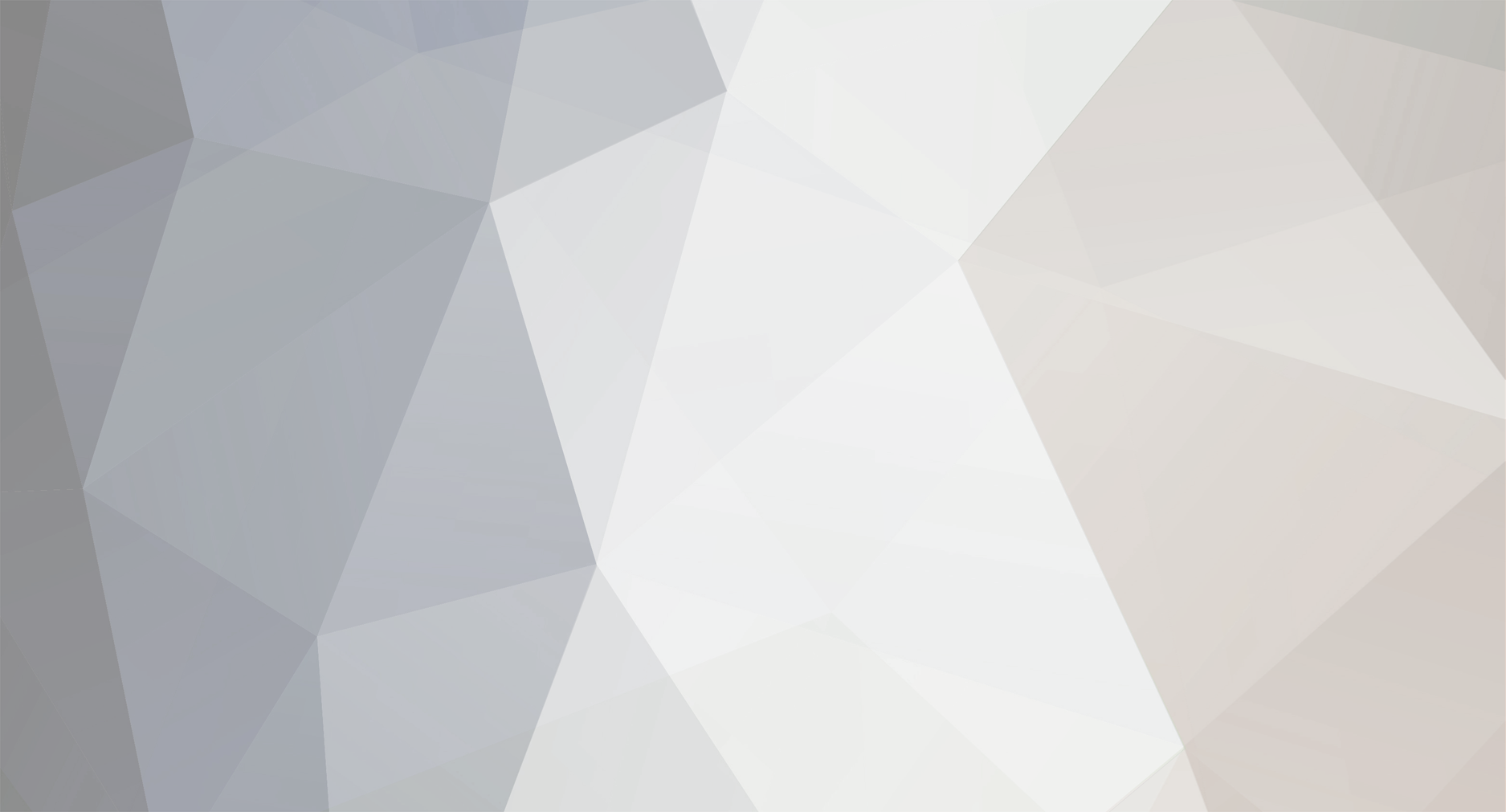
lbhsbZ
Members-
Posts
409 -
Joined
-
Last visited
-
Days Won
1
Content Type
Profiles
Forums
Blogs
Events
Gallery
Downloads
Store
Everything posted by lbhsbZ
-
How far does it move up....it can't just keep going forever. Mark the pulley and the balancer, and run the car around the block a few times...see if the marks are still lined up or if they moved. Spun balancers are not uncommon, especially on a '77. How are the bushings in the distributor? Does the shaft wobble back and forth at all? How is the timing chain? You can check this by rotating the crank back and forth with the Dist. cap off....if there is any lag in movement of the rotor while you are turning the crank back and forth, the T-chain is toast.
-
You do NOT need a 10ga wire to the "batt" terminal on the HEI. I run a 10ga wire on my alternator. A 16ga wire (in good condition) is plenty for an HEI power wire. I've turned 6500rpm with stock junkyard HEIs without problem.....sure, the voltage may drop off slightly at higher RPM, but not enough to limit your RPMs to 4500. Something else is going on. Have you looked at the plugs yet? Its a little harder with an automatic, but if you have a stick....run it WOT in 3rd until it stops accelerating (4500rpm) and keeping your foot flat on the floor, kill the ignition and stand on the clutch. When the engine stops spinning, you can take your foot of the throttle and hit the brakes. Pull a few plugs. This will tell you what ballpark the mixture was in at 4500 RPM. Whats your static timing? whats your total timing? Where do you have the vacuum advance hooked up...ported or manifold vacuum? How did you verify that the secondaries were operating properly? What cam? Any MSD or other wizbang ignition components?
-
I tried to do this....and here are the difficulties: You have to use a steel (scattershield) chevy bellhousing and redrill the holes to mount the trans. The front bearing retainer on the ford trans will have to be machined down slightly to fit in the pilot hole in the bellhousing. The Pilot shaft on the ford trans is about 3/4 of an inch longer, so a 3/4 inch spacer will have to be used between the trans and bellhousing or between the bellhousing and block. Then you have to make a custom pilot bushing because the shafts are different diameters. Once you've made everything fit, you should be able to use a ford clutch disk with a GM pressure plate. This is not the cheap way to do it. If you'd like, I've got a WC-T5 gearbox out of a TPI camaro for sale, and I'm in LA (pretty close by). I've got the shifter and bellhousing aswell. I'll let the whole thing go for $450. Oh yeah, the splines are slightly different sizes and shapes between the ford and Chevy pilot shafts, so while the chevy clutch will slip over the ford pilot shaft, there isn't a whole lot of spline contact and you would probably strip the splines off of either the shaft or clutch or both the first time you stood on the throttle.
-
Check the door chart for recommended settings based on the material you are welding. This will get you in the ball park. The wire feed may need some adjustment though....The door settings will vary depending on your available power supply. When you are welding, pay attention to the wire...if the gun pushes back, like its feeding wire too fast...reduce the wire speed. If the wire is burning back towards the tip, and looks like a bunch of drops of molten metal landing on the workpiece, then increase the wire speed. Check out http://www.hobartwelders.com/mboard/ There is ton's of information there, read up and ask questions.
-
My main concern was whether or not a design flaw had been discovered during the inspection. I understand that parts will break, especially in the environments that most of us subject them to. If the stubs are as good as they get, fine, I'll just inspect them after each event. If any areas for improvement were found, I'd like to get some revised units. I'm very happy with the stub axles, the machine work looks flawless, and its a beefy piece, but I'm not an engineer and don't have the ability to properly analyse a failure like this.
-
Any failure analysis yet from Ross? I'd really like to know what caused them to break.....or what it took to overcome their strength. I bought these thinking that they were indestructable (my opinion, not the words or Ross or MM).....and when they arrived, they looked pretty bulletproof. A failure in a road race car may be fatal, so I'd like some info as to their limitations before I chance it.
-
Eh, I've got 7 welders, so you're TOO crazy yet... TA 185 tig Lincoln 135 Lincoln 175 Harbor Freight wire feeder Dayton 250 AC/DC stick welder Lincoln 200 amp stick welder Craftsman 130 amp stick welder ....and an oxy/acetalyne setup The real question is how many die grinders you have... I have 26
-
The OBX is/was brand new. The chamfer on the gears was like that when I disassembled it the the first time, after I had just received it, New in the box. The only wear in the OBX at this time (after 10 miles of rocket runs in our warehouse complex) is the smashed up washers. Just crappy build quality, no attention to detail, and no pride in their work at OBX. Looking at the Quaife part, I'm sure that after all the workers see the finished product, there is a smile on their faces for a job well done.
-
Does anyone want to buy a "reconditioned" OBX unit for $300?
-
It has been stated in the past that the OBX diff is a direct copy of the Quaife differential. OBX is a company that has a reputation of producing cheap chinese knockoffs of quality parts. I purchased an OBX diff for an R200 off of ebay (brand new) for $375, and I also purchased a brand new Quaife for an R200. Retail on the Quaife is $1495.00. I have a connection that saved me about $300. The only similarity I found was the design and the theory of operation. The parts are all pretty different, which leads me to believe that OBX actually employed some of the own engineering into this one. When the OBX arrived, I noticed what appeared to be a missing bolt, and I also noticed that out of the 11 remaining bolts, 9 of them were marked 8.8 strength and the other 2 were not marked, and had noticably smaller heads. After disassembly, I found that the 2 odd bolts, aside from having smaller heads and no spec markings, were also too short. The appearance of the unit was acceptable... until I opened the box containing the quaife and saw this... I now understand why the Quaife costs 4 times as much as the OBX. I was hesitant to open up the Quaife, because they don't break and the warranty card says I shouldn't, but I decided to because there hasn't been a picture thread comparing the 2 side by side. The first difference, obviously, is the appearance and finish quality of the assembly. The quaife looks like a diamond, while the OBX looks like a rock. The OBX only has Ten 12mm holes to mount the ring gear, so if you are using an early ring gear, you will need to make spacers to take up the extra room around the bolt. Some say this isn't necessary, but I don't think its a bad idea. The Quaife has 20 holes in the ring gear flange....so that you can use either the 10mm or 12mm ring gears. This was a nice touch. The quaife uses 12 12.9 strength M10 bolts to hold the case together, while the OBX uses 9 8.8 strenght and 2 unknown quality M8 bolts to hold the case together. The OBX bolts are on the left, the Quaife bolts are on the right. The OBX uses a 2 piece case, with all 11 bolts from one side, while the Quaife uses a 3 piece case, consisting of basically 2 end caps and a solid center section, and uses 6 bolts to hold each cap onto the center section. OBX is on the left, Quaife is on the right...with only the bolts and part of the case removed. The flash didn't work, so I'll try to get a better pic later. Here is a shot of the pieces removed to take the previous picture, again, OBX is on the left, quaife is on the right. Here are the sidegears from each diff. The OBX uses a gear that simply floats inside in the housing....only centered by the loose fitting axle. The quaife sidegear has a pilot which locates it in the housing. The OBX has longer teeth than the Quaife sidegear. OBX is on the left, Quaife is on the right. Both units each use 12 helical gears....6 for each side, but they are a little different. The OBX helicals have almost 1/4 inch of chamfer on the edges of the gear teeth, while the Quaife has substantially less chamfer. Less chamfer means more surface area able to generate friction against the case. the Quaife also uses larger diameter gears, that have some sort of surface treatment. OBX is on the left, Quaife is on the right Now for the washer stack. The Quaife uses 6 washers, stacked )()()(, while the OBX came with 8 washers stacked ((()())). The washers retainers on the Quaife are considerably larger in diameter and very slightly longer than the OBX retainers. See my other thread for my problems with the OBX washers. Quaife washer stack OBX and Quaife washer retainers While the OBX uses a separate spacer to house the the washer retainers and washers: The Quaife incorporates this into the case center section, so there is no spacer to float around: Thats if for the pics....camara batteries went dead. The Quaife has very finely ground mating surfaces, almost polished, everywhere....there is not a dirty cut or coarse finish anywhere on it. It appears that every component has been though a vibratory deburring process, and then polished...amazingly well. The Quaife came coated in the thick anti corrosive oil, which wiped off easily with a rag and solvent. The OBX diff has only finish machined surfaces, which on cast iron tend to be very porous...and arrived with what appeared to be residual cutting oil soaked into the pores. When you try to wipe it off, your rag gets caught up in the rough surface. No post machining deburring or polishing was done to the case of the OBX. The gears look to have been deburred, but not polished. I think that the OBX diff would be fine for lower TQ applications if some things were replaced on it. First off, the washers need to be replaced. I think the best solution for the washer issue would be to make a spacer for the middle and use only 2 bellville washers, one on each side. Second, the case bolts need to be replaced with something of a higher grade. The OBX bolts are M8 x 1.25 x 60mm, available from McMaster car in 12.9 strength. I have a theory that the reason that my washers were destroyed in the OBX was because the case bolts were weak and stretched, allowing exessive clearance in the washer pack under accel and then impacting them on decel. I don't have the brains to prove this yet, but I'm working on it. Another possible flaw I see in the OBX is the oil holes. The Quaife has more holes for gear oil to enter the assembly, and the holes in the Quaife are much larger than the OBX oil holes. When I reasemble the OBX, I'll be adding a few more oil holes in non-critical spots in the case. The Quaife's M10 x 30 bolts are much less prone to stretch, and therefore the quaife is a much more ridgid unit that can handle more TQ. I hope this is of some use to somebody....
-
I'm still concerned because even uncompressed, the retainers only catch 0.3mm of each washer. When they're compressed, nothing will hold them in place. I'll pull my quaife apart tonight to see how they do it...more pictures to come. EDIT: the quaife (real one) just arrived ::drool:: Seeing these 2 next to each other, now I understand why the Quaife is 4 times the price. The first difference I noticed, is that while the OBX uses 11 8.8 strength M8 bolts to hold the assembly together, the Quaife uses 12 12.9 strength M10 bolts to hold the assembly together. Its also double drilled for the ring gear, there are 20 holes...10 for the M10 bolts and 10 for the M12 bolts. Its a very nice piece. The Quaife also uses 6 washers instead of 8. Pictures to come later.
-
I've got a set of those spacers (all 4) that I'll let go for $120. They're brand new, if anyone is interested.
-
Well, if I do the math, the The uncompressed stackup height would we the same, with very little preload, but on Decel, it would still smash all the washers flat and let them fall out...When the retainers are flush with spacer, there is 8.9mm between the lips on the retainers for the washer stack to go. Each washer material thickness is 1.55mm, and 1.55x6 = 9.3mm. Even with 6 washers, the retainers would bottom out on the washer stack before the side gears hit the spacer.
-
So, Whats the vote on the washer/spacer situation?
-
I think you may have figured it out. Maybe I'll sacrifice my cat on the workbench next to the diff while doing a chant of some type, and it'll start working. Thats probably what they do in england with the Quaife.... The reason the Chinese one doesn't work is cuz the workers probably ate the cats for lunch before they put my diff together, and the gods of speed can't understand their chants
-
I agree with what you are saying, but when the unit is assembled, all of the washers are completely flat, so there are no points.....and there is a 4.45mm gap between the 2 retainers.....the washers are only 1.55mm thick, so that means that 2 washers are not supported at all, and 2 more are only about 1/2 way supported. My diff uses 8 washers, that when the diff is assembled, are compressed flat. I've been doing my reading, and I agree with you that the only way to change the bias ratio is to change the helix angle on the gears...in which case the only purpose served by the washers is to keep everything preloaded so it doesn't clank around. I can make a spacer... 6.25mm long, and use only two bellville washers on each side of it in the retainers. that would completely retain both washers, and each retainer would catch almost 1mm of the spacer, ensuring that everything stays where it was supposed to. The diff still worked fine with the destroyed washers that were in it (no pre-load), so I think it should still work fine if it had half of its intended preload due to only using 4 washers, or better yet, make the spacer 9.35mm long and use 1 washer on each side....then that would even cover some case bolt stretch. Waddya think?
-
I recieved my new washers and other parts today, finished disassebling things, cleaning, and began reasembling. I noticed a few things. 1: I was wrong as to why the washers were destroyed 2: I still don't have any idea as to why the washers were destroyed 3: I longer care why or how this diff design works 3: there is a lot of room for error in the assembly of this differential. Here are what the original washers looked like when I removed them. Here is one side of the diff case, with one of the side gears and the corresponding 6 helical gears dropped in. There is a left and right side gear, and six left and right helicals. If they are installed on the wrong sides of the diff, the helicals will push the side gears against each other instead of outward against the case. I'm not sure how they were installed the first time. This is how far I tore the unit apart to reposition the washers the first time around. This is the spacer that goes between the left and right side gears. These are the bellville washer retainers, and another shot with one of them dropped into the spacer Here is the spacer, with 4 washers installed between the two retainers. There is a lip on the OD of the retainers that catch the washers, so that the function of the washers is only to push the retainers apart. I was wrong about the washers being a friction surface....I didn't have the diff in front of me and forgot the exact washer retainer mechanism. It appears now, that the washers, spacer, and retainers are an isolated spring mechanism inside which abolutely no movement can possibly take place. So I started measuring to make sure I wasn't jumping the gun on my assumption. If I build the diff and install only the side gears and spacer (no washers), there is 4.2mm of clearance between the stacked assembly and the cavity in the case. This means that in order to have 0 preload, and 0 clearance, the washers must be stacked in a manner so that the retainers stick out of the spacer by 2.1mm on each side of the spacer, and take up the 4.2mm of clearance. The spacer measures 22.95mm thick 1 retainer measures 10.90mm thick 1 retainer measures 11.10mm thick, but the spacers are not perfect. There is about a 0.1mm thickness variation in each one. Lets call the average combined thickness 21.95mm The lip on the OD of each spacer is 3.0 mm wide, and located exactly in the center. The total available space for the stackup height of the washers and the retainers needs is 27.10mm to achieve zero clearance. Each bellville washer has an unloaded height of 2.31mm, and a material thickness of 1.55mm. To acheive zero preload, we need 5.64 washers stacked up like ()()(). 6 washers then would be the minimum necessary for quiet operation. This will make the space between the lips on the retainers 12.45mm, and consequently the space between the retainers will be 4.45mm. but we're not using 6 washers, we're using 8, and with a material thickness of 1.55mm, all the washers have to be fully compressed and flat in order to bolt the assembly together. (since the lip is 4mm from the edge). Since the material thickness of the washers is 1.55mm, that means there is nothing to keep the 2 center washers () in place and centered....and they can fall out and contact the splines inside the spacer, then get crunched as the gears smash toward the spacer and force the retainers back flush with the surface of the spacer. This may be what killed my last set of washers, it makes sense because only the 2 washers in the center of the stack were completely garfed up.....but I'm still not sure how it could happen. This may be why the washers were originally stacked )((()))(, so that all of the washers in the middle kept themselves aligned and couldn't fall out of place and get smashed. If I stack 6 washers up ((())) the stackup height is 11.06mm. If I add the next 2 )((()))(, I end up with a stack up height of 15.6mm. This puts us well within the goal of the 12.45mm minimum washer stackup height required. If the two washers on the end are flattened (they will be the first 2 to flatten), the total uncompressed stackup height will be 14.16mm. Now, here's the kicker. With all the washers fully compressed and flat, the stack up height is 12.45mm, exactly the same as our available space....so there is no room for the retainers to move inwards, and therefor no way for the washers to get smashed. WTF am I missing here? The only possible scenario that I can think of is the cheap ass bolts that are used to hold the case together are stretching when I put the power to it, causing the case to spread apart a bit, and the side gears to move further away from the spacer, allowing the retainers to move apart and the spring washers to relax and fall out of line. Then when I get out the throttle, the whole mess comes smashing back together and the washers get impacted to death every time I get off throttle. I don't think the carrier bearing preload would allow this to happen though....is it possible that I'm flexing the whole pumpkin? I dunno though, its a long shot. any ideas? I'm going to read through all this jargon and probably edit it a few more times, so if you need clarification on anything....please ask. I'm getting confused myself at this point.
-
I agree with you that they are designed as 1 way diffs, in which case you must agree with me that the washers are ONLY there to preload the side gears outward against the case. The washers are not intended to act thrust surfaces under decel, but they do, offering a bit of LSD function, intended or not. With the torrington bearings, the washers will still provide the same or better preload on the side gears, but will have no frictional qualities.
-
The only friction I'll reduce will be under decel, which I don't care about. The washers are not supposed to be a friction surface anyway. The only purpose that they were designed to serve, is to preload the side gears outwards against the case, which they will still be able to do properly. The bearing will only allow the washer stacks to rotate against each other without becoming mangled....at least thats my theory.
-
Well, yeah, you do. Steel on steel with no pressurized oil cushion between them makes for a fast wearing bearing surface that will gall quickly and eat itself...period. I don't care what kind of steel it is, if you stack 2 pieces of the same metal next to themselves, then press them together with a lot of force and spin them against each other, they will be destroyed. Especially when there is such a tiny amount of contact area between the components. Flatwashers would fair much better because of the increased contact area, but would still be destroyed over time. Gears don't have this problem because by nature of the shape of the meshing gear teeth, the oil on the surface is more or less pressured locally between the meshing teeth, protecting them. The material might be inferior, but that is not the root of the problem. Putting better washers in will only prolong the agony...something else needs to be redesigned. I've ordered up a pack of bellville washers, shim washers, and torrington bearings from McMaster. I'll attmpt to reassemble this thing properly so that it won't eat itself....ever. I'll post some pics after the parts come in and I figure out the correct stackup heights.
-
I already ordered a Quaife unit, so my immediate problem is solved. I'd still like to make the OBX work though...just because it doesn't look like too bad of a unit, it just needs some design modifications and I'm sure it will work great.
-
The side gears are the ones that the axles are stuck in, they are the last things in line, which means that they are the DRIVEN gears, and cannot be the DRIVE gears. Correct I know I am I concur once again, I agree no, different difference. The side gears are connected to the axles, the scroll gears or helicals move with the case. my understanding is this: before the axles BEGIN to turn, the case has to load itself against the scroll gears...at which point the scroll gears begin to move with the case until the gear tooth clearance is removed between the scroll gears and the side gears, at which point the side gears are resisting being driven by the scroll gears, and that forces the scroll gears inward into the case and the side gears outward into the case, at which point the axles begin turning. correct, my thoughts exactly. The spring washers are between the two side gears, and have nothing to do with the scroll gears (helical gears) I'm tired too....sleep well.
-
I highly doubt that, no testing has been done to prove it or disprove it, but I still call bullshit. And he has never re-disassembled it to check the condition of his new washers, which were also not designed to be dynamically thrust and rotationally loaded, both at the same time. Regardless, I think that bellville washers are not the correct piece to use under these conditions. Bellville washers are a progressive spring, not a friction surface....and under no circumstances should they be used as a friction surface IMHO. There are plenty of better ways to do it.
-
Umpossible. The side gears (two big ones) have no positive mechanical connection to the case, which is driven by the ring gear. The side gear are the "driven" gears, which are driven by the scroll gears (12 little ones). The scroll gears move with the case. So the scroll gears, or helical gears, drive the side gears, not the other way around. Until I understood this, I was all confused about how the thing worked. Edit:, for those picking nits, the quoted statement is true, but only under decel
-
just read the link you posted.....my brain assploded when I got through the part from the Gleason BSME. I don't understand all those numbers...I just make stuff work or blow it up trying.