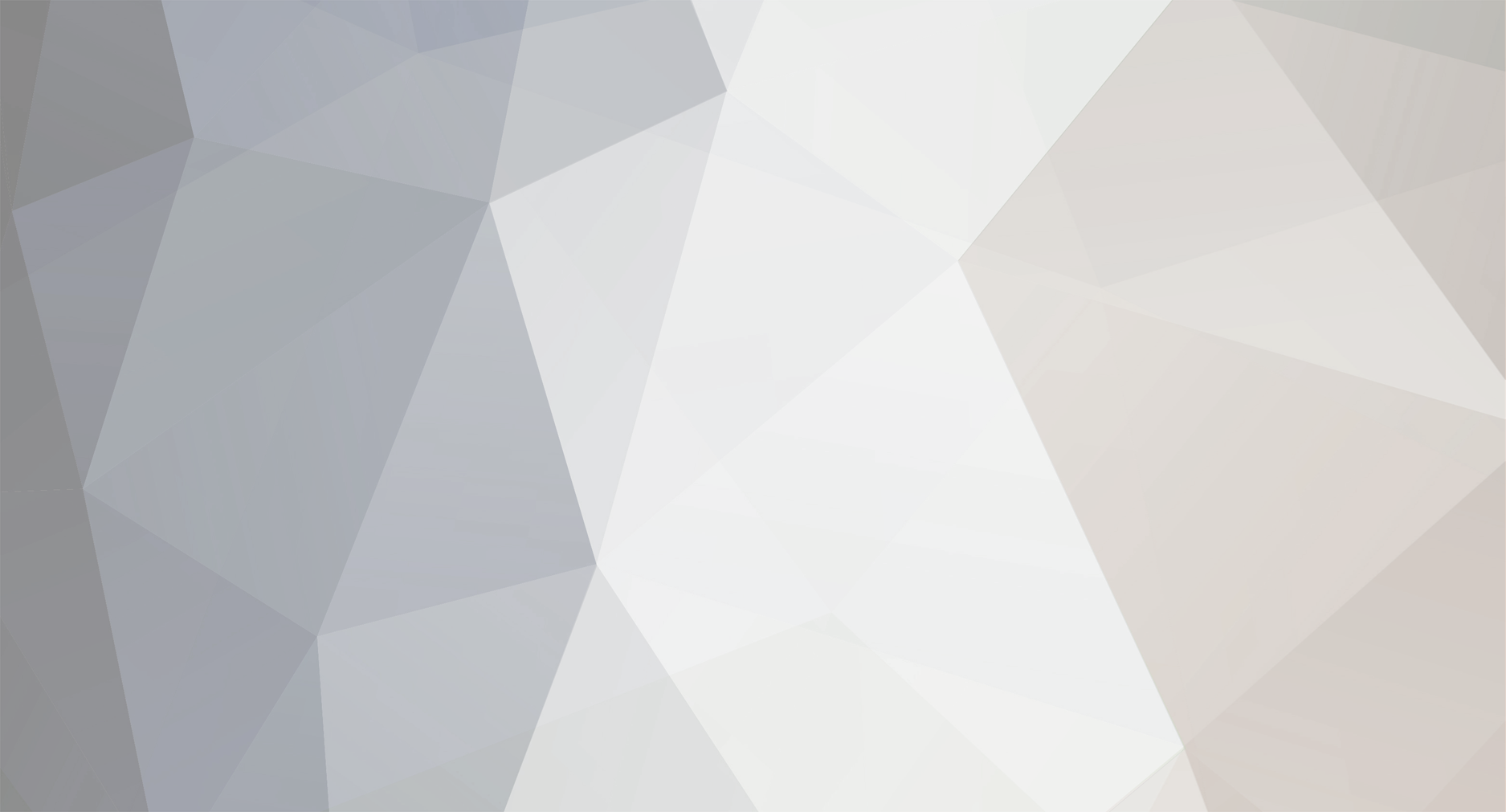
lbhsbZ
Members-
Posts
409 -
Joined
-
Last visited
-
Days Won
1
Content Type
Profiles
Forums
Blogs
Events
Gallery
Downloads
Store
Everything posted by lbhsbZ
-
Look at the first two pictures
-
Cage is done. Some of the welds look like crap...I'd like to blame that on the fact that this was the first cage I made from scratch, and I didn't do so good clocking the notches correctly, so I had some gaps to fill. If that excuse doesn't fly...then I just need more practice welding upside down with my head stuck between tubes. I screwed up a couple tubes, made a bend a little off or in the wrong spot, but was able to salvage all but about 8 feet of tubing. The total project consumed about 70 ft I think, maybe a little less. It was a learning experience, and I now know that I need to get the whole cage welded together while I can still move it around a bit in the car, and mount it to the boxes last.
-
help finding struts/shocks 280z
lbhsbZ replied to gretchen/jason's topic in Brakes, Wheels, Suspension and Chassis
Call Tokico...they should warrantee them. If the don't, call me 310-947-7014. I have a buddy over at tokico that takes care of me on stuff like this. -
Rasing Strut towers?
lbhsbZ replied to JustinOlson's topic in Brakes, Wheels, Suspension and Chassis
or lower the car and use the stock strut -
I agree with you 100%. I said that to illustrate that I had my little machine running as wide open as it gets, which in my case had the feed knob set at about 7/10 or so. The 135 class machines are great, and will do well on almost anything automotive. I just have a little more sense of security doing it with a larger unit thats not running at full tilt. My 110 circuit in the garage isn't all that great, and the welder sometimes pops the breaker. This was the one of the reasons I wanted to step up, because I have a 40 amp 220 outlet.
-
The wire feed mechanism was somehow shorting to hot and caught fire. Dunno what happened. I run my 200 amp Tig off the same outlet wide open and never had any problems...i would think there is enough power to run a 130 amp mig. Anyway, screw Miller. I'll take it back tomorrow and get my $900 back. I just got back from Home Depot and picked up a Lincoln SP175...basically the same thing. My little lincoln has been great. I've never had any issues with it in the 3 years that I've owned it. I'll stick with Red. I layed down a couple beads with the SP175 just now and WOW....nice and clean, no spatter, no sparks in my hair. I've been talking to all my welder buddies trying to figure out why the new Miller spattered so bad....they said thats the way it is with the larger machines. Hmm, the lincoln doesn't spatter. They told me to turn it down a bit. Something was wrong with it from the start I think. Anyway, back to the grindstone tomorrow. Beer time now. I ground into a couple of the welds that I made with the miller, and there are a couple small voids in them and some porosities. I'm gonna grind out all the welds and redo them with the new machine this weekend, then I'll try to roll the car out in the driveway and get some pictures of the rest of the cage and the mounting points.
-
Well, I'm minus one new toy. My brand new $800 miller caught on fire tonight while I was welding.....and I just sold my old Lincoln today. I'm welderless so the cage won't be finished tomorrow as planned. dammit
-
Search "Tubing Bender" on ebay, there is a guy that sells plans to make your own frame, using a Harbor Freight ram and the Protools dies (Pro-tools.com), Or if you call up protools and order a set of dies for around $200, they will GIVE you a set of plans to make a bender frame similar to the Speedway motors unit. I read this thread, and a bunch more, and ordered up the Pro-Tools 105 bender with a 1 1/2" Die. 3 minutes for a ninety degree bend. I made a base to mount it in my receiver hitch on my truck, and it works great. The only thing I'd like to change is to make it a vertical and add an air/hydraulic ram instead of my arm as the power source. It gets tiring after making 5 or so bends in a row. In my opinion, it was money well spent. Sometimes if you just bite the bullet and buy the proper tools, it comes out cheaper in the end. How much money is your time spent jacking around with a HF bender and a stack of kinked, worthless tubing worth?
-
Just run the old coil wire to the MSD, and the MSD output to the Distributor.
-
You're in luck. I've got a set of small block heads and a Camaro WC T5 for sale. Then you can go get your buddy's shortblock and you're all set.
-
Give me about another month. My garage isn't lit very well, so its hard for me to get anything substantial done after work during the week. I'm kinda limited to weekends for the welding and bending. I'll have mine done in a month or so.
-
Dunno about smart....my wallet is quite a bit lighter though
-
I show 4 different boosters for the 240/260/280z . Give me a call at the number above, and I'll figure out which one you need. I've got 2 or 3 of them in stock, but if I don't have the one you need I can rebuild yours. I can ship it back out 2 days after I receive it.
-
I hate it when this happens. I bought a roll cage kit from a reputable vendor, and it did't fit very well, so I got all pissed off and bought a bender from Pro-Tools.....the protools 105, even paid extra for the heavy duty model. Now I can bend my own cage up, and make it right. Then after making a couple of test welds (I always make test welds, try to destroy them, and cut a couple up to check for proper penetration) I noticed that my trusty little lincoln SP135 wasn't really up to par for cage work...even with its nipples twisted (both knobs turned till they don't turn any more). So being the impatient type that I am, I headed down to praxair and picked up a new Millermatic 180. OH yeah, and I also bought 100 feet of DOM tubing for the project as well ( I figure 30 feet or so will be consumed by the learning curve of the bender and notcher). So, I've got a new welder and a new tubing bender and a new notcher....Now I can make it fit right. I think I did pretty good. There is about a 1" gap between the main hoop and the sheet metal, and less than a 1 finger gap between the front tube and the A-pillar, on both sides. The main hoop is hard up against the roof and the body seam by the hatch hinges, so I'm going to stitch weld the hoop in to the body seam. The top windshield bar is also touching the body seam along the top of the windshield, so that will get stitched in too. I cut some plates to take up the gap between the A-pillars and the cage to tie in. I mounted the cage on little boxes..the main hoop boxes tie into the floor, fender well, and rockers, while the front tube boxes tie into the floor, rocker, and kick panels. I tacked everything in place, then knocked out the boxes and lowered the cage about 3 inches to weld the top, then welded the boxes back in and finished welding all the joints. The door bars will be the project for next weekend. I am doing Nascar style door bars that tie into the rockers, and also extending a couple tubes through the firewall on each side. More pictures to come when its done.
-
about to put in bedliner in interior but...
lbhsbZ replied to Ansel Marrow's topic in Body Kits & Paint
2 hours to pull up the tar? Whats your trick? It took me a whole weekend, 2 bottles of propane for my blowtorch, and about 5 wire wheels for the angle grinder to get mine down to clean metal. -
Here's the round lites on a project car that I bought....looks kinda gay if you ask me. I like the options posted above much better. Maybe once I lose the disneyland bumper and the motorcycle exhaust stinger, it will look a bit better. The previous owner apparently didn't have the foresight to use a welder and sheet metal, so there is a 2 inch thick block of bondo across the whole back of the car. Mine appear to be trailer lights
-
Call me tomorrow, I can get you a rebuilt booster or rebuild your original 310-947-7014
-
With a properly functioning brake system, the pedal should be relatively high and firm. The system was designed to consume a certain amount of fluid volume from the master cylinder before the pads are hard up against the rotors, and the shoes are hard up against the drums, any pedal travel after that point is component flex or problems in the system. After all the space is taken up, the pedal shouldn't move much....maybe a little, but at this point braking effort should be proportional to energy excerted on the pedal. If you have too much pedal travel or a soft pedal, that means that for some reason, one of 2 things is happening: 1: The fluid volume requirement of the actuated hydraulics has increased 2: The hydraulic system has air in it. To rule out #1, some diagnosis is in order. First, we must rule out hydraulic leaks, and make sure that the calipers and wheel cylinders are functioning properly. A visual check, including peeling back the wheel cylinder boots should take care of this. Next thing to check is front wheel bearing adjustment. If your wheel bearings are loose, it will have the same effect as sticking a screwdriver between the pad and rotor and prying the piston back into the caliper. Everyone who has ever done a brake job knows that when the pistons are pressed all the way back into the caliper, it takes a couple pedal pumps to move the pistons back out of the caliper against the pads and rotor to acheive a solid pedal. Make sure the wheel bearings are tight and have no play. The surface of the caliper piston must be perfectly parallel with the rotor surface at all times, its it's not, you must determine why either the rotor is out of alignment or why the caliper is out of alignment. I've seen bent caliper mounting ears on previously wrecked cars that caused the calliper to be out of alignment. Then check the rear shoe adjustment. If the wheel cylinders pistons have to extend to take up excessive space between the shoes and the drum, that is fluid volume, and will result in a low pedal. Properly adjusted brake shoes will have a slight drag with the drum and wheel on, with no pedal application. If the shoes are adjusted properly and the wheel bearings are tight, and you've verified that there isn't any visual movement at the front calipers during brake application (with the engine running...so that you see the benefit of the vacuum booster), then deeper diagnosis is in order. Next, all the brake hoses need to be clamped off. Most auto parts stores sell proper line locks for about $5 or so. With the engine running, and all of the hoses clamped off, the pedal should feel like a rock. If it doesn't, something upstream of the clamps (master cylinder, proportioning valves, etc) is the cause of the problem, or there is air in the system. If the pedal is nice and firm, you have determined that the problem lies downstream of the clamps, because the part of the system that you've isolated by clamping off the lines is working correctly. With the engine running, hold your foot hard on the pedal, and get a helper to release the line clamps one by one. It is normal for the pedal to drop a little as each line is released. The wheel or axle causing the problem will cause the pedal to drop excessively. That is the wheel or axle that you need to scrutenize (sp?) to determine for what reason excessive fluid volume is require to operate. If the pedal feels like crap even with the lines clamped off, then find some plugs (bolts of the proper thread pitch wrapped in teflon tape will do) and thread them into the master cylinder fittings after removing the lines. Step on the pedal....it shouldn't move more than 1/4 inch, if that. If the pedal is still soft, either the master cylinder is full of air or the lip seals are worn out and either bypassing internally or leaking into the booster. Check for fluid leaks into the booster, if you have a leak, replace the master. If the booster is dry, try to bleed the master. If bleeding doesn't help, replace it. More later....I'm tired.
-
thinking about buying a crate engine...
lbhsbZ replied to grumpyvette's topic in Gen I & II Chevy V8 Tech Board
I'm going to point out a different take on the situation. I am in the automotive industry and hear tons of stories, every day, similar to this. Say Golen engines didn't screw up. We still, after reading that thread, have no first hand evidence that the engine was as described. Every complaint was started with "My mechanic said..." I find it extremely difficult to believe that ANYONE would ever assemble an engine using 3 different types of rods. Even the greatest idiot wouldn't do something like that (I wouldn't do something like that). There's more to this story that we're not hearing, so for everyone to draw the conclusion that Golen is badness is jumping the gun IMO. His mechanic is the one who installed the engine I imagine....and there was a problem. Is the mechanic going to accept blame for a mistake he made or bullshit his way through the situation blaming whoever else was involved (golen), knowing that if he slips it could cost him thousands of dollars and a bunch or hours working on a corvette, which everyone hates working on. I turned wrenches professionally for 8 years, and now I run the technical support dept for a large brake parts manufacturer. I had someone call up the other day and tell me that they were going to sue our company because the pads that we sold caused their ABS light to come on. Thats like saying a spark plug was worn out and thats why the tire went flat. I can't count the number of "sticking caliper" labor claims I recieve back that I can squeeze the pistons back into with one hand....ironically enough, every single one of them replaced brake hoses at the same time the "defective" calipers were replaced. People who don't know the whole story are always quick to jump to conclusions. The whole story is rarely discussed on the interweb... -
Possible steering rack u-joint source -Woodward
lbhsbZ replied to preith's topic in Brakes, Wheels, Suspension and Chassis
So tell him to make the "weld on" end 3/4"....he should be more comfortable with that. I can turn up .75"OD/.56"ID bushings on the lathe to make up the difference. We'll weld the bushing to the shaft and the joint to the bushing. I really don't see why he has a problem with welding something to the .560 shaft. His only liability is if his joint breaks, not if our welding fails. -
I bought the OBX and simply reorganized the bellville washers to get more preload. It was so cheap, that I figured its atleast worth the amusment I'll gain from disassembling it with a magnet after it explodes. If it doesn't explode, even better. I'm looking to have the car running in by the end of March (all my parts are in) and there is a track day in early april that I'd like to attend, so that will be the test. The casting was not as clean and polished as the QUAIFE unit I ran in the VW, and the bolts that hold the assembly together were of very poor quality...I ordered replacements from McMasterCarr. We'll see what happens.
-
Possible steering rack u-joint source -Woodward
lbhsbZ replied to preith's topic in Brakes, Wheels, Suspension and Chassis
I ended up taking the rack apart...cuz I wanted to figure out how. I have a pinion shaft, wire wheeled, cleaned, and ready to ship. It'll go out tomorrow. Do me a favor and email me your shipping address again. pat@stopitbrakes.com -
http://sandiego.craigslist.org/car/280759389.html I'm a day late and a dollar short for this one, but it sounds like a decent deal. I'll be in San Diego next weekend if anyone wants this thing, I can go by and check it out or tow it back to LA.
-
Front 13" low buck brake kit....DONE!
lbhsbZ replied to lbhsbZ's topic in Brakes, Wheels, Suspension and Chassis
SWEET! I bolted up a ball joint and control arm and I've got 1/2" of clearance with the arm in the full compression position (limited by the ball joint). -
Front 13" low buck brake kit....DONE!
lbhsbZ replied to lbhsbZ's topic in Brakes, Wheels, Suspension and Chassis
No, I said I could get rotors cheap. The core charge on the calipers is what kills the deal most of the time....but here it is. $35 each for rebuilts, with a $20 core charge. So $70 for the pair if you send me your old ones back, or $110 if you keep your old calipers. I also have seal and boot kits so you can rebuild them yourself for $5 each. Unfortunatly, I don't have any race pads for these calipers....the best thing I've got is an Axxis (PBR) Deluxe pad, for $35.