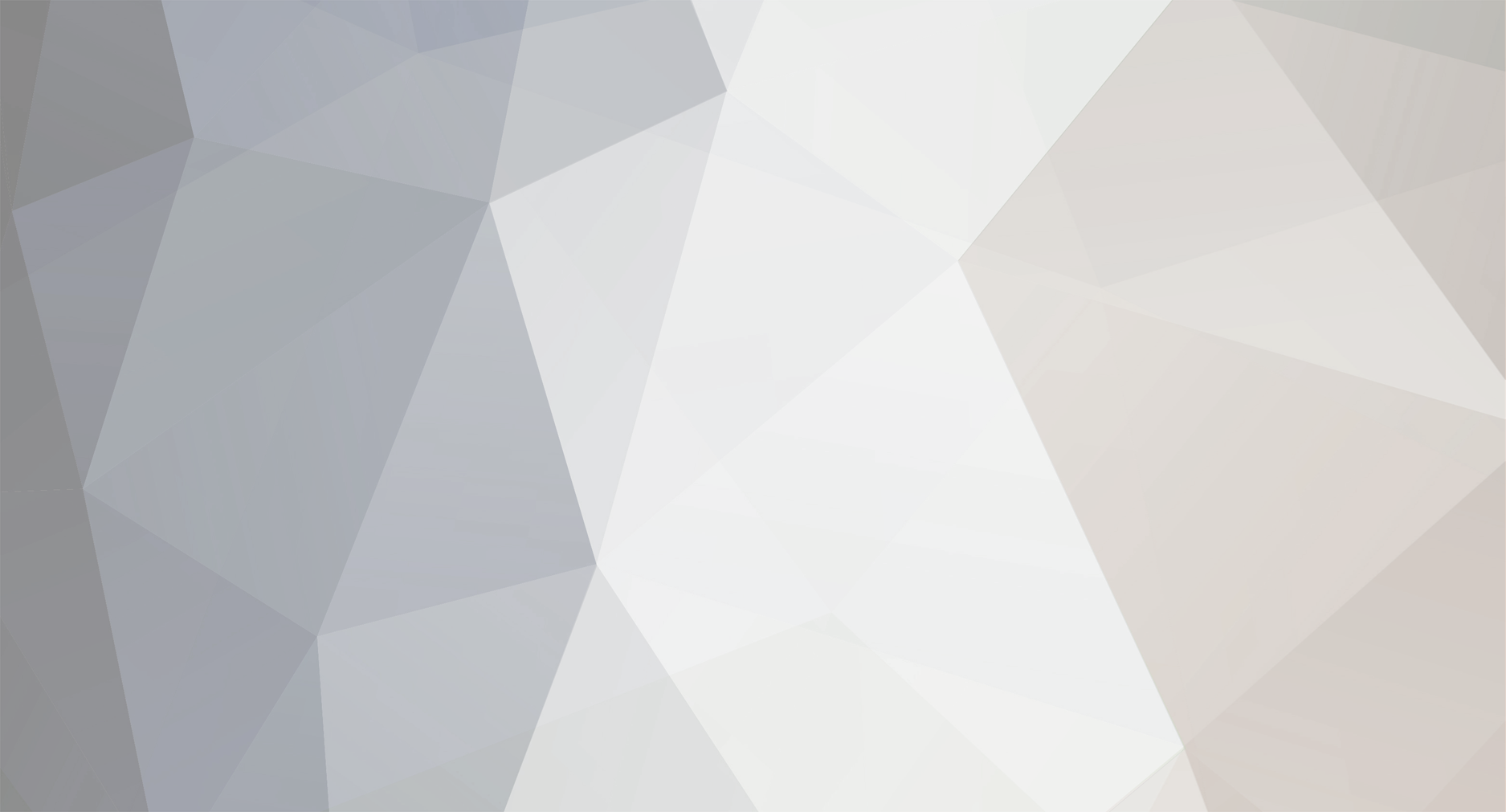
lbhsbZ
Members-
Posts
409 -
Joined
-
Last visited
-
Days Won
1
Content Type
Profiles
Forums
Blogs
Events
Gallery
Downloads
Store
Everything posted by lbhsbZ
-
Just have the cam galvanized
-
Braking - More then Big Rotors and Lots of Pistons
lbhsbZ replied to johnc's topic in Brakes, Wheels, Suspension and Chassis
I'm not sure if you are referring to brakes for a street car or brakes for a racecar, but I'm going to assume the later, because you're a racer...in which case....(and since I like to argue).... I usually agree (after much questioning) with most of your thoughts...but not this one. What I agree with: The stock brakes, in good working order can stop (or slow) your car just as good as big boy brakes. What I disagree with: The stock brakes, in good working order, can stop your car just as good as big boy brakes. I know, that might be confusing, but here's what I've got: Any brake system that allows you to lock up the wheels is adequate, but not ideal. Like your article said, locking up the wheels is not the fastest way to slow a car. Your article also mentioned release, which is a function of pad characteristics and has not much at all to do with the actual brake system design, so I'm not going to get into that. If you can lock up the wheels, you have enough braking power to stop the car as fast as it can possibly be stopped (short of running into a wall)...period. If you can lock up the wheels, larger brakes are not going to make your car stop faster....BUT, read on.... Larger rotors have several advantages....with a larger rotor, you have more leverage about the spindle to slow the wheel (like trying to loosen a lug nut with a 3/8" ratchet versus a 3 foot long breaker bar), so with the same sized master cylinder, and the same size and number of caliper pistons, a larger rotor will require less pedal pressure for the same degree of stopping power. The job of the brake rotor, aside from providing a friction surface, is to absorb and dissipate heat. Rumor has it that objects of greater mass and having more surface area can absorb more heat and dissipate it faster than objects having less mass. Larger calipers, aside from having the ability to more evenly distribute the clamping force over the pad, have no benefit at all. If you use a caliper with larger pistons, you will need less pedal pressure to accomplish the same level of braking than you did before, but at the expence of pedal feel. If you have smaller pistons, you will have to use more pedal pressure to accomplish the same level of braking you had before, but now you will have a firmer pedal, and consequently, better modulation. Running big brakes on the street is stupid IMO. All it does is add weight. If small brakes will stop the car and don't overheat, why bother upgrading. For an autocross car, I don't see why the stock brakes wouldn't be more than adequate.....but there will come a point, where the rotors cannot dissipate the same amount of heat that they are being forced to absorb....ducting can only go so far on a solid brake rotor. For a Road Race or Endurance car, the stock brakes are nowhere near adequate. On my old VW, I had 10" vented rotors in the front and 9.4" solid rotors in the rear, with high dollar race pads....and ducting, and at the end of a 1 hour enduro race, the brakes were gone. When I pulled into the pits, the rotors had 2 large cracks through each one of them....that was on a 1800lb car. In conclusion....I agree with John's perspective for applications that do not see extreme temperature use....which the article did not discuss, but I disagree with John's perspective for applications that DO see extreme use, where lots of heat is generated. Big brakes are not to make you stop better, they simply allow you to stop more. I have 13" front rotors on my car and 11" rear disks, and I would be willing to bet a cold beer that in a series of threshold stops from 100-0, I could carry out 20 in a row, with less than a 20% increase in stopping distance from the first one. I would also be willing to bet another cold beer that a car (the same weight as mine) with stock brakes (using comparable pads)could not perform the same back to back series of stops and keep the distance within 50%. -
how do you tell what tranny you have?
lbhsbZ replied to echocluster@hotmail.com's topic in Drivetrain
did you bleed the clutch hydraulics correctly? -
Coolant temp sensor location, ok?
lbhsbZ replied to 80LS1T's topic in Gen I & II Chevy V8 Tech Board
Nope, doubt it. I just finished an install in a camaro, with the temp sensor in the head (mechanical) an it reads like it should. If the gauge reads 250, it means 250....something is wrong. -
Coolant temp sensor location, ok?
lbhsbZ replied to 80LS1T's topic in Gen I & II Chevy V8 Tech Board
Moving the sending unit doesn't make the engine run cooler....its kinda like lowering your oil temps by getting rid of the 300° gauge and installing a 250° gauge....all it does is make you feel better. Are you sure that the sending unit is correct for the gauge you are using? Try a cheapo mechanical gauge from auto-zone, they give halfway accurate readings. I haven't had any problems with the autometer temp gauges yet, but their oil pressure gauges suck. I've got 5 of them sitting on a shelf in my garage, obviously disconnected, that still read anywhere from 20-80 psi....the needles stick or something. One of them cost me a motor. I run 2 oil temp gauges and 2 water temp gauges now. -
1st track day with the Z (home early)
lbhsbZ replied to lbhsbZ's topic in Gen I & II Chevy V8 Tech Board
OK, I can try fattening it up a bit too. -
Or get a used junkyard motor for $100...of 5 of 'em (spares) and a paxton supercharger for $2500. You'll be into it less than you would a proper 400hp build, and you'll make more than 400hp....and parts are cheap...just go pickup another core. If you get real ambitious, spend $150 on a gasket set, rings an bearings to freshen up your junkyard motor.
-
1st track day with the Z (home early)
lbhsbZ replied to lbhsbZ's topic in Gen I & II Chevy V8 Tech Board
I've order a 185 and 195 high flow thermostat, the moroso restrictor kit, and a stock size crank pulley. I was looking at my radiator mounting this morning, and the way it sits, the lower core support crossmember blocks about 4 or 5 inches of the core all the way across the bottom. I'm thinking of cutting out the crossmember and lowering it so that the whole radiator core is exposed. The other option would be to try and tilt the radiator forward about 12 inches at the top, which may allow me to move the bottom upward enough to clear the crossmember. Other than that, I'm going to try and piece together a water squirter setup. I have to get it as good as I can before I head out to the track, then try all the different thermostat/pulley arrangments once I get there. EDIT: I removed the radiator and my oil cooler tonight, and did a trial fit with the radiator on a 45° angle (tilted forward). The griffin just barely squeezes through the hole in the core support. If I set it up like this, I can look through the grill and see the entire core. The ductwork will be very easy to make and effective if I do it this way. It moves the top of the radiator about 24 inches away from the engine, so I might be able to duct most of the air coming out the radiator too, through some sort of vents in the front 1/3 of the hood..(Ford GT style). This will allow me to utilize the entire radiator core, instead of having 1/4 of blocked off by the crossmembers, I can keep my electric fan, and it will only involve minor trimming of the original core support. I'm hoping that enough air will be forced through it to work correctly.....Pictures soon. I have to figure out the bracketry. -
My .02: Go to Home Depot and buy the Lincoln Weldpak 3200HD if you want a 110V welder. It is the exact same thing as the Lincoln SP135T, just with a different sticker on the side (this was confirmed by Lincoln) You can get them for under $400 If you want a 220V welder, get the Weldpak 175, which is the same as the SP175...I got mine out the door for under $600 I think. I've welded with 2 different miller 180 class machines, and I wasn't impressed. I felt that my first POS mig from harbor freight had better wet-out and puddle control. If you weren't in CA I'd recommend the Hobart Handler 187, but there is very little support for them out in CA and warranty issues may become difficult. For a hobby welder, the SP lincolns are fine. I haven't tried out the 140C or the 180C yet, but I highly doubt that they'd be much better than my SP135 or SP175, which I am VERY happy with....plus, if they break, I can go back to home depot and they'll give me a new one, no questions asked. Don't waste your money on the aluminum liner kit, and don't bother trying to weld aluminum without a feeder gun....its an excercise in futility. Buy a mig for steel and a TIG if you want to do aluminum
-
TonyD came over last week and bought my OBX from me....we assembled it with 6 washers assembled like the Quaife. I send him an IM and see how its working. My OBX made it through about 5 hard launches before it started banging with the old washers. Tony should know right away whether or not it will work with the 6 washers. You don't have to pull the center to install the clips, it's possible with the diff in place...I used a screwdriver to get the rings started crooked in the splines, then used a socket that fit nicely inside the splines to tap the ring until it seated in the groove.
-
1st track day with the Z (home early)
lbhsbZ replied to lbhsbZ's topic in Gen I & II Chevy V8 Tech Board
It is supposed to be the old style pump....although, seeing as how it's both cheap and chinese, it might be wrong. I'm not really sure how I'd tell unless I disassemble it, which should happen tomorrow. -
1st track day with the Z (home early)
lbhsbZ replied to lbhsbZ's topic in Gen I & II Chevy V8 Tech Board
Mine is pretty well broken in, Its had a hard life so far. -
1st track day with the Z (home early)
lbhsbZ replied to lbhsbZ's topic in Gen I & II Chevy V8 Tech Board
John, The sender is in the oil coming out of the engine, so that explains the high oil temps. Maybe I'll look into a bigger cooler anyway, or at least move the temp sender so I don't feel so bad when I look at the gauge -
1st track day with the Z (home early)
lbhsbZ replied to lbhsbZ's topic in Gen I & II Chevy V8 Tech Board
...or maybe I should just trade in my 300° oil temp gauge for a 250° gauge....that would solve the oil temp problem .....If only they made a 180° water temp gauge -
NZeder, the OBX that I had appeared to use the C-clips captured in the side gears....at least thats how I installed it. It wasn't much fun getting the clips out of the old one and into the new one, but I did it, and it worked. The axles still popped out like they were supposed to, so if you are using axles that capture the ring on the axle splines, you should think about how to either modify the diff or the axles, because I don't think you'll ever be able to get the axles out once you install them. The axles themselves weren't hitting the washers, axles were hitting the washer retainers. The problem was that the OBX washers, once compressed, didn't return to their conical shape...so they offered no preload on the assembly. Preload is what holds the 2 center washers in place, especially with 8 washers installed. With 6 washers, they are all held in place by the retainers.
-
You didn't put an OBX LSD in it did you....if you did, look through my recent post in this forum.
-
1st track day with the Z (home early)
lbhsbZ replied to lbhsbZ's topic in Gen I & II Chevy V8 Tech Board
OK, I played with it a bit tonight....I might be on to something. When I first fired the engine a month ago, I had a problem with a few of the headstuds leaking water past the threads....I pulled each stud out 1 at a time, cleaned, resealed, and reinstalled. During this process, some oil got into the cooling system while changing the studs under the valve covers. It was pretty obvious, because there were little oil droplets floating on the water under the radiator cap. So I squirted in a bunch of Dawn dish soap and ran it around for few days at work, then drained it, and refilled with clear water....which is still clear, so it led me to beleive that I had gotten all of the oil out. I stuck my finger in the radiator and felt a oily film all over the inside of the tank.....So I imaging that this same film may be on the insides of the radiator tubes, and the block and head castings....which would explain why nothing can transfer heat like it should......I think. Any Idea's to clean this? I have a pretty stiff degreaser called OilEaters that I was thinking of mixing up 50/50 with water and pouring that in, then run it around and get it hot a couple times with no thermostat, and then drain and flush it a couple times. I also ordered a set of the Moroso water neck restrictors and a stock sized crank pulley to try out. I'll pull the water pump tomorrow and compare the impeller to a stock pump....if it turns out to be a POS, I'll order a better pump too. I'm trying to cover all the bases, because I only have 1 more test day before the next race. -
1st track day with the Z (home early)
lbhsbZ replied to lbhsbZ's topic in Gen I & II Chevy V8 Tech Board
It wasn't to bad today.....kind of pleasant actually. It was about 90 with a nice breeze. Where should I mount the oil cooler? -
Front diff mount broken?
-
1st track day with the Z (home early)
lbhsbZ replied to lbhsbZ's topic in Gen I & II Chevy V8 Tech Board
How would that effect cooling? -
1st track day with the Z (home early)
lbhsbZ replied to lbhsbZ's topic in Gen I & II Chevy V8 Tech Board
I have not tried any other T-stats....I'm not sure how a hotter one would help, but I suppose it wouldn't hurt to try. As far as the waterpump...its a ProComp $65 unit. I'm going to pull it off tomorrow and yank the back plate to compare with an old used cast iron pump that I have. I haven't heard of any issues with the various aftermarket pumps out there though. Is anyone using restrictors in place of their thermostats? I still don't understand how the hell 10 1/2 quarts of oil with 2 filters and a decent sized cooler can go from cold to 285° in less than 4 minutes. After the first lap (about 1:30)...water temp was 210 and oil temp was 240, then things continued creeping from from there. I've never seen anything get that hot that fast. -
I tied up some loose ends yesterday and towed the car out to Willow springs this morning for a track day....the first time the car has run anywhere but our warehouse parking lot. I was amazed at how well the car handles...even when I got it sideways, it was easy to recover, much better than I thought it would be. 3 laps into it, the water temp was at 230 and the oil temp about 280, so I came in....Idling with the fan on didn't seem to drop the temps at all. I went out for 1 more session....3 or 4 more laps and then pulled it on the trailer because everything was cooking again. Now the fun part: Diagnosis!!! Here's what I've got: 24x19 Aluminum Griffin Radiator Aluminum Cheapo water pump 165° t-stat 12x9 stacked-plate style oil cooler (10 quarts of oil in the system) 14" 3400 CFM electric fan (moves lots of air) Undersize crank pulley. Est. HP output: 520 crank. Willow springs is at about 3000 ft, so it probably wasn't making that much power. Mixture was 13.5-13.9:1 according to my AEM wideband AFR gauge, and the plugs looked good, so I wasn't running lean. I can understand if maybe the radiator is too small, or needs ducting, but in these cases, the temp would come down pretty quick idling with the fan on, and it didn't come down at all...so while ducting the radiator may be an issue, I don't think it will help out quite yet. I was thinking that maybe the undersize crank pulley is just driving the waterpump too slow, but I've never seen a case of that before so I don't know what symptoms are. I'm sure the thermostat is working...(if it didn't melt) because you can feel the temp change in the hoses when it opens. Any other ideas?
-
Yeah, I know what you mean about the gears....I just built a mild (325hp) street motor for my buddies '67 camaro....I also swapped out the powerglide for a TH350. I was scratching my head for a while after I got it together and drove it....until I realized that with the Powerglide, GM put 3.08 gears in it. No wonder it doesn't have any kick to it.
-
PLEASE HELP.need info on 85 300zx v8 swap
lbhsbZ replied to a topic in Gen I & II Chevy V8 Tech Board
Search, young grasshopper....the answers are out there -
I'd just pick up a new balancer for the time being, and double check TDC so at least you'll know where the timing is set....thats probably why it has no power....because you have no idea where the ignition timing is actually set. Go for total timing between 38 and 42 degrees. And with a victor junior manifold, that thing won't make any power until you hit about 4000rpm. If it doesn't have a super lumpy cam in it, the cam is probably done making power by the time the manifold starts making power. Maybe try a dual plane manifold on it if the cam sounds pretty tame, I bet that will wake it up quite a bit too. I don't know what kind of carb you've got, but I've got an edelbrock performer manifold for a Q-jet that I'll sell for $50+shipping if you want to try it out.