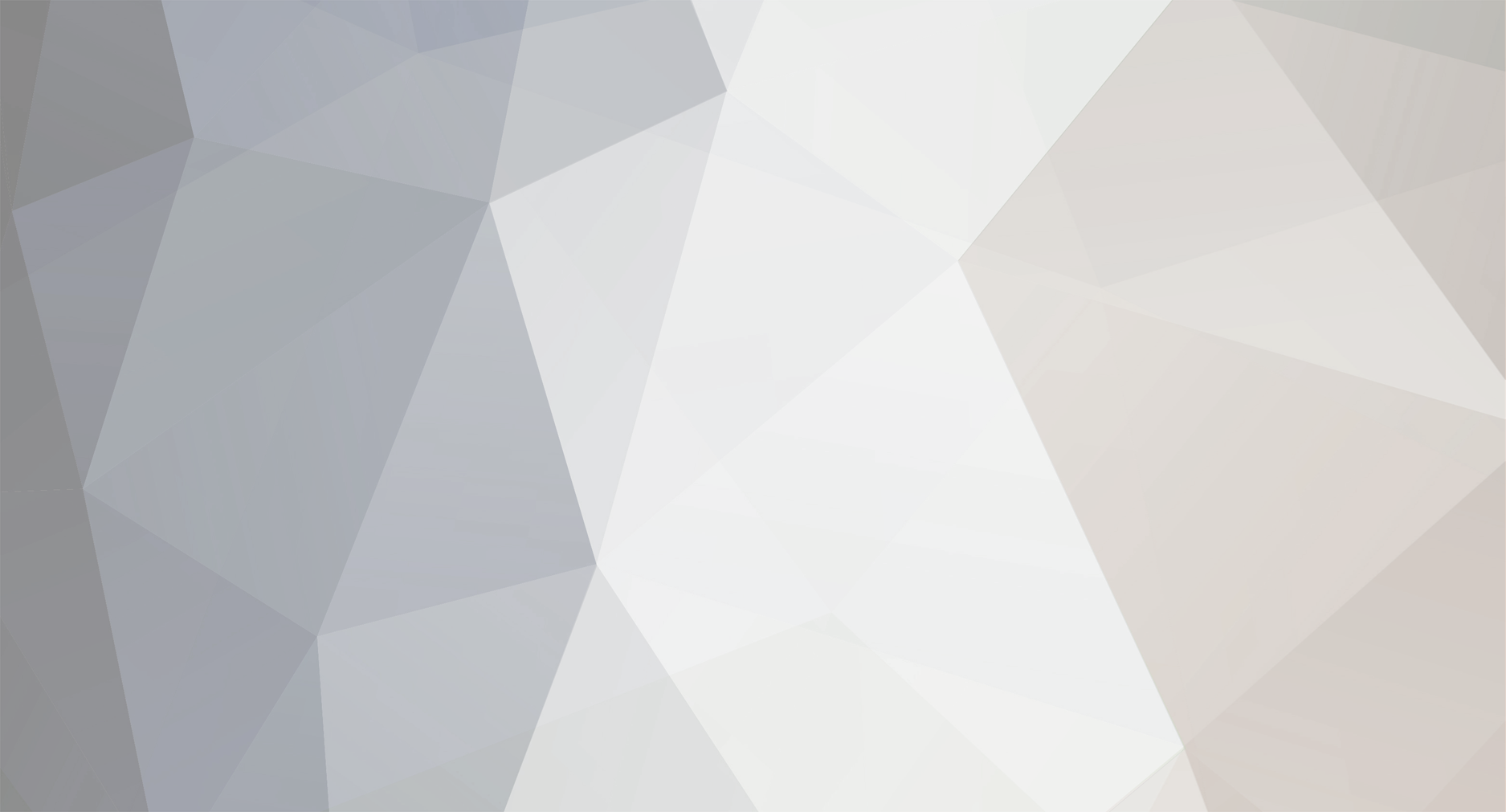
Ironhead
Members-
Posts
529 -
Joined
-
Last visited
-
Days Won
18
Content Type
Profiles
Forums
Blogs
Events
Gallery
Downloads
Store
Everything posted by Ironhead
-
Driveshaft length for R200 Short Nose swap
Ironhead replied to Dwayne_The_Rock_Datsun's topic in Drivetrain
I think it's because there are so many variables... I have the sort nose R200, but also an LS3 and T56. Even with that specific engine/tranny combination, driveshaft length will still vary depending on what engine mounts are used. If your car is completely stock except for the diff, someone might have measurements for you. But it does seem like the safest approach would be to mock everything up and take measurements. Most places that make custom shafts move pretty quickly. -
To help with the impatience (which I have as well) you can cool the metal with compressed air after each small amount of welding. This keeps heat from building in the panels and allows you to move forward much faster.
-
ANOTHER Datsun Z/LS3/T56 Swap Thread
Ironhead replied to Ironhead's topic in S30 Series - 240z, 260z, 280z
Thanks much guys. -
ANOTHER Datsun Z/LS3/T56 Swap Thread
Ironhead replied to Ironhead's topic in S30 Series - 240z, 260z, 280z
Had to custom make a couple of offset interior door handles, as the stock ones would not clear the roll cage door bars. I knew this was going to be an issue, and initially planned to just use a couple of pull-cables to open the doors, but that introduced issues as well. Namely, the cable handles, unless very small, wanted to hang down and get caught when trying to close the doors. This was a bit more work, but hopefully a better long term solution. Basically they differ from stock only in moving the lever approximately two inches downward so they open freely below the door bars. -
ANOTHER Datsun Z/LS3/T56 Swap Thread
Ironhead replied to Ironhead's topic in S30 Series - 240z, 260z, 280z
No, I just buy them piecemeal here and there as I need them. Ordering in bulk wouldn't work because generally you only need a few of specific thread/pitch/length. In fact they come in five-packs...often that is even too many so I have a box with lots of spares. It seems inexpensive ordering a few here and there...but I imagine if I was dumb enough to tally everything I have spent on hardware it would be stupid money. Fortunately I am smart enough to never, ever do that....LOL. -
Project 1973 240z, LS/T56, S14 Suspension, Tube Chassis
Ironhead replied to Turbo6.0's topic in S30 Series - 240z, 260z, 280z
Very ambitious/impressive work! I look forward to seeing more. -
ANOTHER Datsun Z/LS3/T56 Swap Thread
Ironhead replied to Ironhead's topic in S30 Series - 240z, 260z, 280z
Made front and rear tow hooks: And a front splitter. The splitter is 1/4" ABS, which had the advantage of being affordable and available locally, so that shipping didn't kill me. I have a feeling this part (if I leave it on) will need frequent replacement. ABS also seems to have a good combination of adequate rigidity with some flexibility so that impacts "may" not always break it. I am starting to run short of tasks that still need to be done prior to starting painting. So, I need to construct some sort of makeshift paint booth, which will be a chore. Thanks for looking. -
Let's talk brake system design
Ironhead replied to 280Z-LS3's topic in Brakes, Wheels, Suspension and Chassis
You could just call Wilwood, Stoptech, or Essex Parts (AP Racing distributor), tell them the weight of your car, how you will be using it, and what size wheels the brakes need to go under. Budget will be a huge consideration too. Of the three Wilwood will definitely be the most affordable. AP and Stoptech components range from somewhat reasonably priced to astronomically expensive. AP Racing parts go all the way up to F1 components...you can imagine what that costs. Anyway, they could recommend compatible front/rear disc and caliper combos suitable for your use and budget. They could also suggest pedal/master cylinder setups...or you could just shop around after you decide on discs/calipers. I really like Tilton pedals and master cylinders. Coleman racing can machine custom brake hats reasonably inexpensively once you know what you need. I personally would go with floating discs in front, not so important in back because the rears generally see far less heat. -
Let's talk brake system design
Ironhead replied to 280Z-LS3's topic in Brakes, Wheels, Suspension and Chassis
Most of the aftermarket brake companies, be it Wilwood, AP Racing, or whatever manufacture calipers intended for front wheel applications, and others for rear wheel applications. The rear oriented calipers will have smaller overall piston area to give you a default "bias" that is in the ballpark for most cars. The bias is fine tuned/corrected with either dual master cylinders and a balance bar, or with an adjustable proportioning valve. Each method has strengths and weaknesses. In general racing/track cars would be best served by a balance bar, and street cars with an adjustable proportioning valve. The relevant data are combined (assuming multiple piston calipers) piston size for each front caliper, combined piston size for each rear caliper, brake disc diameter front/rear, and tire diameter. With this information, companies like Tilton Engineering can make sound recommendations for front/rear master cylinder sizes. None of this is rocket science, but there is a lot of data and arithmetic involved in sizing everything correctly. I agree with the prior post that many brake "upgrades" are actually not always true performance upgrades. People get away with just bolting on huge discs and 4-piston calipers on the front brakes only, because generally such a mod just dramatically increases front brake bias. Front brake bias is "safe" (it won't cause the car to spin), but many of these aftermarket front brake upgrades will actually increase stopping distance from stock. To do it right, brakes need to be a system involving front/rear, master cylinders, and proportioning systems. If this is done correctly, you can dramatically improve on the stock brakes in terms of weight, "feel", stopping distance, and fade resistance. -
ANOTHER Datsun Z/LS3/T56 Swap Thread
Ironhead replied to Ironhead's topic in S30 Series - 240z, 260z, 280z
Tiny steps forward.... I used small magnetic latches to position/hold down the inspection covers, since the fiberglass fenders deleted the stock parts. Made a simple "grill" to protect the radiator/oil cooler/air filter from rock/other debris damage. Parts are all stainless steel, because I initially planned to leave it unpainted. But, I dunno, it kind of looks like I am trying to prevent pigeons from roosting or something. I will probably have it powder coated black. Grill just bolts into the stock grill mounts. -
Hoke Performance LS2/T56 install starts today.....
Ironhead replied to mrk3cobra's topic in Gen III & IV Chevy V8Z Tech Board
I'm using an electric power steering setup on my LS3 swap build. I am using the Hoke engine mounts, but with a modified Apex crossmember. The steering rack and shaft are not stock, but they run in the same place as stock, and are actually a bit bulkier than stock. You can see the shaft clears (barely) the base of the Hoke mount. Honestly, with electric power steering and the stock parts, it is completely a non-issue as all the power steering components are under the dash anyway. I can't say I am 100% excited with the "feel" of the EPS, but all I have done is power it up and test it as the car is not yet running. It reminds me sort of like the "dead" feeling over-boosted power steering on 1970s Detroit cars. There is a knob with the EPS to control the power boost, but it is less than perfectly linear/predictable. This is NOT a Silver Mine kit, theirs may well be different or better. My plan is to have a switch, power it on for slow speed maneuvering, and more than likely turn it off on track or at speed. -
Nice looking car. If I wasn't an idiot I would have just bought yours rather than spending years building my own... It surprises me a bit how little money these modified/swapped Z cars bring in. No way in hell that car could have been sourced and built for $21K. But that's true of all "resto-mods". I see modified muscle cars for sale at the various televised auto auctions....cars I know have well over $100K into them....hammering at perhaps $45-50K. It goes back to stock collector cars always being worth the most money.
-
set up wheels ( for track or general...)
Ironhead replied to nzarano's topic in Brakes, Wheels, Suspension and Chassis
I have used alignment strings for years also. They are fairly easy and convenient once you have built the jigs for each specific car, but I consider fabbing the jigs to be a bit of a PITA. -
ANOTHER Datsun Z/LS3/T56 Swap Thread
Ironhead replied to Ironhead's topic in S30 Series - 240z, 260z, 280z
LOL...thanks for that. I wish that was my attitude. -
ANOTHER Datsun Z/LS3/T56 Swap Thread
Ironhead replied to Ironhead's topic in S30 Series - 240z, 260z, 280z
This is all pretty much my thoughts as well. But the seller is flakey, and I cannot find any way to contact Restored. It is hard to believe a composite shop could repair it for much less than the cost of the part. Any way you slice it, a lot of labor would be involved. Do you know of a shop in Nor Cal that does that sort of thing? I suppose I could dabble into CF work...but it requires vacuum bagging and all that...so....you know......F**K. I tell ya, my experiences with aftermarket Datsun body parts have, with the notable exception of Ztrix, totally sucked. -
ANOTHER Datsun Z/LS3/T56 Swap Thread
Ironhead replied to Ironhead's topic in S30 Series - 240z, 260z, 280z
Yeah, my Restored hood fits well. I'm totally satisfied with that part. The hatch though is really bugging me. I know I should just live with it, but I also know if I do the poor fit is going to bug the crap out of me. -
ANOTHER Datsun Z/LS3/T56 Swap Thread
Ironhead replied to Ironhead's topic in S30 Series - 240z, 260z, 280z
I thought about doing that, it would definitely be the best way to address the gap. The problem though, is that from then on the body would be "wedded" to an undersized hatch. I have no idea what might happen down the road, but a correctly sized hatch would no longer fit if for whatever reason I had to change out the current one. I could also extend the CF hatch all the way around its perimeter with fiberglass...since I am going to paint the hatch anyway...but it would be a crap-load of work and I don't really know how stable a CF/FG hybrid edge would be long term. Or I can say "racecar" and live with the gap. It's not a functional problem, just looks like shit. I know Restored.JP has a fairly good reputation, but I literally could not find any way to get ahold of them. The "contact" link on their site is non-functional, and there is nothing else. I'm pretty salty about the whole thing....particularly having to go through flakey spare-time vendors like "Datsmo" who are eager to sell expensive products but won't lift a finger to stand behind what they sell. As you can probably guess...that hatch was not cheap. I'm sure he could get ahold of Restored, since he deals their stuff, but he didn't even want to be bothered with discussing it. He tried to tell me the part can't be undersized, but of course didn't want to see photos/measurements/proof that it indeed was. The other thing...I waited well over six months for that hatch. Even if Datsmo was a reputable seller and a replacement hatch could be sourced, I'm not willing to delay the build that long. -
ANOTHER Datsun Z/LS3/T56 Swap Thread
Ironhead replied to Ironhead's topic in S30 Series - 240z, 260z, 280z
I got the rear hatch bolted in place to check fit. It went on OK, but the panel gaps quite frankly suck. I knew this was going to be an issue, because when I received it I took measurements and found it to be roughly .25" smaller than the stock hatch. So the fit is predictable....it "works" but there are huge (roughly 10mm) panel gaps. This all kind of pisses me off. I know CF can shrink during the curing process, but shouldn't the builder know this and compensate? If the common sense expedient of just making the part .125" or so over-sized was followed, the part could easily be sanded to fit. But by making it .25" too small....what the hell can be done to address the fit? There is no practical way to enlarge it over the entire perimeter. I mentioned the under-sizing to the seller ("Datsmo") and was soundly, completely, and entirely blown off by him....his only response "take it up with Restored.jp" (the maker of the part). The only reason I was dealing with Datsmo in the first place was because Restored.jp would not respond to emails and could not be reached....and Datsmo was the only seller for these parts I could locate. Once the problem surfaced, he was unwilling even to contact Restored on my behalf. Datsmo had his money, why should he care? Meh, the Datsun parts aftermarket can be frustrating to deal with. I imagine I will just suck it up and use the hatch, panel chasms and all. I guess it isn't a huge deal. At any rate, no good alternatives.... I made some rear fender liners, using 1/16" ABS made with patterns utilizing Cardboard Aided Design. This was pretty simple, and I found IMHO that the 1/16" ABS was pretty much an ideal material for this task. I mainly just didn't want crap getting thrown up between the fiberglass "over-fenders" and the car body. The fronts will be a bit more complex. We'll see how that goes. -
ANOTHER Datsun Z/LS3/T56 Swap Thread
Ironhead replied to Ironhead's topic in S30 Series - 240z, 260z, 280z
So...I am using the Skillard rear spoiler...and also a CF rear hatch. The Skillard wing uses adjustable turnbuckles to hold and set the angle of the spoiler. The turnbuckles are designed to attach to the stock hatch sheet metal, which is probably up to the task. The CF hatch however had paper thin CF in this area, that would flex with the slightest finger pressure, and I didn't think it was strong enough to support the aerodynamic forces pulling on the turnbuckles. At best I figured it would flex enough to crack the paint. So I started by adding six or seven layers of fiberglass to the portion of the hatch involved: This didn't seem like it added enough rigidity, so I made this contraption out of aluminum plate and spacers: It spreads out the load on the turnbuckles to the aluminum and to the hatch framework, so hopefully there will be no issues down the road. It also doubles as a panel to fill in the hollow portion of the hatch. I figure I will paint it satin black. -
Hoke Performance LS2/T56 install starts today.....
Ironhead replied to mrk3cobra's topic in Gen III & IV Chevy V8Z Tech Board
Everything looks great, fantastic work. I wish mine was that far along. -
ANOTHER Datsun Z/LS3/T56 Swap Thread
Ironhead replied to Ironhead's topic in S30 Series - 240z, 260z, 280z
That's kind of what these lights are Max...they are the same standardized 7" lights like you see on motorcycles...although they do lack the indicators. As far as legality, the USA is kind of funny that way. Other than emissions laws, which this car is old enough to be exempt from, there aren't really that many laws that apply to one-off custom cars built by the owner. Almost anything can go on the road, there are very few laws that apply, and most of the laws that are there never get enforced. Basically I need headlights, brake lights, turn indicators, windshield wipers....I think fenders...and not too much else. -
ANOTHER Datsun Z/LS3/T56 Swap Thread
Ironhead replied to Ironhead's topic in S30 Series - 240z, 260z, 280z
Trackspec...the larger outer ones are part #U5512SHL, the smaller inner ones #U412SHL-B. -
ANOTHER Datsun Z/LS3/T56 Swap Thread
Ironhead replied to Ironhead's topic in S30 Series - 240z, 260z, 280z
Trying to wrap up a long list of small tasks to get the car ready to start painting... From the time I first assembled the fenders/bumper, the gaps circled in the picture below have kind of bugged me. I kept telling myself...you know..."fiberglass front end"...."racecar"....and other excuses to try to just live with them. I knew fixing them would be a bit complex because simple trimming or filler would not do it. Also, this time of year (cold) the fiberglass is taking a long time to adequately cure for sanding. After a couple people looking at the project said "what's with those gaps?" they started to haunt my dreams and I knew I had to get off my lazy ass and fix them.... I ordered some 1/32" G10/FR4 and bonded it to the inside of the fender as sort of a backing: Then carefully sanded down the outside of the fender to make a gradual taper to "zero"....to provide a place for the fiberglass to bond to: Then added four or five layers of fiberglass: After sanding and trimming, I'm happy with the result and glad I did it...I think it looks a lot better. I honestly don't know if this was the "correct" way to extend a piece of fiberglass, but it seems like it worked and the result is quite rigid and seems as strong as the original edge: As can be seen, I also modified the fiberglass to allow the use of the stock headlamp buckets. This was kind of involved as once the flat panel is cut out to allow the buckets to fit in place, the outer section of fiberglass prevents access to the screws to fasten the headlamp retaining rings. The only solution I could conjure was to sand out the divots/recesses in the fiberglass to serve as ports to put in the screws. This required greatly thickening the back of the part with layers of fiberglass in each spot, or the "divots" would have cut through the fiberglass and been "holes". I suppose this would have served the purpose, but it would have looked like shit IMHO: The headlamps are Morimoto Super 7 LEDs. They are kind of interesting in that there is no high/low beam circuit. They are always "on" full bright, but when on low beam there is a metal shield on a servo motor that moves and covers part of the LED to provide a low beam pattern and prevent blinding oncoming traffic. I realize the turn signals won't win any style points. But...I needed to include them....and couldn't come up with any clever/stylish way to incorporate them....so I just sort of "did it". The light bar probably won't be installed most of the time. It is easy to unbolt, and might lessen incoming cooling air somewhat. But this will be a street legal car, and I thought it might come in handy for nighttime canyon drives...or something. I have one of these on my DD Subaru, and once you have used them on dark roads it is hard to be without one. The light they put out is incredible... Thanks for looking. -
Well...my plan involved using thin enough ABS that it would follow the wheel well contour without having to be heated or molded....just sort of flex it in and screw it into place. I am pretty sure I can do this with 1/16", less sure about 1/8"....but the stock fender liners are 1/16" or less thick anyway... Is there something I am overlooking/am I going to have a rude awakening when I try this?
-
I'm planning on making my own out of either 1/16" or 1/8" ABS. I haven't done it yet but it looks like it will be fairly simple (famous last words)....