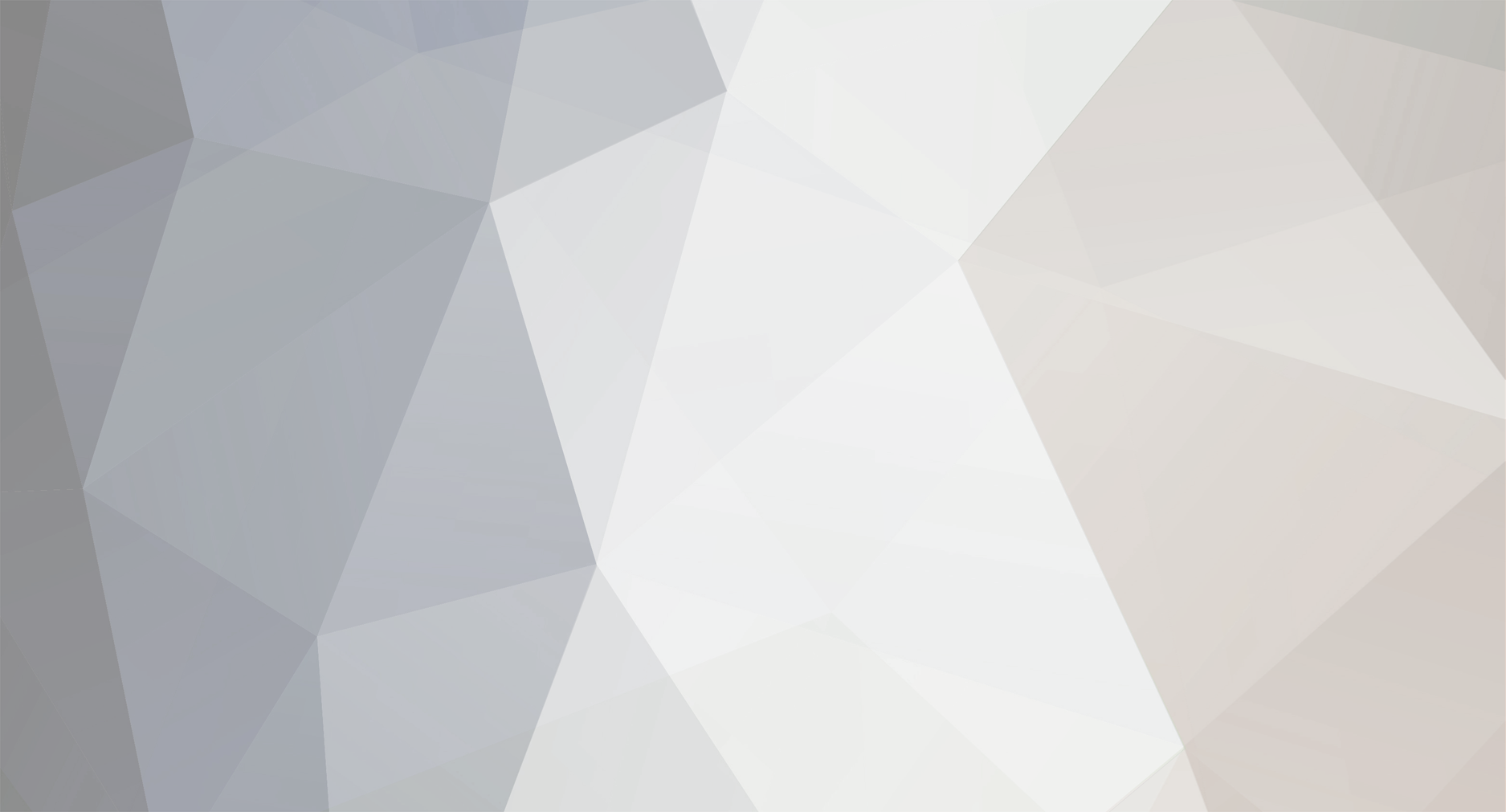
Pyro
Members-
Posts
1189 -
Joined
-
Last visited
-
Days Won
3
Content Type
Profiles
Forums
Blogs
Events
Gallery
Downloads
Store
Everything posted by Pyro
-
Preparing 78 280z for Turbo Swap, Reusing stock block
Pyro replied to Challenger's topic in Nissan L6 Forum
option 4) add megasquirt to the stock N42/N47 combo with 360cc to 400cc low impedance injectors. Then add turbo later. why install a 25 year old efi system? get a good system with properly sized injectors and have ignition timing control. Just need to swap the head to get the compression down to stock turbo levels, as the n42 already has dished pistons. match the head gasket to the block (use a head gasket for a N42) if you plan to use stock boost then the stock N42/N47 compression (8.3:1) will be just fine. 8.3:1 is actually nicer for a turbo if you keep the boost under 10psi or if you plan to add a bigger cam (msa turbo stage 1 cam). you will need a stronger clutch (240mm) for the turbo. I use a bell engineering fmu on my turbo using the stock 76 efi system (na injectors with locked out ignition) and run up to 14 psi of boost. Takes a mean fuel pump to make that kind of fuel pressure (110 psi) with enough volume. I use a bosch 044 pump. Plan to go megasquirt as soon as the stock efi system goes out, been waiting for over 5 years now. hahaha -
310wrhp in a 2450 pound car (with driver) would trap at 117.5 mph which is good for a mid to high 11. But traction will be an issue.
-
350hp at the crank is possible with 20 psi of boost, stock cam, and stock head. in theory, you would need to run 26.5 psi of boost on an otherwise stock L28 turbo engine to make 350hp at the wheels. So, to run a more reasonable amount of boost, you will need more cam, some head work, and more rpms to get 350hp at the wheels. And a setup like this would need a non-stock exhaust turbine (like a T3 stage 3 or 5) which makes full boost later (3500 rpms) and makes power out to 6500 or even 7000 rpms. or maybe lower your goals a little. run a msa turbo stage 1 cam, stage 3 t3 turbine, to4e-50 trim compressor, DIY bowl smoothing around the valves seats, a bar and plate IC, run 17 psi of boost, and make around 300-315hp at the wheels (360-375 crank). 310 rwhp in a 3000lb car is good for 110 mph trap speed in the 1/4 mile which should be a low to mid 12 second run with good traction.
-
well, a "50 trim" indicates it is a T04E compressor. The T04B come in H,S, and V trims. You will know if it is T04E compressor when you try to mount it. The t04B fits without a spacer and the t04E requires a 1/2 inch spacer. Yes, I recommend using the stock T3 housing and wheel with a stock cam. The quick boost and restriction at the higher rpms matches the stock cam well. FYI, a stock turbine will do well with 3 inch exhaust. 15 psi of boost with get you about 250hp at the wheels (300hp crank) with a stock cam and cylinder head. 20 psi to get 300hp at the wheels or 354hp crank I also recommend that you use a NA cam from a 75 to 80 L28. Worth a few more ponies and a few more rpms. (270 rwhp at 15 psi with another 500 rpms of usable rpms)
-
well, a little more to it than measuring a 2.5" inlet and 2" outlet. Plus E's and B's come in various trims which greatly affects the performance. And the turbine (hot side) is just as important. you need to take it apart to get good measurements. FYI, stock cams will work best with a stock 280zxt turbine (t3, ar 0.63)
-
The only thing in the kit that is worth anything is the speedo cable. And that is good only if you use the stock speedo. the engine mounts are easy to make. just make them to the jtr drawings the trans crossmember is a real piece of junk. I have made 3 or 4 over the years and they look much better than the jtr design. I make them so the trans crossmember mounts to the body on the vertical wall of the trans tunnel instead of the floor pans. this makes it much stronger and much smaller (lighter) and doesn't hang under the frame rails. I say make your own kit.
-
if the cam is big enough then 11:1 cr isn't a problem with 93 octane. a 292H with run with pump gas and 11:1 cr in a z (light load). with 91 octane.........If you are going to run a 268H then stop at 9.5:1 with iron heads and 10:1 with aluminum. or 9.75:1 with iron and 10.25:1 with alum with the 270H, or 10.0 w/fe and 10.5w/al with the 280H. The 280H would need a 3.90 gear and a T5 and would be fairly streetable. a 292 is a little lopey for a daily driver. you could even get a 280H cam and have comp grind it on 112 or 114 lsa to smooth out the idle, extend the power band, and drop cylinder pressure. they do custom grinds for an extra $50. good heads do well with wider lsa, due to good intake flow. dynamic compression ratio is what you need to be concerned about. This is mainly determined by the static compression ratio and the intake closing point (cam timing events).
-
my 240 would trap at 120mph (11.7 et) with a 11.1 cr 350 (362 cid) with 200cc dart iron eagles, compcam 292H, long tube headers, dual 2-1/2 exhaust, T5, 3.90 r200, hei with msd conversion, rpm intake, holley 3310 750. then would trap at 135 with a 250 shot of N02 added to that (10.7 et). but when I first took it to the track it ran a 12.7 at 110 using a 11.1 cr 350 (362 cid), ported fuelie heads, compcam 292h, shorty headers, hei ignition, rpm intake, 3310 holley, single 2-1/2 exhaust, T5, 3.90. The car picked up speed and lower the et over a few years of modifications. good heads and the long tube headers with dual exhaust really made big changes. enough power to trap at 120 is about the max the stock axles and R200 can take. If I had to do it all over again, I would had left the car in the condition I took it to the track for the very first time. it got too crazy, broke too often, and became a trailer queen. if you want to drive it daily, then a 3.54 gear and a T5 will work nicely. A set of edelbrock performer heads, a regular edelbrock rpm intake (not air gap), a compcam 268h or 270h is good enough, and a holley 750. should be able to get into the 12's with good traction (new tires). not the worlds fastest car, but a fun daily driver.
-
94 mph trap with a 2700 pound car takes 175hp 97.5 mph trap with a 2700 pound car takes 195hp. stock gearing is a 3.36. old fuelie heads need about 38 total timing. rev it up to 4500 and set the max timing to 38 without the vacuum advance connected. what valve springs are in the head? diameter? installed height pounds? pounds at 0.500" lift? 195hp @ 4500rpm at the wheels is about 235hp at the crank, which is about right for an almost stock cam. what is the engine vacuum at idle? this is an indicator of the cam size. The first thing I would add is a 268H compcam and install a 2400-2600 stall. Then install some better heads, rpm intake, and a holley 3310 750. a 280H or 292H compcam to make max power, but a 3000 stall and a 3.90 gear would be required with the bigger cams. a compcam 268H with a 2400 stall should get you to 275hp (220hp at the wheels), which should net a 102mph trap speed which is good for a very low 13. add some better heads and add another 30hp and trap at 105 which should be good for a 12 with good traction. A T5 would be a nice upgrade but shift it slow.
-
You would get a better response from a circle track or dirt track forum. But I'm sure there are rules you need to follow. but in general, to complete with bigger engines, you will need to use more gear and more rpms. lots of duration (300+ advertised), solid lift, very narrow lobe separation, as much lift as the rules allow or the heads can take, and a good valve train for high rpm.
-
what are the racing rules? lots of rules for different classes. can you use aftermarket heads? can you use a 4bbl carb? are you limited to the amount of valve lift and compression ratio? will using a smaller engine allow you to weigh less? there are plenty of "circle track" cams out there. They typically have very narrow lobe separation angles (104 to 106) and some have extra low lifts to meet the "low lift rules". compcams has a few pages of circle track cams. different cams for different tracks and different size engines and different rules.
-
v8 bogs, fuel pressure regulator?
Pyro replied to Wilson_WWSC's topic in Gen I & II Chevy V8 Tech Board
a bog typically means more accelerator pump is required and/or more ignition timing. -
keep moving the trans over until the shift fits. you have the wrong starter. the starter you have fits the 168 tooth flywheel. I can tell from the diagonal bolt pattern on the starter. you should be using the 153 tooth starter which has the bolt pattern on the starter straight across from each other. the block will have both starter patterns.
-
here is a nice table to convert 1/8 mile to 1/4 mile times. http://www.empirenet.com/pkelley2/eight-to-quarter.htm I would expect 9.3 second 1/8 mile times with your current setup. Maybe more timing will get you there.
-
if you are running stock 79 non-turbo compression ratio (8.3:1) then you can run more than 18 degrees of timing with stock boost. try 26 locked. use the vacuum advance as normal. for 10 psi, I would use around 22 degrees. but 18 degree is too low. 8 more degrees will make it run quite a bit faster. I would use 18 degrees on a 8.8:1cr engine with stock boost (81 to 83 non-turbo setup). you should also consider installing a MSA stage 1 turbo cam. It would work better with the higher compression and make the engine less likely to detonate.
-
must be a misprint. This is from aeromotive's website; "The filter element used on the inlet side of any Aeromotive fuel pump may be no finer than 100-micron (no number smaller than 100), with a surface area of 60 square inches or more." http://aeromotiveinc.com/2010/01/fuel-filtration/
-
if you plan to use a stock cam then use a stock turbine. the stock cam power band matches the spool of the stock turbine very well. If you add more cam then open up the turbine to a stage 3 or 5. a stock non turbo cam is a nice upgrade for stock turbo engine (gives about 500 more rpms). as for the compressor. use a T04e-50 trim. use a water cooled center section because it has a better bearing. external wastegate with 3 inch exhaust would run well for a 275rwhp engine. plan on using 15 psi of boost to make that power with a stock cam. need to add more fuel with more boost. so an aftermarket efi system will be required or a FMU.
-
Yes, 100 micron before the pump.
-
pumps get loud when they don't get enough fuel. if you plan the run the aeromotive pump on the street then you must use the motor controller. the aeromotove pump will burn out running full speed all the time. I recently installed a bosch 044 and it works nicely.
-
Try porting the wastegate exhaust port on the turbo. enlarge the exhaust port a little and smooth out the sharp edges leading to the exhaust output with a die grinder.
-
I run 28 degrees total with 13 psi (7.4:1 cr, msa turbo stage 1 cam) For 18 psi, stock cam, and 7,4:1cr. I would lock the ignition at 20 degrees and try that first. Add more if you can, I would think 24 would be about max.
-
Hybrid Turbo - T04B Compressor, 0.70 A/R
Pyro replied to Ineptitude01's topic in Turbo / Supercharger
I use that compressor. t04b-h3. but use a Stage 5 t3 turbine. that compressor will surge on a L28 if you make boost too soon in the rpms. And a stock turbine will do that. (make low rpm boost). So either swap the h3 for a v1/v2 or s trims, or open up the turbine to a stage 5 to delay the boost. But, a stock cam will only make power to 5000 rpms and the stage 5 t3 turbine makes full boost around 3500 so this will make a short power band. The stage 5 turbine really requires a bigger cam to extend the power band out to 6500. I use the msa turbo stage 1 cam (260 intake/250 exhaust 114 lsa) and it seems my engine makes peak power around 6000 - 6200 rpm and pulls hard to 6500. boost starts a 3000 and hits full boost (12-14 psi) by 3500. The H3 compressor is better for a 3.0 liter engine that is set up for high rpm power. if you plan to use a stock cam then change the compressor to a v1/v2 or s trim. you will be happier. -
always check the rotor to lid clearance on the melling pumps before you use them. They have a habit of making them too tight which causes lots of extra drag which eats up the drive gear on the crank which fills the oil with metal which kills the engine bearings. simple to fix by hand sanding a little off the tops of the rotors.
-
use a stock efi pump with a return style fuel pressure regulator that can be adjusted down to 3.5 psi. aftermarket pumps (holley, mallory, carter, ect) tend to wear out after 1 to 2 years. The brushes on the motor wear out. The stock efi pumps last for years and years and years. Plus are quiet. So, spend your money on a good return style fuel pressure regulator (Aeromotive, summitracing .com) and use a stock efi pump (new or used).
-
if your pump is noisy then I bet the intake tube on the tank is partly clogged.