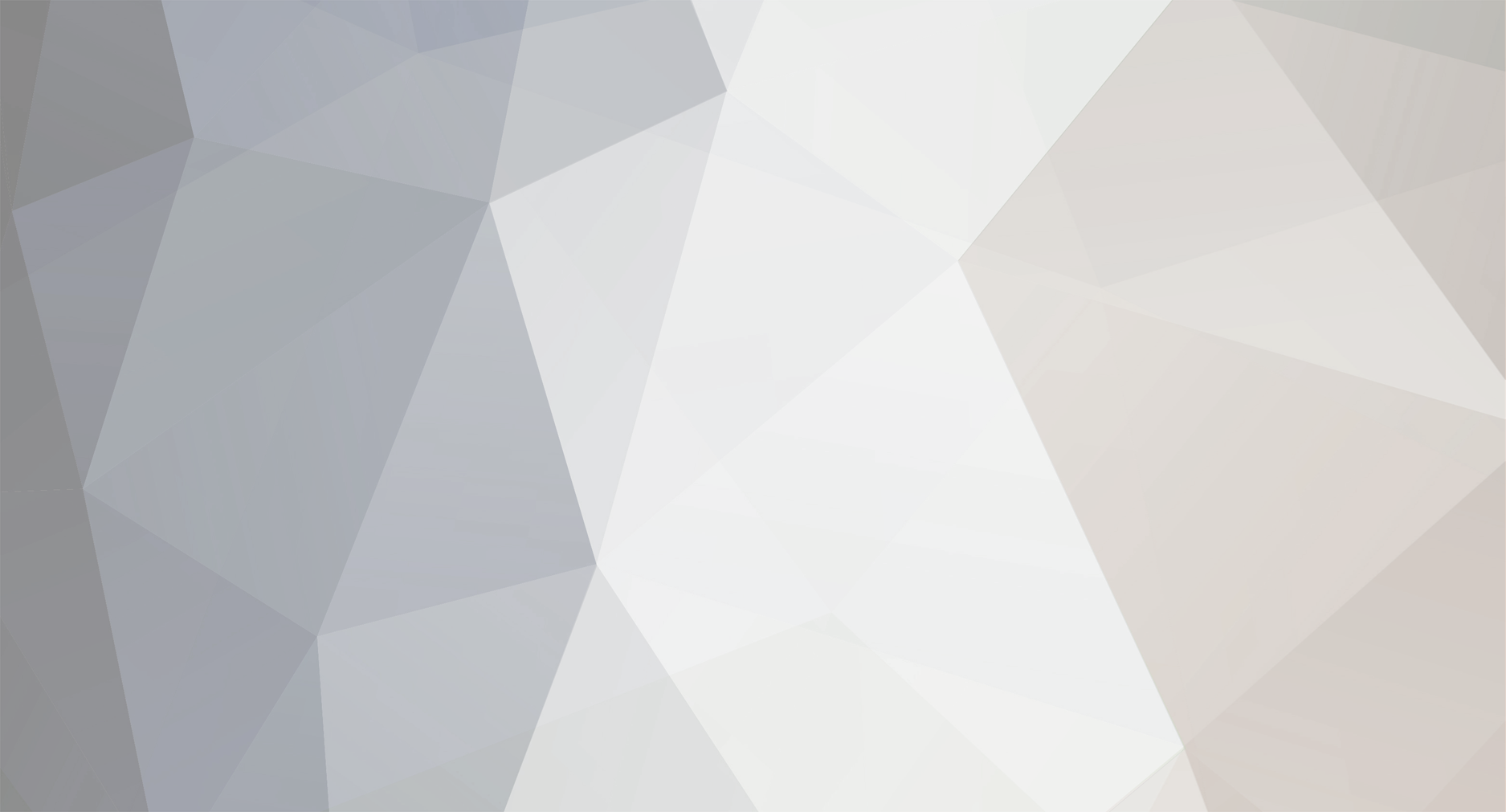
Ironhead
Members-
Posts
529 -
Joined
-
Last visited
-
Days Won
18
Content Type
Profiles
Forums
Blogs
Events
Gallery
Downloads
Store
Everything posted by Ironhead
-
New source for CF and FG body parts...to include the Pantera Hatch!!
Ironhead replied to jhm's topic in Body Kits & Paint
Hey, you never know. They might be fantastic. I think someone should give them a try. Just not me. LOL -
Ford Super 8.8 irs swap thread. Rear brakes too
Ironhead replied to Invincibleextremes's topic in Drivetrain
Great stuff... I am getting the nagging feeling I should have gone Ford 8.8 instead of using the R200 shortnose I have in my build. Too much invested now to switch, unless it breaks once the car is running.- 280 replies
-
- disc brakes
- suspension
-
(and 7 more)
Tagged with:
-
ANOTHER Datsun Z/LS3/T56 Swap Thread
Ironhead replied to Ironhead's topic in S30 Series - 240z, 260z, 280z
I haven't been updating much, just because I have been working on wiring and it seems difficult to take meaningful photographs of that process. Having said that, I did manage to get the engine harness finished: -
Sirpents 260Z / C32 AMG Powered RS30 - Australia
Ironhead replied to Sirpent's topic in S30 Series - 240z, 260z, 280z
Everything looking fantastic! -
ANOTHER Datsun Z/LS3/T56 Swap Thread
Ironhead replied to Ironhead's topic in S30 Series - 240z, 260z, 280z
Very nice of you Britt, but you are giving me WAY too much credit. I appreciate it nonetheless. -
Good work! I can't seem to get anything done in three months...
-
ANOTHER Datsun Z/LS3/T56 Swap Thread
Ironhead replied to Ironhead's topic in S30 Series - 240z, 260z, 280z
I was surprised as well. You have a little bit of flexibility, because a lot of the wires....like the power to the injectors...and the power/ground to the coils....start with just one wire and splice into eight. If you have too few or too many pins in the connector (they only come in limited sizes) you can chose to have the splice either before or after the firewall. Believe it or not, I had to keep all the splices after the connector or 61 pin would have been much too small. There are a lot of wires. The coils use 32 by themselves....you need seven (six plus a shield drain) for the electric throttle control....16 for the injectors....it adds up quickly. -
ANOTHER Datsun Z/LS3/T56 Swap Thread
Ironhead replied to Ironhead's topic in S30 Series - 240z, 260z, 280z
Trying to force some order out of the mess: The engine wiring harness will go through the firewall via a 61 pin bulkhead connector. This actually turned out to be the perfect size for the LS3, handles all the wiring for the engine, additional gauge sensors, etc without single pin left over. The front lighting and wiring for the radiator fans will go through a second much smaller connector. The O2 sensors and transmission wiring will go through a small connector in the trans tunnel. Just seemed more direct. I can say wiring one of these large shell connectors is not something you want to do if you are distracted....it really takes some concentration not to screw it up. Thanks for looking. -
ANOTHER Datsun Z/LS3/T56 Swap Thread
Ironhead replied to Ironhead's topic in S30 Series - 240z, 260z, 280z
Entering the "WTF have I gotten myself into?!" phase of the project..... -
ANOTHER Datsun Z/LS3/T56 Swap Thread
Ironhead replied to Ironhead's topic in S30 Series - 240z, 260z, 280z
Thanks Ian... Thus far I would say there is really no downside to the PDM, except that you have to pay for one. I haven't had the opportunity yet to fully explore the things it can do, just because the whole damn car pretty much has to be wired in order to do so. But, it is definitely very compact and very clean/simple to wire. I really wanted to get by with the PDM15, but even on a fairly simple car like mine it would be impossible to make it work. Both the PDM15 and PDM30 have the same number of 20 amp outputs(eight), but the PDM15 only has seven 8-amp outputs, whereas the PDM30 has 22. I was just wiring the rear part of the car today, and between turn signals, running lights, brake lights, backup lights, diff cooler pump, and diff cooler fans, that is seven 8-amp outputs right there...and I haven't even started on engine/interior/headlights/cooling fans, etc. The radiator fans require two 20-amp outputs all by themselves, the fuel pump a 20 amp, and I am not sure yet on the headlights...but you see my point. You run out very quickly and I wanted to have some expansion room left in the system. I think the PDM15 would really only work on a formula car or something in that mold with a very simple electrical system, or just in a partial usage like you describe. You can combine them...like use three 8-amp outputs to make a 24 amp, but you cannot combine the differing types...like use an 8 and 20 to make a 28. Motec said that would fry the 8 amp channel. I agree with your assessment though. Once the car is wired, and everything working, no way in hell would I go back and redo it. Besides, if you mixed the PDM with a variety of traditional relays and fuses, to some extent I think it would defeat the purpose. -
ANOTHER Datsun Z/LS3/T56 Swap Thread
Ironhead replied to Ironhead's topic in S30 Series - 240z, 260z, 280z
Thanks Skiguy, very kind of you! -
I too am interested in how this pans out when people have had some experience with it. Just looking at the design, I'm not sure I see how replacing the "mustache" bar with a tubular design will greatly increase the resistance of the setup to twisting of the diff...which is the intent....particularly when compared to the TTT rear end design that uses a billet aluminum mustache bar. It seems to me just like a different way of doing the same thing...no better nor worse. This design looks like it has a MUCH more rigid front diff mount that the TTT design however....which is a real problem with the TTT kit. I am currently running a modifying Apex front crossmember, and I am happy with it....so I am eager to hear of other's experience with this kit.
-
ANOTHER Datsun Z/LS3/T56 Swap Thread
Ironhead replied to Ironhead's topic in S30 Series - 240z, 260z, 280z
Thanks! Wire, heat shrink, and Deutsch/"Mil-Spec" connectors from: https://www.prowireusa.com/ and from: https://www.milspecwiring.com/ LS3 specific ECU connectors from: https://www.mouser.com/ Other LS3 connectors from: https://www.eficonnection.com/ -
ANOTHER Datsun Z/LS3/T56 Swap Thread
Ironhead replied to Ironhead's topic in S30 Series - 240z, 260z, 280z
The last couple of weeks I have just been working on getting electrical components installed and building wiring harnesses. As with most things, it is proving more time consuming than I anticipated. This board with the ECU and PDM will go on the passenger side inner firewall. The relay and circuit breaker will supply power to the electric power steering. The PDM is designed to replace typical relays, fuses, and circuit breakers, but the electric power steering has such high power demand that I thought it made more sense to wiring it separately. The relay has 80 amp capacity, and the circuit breaker is 60 amp. I wasn't sure exactly how much juice the power steering required, but I found that most OEM applications using it are protected by a 60 amp fuse, so I think (hope) this will be adequate. The electric power steering +12V connections are 10 gauge wire. The battery cable incorporates a 200 amp circuit breaker, as a last ditch line of defense in case of some catastrophic short circuit. From my reading, using any lower amp rating than that is likely to trip when starting the car. I got most of the dash controls installed. The 15 button panel talks to the PDM via CAN bus, and only requires 4 wires to do so, rather than the usual plethora of wires required on a dash. Pretty much all of the controls will be via these buttons, including ignition on, starter....everything. It greatly simplifies wiring and provides much greater flexibility, since all the functions can be programmed with a laptop. The dash display will also be on the CAN, as well as the ECU, so the dash can display any engine parameters that the ECU receives without requiring additional wiring. This includes engine speed, vehicle speed, water temp, oil pressure, AFR, etc. I am going to add fuel pressure, engine oil temp, diff oil temp, and fuel level, so these circuits will require their own wiring input into the dash. The other controls are power steering assist level, brake bias, coolant flow for the defroster, and battery shut off. I might install a fuel level gauge independent of the digital dash, not sure yet. -
ANOTHER Datsun Z/LS3/T56 Swap Thread
Ironhead replied to Ironhead's topic in S30 Series - 240z, 260z, 280z
Starting the wiring on this thing... Sourcing the various connectors I am going to need has been a challenge in itself. -
ANOTHER Datsun Z/LS3/T56 Swap Thread
Ironhead replied to Ironhead's topic in S30 Series - 240z, 260z, 280z
Well, my car is going to be a stripped down track car....it won't have a center console...so that won't be a problem in my case. As far as the Tremec T56 F....all I can say is "damn". Had I known about that, I would definitely have used one of them. But now, I have already relocated the shifter hole in the tranny tunnel, and of course I am not going to swap transmissions anyway, so I am locked in. For my purposes it really isn't a big deal. -
ANOTHER Datsun Z/LS3/T56 Swap Thread
Ironhead replied to Ironhead's topic in S30 Series - 240z, 260z, 280z
Thanks guys. -
ANOTHER Datsun Z/LS3/T56 Swap Thread
Ironhead replied to Ironhead's topic in S30 Series - 240z, 260z, 280z
I managed to finish the exhaust. I was able to fit two small Vibrant resonators...in the hopes of the car not being too horribly loud whenever I get it running. There are a few things in the result I am not thrilled about and wish I had done differently, but mainly I am tired of purging and welding stainless tube, so I am living with it. -
ANOTHER Datsun Z/LS3/T56 Swap Thread
Ironhead replied to Ironhead's topic in S30 Series - 240z, 260z, 280z
Finished the rear muffler assembly. Looking at it now, it seems a bit over-engineered, but it was the best way I could come up with to have some silencing volume, and use the space I had available. Basically I just have to connect the two oval pipes to the "X" pipe, and I am going to try to install a couple of resonators somewhere in the middle. Thanks for looking. -
ANOTHER Datsun Z/LS3/T56 Swap Thread
Ironhead replied to Ironhead's topic in S30 Series - 240z, 260z, 280z
Still working on finishing the exhaust system. I got the X-pipe finished to bolt up to the headers. The hangers bolt to brackets I added to the Hoke transmission cross member, to support the front of the system and prevent putting too much stress on the headers. There is no escaping the fact that ground clearance will be in short supply. The lowest point on the exhaust system hangs about 1.5" lower than the frame rails, so it will be prone to damage. When I built the headers I could not conjure any way to tuck the header collectors up any higher, so it is what it is. The car is not going to be any sort of daily driver, so basically I am just going to have to avoid speed bumps, crowned curbs, etc. I probably also will have to resist the temptation to grossly lower the ride height. -
ANOTHER Datsun Z/LS3/T56 Swap Thread
Ironhead replied to Ironhead's topic in S30 Series - 240z, 260z, 280z
Yeah....I figured somewhere I would be able to find off-the-shelf parts that would work, but I couldn't. They were made from two pieces of thin stainless welded together then the weld joint ground smooth. -
ANOTHER Datsun Z/LS3/T56 Swap Thread
Ironhead replied to Ironhead's topic in S30 Series - 240z, 260z, 280z
Thanks. I want to use resonators...if I can find some really compact ones and make the "X" pipe section short enough that they will still fit. Time will tell. I am looking at these: https://www.summitracing.com/parts/vpe-1794 The problem is that the trans tunnel isn't wide enough to use them side by side....but if I stagger them, with the "X" pipe...I run out of room lengthwise. -
ANOTHER Datsun Z/LS3/T56 Swap Thread
Ironhead replied to Ironhead's topic in S30 Series - 240z, 260z, 280z
I've been working on the muffler arrangement for the past few days.... I wanted to use "straight through" (Magnaflow style) mufflers, but from past experience have learned that unless you can throw quite a bit of volume at the system, these mufflers usually result in an obnoxiously loud car. I mean, I don't mind if it is a bit loud....but I knew that was inevitable...so I figured the quieter I can make it, the better. That was the challenge here, finding space for reasonably large mufflers, and this is what I came up with. These are a pair of #12259 Magnaflow 3" in/out mufflers. They look small in the pictures but they are pretty respectably sized units. The entire system is going to be dual 3", but I am going to use some oval 3" tube under the rear suspension to keep some reasonable amount of ground clearance. For reasons of style/pageantry...I wanted the tailpipes to exit together in the center of the rear of the car, but this proved impractical/impossible. It would have required quite a bit of additional tube routing, and with multiple 3" tubes you run out of space really fast. The biggest problem is that all the tubes would have completely covered the jacking hardpoints I included on the bottom of the fuel cell mount. My original plan was also to orient the mufflers front to back...but with the tubing factored in there just wasn't enough room for them that way...so I wound up mounting them sideways. Obviously the mufflers are directly below the fuel cell. I am going to put a layer of that hi-tech stainless steel heat shield material between the mufflers and the fuel cell mount, in addition to which there will be two layers of sheet metal between the mufflers and the fuel, and multiple air gaps....so I really don't think this arrangement will warm the fuel very much. Besides, there was absolutely no other place the mufflers would fit....so....off I went. Thanks for looking.