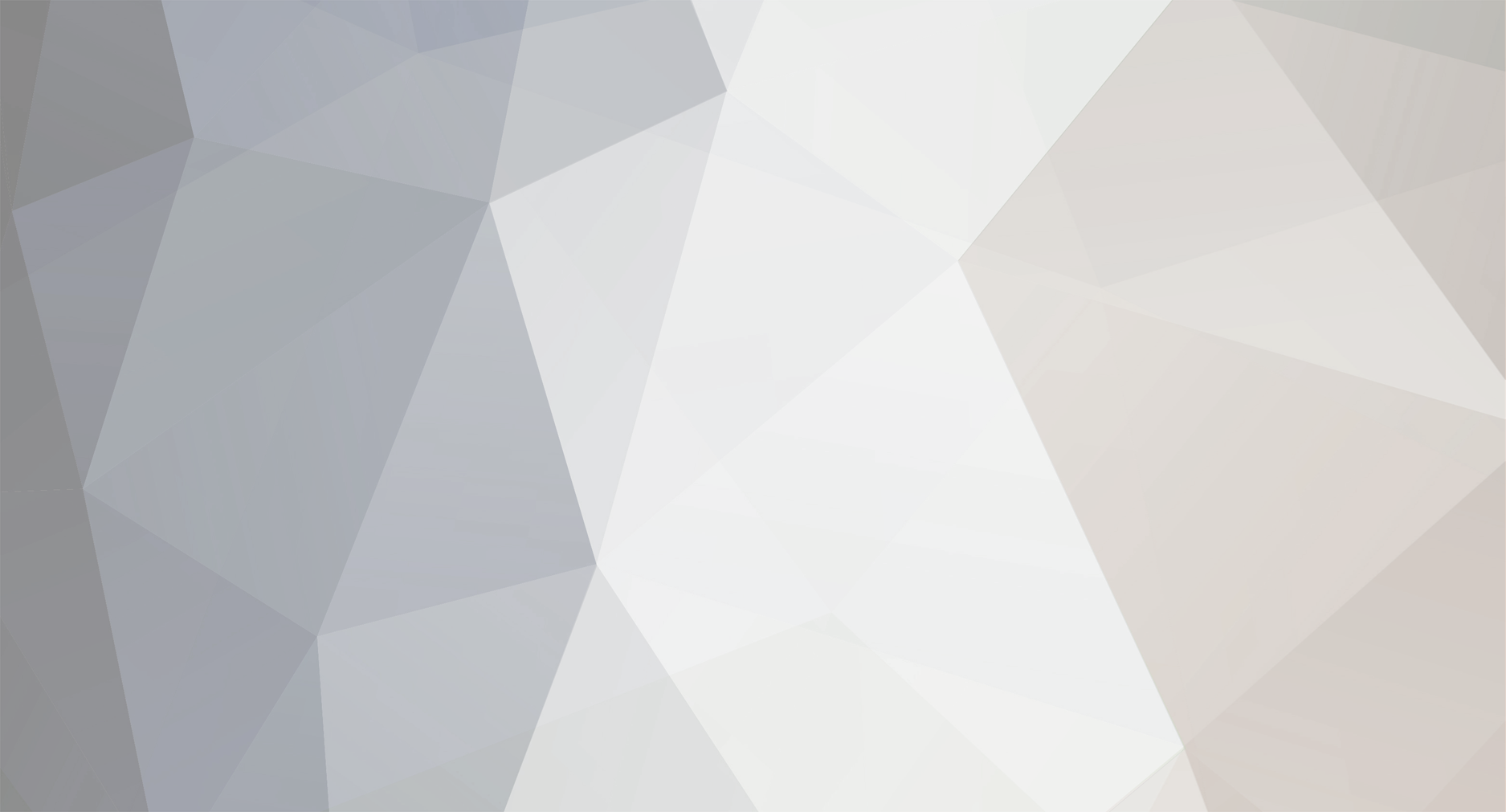
lbhsbZ
Members-
Posts
409 -
Joined
-
Last visited
-
Days Won
1
Content Type
Profiles
Forums
Blogs
Events
Gallery
Downloads
Store
Everything posted by lbhsbZ
-
IMO, the washers shouldn't be loose. I flipped the washers around in mine to get the largest stack-up height...which I interpret as preloads, then used a long pin to keep them aligned while I bolted the diff together. I reused the stock washers, but I'll pull it apart and check everything out after my first event, and replace if necessary. I took the car for its first ride today, and I experienced something that I've never experienced before with a RWD car. Coming out of a corner, I stand on the throttle before I get it straight and the back end starts to step out...pretty far, then, instead of spinning, it sharply snapped back, glued the tires to street and took off..with almost no driver correction. In my truck (with a clutch type LSD), if I tried that I'd be all flipped around. The 315/35/17 race rubber in the back probably has something to do with the way the car acted, but whatever it was, it works awesome. I didn't notice any roughness or noise from it, but I can't hear much with my exhaust.
-
Well, my experience is that removing the thermostat will only make it warm up slower, but the temperature keeps rising. Removing them is a band-aid attempt to fix another problem IMO. either way, make sure that any air near the radiator gets channeled through it, and you'll probably lower your temps considerably.
-
I found a 19x24" griffen aluminum radiator for $180 from Summit. Its about the biggest thing I can imagine fitting in the Z. Its about 3 inches thick, and should do fine. I learned a lot about engine cooling from my old VW GTI. I was able to double the engines horsepower without upgrading the radiator...and it worked once I figure out how. You have to keep a thermostat in the engine, don't take it out. While it may solve one problem, it will cause plenty more. You can also make a stock radiator much more effective by ducting it. Build a 2 or 3 inch box around it and mount it to the front, maybe even angle the sides of the box to make it like a funnel. A 19x24 radiator has a surface area of 456 sq/in. If you make a funnel on the front of the radiator, and angle the sides so that the frontmost part is 20x25, you are now taking advantage of 500 sq/in worth of air, thats almost 10% more air going through it. Air will take the path of least resistance, so once air gets near the radiator, it has to be forced through the radiator, instead of letting it leak around the sides, top, or bottom. On my VW, I made a box out of 3 inch wide sheet aluminum, with no angles, just straight forward, and it dropped my water temps on the track by at least 20 degrees, and kept it there as long as the car was moving. when is your car getting hot....idling, sitting in traffic around town or when you're running it hard?
-
Help! oil gallery expansion plugs
lbhsbZ replied to spineless's topic in Gen I & II Chevy V8 Tech Board
I assume you are talking about the plugs that go behind the cam gear. Go find a 1/4NPT tap and some threaded pipe plugs. The factory uses expansion plugs and stakes the block to make sure they don't come out, but the threaded plugs are a better solution, and easier to deal with when it comes to the next teardown. Tapping these holes should be standard procedure with block work at most machine shops. -
I finally got most of the bugs worked out and took a slow ride to the end of the block and back on Saturday. I buttoned up a few more things and took it down to the shop this morning and gave it a work out....until the Sheriffs showed up. I sweet talked them for a bit and let one of them drive it....they won't be giving me any more trouble. The car ran good, right off the trailer, I got it straight and put the pedal to the wood. It stepped out a bit, but snapped right back and hooked up. I was able to run it almost to the top of 3rd before getting on the brakes. The brakes suck. I have some vacuum issues that I need to figure out. The cheapo OBX diff (surprisingly) seamed to work very nicely, made the car very controllable, even coming out of a corner while mashing the pedal. I took a few corners pretty hard, and it stuck. The car is fast, but not as nutz as I expected. I was shifting at 6K, but it was still pulling...hard. I've got the rev limiter set at 6400 for now, but the motor should be able to do 7500rpm safely. Its running pig rich right now, as evident by the sides of the transmission (behind the header collectors) that are pitch black, covered in soot. I'll get the wideband A/F meter installed this week and get the jetting right, and it should pick up a few more ponies. The water temp went to 180 and stayed there, when I turned the fan on, it pulled it down to 165. I got the oil temp up to about 180, but it wouldn't get any hotter than that. The only problems that came up was an oil leak from my remote filter adapter, which was in questionable condition to begin with, and the battery went a little too dead and needed help from the charger to fire it up once. Of throttle, its got a pull to the right, but on throttle it goes straight as an arrow. I'll play with the alignment, but I kind of like it the way it is. None of my buddies showed up so I didn't get any video...but soon hopefully. I'm calling the project a success. I was very impressed. Gotta go see when the next track day is. Here's some pics of the (almost) finished car. The rear bumper has to go, and it needs a few more greasy handprints in the primer, but those things can wait. It was a rush to finally drive it. And I'm glad I can now take a much need break from it for a little while. Special thanks to: JohnC at BetaMotorsports Stuart at Technafit Tony at TG's machine shop --without whom I probably wouldn't be done yet.
-
Well, I decided to pull one stud at a time, clean the threads and reinstall with a better sealer. I ended up wire wheeling the threads until all the black oxide coating was gone and they were shiney clean silver metal. Then I shot some brake cleaner in the hole, dried it with air, reinstalled the stud and torqued the nut. I did this with each external stud (not under the valve cover). I pulled about 7 of the studs under the valve cover, and they looked good. The Teflon sealer had coated the threads nicely and appears to have sealed. So I cleaned and resealed them and reinstalled. I let it sit about 24 hours and then refilled and pressurized the system. It held 20 psi for 2 hours, so I think its good. I'll keep an eye on it though.
-
What blowproof bellhousing to run?
lbhsbZ replied to HarrisonTX's topic in Gen I & II Chevy V8 Tech Board
I'm running the McLeod bellhousing that I got from Speedwaymotors.com. I had to do a little trimming to make it clear my longtube headers, but it clears the firewall fine with the scarab setup. I also used the pull type slave cylinder and it works well. -
I read through that thread, and I agree with most of it. Stopleak is not the answer. There has to be a better way. The only thing I can think of is that the surface treatment on the ARP studs is too smooth and polished, and maybe that prevents the sealer from adhering properly to the stud. I will remove them one at a time and replace them after sandblasting the threads and applying a high quality silicone sealer. I'll post my results later in the week.
-
I run the Tech Support, Quality control, and caliper production dept. for Centric Parts. Its a 9-5 job, so I've got some time after work to get MY work done. We've also got quite a few connections through work to get parts quick. JohnC did an awesome job getting me stuff when I needed it. The car, when its done, will be wearing some nice big BetaMotorsports stickers. I couldn't have done what I did to the car without the help I received from a few select vendors.....and my machinist, who pissed me off in the beginning but has showed up at the house the last few nights to turn wrenches, weld, whatever needed to get done. JohnC, I thought about it for about 2 minutes last night....I could have resealed just the leaky studs and been down the road, but the last thing I wanted was for one of the studs under the valve cover to start leaking and contaminate the oil...I figured it would be best to admit defeat now, instead of later on this weekend, and then go out with solid equipment for the next race.
-
Can you get some more pictures of the exhaust....preferably the rear section? What kind of ground clearance do you have underneith the mufflers?
-
I'm not racing this weekend, I'm going as a crew chief only for our team. So instead of driving the fastest thing I've ever sat in with 4 wheels, I'll spend the weekend drunk, turning wrenches, playing with strippers, and whatever other trouble I manage to get into....so it won't be all bad, just kind of a bummer for me right now. I was really looking forward to running the Z.
-
Well, I lost the bet. I got home from work tonight, and the garage floor was covered with water. One of the pipe plugs in the right cylinder head was leaking....no problem. I tightened it up a few turns, the pressure tested it to make sure it was fixed....and it was, but now there were a couple more leaks. Water bubbling out around 5 of the head studs. I used Permatex Teflon thread sealer liberally on all the head studs. There is no reason why they should leak. I could just yank the studs, butter them up with Silicone, and reinstall them, but if 5 are leaking for no reason, there's no telling whats going to happen with the others, so I'm going to yank the heads, re-chase all the bolt holes, clean all the studs, use a better sealer, and put it all back together, which I don't have time to do before the race, and I can't get another set of headgaskets tonight. Otherwise, the car is ready to hit the track. If I didn't have as much money in the motor...I'd do the band-aid fix, but I can't afford to build another one of these, so I'll do it right. I lost my dollar. Dammit.
-
Grease seals for 300zx 5 lug front hub
lbhsbZ replied to lbhsbZ's topic in Brakes, Wheels, Suspension and Chassis
Sorry, I didn't have time to search....got 2 days left to button this thing up. The seals I'm using are what the BCA catalog lists for the 300zx....and they don't work. -
ITS ALIVE!!!!! And it sound @#$%#$ mean! Official Update: All the fluids are filled, we've got a bit too much fuel pressure, so I'll have to pick up a regulator in the morning. The suspension is set right, I'll cornerweight it tomorrow night just to be safe. I've got the belts in, mirrors on, everything under the car is bolted down...just the little piddly stuff left. I've got another few hours tonight, so I hope to get most of the nut & bolt stuff done. Practice starts on Saturday morning, but we usually leave friday morning and get there early to set up the paddock. I wish I had more time, but it looks like the maiden voyage might take place around our warehouse on Friday morning, and then its off to the track. I think I made it. Pictures later tonight.
-
Grease seals for 300zx 5 lug front hub
lbhsbZ replied to lbhsbZ's topic in Brakes, Wheels, Suspension and Chassis
I've got to race this thing on Saturday.....help me out guys. The 300ZX seals are loose in the hub and don't fit over the spindle. The 240Z seals don't fit in the hub. -
I can't wait till its over.....I need a break. This is too much like work....gotta go git on it again in about 30 minutes...hopefully I'll make it to bed before 3:00 tonight.
-
Brake hardlines...problems
lbhsbZ replied to lbhsbZ's topic in Brakes, Wheels, Suspension and Chassis
Problem solved....I didn't have time to post last night. I had a buddy come by last night who has several contracts to make brake lines for limited run vehicles. He took one look at my seemingly perfect flare and told me what the problem was. My tool wasn't making a big enough bubble in the line before I crushed it into the flare. We tried a bunch of samples last night with my old tool, trying different stickout and everything, and nothing could duplicate the bubble made by the good tool. Maybe mine is wore out, I dunno. I haven't used it all that much. He brought his $400 flaring tool over, which is cake to use, doesn't garf up the line where grab it, and make huge bubbles. I used that to remake all the lines again and I've got a solid pedal with no leaks. -
Had some serious brake line issues on Sunday....every flared line connection leaked....bad. I remade all the lines and they still leaked. Today at work I made some calls and had Mr. Brakeline himself come by the house tonight....took one look at my flares (which looked perfect to me) and said they were crap.....told me to throw my tool in the trash. I used his $400 tool and redid the whole car again...now they don't leak, and I've got a solid pedal. I changed the booster tonight as well, and finished hooking up the sway bars and rear axles. Tomorrow I'll do the wiring and exhaust, and hopefully I'll be able to fire it up. 3 days left
-
Brake hardlines...problems
lbhsbZ replied to lbhsbZ's topic in Brakes, Wheels, Suspension and Chassis
I agree. According to the ridge on the die, I should have about 1/8" stickout. In the past, I've always gone with stickout the same as the diameter of the tubing. I tried both ways, and they both leaked. I ordered a new flare tool, 50 feet of line, a few pounds of TEEs and line nuts, and 2 more master cylinders (The fittings are in so tight I can't get one of them out). I'm gonna sit in the garage all night tonight and make lines till I figure out why they are leaking. -
So in my effort to get the car done by next weekend for the race, I decided to bleed the brakes today. I had fluid leaks everywhere. Both fittings at the master leaked, both the front and rear TEEs leaked, the only things that didn't leak were my prop valve and the connections at the brake hoses. I remade all the lines at least twice, and replaced all the TEEs a couple times. I can't see anything wrong with them after disassembly. I'm using bundy-flex, or soft steel line, not stainless. Here's my flaring procedure, let me know if I'm doing something wrong Cut line with tubing cutter Clean up hole with tapered reamer, and deburr edge with file Clamp line in tool with 1/8" stickout, and make bubble flare Remove die and make inverted flare I tried not crushing the flare down too hard, and then crushing the hell out of it, both ways leaked. I'm running out of patience with these lines...but regardless of whether or not I make the race (its looking like I'm not going to make it), how the hell do I make the lines stop leaking?
-
UPDATE: Things are going well. Last night I made new hardlines for the front brakes because they were kinked. Today I rebuilt the rear suspension, welded on new spring perches, built a R200 diff with a Quaife and put that in, machined and welded on brackets for the rear calipers, and bolted everything together in the back of the car. Cut out the trunk floor and made the fuel cell hangers and installed the cell and plumbed the fuel system. I'm taking a break now to pick metal splinters out of my hands. Only problem I've encountered today....my new driveshaft is too long. I have to get it shortened and rebalanced on monday. Tomorrow I'll finish the wiring, get an upper radiator hose, and figure out another alternator bracket. Monday, pick up banjo bolts for the rear calipers, get driveshaft shortened, get correct lug nuts and a few more studs (I seem to have lost them), fill all the fluids and fire it up. I'm going to go register it monday morning, so if all goes well, I can drive it to work on tuesday. 5 days left (I have to leave on Friday morning) Oh, another problem I need some help with. I sold my dolly, and planned on borrowing my buddies trailer...but he sold it. I need an open trailer, preferably with brakes...in SoCal. If anyone has one for sale reasonably, lemme know. If I can't find one...I'll guess I'll just drive the car to mexico for the race....that should be worth another dollar. More pics tomorrow. Special thanks to JohnC at BetaMotorsports all his good advise and for not letting me walk out of his shop without a set of 5 inch threaded shock collars...even though I didn't want them. turns out I needed them for the rear. John, I'll be sending you another check Also, special thanks to Stuart at Techna-fit for all my -AN and brake lines, If anyone needs any custom -AN lines or SS brake lines, give him a call at 310-212-5051
-
I want to point out that this also works for the Tremec TKO gearboxes behind a SBC....and that the Wilwood SC is overpriced. Summit has a HOWE pull type slave for about $45....the Wilwood is almost twice that price. I used the HOWE and didn't have to fab up a bracket for it. There is an ear cast into the side of the case that was the perfect distance away from the fork.
-
I've got the TA185 and I'm very happy with it....more features than I know how to/care to use at this point, and takes care of everything I need to do.
-
Made some good progress tonight. I finished up the front suspension and set the car down on the ground.....its looowwww. Gonna have to raise it an inch or so I think. Got all the brake hard lines plumbed. For the clutch slave, I used a pull type like in the Sticky in the driveline forum, but I used a HOWE unit from summit. Same basic specs but 1/2 the price. Drilling and cutting the fork sucked. I also ended up cutting out some of the firewall/tunnel to make it fit. Also got all the braided lines hooked up under the hood. Here's some pics from tonight. I might make it.....8 days left