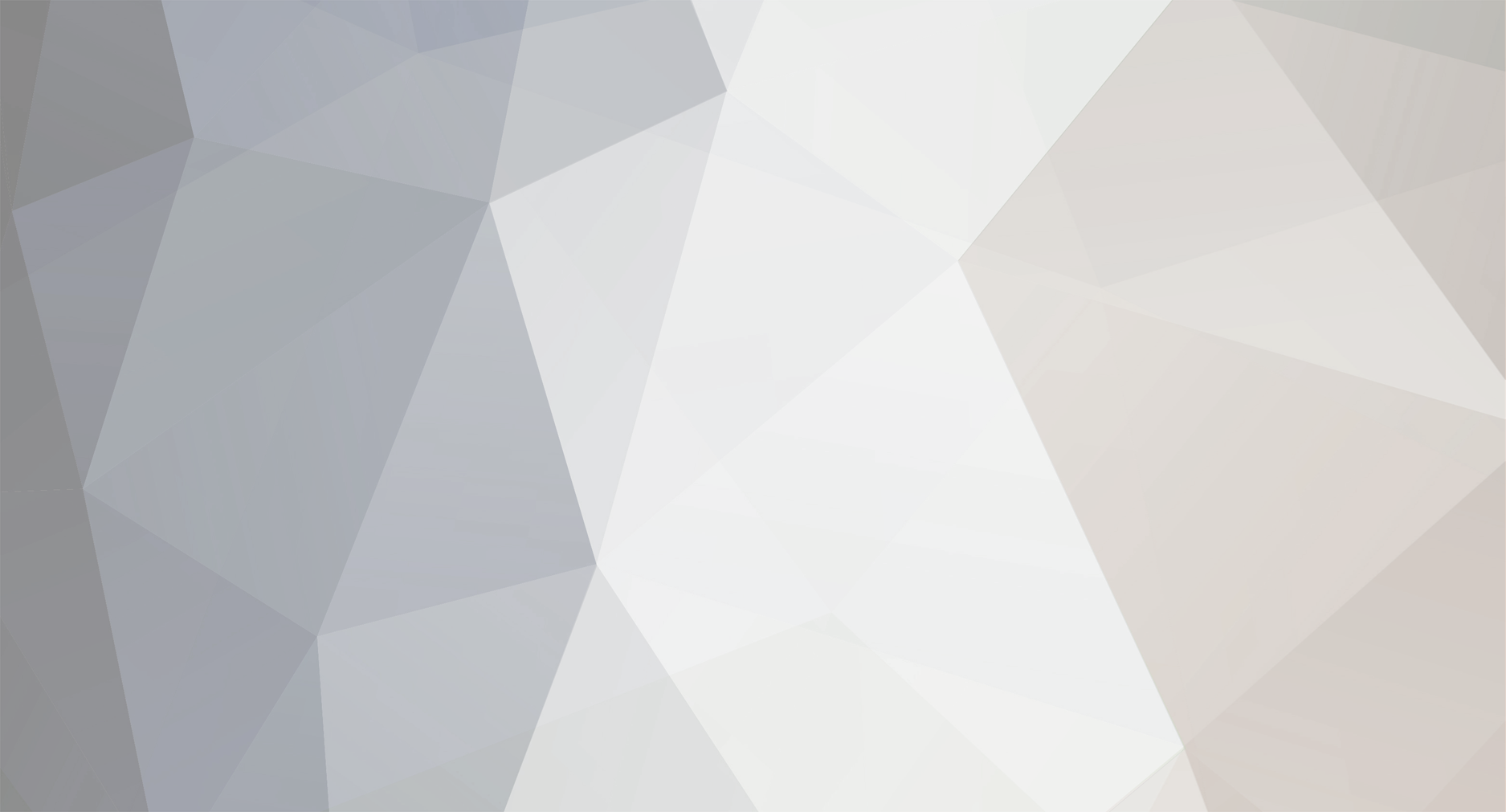
lbhsbZ
Members-
Posts
409 -
Joined
-
Last visited
-
Days Won
1
Content Type
Profiles
Forums
Blogs
Events
Gallery
Downloads
Store
Everything posted by lbhsbZ
-
I've got an R200 w/ a OBX cheeze diff. If I don't have time to get that in, I'll weld the R180 and hope for the best.
-
Well, not much progress made today either, but I gathered up more parts. JohnC at BetaMotorsports went out of his way to get me a set of EMI camber plates in less than 24 hours. I picked those up today, and also picked up my driveshaft. $300 for a custom driveshaft with a C6 front yoke and rear datsun flange that uses a GM u-joint. Not a bad deal. The guy built it for me in less than 24 hours, I ordered it yesterday at noon and picked it up this morning at 9. I got the front suspension together, but now I'm waiting/trying to find a set of 2" wheel spacers for the rear so I can bolt on my 17x10.5s with 315/35/17 rubber. The 17x9 with 295s cleared by 1/2" in the front without spacers, I was amazed.
-
That sounds like a good idea...thanks john
-
I'm done for the day. Got the plug wires cut and fitted, made brackets for the griffin radiator and installed it, mounted up the oil cooler, and ran a little more wiring. Lots of running around tomorrow, I'll post more pics tomorrow night.
-
Whatever happens, the slave cylinders needs to push the throw out bearing TOWARDS the engine. figure out how your fork is setup and get the appropriate cylinder. Some ford gearboxes use a push type setup.
-
Does anyone have any insight as to whether the header wrap and plug wire wrap will keep the wires cool enough to not melt? It'd be a real pain in the ass to do all this if I'm gonna have to find different headers or straight plug heads
-
I'm a little behind schedule...couldnt' find anyone to help push the car into the garage yesterday (sloped driveway). Its 2:00 sun. and the motor and trans are in, new trans mount fabbed up, wiring almost done. Some shots from yesterday My quicky alternator bracket And it's in I only had to cut the shifter hole about 3 inches for the TKO600 gearbox And here's a shot of the dash, but that was done last week. Taking a beer break now, its hot outside. 12 days left
-
I've got a buddy with bone stock, clean, rust free 71 240 in SoCal that he'll take $3000 for. I've also got a spare SBC motor, which is no punk, a T-5 trans, and pretty much everything you need make it work. If you're interested, hit me up.
-
My Dipshit coworker and competitor has bet me a single dollar than I can't make the car run and keep it running through at least 1 practice session for the race weekend of the 18th/19th of this month. His dollar is worth a million to me. I think I can make it happen. The car's current condition: Caged body with 20 year old unknown "performance suspension" under it with stock brakes, no motor/trans, interior is cleaned up, pilot seat installed, primer paint job (soon to be camo primer paint job). After many speedbumps, I finally got a motor together, not exactly what I wanted, but I figure 600HP is enough for a 2200lb road race car. I just finished up the strut sectioning/front brake bracket gussets tonight, sealed up the motor, aligned the bellhousing and bolted the TKO600 on it. It will go in the car in morning. The springs just showed up today from H&R, I'll use the threaded perches off my VW, and I've got all the parts to put the whole thing together. Wish me luck. Here's the official thread: http://roadrace-autox.com/bbs/forums/thread-view.asp?tid=3809&posts=23#M79740
-
Should've said something...I've got a fresh scat 9000 crank I'd sell you for $150. Its funny how the stock cranks are softer than the thrust bearings. I was tearing down a core with 40K on it (documented) and as I was rolling it around I heard clunks....1/4 inch of crank endplay, bearings looked perfect, crank was toast.
-
I hope its OK to post this here because Its not car parts... I just bought a 10x24 Atlas so I'm selling my little mini-lathe. Its a Cummins 7x12, similar to the Harbor freight mini-lathe but a couple inches longer. The biggest thing you can fit on it is a 5 lug 300ZX hub. I build a spherical bearing suspension setup for my old GTI on it, made numerous spacers, fittings, couplers, pretty much anything. It doesn't take up too much space, and comes in handy all the time. Here's a picture: It comes with digital readouts for the cross-slide and compound, a 4" 4 jaw chuck for holding square or odd shaped stock, a 3" 3 jaw chuck, a Quick Change tool post, tailstock, steady rest, carriage rest, a bunch of spare gears, parts, and a little bit of tooling. These machines have tons of support. Every replacement part and accesory imaginable is available through littlemachineshop.com There are yahoo groups and several other websites dedicated to these little lathes. They require a bit more attention than a big boy lathe, but its easy. I'd like to get $450 for the whole package, as I have about $700 invested in it. I'm located in LA.
-
This weekend was productive. I stuffed a set of .040 pistons into a fresh .044 over block that I had, and the shortblock went together without a hitch. I didn't feel like putting the Dart heads back together, so I bolted a brodix head down with no gasket to see if the thing would turn. The pistons just touched the head, but it turned. No problem....I spent about 2 hours grinding and CC'ing until I was pretty damn close to 66cc in all 8 chambers...and I then dropped my burret tube and broke it, so I decided I was close enough. The last measurement had be within .4cc on all 8 chambers. I stuffed the cam in....and amazingly enought, the valves don't hit the pistons either. Even at .675 lift, I've got .115 clearance between the valves and pistons...with no headgasket. So I did the final assembly of the long block, I need to find some 3/8" x 8.000 pushrods tomorrow, then we'll be done with motor. WOOHOO...finally. I figure the guideplates will test my patience, but I can deal with that.
-
If he wants 3K for it, its probably worth 1K. After you check it out and if the cancer isn't too bad, and it runs decent, I'd offer him $1500. These cars have a special following, they're not the easiest thing to sell...I'd bet he'll take it.
-
Every engine makes pressure in the crankcase, regardless of the condition....worn out ones make more pressure. When I build motors, I always put the rings in dry....and they generally seat within about 5 minutes of running the engine. I always have to make some type of baffle for the breathers, if one isn't already in place.
-
The oil out the breather problem has bothered me in the past. Usually with LOGO valve covers, on one side the breather is in the front, and the other side the rear. The rear one always drips. I try to get plain covers and put both breathers forward, which definately helps, but you've alread tried that. They sell grommets with no holes in them. It looks like a rubber cup. Go get one of those, but instead of cutting the bottom off of it, just take a razor blade and put a few X slits in the bottom of it. It will allow gas pressure through, but little or no oil. This is the only thing that seems to work, short of venting it into a catch can or the header collectors.
-
I've been running into lots of problems getting the engine together, so I won't have mine in and running for another....who knows. I will post an update when I try it out. Does anyone have a set of R200 gears for sale? I've got a 3.50s, but I'd like something a little shorter, like a 3.90 or so.
-
I have a set of billet stub axles that I'll sell you for what they cost me. I need them, but not for at least another 2 weeks. If you are in a rush, I can get mine out tomorrow for you, and you can have them wed. I have to figure out what they cost and I'll have ross make me another set. If you're interested, give me a call. 310-947-7014 -Pat
-
I've gotten a little closer with owner of machine shop #2. Every tuesday night is a late night at the shop, and a few guys (and myself) show up with beer and pizza and we shoot the $hit till about midnight. I've been working on him, and he actually went out and bought a couple torque plates....and I saw a block being bored with the main caps torqued the other day when I walked in at lunch time to pick up some bearings. He's coming around. I brought him another block (I have a mild street motor to build for a buddies camaro) and he said he'd have his guy stay late on tuesday night so I could watch everything as it was being done, and make sure it's done my way. Thats what I'm talking about. He actually came onto this site and found the post that grumpy made (I think its on about page 106 of this forum) about torque plates....and showed me one night when we were at the shop. At least he looks like he's trying. He'll probably read this too. As far as the Brodix repair work, thanks for the heads up. I'll be sure to request a final quote before any work is done. And about luck, I have none. Even after all this, I tried to do a favor for this old navy man I know who has a '47 Willys navy jeep. It started off as a carb adjust, then turned into rebuilding his starter....then the alternator, then finding and replacing the fuel pump....at which point I noticed the bungee cord holding his brake pedal up....crawl underneith and set my head down in big puddle of brake fluid. I'm in the brake business, talked the boss into giving me a master cylinder, no problem. then the head gasket went....all within about 2 weeks. He wanted to get the radiator rodded out too. So I bring the radiator to the shop, they pressurize it and the core starts leaking. $300 later the radiator is re-cored and ready to go. I magged the head and checked with a straight edge to make sure it wasn't warped, and did the same with the block surface (straight edged, not magged) So tonight I chase all the holes in the block, installed all new headstuds, new gasket, head, and begin torquing the nuts down. The last 3 in the sequence pulled the threads out of the block. Now I get to buy another headgasket for the guy, yank the head, helicoil the block, and do it all over again. Why should I have expected any less. Buts he's a vet, so I'll do what it takes to fix his jeep. Its a pro-bono job too. Even those go crappy.
-
Today I did just that....called up Brodix and asked what they would charge to fix the chambers, I figured they had the fixtures and the NC programs already to do it. They said they'd have to do it by hand, for $375....I about fell out of my chair. That is remarkably cheap for that kind of labor in the performance world, especially from a big player like Brodix. Needless to say, the heads are boxed up and ready to go out. Now, another update on the motor. I ended up taking the shortblock back apart to get the crank out so I could use it on my other engine (that is also in pieces), and decided to further investigate a couple things that were bothering me about this one. As some of you may recall from the thread I started about machine shops, the work on this block was done by Speed-o-motive in West Covina CA. I paid $740 in the end for them to clean, mag, blueprint (line bore and hone, deck, cylinder bore and hone, and make sure the block was perfectly square), purchase main studs (for use during line boring and honing), and installing freeze and galley plugs. This was about twice what my local shop charged, but after seeing their shop and seeing the employees paying great attention to detail (seemingly) for the short time I was there, I figured it was worth the extra cash. I was a little disturbed when I received the block back from them with the main caps and stock bolts in a box, and the ARP studs still sealed in the ARP box. Maybe they had another set of studs that they used for all their machine work. I also noticed, after I had most of it together, that they didn't thread the oil galley holes behind the cam gear, but used freeze plugs instead....and didn't even stake them in. I took them out, and it was easy. 10psi of oil pressure would have blown them out of the block. I also paid an extra $40 for Speed-o-motive to glyptol the lifter valley and timing chain area....they gave me more than I paid for, there were drips of cured glyptol (hard as a rock) running down all the lifter bores, which I didn't notice until after the shortblock was built. The engine is back at Speed-o-motive, and while I was there, I had them measure the mains with the studs installed and torqued properly......they were out, not enough to stop the crank from turning, but enough to make me pissed off for having paid them what I did. I imagine that since the studs changed the main alignment, they also changed the bore shape. I'm not sure how they plan to fix the main line bore while keeping it square to the deck and cylinder bores, but we'll see. I'm also not sure how they plan on straightening up the cylinder bores without making then too big, but we'll see. I have enough room for another .0005" on the cylinder bores. Maybe machine shops constantly get away with work like this simply because the customers see a nice shiny crosshatch in the cylinders and a freshly cut deck and are satisfied....nobody checks or questions their work. Anyway, I'm getting to the point where I don't really care weather its perfect or not because I don't think I will ever have a perfectly machined block. I just want to put a motor in the car and have it run. I'm running out of time, money, and patience. The race season starts in less than a month, and I haven't even started on the suspension or electrical.
-
Oil Filter Bypass block-off???
lbhsbZ replied to Zerrari GTO's topic in Gen I & II Chevy V8 Tech Board
Its pretty common with performance engines. Jegs, Speedway, Summit, and all the other speed shops sell a little plug to replace the bypass valve, and also sell a different oil filter adaptor w/o the bypass valve. -
There's another guy on ebay that sells SFI rated steel flywheel for about $80. They weigh in at 18lbs IIRC. The stock flywheels are closer to 35lbs
-
He ran flat tops, but I wanted more compression than 9.5:1.
-
I'll take some pictures in the next day or so showing the interference. It not a simple "take a little bit off right there" kinda fix.
-
I'm sure a bunch of teenagers showing up in Turbo or V8 Z cars would go off real well.
-
Well, the heads are Brodix X11s with a lot of port work done on them, I bought them used from a small sportman level nascar team....I have other heads, but not like these. It would cost me $2500 to replace these heads. I'm thinking that I might just park this motor in the corner and put together what was going to be the "spare". Then when I regain some level of patience, spend the time to carefully reshape the chambers and assemble the engine. Grumpy, the crank stops turning with the pistons about 1/4 inch from TDC, which means that I have to remove a considerable amount of material for it to clear, and then a little more to make for safe clearance. I haven't even put a spark plug in yet to see if that will work. I'll have to make a pattern of the dome shape on the piston, and reference off of a couple of head bolt holes, then blue the head, and scribe the pattern into the head surface....after the rough cuts, I'll have to polish it until they all CC the same. This will be a project I think. My machine shop has offered to do it...says it will take "a couple of hours", but for some reason, I don't think that they would put the same level of care into it that I will. Damn, I hate pulling unfinished engines off the stand...its kind of like pushing the car OUT of the garage....defeat.