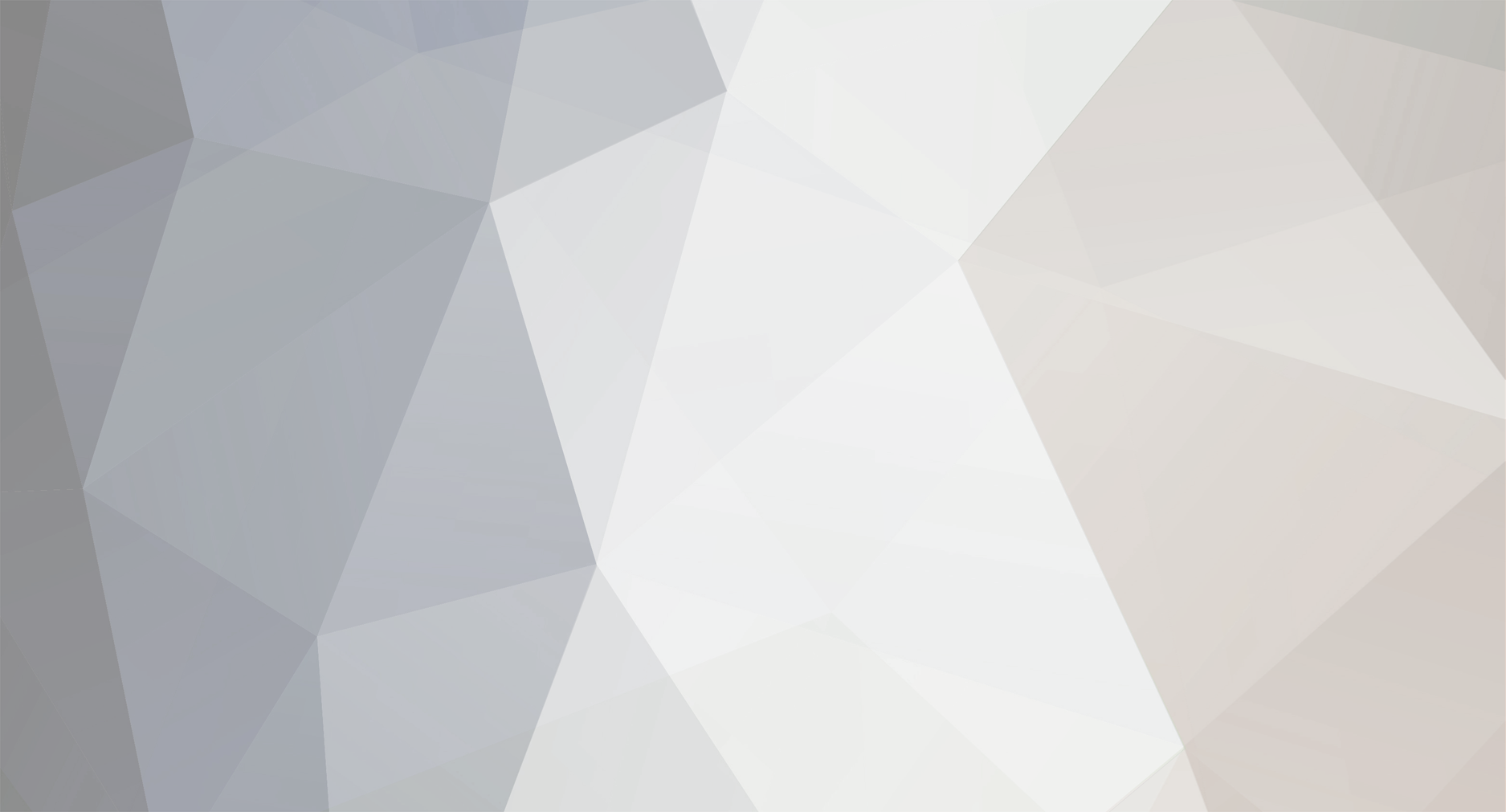
lbhsbZ
Members-
Posts
409 -
Joined
-
Last visited
-
Days Won
1
Content Type
Profiles
Forums
Blogs
Events
Gallery
Downloads
Store
Everything posted by lbhsbZ
-
Front 13" low buck brake kit....DONE!
lbhsbZ replied to lbhsbZ's topic in Brakes, Wheels, Suspension and Chassis
Ok, just measured things up. The rotor height is 2.29", and the hub thickness is 0.67", bringing the total hub face to back of rotor distance to 2.96". BUT, you used 280 hubs. From what I've read, the 300ZX hubs are offset another 3/4" outward....so my 2.96" is equal to your 2.21", provided that the thickness of the hubs is the same. Here's hoping. -
Front 13" low buck brake kit....DONE!
lbhsbZ replied to lbhsbZ's topic in Brakes, Wheels, Suspension and Chassis
Hmmm... good point. I kinda eyeballed it and it looked like it would clear fine. Didn't think about the bump steer spacers though. I'll have check it out tonight. Damn, I thought I had it for sure. Leave it to a ford guy to pee in my Koolaid -
Front 13" low buck brake kit....DONE!
lbhsbZ replied to lbhsbZ's topic in Brakes, Wheels, Suspension and Chassis
I can do the cobra calipers with brackets for about $150 each, brand new, but it will take me a couple weeks to get them. Pads are another $20 or so for street pads, and $60 for entry level track pads. I also have PFC and Hawk race friction. -
Front 13" low buck brake kit....DONE!
lbhsbZ replied to lbhsbZ's topic in Brakes, Wheels, Suspension and Chassis
If anyone else wants to do this, you can get all the parts from me. (I work for a brake parts manufacturer). I can get the rotors for less than 1/2 that price. -
Front 13" low buck brake kit....DONE!
lbhsbZ replied to lbhsbZ's topic in Brakes, Wheels, Suspension and Chassis
John, I'm familiar with backstepping, I did the welds in 3 sections on each side. I did the one end, then the other, then the center, flipping the parts and alternating sides between each weld. Every time I made weld on the front side, it pulled the bracket. I had to make a partial second pass on the backside to pull it back straight. Thats a good link though. Miller has some excellent information on thier website as well, as does Hobart. Every amature welder should read up on these sites....there is a lot of helpful information out there. -
Front 13" low buck brake kit....DONE!
lbhsbZ replied to lbhsbZ's topic in Brakes, Wheels, Suspension and Chassis
Rotors are 25mm thick...same as the Cobra rotors. The only difference is the offset and the vanes. The cobra rotors have directional vanes, the lincoln aviator rotors have radial vanes. But the aviator rotors have more vanes than the cobra rotors do. I plan on building some proper brake duct registers that will bolt onto the spindles, so I think I'll be able to keep cooling under control. I plan on this car going 160+ on the long straights in Tecate and Tijuana, which are very hard on brakes...we'll see. I'll put a parachute in the back just in case..LOL. -
Front 13" low buck brake kit....DONE!
lbhsbZ replied to lbhsbZ's topic in Brakes, Wheels, Suspension and Chassis
I don't think so, the rotors are 6mm thicker than the 4 runner vented rotors so they probably wouldn't fit inside the calipers. BUT, there's always the landcruiser calipers, which use a much thicker rotor. I don't have the thicknesses off the top of my head, but the problem you'd run into would be once the pads wear more than 60% or so, the only support would be from the pins, which would be bad. I'll check on monday, I've got another set of struts that I haven't cut up yet. -
I couldn't bring myself to buy Ross's $500 hubs and the rest of the stuff needed to do the cobra upgrade, and I'm in the brake business, so I picked up some 300ZX hubs, took some measurements, and hit the rotor spec sheets. I found one that is almost perfect. Almost perfect means that it doesn't need to go to a machine shop to make it fit, its readily available, relatively cheap, and all the dimensions are pretty close to perfect. I wanted something that I can go to the parts store and buy whatever replacement parts I needed. Here it is: The rotor is from a Lincoln Aviator. 13" diameter, and the pilot hole is about 0.5mm larger than the pilot on the back of the 300 ZX hub. No problem, I welded a small bead around the hub pilot and turned it down to perfect....I'll never have to touch it again. The only thing I had to do was redrill the 5 bolt pattern to mount the rotor to the hub. I used lug studs through the rotor holes and hub lug holes to center everything, then used a transfer punch to mark the new holes and drilled them with my battery drill (it wouldn't fit on my drill press). Now to make the caliper fit. I toyed with the idea of making a bolt on bracket, but the bracket would have to be pretty big because the existing caliper ears on the spindle interfered with the holes on the new caliper carrier. I would have had to position the caliper about 30 degrees farther up the rotor in order to have everything clear. A larger bracket wouldn't resist the twisting force of the caliper as well as a smaller bracket, so I opted to do it this way. I cut the ears off the spindle, then with lots of measuring and spacers at work, properly located the new bracket (3/8"x1.5" 1018 steel) and Tigged it on. I did some test samples on the welding with another strut I had and cut it up to verify proper penetration. this is about the thickest material I've ever had to make a structural weld on, so I did a few practice runs first to find the proper settings and technique. I was most happy with 180 amps on my little TA185 welder. One of the problems was distortion of the bracket after/during welding. The first weld didn't upset the alignment of everything. When I flipped it and made the second weld, the bracket pulled toward the second weld and hit the rotor. I ran a second pass over the first weld and it pulled the bracket back straight....this was a frustrating lesson to learn, but I'm glad I figured it out. I'd like to add gussets, but I'm scared that the welds will misalign my bracket again. I've got to talk to the engineers at work on monday before I go screwing it up again. My main hurdle with the brakes was making the pieces fit. I plan on using a chrysler aluminum 1 1/16 bore cylinder (same bore size as the cobra master) and also cobra rear calipers. I have an adjustable prop valve that I can use to limit pressure to the rears, but it shouldn't need too much limiting, as the rear rotor will be slightly smaller than the cobra rear rotor. How'd I do?
-
http://losangeles.craigslist.org/lac/pts/278374557.html Found this trans for sale on craigslist, A good price for anyone in central california Damn, and I just ordered my TKO600 today.
-
strut tower bar question......
lbhsbZ replied to FJ 280z's topic in Brakes, Wheels, Suspension and Chassis
We could run a string tight between the two rear strut towers (or the front if you want to drive around with the hood off) and have your passenger watch the string as you run the car through some hard corners. That would at least give us an idea of how much movement we are trying to stop. I'd do it, I can't push my car around corners fast enough to flex the body.....have to wait till I get the motor back together. -
Google Megasquirt and see what you come up with. Its available as a kit or prebuilt ECM, and its pretty user friendly and the limits to what it can do are almost endless. I've got an assmebled V2.2 ECM and wiring harness, all brand new for sale (cheap) if you're interested.
-
I ran that same package on a 350 with flat top pistons in a 3600lb chevelle with a stock converter. The cam didn't come on until about 4000rpms. I was really unhappy with it. In a lighter car with a stick shift, it would probably be a lot more fun though. The holley heads are supposedly the same as the brodix track1 heads....an entry level aluminum head, along the lines of the edelbrock performer. The heads are good for about 450hp in stock trim. If you are running it with an automatic, run a higher stall converter and you'll probably be fine with the cam that came with the package.
-
Possible steering rack u-joint source -Woodward
lbhsbZ replied to preith's topic in Brakes, Wheels, Suspension and Chassis
I've got an old rack out of 240. Give me the address and I'll tear it apart tonight and send the piece off. -
strut tower bar question......
lbhsbZ replied to FJ 280z's topic in Brakes, Wheels, Suspension and Chassis
::scratches head:: -
strut tower bar question......
lbhsbZ replied to FJ 280z's topic in Brakes, Wheels, Suspension and Chassis
Sorry BJ, I should have been more clear. I wasn't asking if we'd be able to do it to fit into the rules, I was asking if it would work and be halfway functional. I understand the characteristics of a straight piece of tubing with respect to compression and tension loads, but where is the limit? I'd still like to know how to calculate the yield load for a given tube under compression. Hell, If I can get away with using 1/16 wall 1 1/4 inch aluminum tubing for all my bolt in stiffening members that don't require bends, that seems like the way to go to save weight. -
Welcome to the board....I'm kind of a newb myself. Do yourself a favor and use the search feature. If a part exists, theres a good possibility that someone has already tried to bolt it to a Z...and made a post as to whether or not it worked. There is an astonishing wealth of information on this site already, you just gotta search for it.
-
strut tower bar question......
lbhsbZ replied to FJ 280z's topic in Brakes, Wheels, Suspension and Chassis
OK, Now that I think about it a little harder, that makes sense. A straight bar (with no bends) would not, under normal conditions, be loaded in such a way that it would bow in the middle. A bar WITH bends in it would. I have a question that maybe one of you can answer. I'll try to be as clear as I can but I'm not sure of the proper terms for this. A curved bar would be loaded so that it would bow, but a straight bar would be loaded so that it would crush should those loads become great enough (which they won't in a strut bar application). Is there a middle ground between crushing and remaining straight....kind of like the plastic state that aluminum goes into right before it melts? Or will the bar simply remain perfectly straight until it reaches its yield strength and then collapse? How would one calculate the yield strength of bars loaded in this manner? Since it wouldn't have the tendency to bow, then does that enable us to use extremely thin wall (light weight) tubing for the strut bar and other non-sanctioned chassis stiffening members loaded in this same fashion? -
strut tower bar question......
lbhsbZ replied to FJ 280z's topic in Brakes, Wheels, Suspension and Chassis
If the suspension components move, then heim joints are required. Look at it this way. If you have your strut bar mounted with hiems, grab the middle of it and bow the bar. When you do this, you can watch the heim joints move. The angle between the bar and the strut tower will change when the bar is bowed, and the heim joints don't resist the angle change. I think that with a solid mounting plate welded to the bar and welded bolted to the strut tower, it would resist the angle change more than a heim joint, and the therefor resist flexing or bowing the bar. -
I thought I'd post this here since this is the only group that it applies to. I sold one of my other trucks and have a little money now, so I want to step up to TKO600 gearbox....If I can sell the T5. It should be fine for mild (under 400hp) small blocks, but my sights are set a little higher than that. I'd like to get $550 shipped (in the US) for it. It appears to have been rebuilt, becuase the tag is missing and there is silicone sealer (non OEM) between the seems.
-
strut tower bar question......
lbhsbZ replied to FJ 280z's topic in Brakes, Wheels, Suspension and Chassis
I'm just unclear as to why anyone would use heim joints to mount anything that isn't supposed to move. Heim joints are low speed bearings for stuff that moves. If a bar is mounted with heim joints on each end, I think it would make the bar less resistant to bowing under load than if a non-pivoting type mount were employed. -
I was going to say the same thing about the duct tape bandages...lol I made an aluminum dash for my GTI race car a while back, swirl polished it. It looked bitchin' in the garage, but as soon as I pulled it outside into the sun, I couldnt' see a damn thing out the windshield...like staring into a spotlight. I shot it flat black and the problem was solved. If you cover it with alcantra, it will look nice and you won't have the glare.
-
Its not the best idea to make a structural weld to cast iron using typical methods. You can braze to cast iron or weld using a high nickel rod. Standard mig wire will make the parts stick together, but cracking is usually a problem. One way to tell weather it is cast iron or cast steel is to go at it with a drill bit. Steel will give you nice ribbons off the bit, iron will give you small chips and dust. Check out the Hobart Welding website forum and do a search for CAST IRON. there is tons of info there. If you must weld cast iron, preheating and slowcooling is a must.
-
How to center a 3 jaw: If the chuck itself is not acurate, clamp something in it to secure the jaws, and cut them true with either a boring bar (inside jaws) or tool bit (outside jaws). Generally, my chinese 3" 3 jaw clamps work perfectly, with no radial runout. I also have a chinese bandsaw that couldn't cut straight if my life depended on it, so if I chuck up something that I've cut on the bandsaw and measure runout an inch or so away from the chuck, its all over the place. Just get a dial indicator and small mallet and tap tap tap until you can measure runout in 2 places on your piece of stock and come up with 0. I through a hub on my 7x12 the other night to try to make it fit in a cobra rotor, and measured runout on the hub face as well as the radial runout. It took all of 2 minutes to get everything to 0. 4 jaw chucks are a pain in the ass. Maybe I'm just slow, but I usually spend at least 10 minutes or so trying to get something straight in a 4 jaw. I only use it for cutting odd shaped stock or offset holes. The 3 jaw gets used for everything else.
-
building a dream or wasting your cash?
lbhsbZ replied to grumpyvette's topic in Gen I & II Chevy V8 Tech Board
For me, most of the fun is building it. I've built 2 racecars and 1 t-bucket roadster in the past. The T-bucket went from cradle to grave in one month flat, then I ran out of money so threw a bean bag chair in the bucket and that was my seat for the next 6 months. I also did a VW rabbit stock class car and a MK2 VW GTI open class road racer. Here is what the GTI tought me. #1. Patience is everything, it can make or break a project and your pocketbook. (I have no patience) #2. If you can afford the best parts, buy them the first time. If you buy substandard or "good enough" parts the first time around, you will eventually upgrade a couple of times until you get to the best stuff in the long run, and you will have ended up paying for 1 or 2 sets of lesser parts and one set of top shelf parts in the long run. Buying the best in the beginning saves you money, but requires patience if you're not a rich man. See #1 #3: Don't make compromises due to supplier screw ups, parts availability, or tooling limitations. If you don't have the tools to make the parts you want, spend the money and buy them. They will prove to be invaluable to you through many other projects. If you pay for the parts you want, make sure that the suppliers ship you the parts you want. I've sent back over a couple grand worth of parts for the Z project because suppliers were trying to be cheap. #4: If money is an issue (which it is with me), don't count out used parts. With enought patience (see #1) almost everything you could ever want can be found used, at deeply discounted prices. I found a set of custom made long tube 1 7/8" headers, ceramic coated, for the JTR setup on ebay about a month ago for $200....and they fit too!!. A dream car to me is something that I built. Something that when you peak under the hood or peek inside, all you see is a bunch of slick ideas that you carried out. I usually get tired of stuff after a year or too....just about when I get it the point when its nice and reliable, and finished. If I can't work on it, I get bored...at which point its a big hunk of parts sitting in the garage collecting dust. Time to move on to another dream build..... -
strut tower bar question......
lbhsbZ replied to FJ 280z's topic in Brakes, Wheels, Suspension and Chassis
I'm saying that for the removable bars, make them bolt using at least 2 of the strut hat bolts on each side, Not a clevis or hiem joint. Weld a round plate to the brace, then bolt that 2 the strut tower. I think that would be a stiffer design than using a single attatchment point on each side.