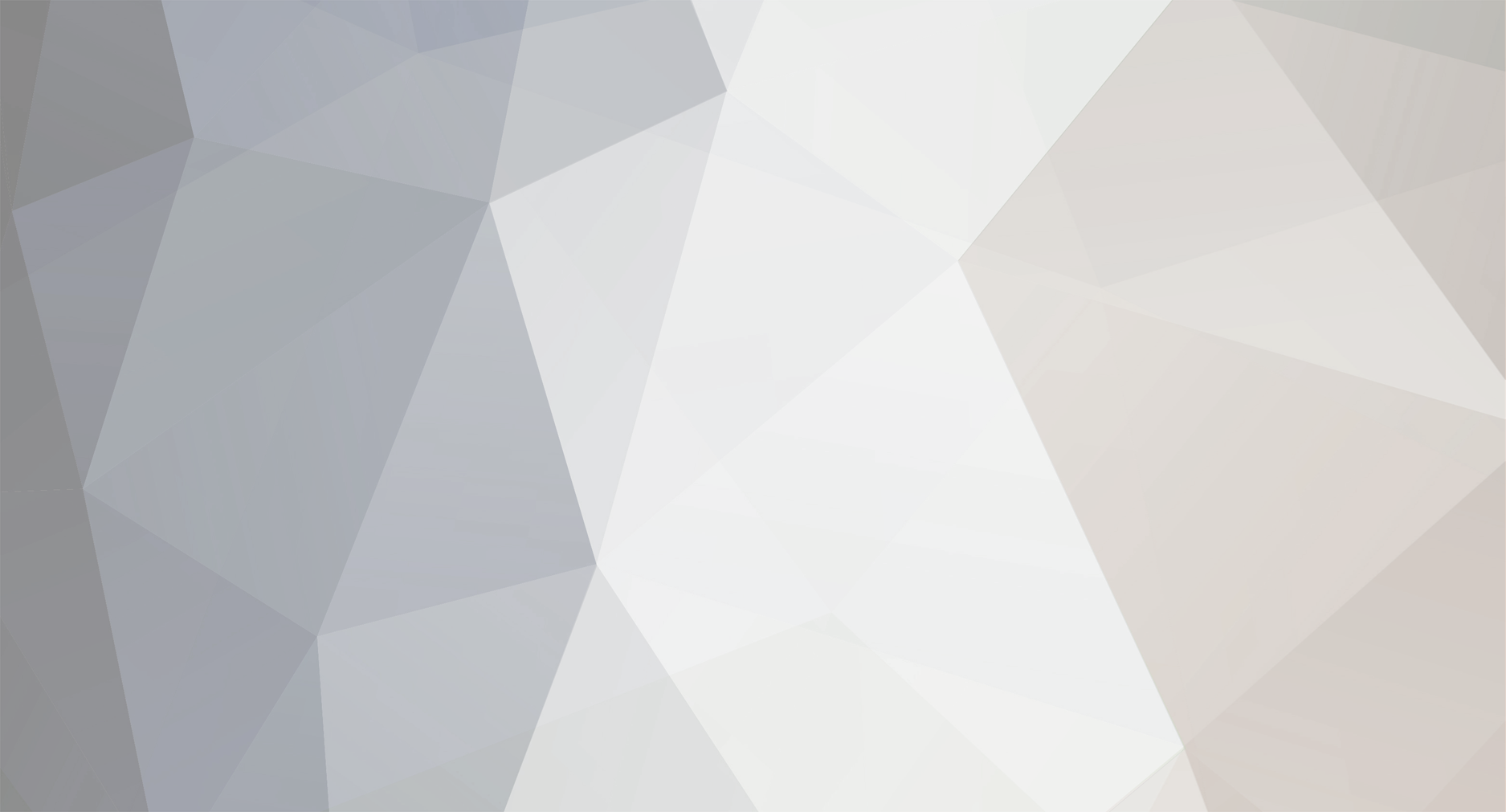
Ironhead
Members-
Posts
529 -
Joined
-
Last visited
-
Days Won
18
Content Type
Profiles
Forums
Blogs
Events
Gallery
Downloads
Store
Everything posted by Ironhead
-
Just to add my $.02.... I installed a diff cooler with an electric pump and electric fans during the build of my car. I also have a diff temp sensor, and the pump/fans are set to go on when diff oil temp reaches 240 F, and goes off when it's down to 220 F. I am running an R200 short nose with Giken LSD with the Giken oil. In street driving, even in 100 F weather, it never goes on. Diff temp stabilizes at about 210 F. On track, with 20 minute run sessions, the diff just barely reaches 240 F at the end of the session. The system usually switches on just as I am entering the pits, cools the oil to 220 F in a minute or so, and switches off. This was the case even during a 93 F track day. So I am wondering, for my purposes, if diff cooling is even needed. The oil would cool anyway as the car sits between track sessions. On street it's a complete non-issue. The Giken people said their diff oil is fine up to about 270 F. Obviously it would be needed for endurance racing or long track sessions, but neither is me. So I read all the machinations here about diff coolers, and thought I should mention that I am considering removing mine, just in the interests of simplicity and lighter weight. The pump, cooler, mounts and plumbing probably weigh 5-10 lbs.
-
IMSA GTU vintage racer build
Ironhead replied to clarkspeed's topic in S30 Series - 240z, 260z, 280z
I've used floating rotors for years on a couple of different track cars. They are particularly important on applications that require a relatively flat mounting hat, because such hats have almost no radial flex and if the discs are not floating they can easily crack with temperature extremes. I've used a couple of different designs, and all of them were secured with bolts and "jet" nuts (all metal lock nuts that "lock" due to elliptically offset threads) and thus required no safety wiring. In fact, there really wouldn't be any logical way you could safety wire them. The so called "jet" nuts will never loosen anyway, no matter how many heat cycles and how much vibration they are subject to. Once you tighten one on a bolt, you will understand why. -
I don't have any input beyond what the others said... I just wanted to say that picture you posted is pretty badass.
-
Bit late to the party, but this is how I did mine... I just welded two 1/8" thick plates to the bar so that they bolted to OEM holes in the stock roof reinforcement piece. This is probably no better or worse than just welding to it would have been, but for some reason this was my approach.
-
ANOTHER Datsun Z/LS3/T56 Swap Thread
Ironhead replied to Ironhead's topic in S30 Series - 240z, 260z, 280z
Naw. Not that kind of car. I'm fine with it as is. -
ANOTHER Datsun Z/LS3/T56 Swap Thread
Ironhead replied to Ironhead's topic in S30 Series - 240z, 260z, 280z
Thanks much! It's all good. Far more reliable than I ever expected such a concoction to be. Thoroughly enjoying it. No complaints at all, except I don't drive it much in the summer here because the interior gets pretty warm. -
I dunno, I personally am very, very careful about what I buy from RockAuto. Some of their parts are the same quality as you would get from the OEM dealership, others are so bad as to be utterly useless. You need to have a good idea what you are ordering and what it "should" cost from a reputable source. When I was putting together my car I bought a CV axle for a Q45 from them. The cost was $96. This really had me on guard, as at that time the OEM equivalent was $1200. I figured I had nothing to lose. Well, I did, I had $96 to lose. The part was such utter crap that I wouldn't have used it on anything. I dismantled the CV joints to see if any parts were usable, and I don't even have the words to describe how bad they were. I'm positive they would have knocked like crazy out of the box. As to Whitehead, the negative reports from customers have been going on for so long now that I'm surprised they are still in business. Really sad to hear people are still getting taken by them.
-
You can get a fiberglass cowl panel from Ztrix that has no holes for the wipers, but it also deletes the grills for the cabin air intake system and is a solid piece. I don't run wipers on mine currently, but I have the motor and hardware installed. I just haven't put on the wiper arms.
-
Welding VBands and keeping them from distorting is actually slightly tricky. I assemble them, with the two flanges clamped together, before final welding. If you don't do this, and weld with much heat, the flanges can distort like a potato chip.
-
When welding tubing...like an exhaust...you will find that nothing moves around much if your fitup is perfect or very good. I always face the ends of the tube on a disc sander, so that they fit together with no gap. If you do this you will get little or no movement when you final weld it. If your fitup is good you can "fusion" weld it together, with no filler, but I personally never do. I just feel better about the weld if I add some .035" or .045" filler when final welding. I realize a properly designed exhaust isn't under tremendous stress, and it's not like welding an airplane structure, but I always use a bit of filler regardless.
-
You can do a few experiments on scrap pieces and it becomes pretty apparent that back-purging on tacks isn't really necessary. As long as the fit is decent and thus the tack is pretty quick, you won't see any significant "sugaring" on the back of the tack. But when fully welding all the seams, I think back-purging is critical and I never fail to do it. Again, experiment on scrap. You will see the porous gonad-looking growths that appear on the back of a stainless weld if you don't. Not only are these likely places for cracks to start, but if every seam is welded in this matter, it would be hugely detrimental to exhaust flow as well. There are occasional welds wherein it is either impossible or impractical to back purge. In those places I either use Solar Flux, or clamp a piece of aluminum on the back of the joint to serve as a heat sink/argon trap. If none of this is possible....I just grind off the sugaring when I am done welding.
-
how do you feel your engine swap changes the character of your Z?
Ironhead replied to thedarkie's topic in Non Tech Board
It is amazing, on track, how massive amounts of torque seem to minimize the effects of sloppy driving. I also have a BMW E30M3 track car, with an N/A four cylinder engine that has very little torque, and really only develops HP above 5000 RPM. It's a classic momentum car, in which you have to take turns at the absolute limit, keeping momentum up, particularly before the long straights. If you fail to do this your lap times plummet. The LS swapped Z is completely different. Any momentum lost is immediately regained with a stomp on the throttle, almost regardless of RPM. Obviously both cars take a great deal of concentration to drive at their individual limits, but just "going fast" is so much easier in the Z. I can just mosey through turns, nowhere near the limit, and still lap significantly faster than the BMW. -
how do you feel your engine swap changes the character of your Z?
Ironhead replied to thedarkie's topic in Non Tech Board
There's no doubt an engine swap completely changes the character of the car. Mine has a 525 HP LS3, and it is more like a lighter, less refined Corvette than a Z car, honestly. Some might say I should have just bought a Corvette, but I have a method to my plan and I am happy with the outcome. -
I just wanted to say, this post made me LOL. I have wondered the same thing about the "hella flush" cars. I see so many on the 'net that cannot possible have any meaningful suspension travel. Not just Zs either, the RWB Porsches being the best example I can think of: https://fifteen52.com/blogs/52/27618305-rwb-x-fifteen52-porsche-911-993
-
I'm Back, 1971 240Z and Yes, it will be TurboCharged
Ironhead replied to 240Z Turbo's topic in S30 Series - 240z, 260z, 280z
Looks like great work on a very "needy" shell. I was just trying to imagine, think how different our "hobby" would be if cars didn't rust. By different, I mean better. -
AME complete chassis '77 280Z
Ironhead replied to lifeprojectZ's topic in S30 Series - 240z, 260z, 280z
Just reading over your plans, and have to say I was getting a bit annoyed just hearing about how hesitant AME has been to convey information or "work with you" on anything custom regarding your project. It kind of gives me the impression that their chassis are intended for show car builds wherein they do little but provide the means for the completed project to roll on and off a trailer.... -
ANOTHER Datsun Z/LS3/T56 Swap Thread
Ironhead replied to Ironhead's topic in S30 Series - 240z, 260z, 280z
I think the gearing/final drive is perfect for a track oriented car, not so much for street driving. In 6th gear at 75 MPH it is turning around 2700 RPM. I am only getting around 10 MPG street driving. The HP was alarming when I first drove the car, bit I have gotten used to it. The car puts power to the ground very well, amazingly well, actually. I can certainly break the tires loose, but only if I do it deliberately. Rear "R" compound 315 wide tires definitely do their job. I have no desire yet for more power, but I think the car could handle it fine. I have not weighed or corner balanced it. It could definitely be pretty heavy for a Z. I built it prioritizing strength/safety over light weight. Once I got the brakes dialed in, I think they are perfect. Except for the squealing. That is horrendous. Driving through my neighborhood I stop with the handbrake, just so my neighbors don't come after me with torches/pitchforks. For some reason just using the rear brakes kills the squeal. -
ANOTHER Datsun Z/LS3/T56 Swap Thread
Ironhead replied to Ironhead's topic in S30 Series - 240z, 260z, 280z
I used Lizard Skin sound deadener on the inside of the roof, but again, all it really does is get rid of the tin-can ringing effect. It doesn't deaden noise much beyond that. It's funny, I am using dual 3" exhaust and I don't consider the exhaust on the car to be particularly loud at all. The "noise" in the car is mostly coming from other places...suspension movement, road noise, and engine mechanical noise primarily. My exhaust does include a resonator and two large mufflers though. I wanted the dual 3" just in case down the road I decide to be an even bigger idiot and seek more engine power, the exhaust won't be a limiting factor. Regarding the 2.66 rack, that would be way too fast for my tastes, but then again I don't autox. If I did I would probably see it differently. -
ANOTHER Datsun Z/LS3/T56 Swap Thread
Ironhead replied to Ironhead's topic in S30 Series - 240z, 260z, 280z
Lock to lock is about two turns, but that doesn't mean much as I have rack stops in place to stop interference issues at full lock. I would say the steering rate is similar to a modern Vette or something along those lines. It still has plenty of lock to do a "U" turn on a fairly narrow street, but not enough for drifting for sure. Much of the harshness in my case comes from the fully Heim jointed suspension....and also very stiff springs. It handles great, but hates major bumps. When I hit a bump unexpectedly, it feels/sounds like I broke something....LOL. I also have very little in the car to absorb sound. The floor of the car has a coat of Lizard Skin, but honestly that really only takes away the "tin can" ringing...the car is still loud inside. I went dry sump because I have another track car, with a very sophisticated wet sump pan, and I still see the ******* oil pressure light come on during hard braking. It drives me crazy. The dry sump also greatly helps ground clearance of course, and I have read multiple accounts of wet sump LS motors having oiling issues on road courses. Dry sump is better in every way except cost. I think going with a custom chassis is a cool idea. Best of both words if you aren't concerned with "originality", which obviously I am not.... -
ANOTHER Datsun Z/LS3/T56 Swap Thread
Ironhead replied to Ironhead's topic in S30 Series - 240z, 260z, 280z
The 2.09 is what I am using. Keep in mind my shorter than stock knuckles factor into it all too, but the combination feels really good to me. You will definitely need power steering, particularly if running wide tires, which I imagine you will. I would guestimate 1.75 is close to stock Datsun ratio. If your goal is primarily a street car, you definitely want to do a lot of things differently than I did. Mine can be driven on the street obviously, but it's all pretty harsh and kind of kicks my ass after an hour or so. -
ANOTHER Datsun Z/LS3/T56 Swap Thread
Ironhead replied to Ironhead's topic in S30 Series - 240z, 260z, 280z
Thanks for the kind remarks. I am not the least bit disappointed that there were a few issues to sort out once the car was running. Truth be told, there were far fewer than I expected. Also, the car has never actually "broke down", nor has anything failed in a catastrophic sense that damaged other components. I have been driving the car a great deal and honestly it has been pretty reliable. Regarding your questions: I went with the tandem master cylinders w/o power boost so I could use a balance bar to adjust front/rear bias from the driver's seat. It also makes it very easy to swap out master cylinders for different sizes to get a perfect balance of effort and front/rear bias. I did have to experiment with master cylinder sizing, pedal ratio, and most importantly pad compounds, to have what I considered "good" pedal pressure and acceptable cold braking. I settled on very aggressive pads (Carbotech XP20) and absolutely love them...great cold bite...zero fade....etc. The only downside is major squealing when light/moderate braking, like is common in street driving. I can live with that...as this is mostly a track car. After the fiddling, the brakes on this car are fantastic...I wouldn't change a thing. Well, I would like to have had ABS, but the costs and complexity of installing a motorsport ABS system were insane...no way I was going to do that. The electric power steering is sorted. I started with a Datsun Z specific kit that used a stock Datsun steering column. That was the setup that I found gave erratic boost, and didn't really seem to respond to the rheostat knob adjustments. Also, the steering column bearings were shot, and the column would clunk whenever I changed steering direction. The PS motor that came with this kit was from some weird Renault I believe. I started from scratch and built a new EPS setup using the Saturn motor and a Woodward steering column. It took a bit of fab work, but it works perfectly now. It uses a rheostat knob to adjust the amount of boost. I would recommend ordering the slowest steering ratio that Woodward sells...I can't remember the specific ratio. I am using the shortened Apex Engineered knuckles, and between those two factors, the steering is pretty quick, much quicker than stock Datsun. It is also far too heavy to even consider using without some sort of power steering, although the 275 wide front tires are definitely a factor there. Ignore the steering ratio I said I was using in the thread...I believe that was the "medium" Woodward ratio, which I have since ditched for the slowest one. The medium ratio was completely drivable with the EPS, but I just found it disconcertingly quick. I didn't like it. It was go-cart like. -
I too used this kit: https://www.ebay.com/itm/322668159056 It worked well, no complaints. I can't help you with the roller detent pin. You might have no choice but to have one machined.
-
The Vintage Rubber front and rear windshield gaskets can (maybe) be made to work, but they are extremely difficult to install. At least they were on my car. After a huge struggle I got the rear one in place, but I can't even describe what an ordeal it was. In the front I wound up cracking the windshield trying to "persuade" the gasket into place. So I had professional installers come in from a place that specialized in vintage car window glass. They struggled with the gasket for over an hour and could not make it work. I finally gave in and had them use an OEM Nissan gasket ($$$) that I was going to sell because I figured I could use the Vintage Rubber gasket. The OEM one went in a breeze. I think the problem with the Vintage Rubber gaskets is just that they are slightly too stiff and the rubber is a bit too hard to work easily. I do realize, however that our choices are limited. I don't know what else to say though. I could not make the front one work nor could the pros.
-
I used Trackspec vents on my build, not exactly the ones you mentioned, but I think they are all pretty similar. I think they are great. No complaints at all.