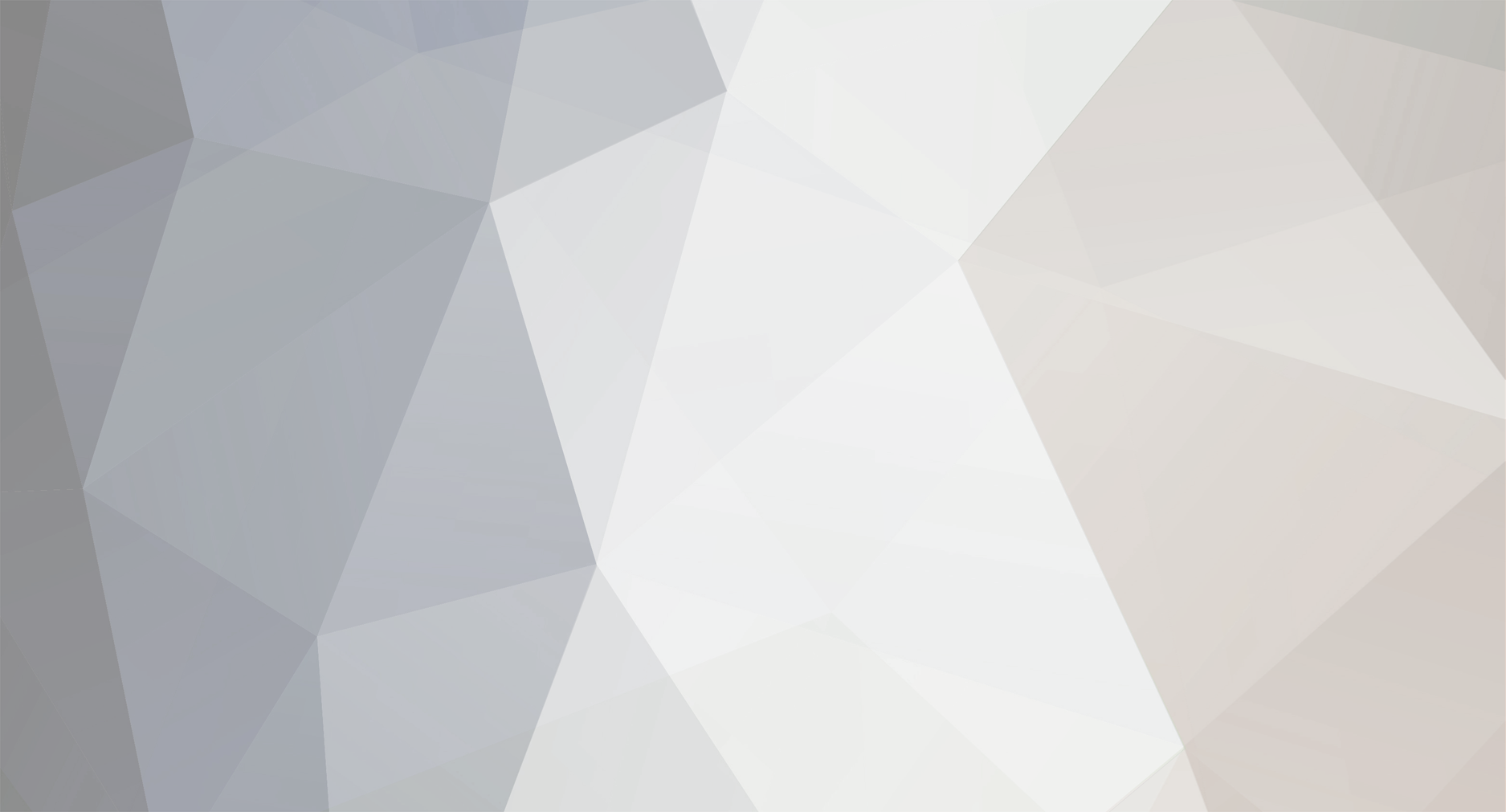
Ironhead
Members-
Posts
529 -
Joined
-
Last visited
-
Days Won
18
Content Type
Profiles
Forums
Blogs
Events
Gallery
Downloads
Store
Everything posted by Ironhead
-
ANOTHER Datsun Z/LS3/T56 Swap Thread
Ironhead replied to Ironhead's topic in S30 Series - 240z, 260z, 280z
Hood pins/latches and vents installed: -
ANOTHER Datsun Z/LS3/T56 Swap Thread
Ironhead replied to Ironhead's topic in S30 Series - 240z, 260z, 280z
Moving forward at a glacial pace, but I did manage to add an aluminum stiffener to the bottom of the air dam, to tie everything together and keep the fiberglass parts rigid. This plate was going to be the attachment point for a splitter, but I have a nagging feeling given my intended use, a splitter might be more of an PITA than it's really worth. Ground clearance is going to be an issue already. -
I installed them on my early '74 260z. In my case, I plug welded them. Most of these cars have bowed /damaged floorpans. I found that by drilling holes through the floor/stock rails/Bad Dog rails, I could use M5 bolts to draw it all tightly together. This pretty much straightened out my floor pans and the stock rails. IIRC correctly, I made plug welds every inch.
-
I don't know the car, but I am in California. Do you by any chance know what city it is supposed to be in?
-
ANOTHER Datsun Z/LS3/T56 Swap Thread
Ironhead replied to Ironhead's topic in S30 Series - 240z, 260z, 280z
Thanks much for the input. I'm not too worried about the edges of the splitter hitting in a corner and unloading the front wheel, just because the outer edges of my splitter plate would not be supported by anything more than fiberglass. If it hit the roadway the splitter edge /fiberglass would flex upward before significant "unloading" of the tire could take place. My "rigid" support structure would only be supporting the splitter more under the center of the car. But I have no doubt in such a contact with the road the splitter would be bent/possibly destroyed... Just so I understand....you are talking about mounting the splitter plate on a hinge, and only connecting it to the bumper with some sort of flexible material to block the wind? So the splitter could hinge and move upward with any impact, while the air dam/bumper remain stationary? -
Great work and mucho respect for taking that car on. I think I would have run screaming from it. Lots of rot.
-
ANOTHER Datsun Z/LS3/T56 Swap Thread
Ironhead replied to Ironhead's topic in S30 Series - 240z, 260z, 280z
Sorry...having trouble visualizing. If the splitter could hinge upward, wouldn't the bumper have to move upward equally? And the fenders? You have any photos of how you tackled this? -
ANOTHER Datsun Z/LS3/T56 Swap Thread
Ironhead replied to Ironhead's topic in S30 Series - 240z, 260z, 280z
Very much so.... The car is going to have ground clearance issues already, and while the splitter won't be much lower than other parts of the car, the further forward it is from the front axle, the bigger clearance problem it will become. One of the reasons I only want it installed for track events. Unless I don't understand your question....? -
ANOTHER Datsun Z/LS3/T56 Swap Thread
Ironhead replied to Ironhead's topic in S30 Series - 240z, 260z, 280z
Finished the bumper/splitter mount. I know it looks like an over-engineered monstrosity, but it actually weighs less than 10 pounds. My plan is to bolt a piece of 3/16" aluminum to this framework, which will follow the contour of the bottom of the bumper to reinforce it. The splitter will attach to this aluminum plate, not sure yet what the splitter itself will be made of. I want to do it this way because the splitter will obviously be prone to damage, and I wanted it to be as simple and cheap to replace as possible. Also, the car will see some street driving, and ...I dunno....driving around with an aluminum knife blade sticking out the front of the car seems maybe a bit...uncool. Finally, the splitter is bound to exacerbate problems with speed bumps, curbs, etc. Basically I wanted the splitter to be easily removable without having to take the entire front of the car apart, and only have it installed for track events. I wanted to use carbon fiber for these large sheet parts....but if you have ever priced 3/16" CF roughly 30" X 70"....you will understand why I went with aluminum. -
ANOTHER Datsun Z/LS3/T56 Swap Thread
Ironhead replied to Ironhead's topic in S30 Series - 240z, 260z, 280z
Thanks! -
ANOTHER Datsun Z/LS3/T56 Swap Thread
Ironhead replied to Ironhead's topic in S30 Series - 240z, 260z, 280z
Yeah, it's one of those things, when not sure of the forces involved, the tendency is to overbuild....at least that is my tendency. I hope I don't wind up with a 3000# car. On assorted amateur motorsports resources, I read that you should be able to stand on a properly supported splitter. And I'm a big f***. So, that's what I was aiming for. The bumper needs a surprising amount of support or it is literally going to flap in the wind. It is supported now in multiple places, and the lower rear corners (front of wheel arches) still move all over the place. The framework I built I think looks beefier than it really is. The tubing is .035" wall. I would be surprised if the whole thing weighs more than five pounds. But it is 4130 tube, which is pretty strong stuff. -
ANOTHER Datsun Z/LS3/T56 Swap Thread
Ironhead replied to Ironhead's topic in S30 Series - 240z, 260z, 280z
Good idea. But the structure also has to support a lot of force, as I am also going to use it to mount a splitter... I wouldn't want the down-force to start bending things. Not being an engineer, this stuff is hard for me to calculate. I'm pretty much just guessing. -
ANOTHER Datsun Z/LS3/T56 Swap Thread
Ironhead replied to Ironhead's topic in S30 Series - 240z, 260z, 280z
Support structure for the front bumper: -
ANOTHER Datsun Z/LS3/T56 Swap Thread
Ironhead replied to Ironhead's topic in S30 Series - 240z, 260z, 280z
Working on fitting the air dam/bumper. The Ztrix piece is of course just a fiberglass shell, without much rigidity, so it is going to require a fairly elaborate support structure to be fabbed up to mount and support it. I made two brackets to bolt inside the wheel wells to support both the sides of the fenders and the sides of the air dam. I also included a piece to strengthen the fiberglass headlamp mounting panel, as it was pretty flexible and I don't want the headlights to vibrate excessively. This larger tube structure (it bolts into what I think used to be the OEM bumper mounts....but don't remember for sure) will be the foundation for the rest of the support for the air dam, and I also need to conjure up some structure to support a front splitter. All the tubing I am using for these parts is very thin wall. My hope is that in a minor front end collision the tubes will bend before they transfer damage to the car unibody structure. Not sure it will pan out that way, but that is my hope. -
ANOTHER Datsun Z/LS3/T56 Swap Thread
Ironhead replied to Ironhead's topic in S30 Series - 240z, 260z, 280z
Thanks for the kind words gents. -
Dustless Blasting or Sand Blasting not a good idea?
Ironhead replied to FairladyGTR's topic in S30 Series - 240z, 260z, 280z
Clearly it can be done if the place takes care and knows what they are doing. All the panels on my car received no damage and I had the entire thing done. It was a place that sort of specializes in classic cars though (American Stripping Company in Sacramento). I considered dipping, but my main concern was that it removes paint even on the inside of frame rails and pinch welds, etc, places where rust preventative might be difficult to re-apply, but rust could most certainly be a problem. Now acid dipping combined with dip-priming seems like it would be ideal....but I never found a place that did dip-priming. I think it is pretty much OEM only. -
ANOTHER Datsun Z/LS3/T56 Swap Thread
Ironhead replied to Ironhead's topic in S30 Series - 240z, 260z, 280z
So last post I was pleased with myself about reinforcing with aluminum the sagging cutout area around the inspection panels. After that good feeling wore off and I started thinking, it actually seemed like a poor idea. Aluminum and fiberglass are bound to have radically different rates of expansion, and I figured that at best the bond would soon fail, crack the paint, and be a mess. At worst I feared it would crack the fiberglass. After reading some opinions from people who actually know what they are doing working with fiberglass, this fear was confirmed: Bonding metal to reinforce fiberglass is a bad idea, generally. So I inquired of a local plastics supplier of a product to bond to the fiberglass and provide some rigidity. He recommended G10/FR4 fiberglass reinforced epoxy composite. So I used some 3/8" thick. The stuff is crazy strong and rigid, and hopefully will have similar expansion/contraction to the fiberglass fenders and will remain bonded for eternity. After a ton of work, the fit between all the front end components is actually approaching kind of decent. Keep in mind I am not shooting for SEMA quality panel gaps, this isn't that kind of car, but I wanted it to fit together/look halfway acceptable. The "sparkly" appearance in some of the photographs is from the camera flash bouncing off the massive quantity of airborne fiberglass dust....LOL. -
Dustless Blasting or Sand Blasting not a good idea?
Ironhead replied to FairladyGTR's topic in S30 Series - 240z, 260z, 280z
They removed the undercoating on mine, but it wasn't dustless. Judging from the endless amounts I have vacuumed and blown out of the frame rails, it was a mix of walnut shell, and plain old sand. If you can find a place, I would recommend that they epoxy prime as soon as the blasting is completed. Otherwise, depending on your climate, the steel can begin rusting almost immediately. When they say "dustless" blasting, they still use some sort of blasting media, it is just mixed with water to keep the dust cloud down. But the water has the added benefit of keeping the panels from overheating. The only part I don't understand, is why the freshly blasted metal is not instantly rusted by the water. -
Dustless Blasting or Sand Blasting not a good idea?
Ironhead replied to FairladyGTR's topic in S30 Series - 240z, 260z, 280z
I had mine blasted at a place that specializes in classic cars. No damage resulted, but I imagine it could have if it wasn't done right. It is kind of a PITA though to have all the hollow areas of the car filled with blasting media.... What choice do you have though? I cannot even imagine trying to strip an entire car by hand. There is also acid dipping, but relatively few places do that, and the process brings risks and concerns with it as well. -
Front brake upgrade with slip-on rotor
Ironhead replied to calZ's topic in Brakes, Wheels, Suspension and Chassis
Most of the aftermarket CNC parts are made of aluminum, not necessarily because it is always the best choice, but because it is vastly cheaper and easier to machine than steel parts. I suspect your engineer friend is onto something. Not only from my experience with the TTT hubs, but because I have never seen an OEM car come with aluminum hubs, even considering high-end performance models from Porsche or whatever. Considering hubs are unsprung weight, aluminum is not significantly expensive, and it is easier to machine than steel, I think if it was the way to go with hubs we would have seen them on production cars for some time now. Also, the TTT hubs are so much thicker and beefier than the stock steel hubs, I would wager the weight difference is negligible if there even is one. -
Front brake upgrade with slip-on rotor
Ironhead replied to calZ's topic in Brakes, Wheels, Suspension and Chassis
I did this on my build. Not only did it make no sense (to me) to have to dismantle the hub bearings to change the disc, the OEM setup also severely limits your options regarding disc choice. I used floating discs, for example, which would not have been possible with the OEM setup. I did have problems with the TTT hubs however. Once everything was assembled, I noticed the disc had a visible wobble when mounted on the hub. I hooked up a dial indicator and measured something like .015" wobble at the outer edge of the disc. Obviously that was FAR more than could be ignored...most OEM manufacturers specify no more than .001" runout of the disc: Then I measured the runout on the TTT hub without the disc attached, and got a .002" wobble on the hub face. I think that was the source of the problem, and the wobble just magnified on the disc face since it was much larger diameter. I measured my 45 year old OEM hubs, and they measured perfectly true, no wobble whatsoever. So after pondering things for a bit, I decided to just use the stock hubs. Since I have staggered front/rear wheel/tire sizing, I couldn't really see any downside to having 5 lug in the rear and 4 lug in front. This did involve getting new front brake hats machined, but fortunately at that time I had not yet ordered wheels. I mean, I would rather have used the TTT hubs, but I knew the wobble would have been a major problem, not just with the brakes but I am sure it would have introduced a "shimmy" into the steering wheel as well. Once I received the new brake hats, the discs ran perfectly true on the OEM hubs. For the record, I do not blame TTT for the problem. I have no doubt the hubs were manufactured true. The way CNC parts are made, it would have been a far greater challenge to make them wobble than to machine them true. I think I created the problem when I pressed the bearing races into the hubs. Aluminum is very soft, and the bearing races are hardened steel. Unless they are pressed into the hubs PERFECTLY straight, I could easily see them distorting the bearing bore or shaving a small lip, in which case they would not seat perfectly true and could easily cause a wobble. I think that is what happened, and it is my fault, but I suppose it does raise some questions about the suitability of aluminum as a hub material. -
ANOTHER Datsun Z/LS3/T56 Swap Thread
Ironhead replied to Ironhead's topic in S30 Series - 240z, 260z, 280z
Still messing around with the fiberglass fenders. The RF fender lined up slightly shallow next to the door, so I built up approximately .100" thickness additional fiberglass in that area to sand it to a closer match. It has been fairly cold here and the resin is curing slowly, so I have not been able to sand it yet (still gummy). I'm not opposed to using filler for some of this, and I'm sure I will before I am finished. But for the more significant alignment errors I am trying to build up the fiberglass where I can, just to keep the inevitable use of filler to a minimum thickness. I made the cutouts for the inspection doors, and doing so required me to remove the edge ridge that was molded into the fiberglass. On the driver's side I had to remove the ridge all the way back to the windshield, to slightly narrow the fender to make it fit on that side. Without the ridge, the parts lost a lot of structural strength and sort of sagged. So I made a couple of stiffeners out of 1/8" aluminum angle stock to straighten the parts and restore their rigidity. Bonded in place with 3M #08219 urethane structural adhesive. I will probably add a couple of layers of fiberglass over the outer portion of the brackets once the adhesive has cured, just to make everything one solid piece again. Sorry for the dull photos/mundane updates, but it's all I have.... -
ANOTHER Datsun Z/LS3/T56 Swap Thread
Ironhead replied to Ironhead's topic in S30 Series - 240z, 260z, 280z
I test fit the modified RF fender and found the fit to be vastly better. Not "perfect" yet, but definitely workable now. I had the fuel cell mount powder coated black, then sprayed the inside with Lizard Skin noise control, Lizard Skin temp control, then covered that with black Raptor Liner. I was of course interested in the Lizard Skin products to minimize noise and heat transfer, since the fuel cell will sit directly above the mufflers, but it was also an experiment to see if the Raptor Liner appeared to be compatible with the Lizard Skin products, since this is the combination I plan to use on pretty much the entire interior of the car. Everything went well with the coverings. The reddish strips are just adhesive backed silicone rubber strips, to cushion the cell a bit and prevent metal to metal contact. -
I pretty much gave up trying to use continuous beads when welding very thin metal, and use a series of connected spot welds. With such thin metal, you still get ample penetration, and for me (limited skill level) it is the best way to keep the heat under control. Every place I tried continuous beads on the Datsun sheet metal, it was a shit show...both in terms of burn through and horrible distortion.
-
ANOTHER Datsun Z/LS3/T56 Swap Thread
Ironhead replied to Ironhead's topic in S30 Series - 240z, 260z, 280z
Exactly right, I hope to dial in everything I possibly can before paint. Mechanical/electrical are done, just doing bodywork and final details now. Hope to start painting when the weather warms up in the spring. Thanks much.