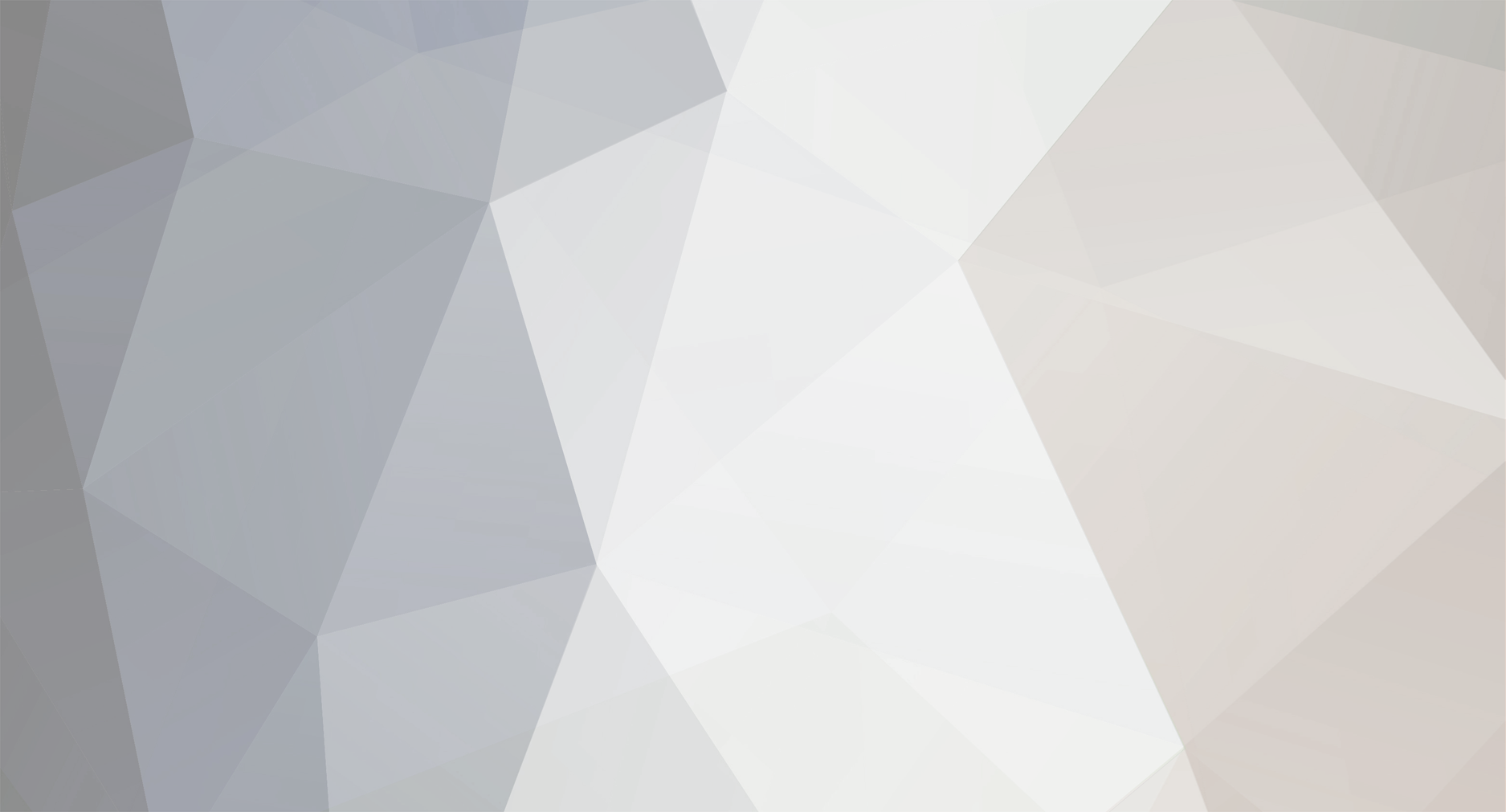
lbhsbZ
Members-
Posts
409 -
Joined
-
Last visited
-
Days Won
1
Content Type
Profiles
Forums
Blogs
Events
Gallery
Downloads
Store
Everything posted by lbhsbZ
-
Type of welder used when seam welding chassis
lbhsbZ replied to icesky's topic in Fabrication / Welding
Icesky, I'm in LA. depending on where you are, and how far you'd like to drive, I've got a Lincoln 110 mig laying around (just upgraded to a 220 mig) that I'd let you borrow to do the job. It'll cost you a deposit and some beer though. Give me a call. 310-947-7014 -Pat -
Well, seeing as how you already bought the compressor, this is what I think you should do now. Go down to harbor freight and get an air cutoff tool and a couple of those $7 die grinders. I've got 10 of the die grinders. They're so cheap, I leave a different bit in each one of them. while you're there, pick up a couple of those orange electric angle grinders. Use one with a flap wheel for cleaning and prepping metal, and use the other one with a cutoff disk for your heavy cutting. If you want to do sanding, get a orbital electric sander. Save the compressor for impacts, air ratchets, minor cutting and grinding, etc. Unless you are a smoker and drinker, the breaks you have to take every 5 minutes to let the compressor fill back up will start to piss you off quick.
-
Type of welder used when seam welding chassis
lbhsbZ replied to icesky's topic in Fabrication / Welding
I seam welded mine with a mig. Unless you can get the metal perfectly clean, TIG isn't going to be a good time. Migs are a lot more forgiving of dirty metal. Even with the mig, I had a hell of a time. Maybe someone has a better way to clean the seams, but I used a propane torch, and heated the seam until the glue started bubbling a bit, then went at it with a wire brush. I got a bunch of sealer out of most of the places, but still had trouble with porous welds do to contamination. I'm not worried about it because they are only seam welds, not super critical, but I'd like to know how to properly clean the seam. -
http://www.howeracing.com/BuildMaterial/Index-Construction-AdelClips.htm Google "Adel Clips"
-
If I was running the baja, I'd use a Ford 9" or bigger Thats just me though. Both answers are correct. AFAIK, The ring gear is designed so that the bolts, loaded in tension only, provide enough friction between the ring gear and the diff to keep everything in place so that bolts are never loaded in shear. But, if enough load is put on the ring gear to overcome the amount of friction between the ring gear and diff, then they will spin indepenently and load the bolts in shear. Now the question....since the bolts aren't supposed to be shear loaded anyway, does it matter if they are loaded by a steel spacer or a cast diff? I dunno.
-
Check your timing, I 12-16 degrees is a good starting point for static timing. What type of fuel pump is being used? What if, instead of pulling into the street and "hammering it", you just smoothly and slowly open the throttle. Does it run OK when you do that? If it does, make sure the accelerator pump on the carb is working properly. If you look down the primaries and open the throttle, you should see 2 strong streams of fuel coming out of the nozzles. If its working properly, start playing with cams and larger nozzles. Does this carb have the 35cc pump or the 50 cc pump. i would upgrade to the 50cc pump.
-
I don't know about you guys, but I've had my share of bad luck with them. I thought maybe we could start a thread and stick it in the FAQ section, organized by region, of shops that do good work that we have experience with. I don't claim to be a machinist by any means, but I do understand the procedures involved, and how critical it is to adhere to those procedures so that parts get machined correctly. I've recently went through 2 local shops one of which didn't measure properly (or at all) when doing a valve job, and another one that I switched to after that, who up until now has had my business....until I watched them machining a block for me, with no torque plate, no main caps torqued in place, on a beat up old machine that IMO was well past its prime. I walked out and told them to keep it, and the owner doesn't understand why. So I started looking around and stumbled on to Speed-o-motive in West Covina CA. After reading all the technical stuff on the website and spending about 20 minutes on the phone with them, I was fairly impressed. They asked me to come out and take a tour of the shop and watch some of the processes, so I did that today. WOW! Everything in the shop was spotless clean, at least 6 CNC machines all working away. The operators took the time to explain to me what each one of them were working on, how they set it up and why, and exactly what the machine is doing. Then there was a guy with a roll of tape and an X-acto knife doing a better job masking off a block for paint than most body shops do on bodywork. I spent about an hour in the shop, just observing. The attention to detail that I saw was simply amazing...so I dropped my 3rd core off (the other shops ate the other 2 cores), went over the specs I wanted, and we drew up the estimate. All this accuracy and attention to detail doesn't come cheap. To bake and shot blast the block, magnaflux, measure it up, blueprint it (align bore, cylinder bore, deck, remeasure), install cam bearings, ran me just shy of $900. I thought it was worth it after seeing what $300 got me at the other places.
-
They're actually quite easy, the cone just needs to be machined at an angle of 91 degrees or less, because the flare on the line is generally 90 degrees or more.
-
With what pistons?
-
Thats funny, the main hoop is the only part that I thought fit rather nicely.
-
Yeah, I was using mine the other night (another project) broke a 2 teeth of a Starrett hole saw and I was using a big old Black and Decker 10 amp 400 RPM drill motor....the hole saw hooked in, damn near broke my arm and bend the hell out of the notcher mounting bracket. It used to sit horizontally on my bench, now it sits vertically. Time to make a new one. I never got a call from you on the Autopower you bought from me....am I to assume that you made it work?
-
Ferrea Components for LS2 240Z
lbhsbZ replied to duragg's topic in Gen III & IV Chevy V8Z Tech Board
The LS motors use a beehive shaped valve spring, not the conventional type. Those are almost a 1.5" OD spring, and I doubt that there is enough room in the head to machine the spring seats out to accept these larger diameter springs Also, I'm not sure what stock seat pressures are on the LS2 springs, but 285 open seat pressure at .550 lift isn't a whole hell of a lot. The stock cam I beleive is about .500" lift, which would be 272.5 lbs of seat pressure with the valve open. I don't know if thats enough. If you look at the Ferrea catalog, you'll see that the lightest springs they make for the LS engines has 320lbs of seat pressure @.550 lift, and the more aggressive springs are 470lbs @ .600 lift. I run 230lbs of seat pressure with the valve closed, and about 600lbs at .680" (not an LS motor though). I don't think you'd be gaining anything over stock springs with those Ferrea springs, if you can make them fit. They are probably not any stronger, maybe even weaker than the OEM springs....If you are using an aftermarket cam, see what the cam card specs out for open and closed seat pressures, and get the correct springs that satisfy both the open and closed pressures called out by the cam manufacturer. -
The tig would have been the weapon of choice, had I been able to get perfect fitup on all of the fishmouth joints, but the Harbor Freight tubing notcher (and possibly my notching skills) were slightly less than accurate, leaving me with some gaps to fill. Filling gaps with a Tig sucks. Filling gaps with a MIG is easy. I chose the MIG. Towards the end of the job, the joints got much better as I modified the notcher and got more practice with it.
-
Need help! Removing the strut cart.
lbhsbZ replied to CruxGNZ's topic in Brakes, Wheels, Suspension and Chassis
Drill a small hole in the bottom of the strut, but not through the cartridge...give it a couple shots of starter fluid, Tape a match to a long stick, strike it on the ground and wave it by the hole. Before you do this, it would be best to chain both piece to a tree, and make sure your stick is longer than the chain. If it does work...should be fun to watch. You've got to video this attempt though. -
Glad I could help
-
Stay away from TGs on Prarie, they are the cause of my current drinking. In the past, Vellios has been the cause of my drinking. I'm trying to get ahold of an old friend of my father's, that used to build big horsepower drag motors. I met with him a couple times, and recall that he went through every machine shop in the area before he found one in orange county that did good work. I also hear that Cosworth down in Torrance is doing job shop machine work now, though at this point, without bringing them a dummy block to prove themselves with, I'm not ready to pay anybody a dime. I tried not to be cheap this time, and buy the top shelf parts and pay for top shelf service, but it all bit me in the ass. I'm at a point now where I'm almost ready to crush the car, throw all the parts on ebay, and cut bait. Too much bad luck. I bought an autopower cage, but I didn't like the fitment, so I sold it. The buyer said nothing would fit so I have to refund his money (I don't believe in screwing people). I bought a bender and a new Miller 180 Mig welder to replace my Lincoln 135 to build my own cage. The Miller caught fire the first night I used it. It was like pulling teeth to get my money back. Then the engine came back all screwed up....on top of the seller of the car that I bought (owner of a reputable shop) lying through his teeth about the condition of the powertrain. Maybe I should cut my losses and throw it all in the trash, while I still have some money in the bank.
-
The filler neck on those cars is about 10 inches long and comes right out of the tank. What exactly do you want to "pull off" of the donor car? There are 2 pieces to the system, the hinge on the licence plate frame and the gas tank. Most of the late 60s, early 70s vintage GMs used this design.
-
AH, finally a thread for guys like us. I just got my block back from the machine shop after 4 months....they got me most of the rotating assembly too. Parts kept getting more expensive, then they overbored the virgin block that I brought them, so that the $900 pistons that I had made wouldn't work. Then they found another block, prepped that, and I picked everything up on Friday. Just got around to putting the crank in tonight and it doesn't turn when you torque down the rear main. I dykemed the rear main bearing and thrust surface and muscled the crank around twice, took it off, did some measuring, and the thrust surface/bearing surface on the rear main cap is off by about .008"...Dammit. Time to find a new machine shop....and a new block.
-
My car had a similar setup on it when I bought it, just a little more homegrown and a lot more hacked. There didn't seem to be any clearance issues.
-
The typical EZ-outs are junk. Every time I've ever used one, it broke. I have a set of extractors that I purchased off the MATCO truck when i was working at the dealer. They are like EZ-outs, but different. Each one is only about 1 1/4 inches long, and they use a 13mm (1/2") hex that you can put a wrench on to turn it. The Extractor part is only 1/2" or so. One of the reasons that EZ outs break is because they are too long and flex to much. The Matco units work awesome, I've probably taking out 100 broken bolts with them, some crossthreaded and some rusty, and never had a problem. Once the EZ out breaks off, you're kinda screwed. They're made out of the same stuff that conventional drill bits are, so you can't drill them.....unless you use a carbide tipped masonry bit. Yes, masonry bits will drill through taps and ez-outs that you've broken off in a hole....the only problem is, you can't find masonry bits in very small sizes. I busted a tap off in a 6mm hole yesterday. I got it out using my O/A torch with the smallest tip I could find, got a tiny hot little blue flame and hit the piece of tap till it glowed, then shut off the Acetylene and it blew right out. The hole was a little damaged, so I had to tap it to 8mm and then drill and tap an 8mm bolt to 6mm, but I made it work.
-
I think i understand your problem. The TEE you got uses bubble flare seats (like a little valley at the bottom of the hole), while your lines are flared to screw in to fitting with an inverted flare seat (little mountain at the bottom of the hole). Am I right? if this is the case, there are two possible solutions. #1, go out and buy yourself a flaring tool. Making a flare is a 2 step process....first you have to use the die that fits inside the line to make a bubble, then you use the conical shaped die on the press screw to crush the bubble making your inverted flare. You can make new hardlines using only the first part of the flaring process, and they will work in your new TEE. #2, if you have access to a lathe, you can make some small inserts that press into the holes in the TEE. I have a picture of one at the office I can post tomorrow so you know what I'm talking about. I think it would be easier to remake the lines with the proper flare for the fitting you have.
-
As proud as I am of my work, I'm not gonna sit here swingin' my dick, My cage is far from perfect compared to what JohnC or others who do this for a living can do. I don't have half the welding or fab experience that he does. I just like my car the way I like it, which is why I spent the money to do it my way....because experience has taught me that nobody, no matter how much you pay them, will do it exactly the way you want it done. I got the cage fitment nailed, but my welds look like crap. I know they are solid only because I watched the puddle through every single one of them...even used a mirror so I could see it properly on some of them, but they're kinda ugly. The last cage I installed was a crappy fit, leaving plenty of room to access the joints and make nice pretty welds....this one was a tight fit, and tough to weld. The mig gun wouldn't even fit in a couple of spots, so I had to break out the stick welder and bend a piece of rod to get to them. I'd be more than happy to build cages for anyone here....I've got a couple local jobs lined up in the next couple weeks to help me ammartize (sp?) the cost of the bender. I learn more tricks on every one I do....but I work out my garage, and for now I'm an amature, and I don't want to take business away from the real fabricators out there.
-
...until you bend it Aluminum work hardens, so if you make fuel lines out of it, secure them well so that they cannot vibrate independently of what they are attached to, and you should be fine.
-
I run the Tech support dept, quality control dept, and do all of the brake caliper production planning for Centric Parts. I've been there for about 4 years. Some days I like it, some days I hate it. I also do auto repair on the side out of my garage, and some minor Fab work too. Hopefully some day I'll have my own shop, doing everything from basic auto repair, to building cars to whatever odd jobs I can get. I hate doing the same thing every day, gets boring. I like to take on new challenges becuase most of the time they are a learning experience.
-
I bought the bender through Pro-Tools.com. Its the Pro 105 model...a little less than $800 shipped. It was worth it. Takes 5 minutes or less to make a bend. The guys in the video must be bending conduit or something...makes it look easy. I used .120 wall tubing. I weigh about 200 lbs and I had to brace myself against the side of my truck to pull the handle (I made it mount in my receiver hitch).