient challenge for me just to find a place for the tubes where they won't hit or burn any other parts. Among my goals were to avoid the common problem of burned plug wires, and to make the headers removable without having to lift the engine. This made "equal length" virtually impossible. The lack of space also forces each tube to have a lot of bends in different planes, which means a lot of cuts, positioning, and welding. The owner at SPD exhaust (close to me so I buy components there) said the need for equal length tubes is greatly exaggerated anyway. Just the sort of canned excuse I needed to hear! Things would be much easier if I had a band saw, but I do not. I have a chop saw, but cutting up the bent tubes at angle makes it impossible to use. So I have resorted to using a grinder/cut off wheel then dressing the ends on a disc sander. This works, but it is pretty time consuming. All I have completed are the two rear tubes, and there is a lot of time invested just to do them. I'm committed now though....so I will get through it. -
ANOTHER Datsun Z/LS3/T56 Swap Thread
Ironhead replied to Ironhead's topic in S30 Series - 240z, 260z, 280z
Last week or so have felt like I am spinning my wheels. I am trying to finish plumbing the engine, and doing a lot of "what will fit where" experimenting. I got the oil cooler installed and plumbed, and installed the coolant overflow tank in front of the radiator, just because things are getting really tight in the engine compartment and I could not find a location for it. The "heater hoses" are installed but are really just providing heat for a defroster/demister. I had to re-route the radiator hoses, as I realized the prior routing would not have allowed room for 4" intake tubing, which seems to be the recommended size for the LS3. About the only "plumbing" item left is the breather can and breather hoses...unless I find other items which interfere with each other....which I am sure I will. Then I have to tackle building headers....which I am more than a little apprehensive about successfully pulling off. Thanks for looking. -
ANOTHER Datsun Z/LS3/T56 Swap Thread
Ironhead replied to Ironhead's topic in S30 Series - 240z, 260z, 280z
I am for sure going to run them off a thermostat, to go on at around 190 degrees. But, I probably will install a manual switch as well...not 100% sure yet. I am not going to stagger them at all....either both will go on or neither.