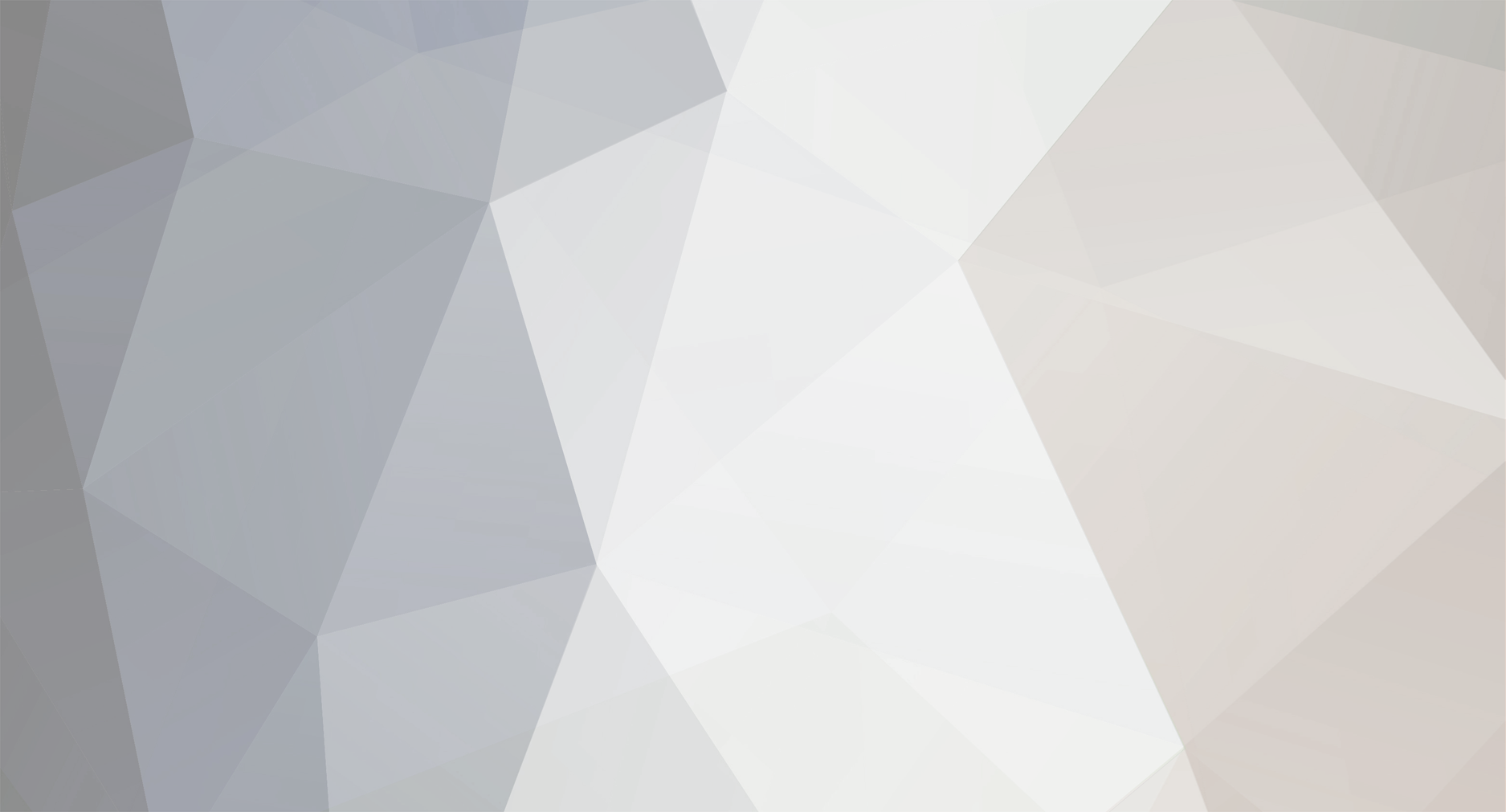
Ironhead
Members-
Posts
529 -
Joined
-
Last visited
-
Days Won
18
Content Type
Profiles
Forums
Blogs
Events
Gallery
Downloads
Store
Everything posted by Ironhead
-
That is freakin awesome. Very clean and well done. When I see a car like that, with the Nissan six and triple carbs, I always wonder if I did the right thing going small block with mine.
-
ANOTHER Datsun Z/LS3/T56 Swap Thread
Ironhead replied to Ironhead's topic in S30 Series - 240z, 260z, 280z
Finished fabricating the mount for my Woodward steering rack. The new rack is significantly quicker than stock, with a 2.36 ratio, and also simply serves as a replacement as my stock rack was pretty tired and loose. I was unable to find most of the parts to rebuild it, so I figured this was another area where going aftermarket was a good long term strategy. The crossmember is the one from Apex Engineered, and all I did was cut off the stock rack mounts it comes with and make my own for the Woodward rack. The crossmember has some useful features, like multiple control arm pivot point locations and bracing attachments to the rear control arm mounts. It was also much easier to modify for the Woodward rack than the stock crossmember would have been. As shown, the rack is mounted in the stock location relative to the crossmember mounting surface, but it can easily be moved up or down as need be down the road, simply by removing the two bolts and changing the spacers. I am banking a lot that the electric power steering will work as I hope, because with this quicker rack and the 275 tires I plan to use in front....I doubt I would even be able to turn the wheel at parking lot speeds. -
ANOTHER Datsun Z/LS3/T56 Swap Thread
Ironhead replied to Ironhead's topic in S30 Series - 240z, 260z, 280z
No...SCCA rules allow fuel lines to go through the cabin as long as they are braided steel or metal hard lines, but the idea doesn't really sit well with me. I have an aluminum cover made that goes over the fuel cell, again as required by the rules. I am going to simply run the fuel lines out the cover and under the floor with bulkhead fittings....so perhaps 6" of fuel line is all that will be inside the car. Then I am going to run the fuel lines in the trans tunnel, pretty much like stock. Plumbing is made pretty simple by this particular cell, as the fuel pump is inside of it, so I don't need to conjure a place to mount the pump and such. -
Heavy Duty frame rails and connectors
Ironhead replied to toolman's topic in Gen III & IV Chevy V8Z Tech Board
Looking great... The only downside I have found to the blasting, is that the blasting media gets into EVERYTHING. I would wager that inside the assorted enclosed areas of the, frame rails and such, you have a lot of it. I haven't come up with a slam dunk way to get it all out, but compressed air and a shop vac are your best (only) hope. My car was blasted almost a year ago and I am still finding blasting media in various places. I guess it doesn't really hurt anything, but it definitely bugs me. -
ANOTHER Datsun Z/LS3/T56 Swap Thread
Ironhead replied to Ironhead's topic in S30 Series - 240z, 260z, 280z
Finished the fabrication to mount the fuel cell: My original plan was to weld the actual cell "cage" into the framework, but while test fitting it I realized that it was very bulky and blocked access to many areas under the car. In particular, seam sealing and painting several areas under the car would have been very difficult with the cage in place. So I decided bolting it in was a better long term plan, as far as future flexibility and serviceability of the car. This will also allow me the get the entire cell cage powder coated rather than having to paint it. Painting it would have been a difficult proposition as it is nothing but nooks and crannys. It is bolted in with eight 3/8" ARP bolts, that screw into weld nuts on the underside of the framework. Perhaps not quite as strong as welding it in, but more that strong enough for any plausible eventuality. Cell then drops into the framework and bolts in as shown. The attachments on the bottom of the cell cage are stainless steel stock that I made into jacking/jackstand points. They are stainless as I intend to leave them unpainted, since jackstands always seem to remove paint anyway....and at least they won't rust. A bit over-engineered...I know. They are off to the sides because I am about 80% sure I am going to run my exhaust right down the middle below the fuel cell (with heat shields). Thanks for looking! -
ANOTHER Datsun Z/LS3/T56 Swap Thread
Ironhead replied to Ironhead's topic in S30 Series - 240z, 260z, 280z
Well, I have been regularly working on the car since my last post....just haven't posted in a while because it feels like I am spinning my wheels and not getting much done. I managed to finish the strut tower bars and sway bar mount reinforcements, and completed the modifications to the firewall to mount the Tilton master cylinders: Finished the structural modifications to the rear of the car for the fuel cell cage to drop in. Just have to re-skin the framework with sheet metal: And, spent some time welding up the assorted cutouts and holes from the bumpers, OEM exhaust, marker lights, antennas, and other items I won't be using. That's pretty much it. Feels like a lot of time invested over the past month or so without much progress. Thanks for looking. -
Lookin great dude....thanks for the update pics!
-
I too just now saw this post.... The most common problem for beginning TIG welders is overheating the part by moving too slowly and "heat sinking" it. This is particularly an issue when welding thin stainless. It takes very little time for this to happen, and you wind up with grey welds that have lost their stainless properties, I think primarily from the chromium cooking out. It is sort of a balancing act between using enough heat to quickly get a weld puddle, then promptly getting moving so the part is not overheated. I saw a video on "Welding Tips and Tricks" where he did some tests with TIG welding, and the amount of heat absorbed by the parts being welded had far more to do with the speed of travel than with the heat settings on the welder. When I welded my first stainless exhaust....I simply did not have the experience/skill to move the puddle fast enough and was overheating all my welds. I finally managed to come up with a workaround, just clamping thick copper pieces to the parts to serve as heat sinks. That buys you a bit of time, but really it is an issue of just needing more practice.
-
Z-Envy Race Car - Champ Car Series
Ironhead replied to Gmagno's topic in S30 Series - 240z, 260z, 280z
Looks like a great project, congrats! Some of the things that have been done to old race cars always intrigue me. I wonder why they added the framework under the driver and passenger floor? Seems like it would add no rigidity but a lot of weight.... -
ANOTHER Datsun Z/LS3/T56 Swap Thread
Ironhead replied to Ironhead's topic in S30 Series - 240z, 260z, 280z
I spent my last few days of shop time conjuring a mounting system for my steering column and bias bar pedal system. I am using electric power steering, which occupied some of the room for the pedals, and the pedal assembly was not compatible with any of the stock mounting locations, so I had to cut it all out and start from scratch. The steering column mount was easy...it just consists of two heavy duty 1.5" tubing clamps welded together at 90 degrees with a short section of tube between them, then bolted to the dash bar and column. I was a bit surprised that a 45 year old Japanese car used 1.5" tube for the steering column...but that is the case and it made things easy. The mount is so rigid I have no doubt you could lift the car by the steering column and the mount would not shift. I wanted it really beefy because the mount supports the weight of the power steering motor, which is cantilevered a foot or so outward. The motor for the electric power steering wanted to interfere with the pedal assembly...so it took some dicking around to figure out the best way to mount everything and have it peacefully co-exist. Just one of those jobs that is simple in concept, but time consuming to actually implement....at least for me. Thanks for looking. -
ANOTHER Datsun Z/LS3/T56 Swap Thread
Ironhead replied to Ironhead's topic in S30 Series - 240z, 260z, 280z
Calling the cage done, at least from the dash back. Also hit the tubes and welds with Scotchbrite so they are ready for primer. -
TrackZpeeds CXRacing LS1 T56 240z
Ironhead replied to trackzpeed's topic in Gen III & IV Chevy V8Z Tech Board
Hard to make recommendations...colors are so personal. For track cars I like saturated non-metallics...pastel easter-egg type colors.... Like the colors Porsche offers in the GT3 RS. I would like to see a "Z" in Porsche "Signal Green"....for example. -
ANOTHER Datsun Z/LS3/T56 Swap Thread
Ironhead replied to Ironhead's topic in S30 Series - 240z, 260z, 280z
Just a small update... In trying to finish up the cage, I thought I had planned sufficiently and left adequate access to 360 degree weld up all the joints. But with the bases of the main hoop...no matter where I stick the welder, I could not get the angle/visibility I thought I needed to lay down a decent bead. And I knew if I fucked it up....getting a grinder in there to redo it would be a nightmare. The easiest approach wound up being to cut weld portals in the fender. Sounds like a bit of poor planning, but it worked out OK. Started assembling the rear hub uprights from T3. I found that the way they were machined, the stock Nissan axle seals would not fit. I perused the 'net every which way, trying to find a seal that would work....but found nothing. So, I wound up having aluminum bushings machined to press in so that the OEM seals would work. Maybe overkill....I dunno...since the wheel bearings have their own seals. But Nissan (Infiniti) used the axle seals in the OEM application, and I figured they must have had a reason.....so I went with "better safe than sorry". Thanks for looking. -
It's kind of funny...with that stitch welding....I found it was easier to just do everything than to decide where there might be a benefit and where there wouldn't. As long as you do it slowly and don't overheat things....there is no way a stitch weld can really do harm...so....you know....go for it. Project looking great dude.
-
ANOTHER Datsun Z/LS3/T56 Swap Thread
Ironhead replied to Ironhead's topic in S30 Series - 240z, 260z, 280z
I had a bout of flu and took a couple of weeks off from working on the car... When I returned to it I decided to tackle the rebuild/assembly of the CV axles, using the T3 shortened axle shafts. Early on in this project, I purchased the entire rear end assembly of a junked 1994 Infiniti Q45. This included CV axles, but I had some doubts about their condition because it was apparent that all of the parts had simply been sitting outside in the elements for many years. The wheel bearings and many other parts were shot. So, I also ordered a cheap set of CV axles for $70 each from a major online parts retailer. That price, when the OEM Infiniti axles are around $1K each....should have been more of a warning than it was....more on that later. Trying to disassemble the axles, the "inner" bolted portion came apart without issue. But the other end, where you have to basically knock the CV bearing off the end of the splined shaft, over a snap ring, simply would not come off. I beat on the thing until I was hating life, and even tried dropping it inside a piece of 2" tube, but it would not budge. Since I was not going to re-use the shafts, out of desperation I wound up taking a cutoff wheel to the shafts, cutting them as close as possible to the CV joint. This allowed me to pivot the CV sufficiently to take out the bearings, then remove the cages. I was pleasantly surprised, the bearings actually looked pretty good. No pitting or signs of significant wear on the races. I also dismantled one of the new $70 CV axles....just to compare. It was immediately obvious the cheap replacements were crap. The machining of the parts, the tolerances, everything....was clearly vastly inferior to the OEM Nissan components, so I decided I would just clean and re-use the junkyard parts. Along the same lines, I had some "universal" CV boots that I ordered online to use on the rebuild. Here again, the aftermarket parts had little in common with the Nissan parts....the aftermarket boots for example were about 1/3 as thick as the OEM ones....and I had major doubts about how long they would last. So I managed to track down some CV joint rebuild kits from Nissan and used them....which of course cost about 6 times as much as the generic boots. So I wire brushed and painted the junkyard parts, then it was just a messy/greasy job re-packing everything and putting it all together. I wound up using the crimp-on style boot clamps (the OEM Nissan ones work differently) just because I happened to have the proper tool for crimping them. For grease, I used Redline synthetic CV joint grease....mainly because I have trememdous faith in all Redline products. These Q45 axles are pretty beefy....I figured since they came on a RWD car that weighed twice as much as what I am building, they were the best bet for withstanding the LS3 torque. Thanks for looking. -
TrackZpeeds CXRacing LS1 T56 240z
Ironhead replied to trackzpeed's topic in Gen III & IV Chevy V8Z Tech Board
I know T3 currently sells front struts wherein the entire thing....spindle included....is manufactured/machined for them. No OEM Datsun parts used at all. I presume that would make them a bit stronger....but not sure. -
ANOTHER Datsun Z/LS3/T56 Swap Thread
Ironhead replied to Ironhead's topic in S30 Series - 240z, 260z, 280z
Thanks much Mike, glad you are getting something out of it. I got the cage dropped to fully weld all the awkward joints up by the roof and other body panels. I thought this would be kind of a hassle, but it went fairly smoothly. I wish I could do prettier welds. I can do OK on a bench when light and position etc are perfect....but welding up the cage...with all the contortions and awkward positions, is a different story. I know the welds are all structurally sound and are not coming apart...at least. I also permanently welded in the base structures for the main hoop. Probably overkill, but I also welded a support inside of them out of a piece of tubing...since it added virtually no weight and should make them extremely robust. Thanks for looking. -
Nelson, do you have any estimate as to how much of the flares will be filled up with the 275s? I suppose without your drivetrain mounted it is pretty hard to guess.... I am "thinking" (still a ways down the road) of running 315s in the rear....and I was wondering if the YX flares would fit them....or if I would have to go with the IMSA kit....
-
It looks like you are pursuing the same basic vision as I am...you are just much further along. Looking really great. What do you think of the basic quality and fit of the Ztrix parts? I am torn between the IMSA kit, the YZ kit (like yours), or the Pandem kit. I like the looks of the pandem kit the least, but being Japanese it is probably of very high quality. Do your strut tower bars tie into the dash bar, or ? And do they eliminate the possibility of using wipers? I still haven't decided how I am going to handle doing that portion of the cage. I admire the dedication of your fab guy doing the stitch welding for you. I did it on my own car and thought about killing myself a few times. It really is a sucky job, particularly if done thoroughly.
-
Hoke Performance LS2/T56 install starts today.....
Ironhead replied to mrk3cobra's topic in Gen III & IV Chevy V8Z Tech Board
Hoke provides driveshafts now too huh? That will be good to know down the road. Project is looking great! It kind of reminds me that in many ways a pure track car like I am building is so much simpler....no messing with getting a decent stock dash and all that! -
ANOTHER Datsun Z/LS3/T56 Swap Thread
Ironhead replied to Ironhead's topic in S30 Series - 240z, 260z, 280z
Got the door bars done. I still need to add a harness bar and a dash bar (I will do those after dropping the cage and welding the awkward spots), and some gussets, but other than that I think I am calling everything from the dash back to be "done". I can think of additional bars I could add that might stiffen things up a bit, but IMHO I kind of feel most of it would be diminishing returns. Everything has been a trade off of adding stiffness and chassis integrity, while still allowing decent access in and out of the car. I think I am at a decent place to stop. Thanks for looking. -
ANOTHER Datsun Z/LS3/T56 Swap Thread
Ironhead replied to Ironhead's topic in S30 Series - 240z, 260z, 280z
Got a bit more done on the cage today. I put in the diagonal bracing in the plane of the braces to the rear strut towers, rather than in the plane of the main hoop. I have a very far rearward seat position, and a diagonal brace in the main hoop would interfere with some of my seat placement options. The rearward diagonal braces as I have done are allowed in the SCCA regs in place of a diagonal brace in the main hoop, I presume for the same reasons I chose to do it...room for seat placement. I am looking for opinions...virtually every "Z" cage I have seen done has used a horizontal bar between the rear strut towers. I am thinking that in my case, with the rearward diagonals...the horizontal bar would be wasted weight and bulk. I don't see how it could do any more to brace the strut towers than the bars I already have in place. What do you all think? It is tempting to include all sorts of bars here and there to increase rigidity, but it definitely becomes a decreasing returns thing at some point...and needless weight. -
ANOTHER Datsun Z/LS3/T56 Swap Thread
Ironhead replied to Ironhead's topic in S30 Series - 240z, 260z, 280z
Thanks...I can see where it would be less than rigid. Is there a better design available, or is it a matter of fabbing something up? The diff will be a short nose R200. -
ANOTHER Datsun Z/LS3/T56 Swap Thread
Ironhead replied to Ironhead's topic in S30 Series - 240z, 260z, 280z
I honestly don't know. The way I read the SCCA regs, the cell itself has to be enclosed/partitioned, but it doesn't specifically mention remote fill points one way or the other. Maybe someone with experience wheel to wheel racing will weigh in. Since the one way fill valve is in the cell itself, it doesn't seem intuitively that a remote fill cap outside the enclosure would greatly increase the hazard....but what do I know? I know SCCA regs allow fuel lines to run through the driver's compartment (as long as they are braided steel or hard lines) and those contain pressurized fuel. It seems like an 'empty' fill hose would be a lower risk than that? I don't plan on ever having to pass tech with my car....I just think following the safety regs is a good idea. -
ANOTHER Datsun Z/LS3/T56 Swap Thread
Ironhead replied to Ironhead's topic in S30 Series - 240z, 260z, 280z
Thanks much! I would like some sort of remote fuel fill...I am thinking I might just put a fill cap in the stock location, connected to the fill neck on the cell with a 2.25" filler hose. But, I plan to enclose the top of the cell in an aluminum bulkhead (as required in SCCA rules for cars without an enclosed trunk area), so ideally the fill hose would also have to be enclosed in the bulkhead...which would be complicated. I could just run the fill hose through the bulkhead...which would slightly compromise the safety aspects....so I dunno. You have a good eye...I have both a direct fill plate for the cell and a remote fill plate....because I keep going back and forth as to which approach makes more sense. I might just encase the cell in the aluminum bulkhead, and put a remote fill cap on top of the aluminum. Then I would have to open the hatch to fill up, but not open a trap door to get inside the enclosure to access a direct fill cap. I spend a lot of time pondering these details.... I am also not decided on which fender flares I am going to use...as the full blown IMSA style flares completely cover the stock fuel port IIRC.