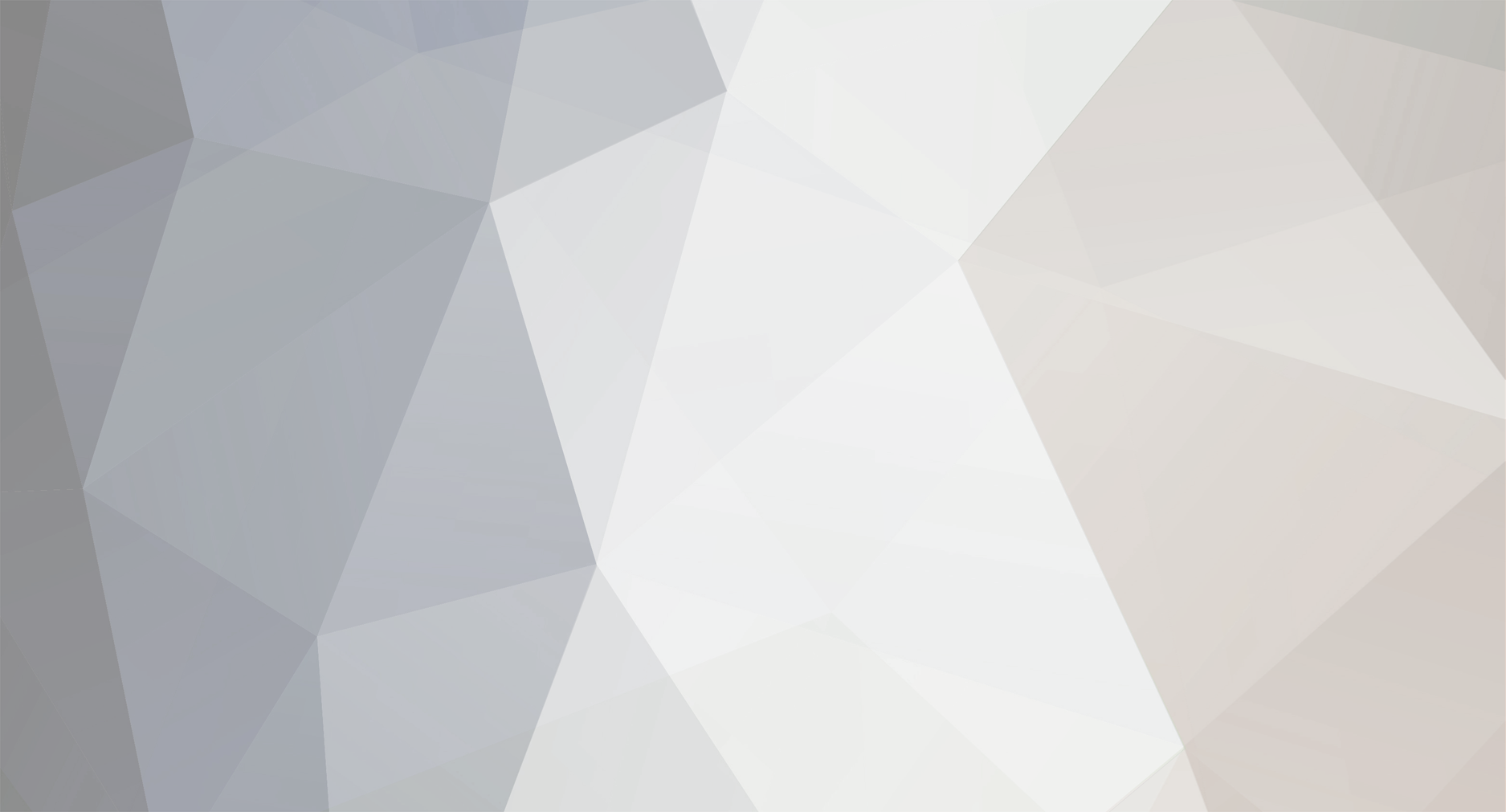
Pyro
Members-
Posts
1189 -
Joined
-
Last visited
-
Days Won
3
Content Type
Profiles
Forums
Blogs
Events
Gallery
Downloads
Store
Everything posted by Pyro
-
You need around 60 psi of fuel pressure with 7 to 8 psi of boost with a na efi setup. A 8:1 fmu with 8 psi of boost makes 64 psi of fuel pressure (8 x 8 =64). I have seen adding 50% of the static fuel pressure to the fmu pressure result, but I haven't seen that in practice. The stock pump will quit flowing around 65 psi always, so it acts like a fmu all by itself. The stock pump will max out around 60 or 65psi with enough flow. Fmu's cost about 100 on ebay. bell engineering makes an adjustable fmu for 225.00
-
Use a 8:1 fmu. A 6:1 fmu will not add enough fuel.
-
Trying to ascertain what carb I should be running on SBC
Pyro replied to tommott77's topic in Gen I & II Chevy V8 Tech Board
Use a holley 3310 with a regular RPM intake (with square flange carb, not RPM air gap). http://www.summitracing.com/parts/HLY-65-3310/ -
use a cam out of a 75 to 80 L28 engine with a N47 head. These are the biggest internally oiled cams. I started with a stock turbo cam. It was ok for a stock turbo but ran out of rpms too early. So I put in a msa turbo stage 1 cam. The valve train was a little noisy for my taste and the power band a little too high. So after a few years of using the msa cam, I switched over to a stock non-turbo cam and I really like it.
-
Another option is to just add the turbo stuff onto your 75 engine. The 75 engine has dished pistons and 8.3:1 cr. You can drop the compression of the stock 75 engine to the stock turbo level (7.4:1) by putting the P90 head onto the 75 block. Use the head gasket that matches the block year. If you don't, then it will over heat. then add a megasquirt 2 efi system. or you can install a 8:1 fmu ($100 from ebay) and lock out your ignition mechanical advance curve and set the timing to 25 degrees. This will allow you to use all the stock 75 efi stuff (intake, injectors, ecu, ignition, engine, head....) works OK to 8 psi of boost. If you plan on using stock boost, then I would use the 75 engine with the turbo bolt on stuff. A Megasquirt efi system would be best, but a cheap and easy to install FMU would get you boosting much sooner.
-
I found the stock non-turbo cam works well as a "performance cam upgrade" for a low rpm boosting turbo setup. The stock non-turbo cam has 8 more degrees of intake duration, as compared to the stock turbo cam, which is good for about 1000 rpm more of power band.
-
my 71 240 with a 350 with T5 ran a best time of 11.7's at 120 mph on the motor and 10.7's at 135 with NO2 (200hp shot). And used a MT drag slick with a r200 rear end (3.90). The trick is to shift it slow, don't bang the gears, and go easy on the clutch drops (no driveline shock). at the drags, I use a brake line lock at the starting lights and slip the clutch a little to take up all the driveline slack before dropping the clutch at 5000 rpms. best 60ft was 1.5 seconds with 26x8 inch MT drag slicks. Then shift it slow for each gear change which makes the car looks like a porpoise going down the track. also, avoid full power in 5th.
-
that is not a turbo cam. has narrow 110 lsa and more exhaust than intake duration. the amount of overlap a turbo engine can take depends on the restriction in the turbine. Small restrictive, low rpm boosting turbines can't handle any overlap. A big, high flow, higher rpm boosting turbine can handle more over lap. at what rpm does you engine start to boost and make peak boost?
-
your need to do 2 things. lock the mechanical advance in the stock distributor and set the timing to 30 degrees at idle. You will need to disassemble the distributor to get to the mechanical advance system. then there are multiple ways to lock the mechanical advance (wire, glue, welding...) FYI, stock initial timing for a turbo engine is 20 to 24 degrees. get a 8:1 FMU off ebay ($100). When you add boost, you also need to add fuel. The fmu will increase fuel pressure while on boost, which makes the injectors flow more gas. so at 8 psi of boost the 8:1 fmu will make 64 psi of fuel pressure. This is about all the stock efi pump can handle. this will work OK for stock boost (8 psi) and 7.4:1 cr.
-
That is a good carb. I use on on my 454 in my 70 c10 and my 350 in my 71 240. if the secondaries aren't working then either the big diaphragm is busted (or not installed right) or the oil ring where the diaphragm housing bolts to the main carb body is leaking. an easy fix. I would try fixing what you got first. for 20 bucks you should be able to fix it. and try a smaller piece of paper. one layer of 1/4" x 1/4" should do it.
-
i guess a wad of paper would work if it is small enough. But I would use a small flat piece around 1/4" x 1/4". what carb are you using??
-
vacuum advance working? low ignition timing will also make it run hotter? but temps going up and down is most likely a t-stat issue
-
Is my oil feed and drain ok? Check out my new blog as well
Pyro replied to jacob80's topic in Turbo / Supercharger
should drain. But the fix is to clock the center section relative to the turbine. Turn the center section so the oil and drain feed is vertical. loosen the clamp, heat the turbine/center secgtion interface with an oxy acetylene touch for a few minutes and rotate the center section. -
280zx turbo timing and other problems
Pyro replied to abc_was_here's topic in Ignition and Electrical
or maybe the wires are off one position around the cap. -
could be a very stretched timing chain. does it knock on shut down?
-
I'm talking about rotating the exhaust turbine in relation to the center section. Not rotating the compressor in relation to the turbine. The compressor side rotates easily, so not over concerned about that. The 4th picture shows the different positions of the exhaust turbine as compared to the center section. In order to get the oil input port in a straight-up position, the exhaust turbine needs to be rotated (not the compressor).
-
To fit a first gen 300 turbo in the exact same position, the exhaust turbine also needs to be reclocked. Looks about 15 degree difference between the 280zx and 300zx turbines. But, not so easy to reclock the exhaust housing, as these tend to "rust lock" on the center section.
-
3" Downpipe, 38MM Divorced Port Wastegate
Pyro replied to Cannonball89's topic in Turbo / Supercharger
I did about the same, but used 2.5 inch pipe and plumbed the wastegate exhaust back into the exhaust system for a quieter boost application. -
aftermarket mini starter for a sbc.
-
Motor and trans mounts are, by far, the easiest part of the swap.
-
You will need a 60hp shot of N02 too make 275hp with your build.
-
After 3 years, I am heading to the dyno on the 5th
Pyro replied to mr jdm's topic in Nissan 4 Cyl Forum
all I can say is, some people you just can't reach. -
After 3 years, I am heading to the dyno on the 5th
Pyro replied to mr jdm's topic in Nissan 4 Cyl Forum
"It's a wack calculator. PSI itself has not much to do with power levels. All things a side, 14.7 psi on a gt25r compared to 14.7 psi on a gt35r, not the same power. Psi doesn't matter, flow does." You are absolutely correct, boost by itself has not much to do with power levels. There also needs to be a base hp level for the equation to work. Yes, 14.7 psi on a gt25 is not the same on a gt35, you got it, as these engine will also have very different normally aspirated power levels. Different normally aspirated levels is the root cause of different hp gains from boost That is the entire point. 7.5 psi on a 1000 hp engine will make 1500hp and 7.5 psi on a 100 hp engine will make 150 hp. Very different hp gains but the same percentage gain. Hey, I didn't invent the boost theory. It is simple, doubling atmospheric pressure doubles the hp. simple physics. I don't understand why you don't understand the simple formula or why you don't want to hear it. But that is what it is. -
After 3 years, I am heading to the dyno on the 5th
Pyro replied to mr jdm's topic in Nissan 4 Cyl Forum
power in a normally aspirated engine would also go up with rpm, so I'm not understanding your point. a turbo doesn't effect where the max power is made. the cam does that. if you have a 200hp engine that makes max hp at 7000 rpms then add 14.7 psi of boost then it will make 400hp at 7000 rpms, (14.7 +14.7)/14.7 =2. That is what will happen if everything is perfect. It can only lose power from there. -
After 3 years, I am heading to the dyno on the 5th
Pyro replied to mr jdm's topic in Nissan 4 Cyl Forum
there are lots of boost calculators of the web that do what I'm talking about. Again, just a simple formula. here is one. http://www.csgnetwork.com/blowerhpcalc.html