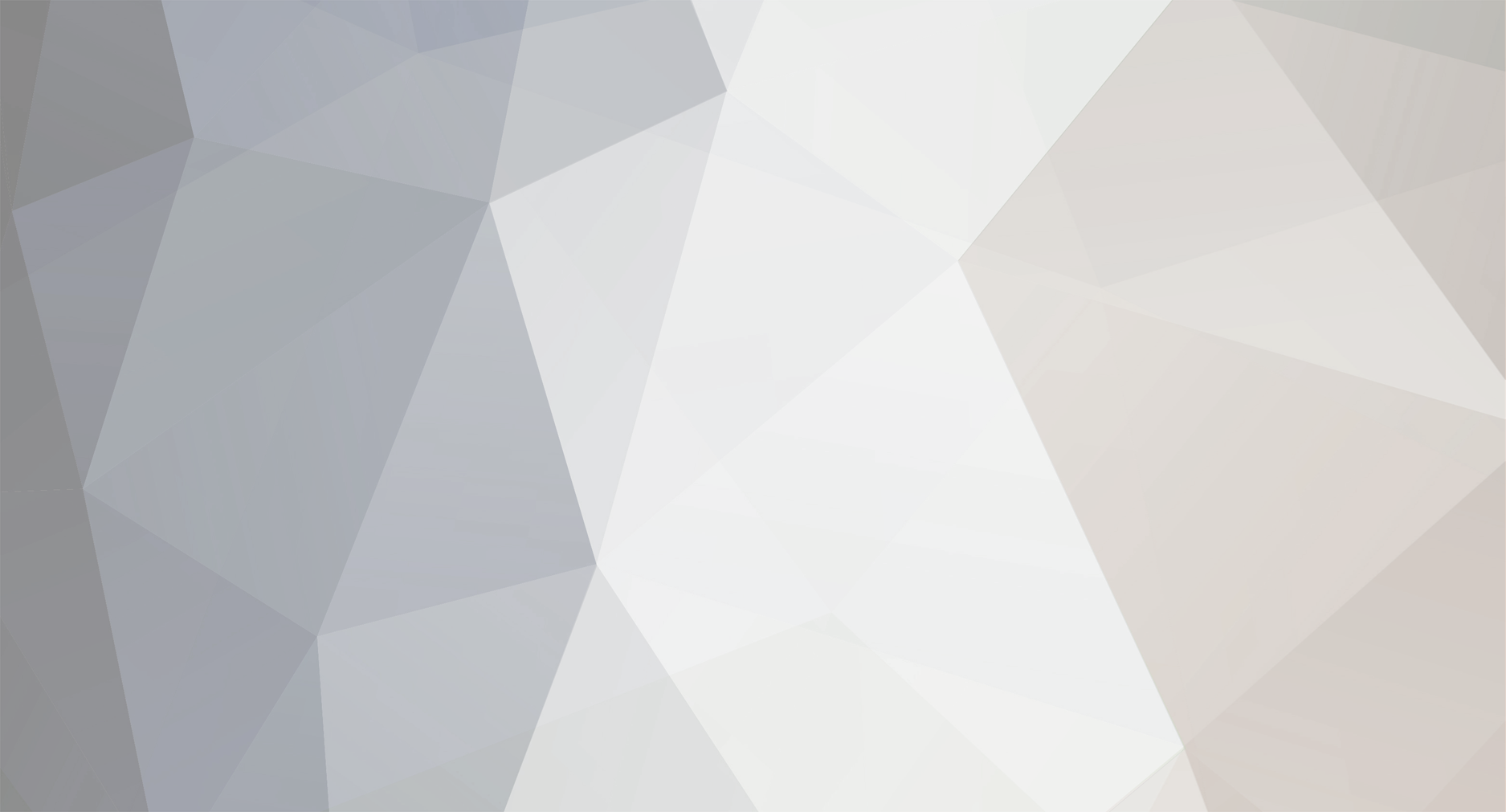
rsicard
Members-
Posts
889 -
Joined
-
Last visited
Content Type
Profiles
Forums
Blogs
Events
Gallery
Downloads
Store
Everything posted by rsicard
-
Power drain from Timing Chain / Valuable Build Tips herein...
rsicard replied to galderdi's topic in Nissan L6 Forum
TonyD: I don't see where there is a disconnect. If each of the journals of the Crankshaft and Main Bearings, with shells installed, is visually inspected and tested for concentricity and proper clearances, then when the two are assembled with proper lubrication there should be minimal level of friction. This can be quantified with an inch pound torque wrench. As for engine experience, I have owned three aircraft and rebuilt engines in two of them guided by a qualified A&P mechanic. Also renewed a Peugeot, Renault, Volvo (PRV) aluminum V6 under the guidance of an experienced mechanic. Rebuilt a BBC 454 now 489 cu in and in my truck and it runs VERY WELL. Rebuilt a 350 SBC for my 240Z bored and stroked to a 383. Used a tested baseline of 500 HP/TQ and exceeded every specification for same. Fabricated a test stand and both the 489 and 383 run in and tested on the stand. Both run just fine. The 383 has the most accurate and flexible EFI system installed ever made. As far as friction is concerned, see the article at: www.fev.com/ content/ public/ secure/ protecteddocs/ OptimizedCranktrainDesignSupportedbyCAE.pdf. -
ckrell: Where was the sway bar item sourced from. Would like to do the same. Please reply. Thanks.
-
Realistically, there is not way to quantify the torque value at which certain parts will break in the R200 diff. The probability of failure of the U-Joint halfshaft or the 27 spline stub axle are about equal. When using the Z31T CV half shafts and 27 spline stub axles, the stub axle will be the point of failure. I followed this several years ago and worked with the gentleman at Modern Motorsports to come up with a much stronger design for the stub axles. I must have been one of his first customers for those BEEFY stub axles which are now in my 240Z with Z31T CV halfshafts and 3.7 CLSD R200. Want to upgrade the R200 to OS Giken CLSD.
-
Power drain from Timing Chain / Valuable Build Tips herein...
rsicard replied to galderdi's topic in Nissan L6 Forum
An answer with emotion and not fact is not an intellectual answer. Art and Science are two different things. Art is tied more to emotion. Science is not. The best science is based on known and provable facts. -
Power drain from Timing Chain / Valuable Build Tips herein...
rsicard replied to galderdi's topic in Nissan L6 Forum
What PMC has said is all fine well and good. What I was getting at is the actual TESTING for position tolerance of the Main Bearings and inserts for same, in relation to each other, assembled and torqued less the Crankshaft. This same level of testing of the crankshaft to make CERTAIN that the circumference of each main bearing is in line, or concentric, with each other Main bearing. Then this SHOULD allow the least amount of friction once the Crankshaft is assembled into the Main Bearing Saddles along with the bearing inserts. Not certain whether this is "ART" seem more like "SCIENCE". Constructive comments invited. -
Power drain from Timing Chain / Valuable Build Tips herein...
rsicard replied to galderdi's topic in Nissan L6 Forum
PMC raceengines: Thanks much for the tips. It seems that the best way to do the fitting of the crankshaft and main bearings is to use a coordinate measuring machine (CMM) to map the exact tolerances of the main bearings and the crankshaft journals. Making certain that the crankshaft main journals are all exactly where they should be. Secondly, with the main bearings inserted and torqued down, use the CMM to see how exact ALL of the main bearings are where they are supposed to be. Even after the main bearing journals have been Line Honed, inserting and torquing the bearing shells, these shells could well be out of exact alignment. Swapping the bearing shells around may solve SOME of the out of alignment, but not all of it. Maybe if there were THREE sets of NEW bearing shells, then the best of the lot can be selected for use ONLY after careful torquing and measurement to get as EXACT alignment as possible. -
Power drain from Timing Chain / Valuable Build Tips herein...
rsicard replied to galderdi's topic in Nissan L6 Forum
Any techniques you can share to get the crankshaft and bearings for same to fit such that it will spin free once installed? Please advise. Thanks. -
Power drain from Timing Chain / Valuable Build Tips herein...
rsicard replied to galderdi's topic in Nissan L6 Forum
PMC raceengines: Good to hear you chime in. The statement "A short motor will tern by hand,, 14,lbs" does this mean 14 foot/pounds torque applied to turn the short block assembly over? Please reply. Thanks. -
Power drain from Timing Chain / Valuable Build Tips herein...
rsicard replied to galderdi's topic in Nissan L6 Forum
Tony D: Now my curiosity is peaked. Please expand on: "Some people are more meticulous than others. If your crank doesn't freewheel several revolutions in the mains once assembled before putting rods on---you need to go back and check more closely! Something isn't right.' Is this level of quality attainable? How many aftermarket engine machine shops achieve this level of quality? What kind of equipment and techniques does it take to achieve this result? I would like to achieve this level of quality in V8 engine rebuilds. Please advise. Thanks. -
Power drain from Timing Chain / Valuable Build Tips herein...
rsicard replied to galderdi's topic in Nissan L6 Forum
Tony D: How many engines, which have been aftermarket machined, have you assembled to specifications and found "will freewheel spin given a stout turn on the drive flange if you have a strong enough grip"? Just forget about an assembled LONG BLOCK. Just working with the short block wherein the only friction is the Crank Bearings and piston rings. What are the typical clearances for Crankshaft Main and Rod Bearings? -
Power drain from Timing Chain / Valuable Build Tips herein...
rsicard replied to galderdi's topic in Nissan L6 Forum
JohnC: With all due respect to your skills, Valve spring seat pressure should be a fraction of the total Piston Ring, Crankshaft Bearing, Camshaft Bearing and Oil Pump Friction. Assuming VERY round cylinder bores, loose forged pistons, less the rings, should have very little friction in a vertical bore engine. The Rings have the largest amount of friction in the engine even though they may be only two per cylinder and VERY thin. That would necessitate the use a a vacuum pump to evacuate the crankcase pressure. Without the metrics of actual measured friction in the short and long block assemblies, it is hard to determine actual friction levels. Crankshaft bearing clearances, not weight, have to do with overall engine friction. Same is true with the camshaft. -
Power drain from Timing Chain / Valuable Build Tips herein...
rsicard replied to galderdi's topic in Nissan L6 Forum
John: Explain how there can be SO LITTLE friction in a L6 engine that it could almost be turned over by HAND! That one is a BIT HARD TO SWALLOW. What is meant by a properly assembled engine? Please go into detail how friction was reduced to that level. Six Ring Packs, Crank Bearings, Cam Bearings, Oil Pump all contribute to friction. Also with a finished engine, upper end cylinder head valve springs, rocker arms, etc. also promote resistance to turning over. What was the measured value of friction by Sunbelt, of the short and long L6 engine? Would be nice to hear the reality of the engine build. -
1973 Datsun with the Lt-1 Swap
rsicard replied to King's Evil's topic in Gen I & II Chevy V8 Tech Board
Thanks for the answer on LE3 heads. Did not know about Lloyd Elliot. Compare what he wants for his head mods with new AFR heads for a LT-1/4. I really think that a LT-1 with AFR heads and 383 displacement is superior to anything else in this displacement bar none. The key to power is the cam/head/induction combination. With the 24lb injectors, an increase in fuel pressure should compensate just fine. -
1973 Datsun with the Lt-1 Swap
rsicard replied to King's Evil's topic in Gen I & II Chevy V8 Tech Board
Curious, what are lE3 heads? -
1973 Datsun with the Lt-1 Swap
rsicard replied to King's Evil's topic in Gen I & II Chevy V8 Tech Board
The leak-down tester will help tell what is leaking. The piston rings, intake, exhaust valve or head gasket. The cylinder head and block surfaces can be checked for straightness with a machinist straight edge. Once the valve job is done, a leak-down test can be performed to measure ring leakage. Clean block surfaces before reinstalling cylinder heads after reconditioning. Strongly suggest purchasing ARP cylinder head STUDS. Put Loctite sealer on stud threads and thread into block. Put ARP assembly lube on upper portion of cylinder head stud, washer and nut. Three stage progressive torque to spec in a circular pattern starting from the center and going outward. Then assemble the remainder. Run engine. Let it cool and perform cylinder leak-down test. -
Displacement for displacement, there is NO advantage in using a LSx or BBC. For even greater power numbers, a supercharger or turbocharger can be used on a SBC.
-
How to redo your LT1 wiring harness.
rsicard replied to dat240zg's topic in Gen I & II Chevy V8 Tech Board
A speed density EFI system DOES NOT USE a MAF sensor! -
After having rebuilt Chev Big Blocks and Small Blocks, the advantage of size and power goes to the small block. With equal spec/quality parts and displacement, the SBC and LSx provide the similar POWER output. The advantage the LSx engines have is that GM cast stock aluminum blocks. To obtain an aluminum SBC, one has to go to the aftermarket. The LSx engines have gone full circle and come back to the rectangular intake port for performance purposes rather than the Cathedral Port configuration. For its compact size, the SBC is hard to beat for HP and TQ. Aftermarket SBC blocks go beyond 454 cu in displacement in the same outward physical size. Add a supercharger or Turbo charger, and the SBC will out do the BBC.
-
How much power is actually needed?
rsicard replied to vega's topic in Gen I & II Chevy V8 Tech Board
Focus on the point of the post. -
How much power is actually needed?
rsicard replied to vega's topic in Gen I & II Chevy V8 Tech Board
The 240 and 280Z axles have a natural weak spot that shows up at higher HP/TQ numbers. The BEEFY stub axles cure this situation. -
There are a number of aspects that should be considered when using USED parts. If there is a goal to spin the 327 to 6500-7000 RPM, then it would seem prudent to do a magnetic particle inspection/test on the crankshaft and connecting rods. The unknown may be the number of hours and miles on the bottom end components. It is not the cylinder heads that determine what RPM the engine can be spun to. It is the strength, integrity and balance of the bottom end.
-
Still need more specifics about the 327. It likely has FLAT TAPPET lifters. That in itself is a limitation. The valve springs are another limitation. Going to 6500-7000 RPM is not necessary to make good power. It is most dependent on Cylinder Heads, Camshaft, Lifters, Pushrods, Valve Springs and induction system. The dangers are the flywheel/flexplate, front balancer, connecting rods being out of balance or TOO WEAK to handle the strain at those RPMs. Going safely to those RPMs takes a complete internally balanced FORGED bottom end components, good balancer and flywheel/flexplate along with aforementioned items.
-
The Bad Dog sub-frame rails front and rear to do not strengthen the torsional stiffness of the 240Z. I installed them on my 240Z and all they did was make the floors stronger. The sheet metal in the floors is so thin, that I did not weld the Bad Dog rails to the floor. I used 2 inch spacing and 10-32 screws and fender washers on the upper side and it made the FLOOR much more solid. Did nothing for torsional strength. The rocker boxes under the doors are one of the strongest parts of the 240Z. Welding a roll-cage to these channels helps with strength. Welding an "X" to the back of the roll bar back to the rear strut towers would yield torsional stiffness for the rear of the vehicle. Obtaining torsional stiffness for the front is more difficult. A six or eight point roll cage may add torsional strength to the front. The sure fire way to handle the engine torque is to put a welded torque tube from the rear diff to the transmission.
-
Dunlop: Some of the posts may be OVERBLOWN. Purchased KMJ block hugger headers and they fit just fine. I have AFR-195 heads and the exhaust ports are 1.5 inches rectangular. Much larger exhaust port than the opening in the KMJ headers. Sanderson recently cam out with CC-178 headers which are 1 7/8 inch in OUTSIDE diameter. Purchased these and they interfere with the steering shaft. Purchased shafts and U-joints to go around the headers. Got it all mocked up, then said if this is what it is going to take, might as well go to Subaru PS rack. In the early stages of doing that. Don't know the exhaust port configuration of your Dart heads. KMJ block hugger headers can be slightly ported to help the interface to the Dart heads.
-
Looks like a Marine engine. Before anything else, have the block checked for cracks and cylinder walls sonic tested for thickness. It's already .040 over on the bore. Even more reason to sonic test.