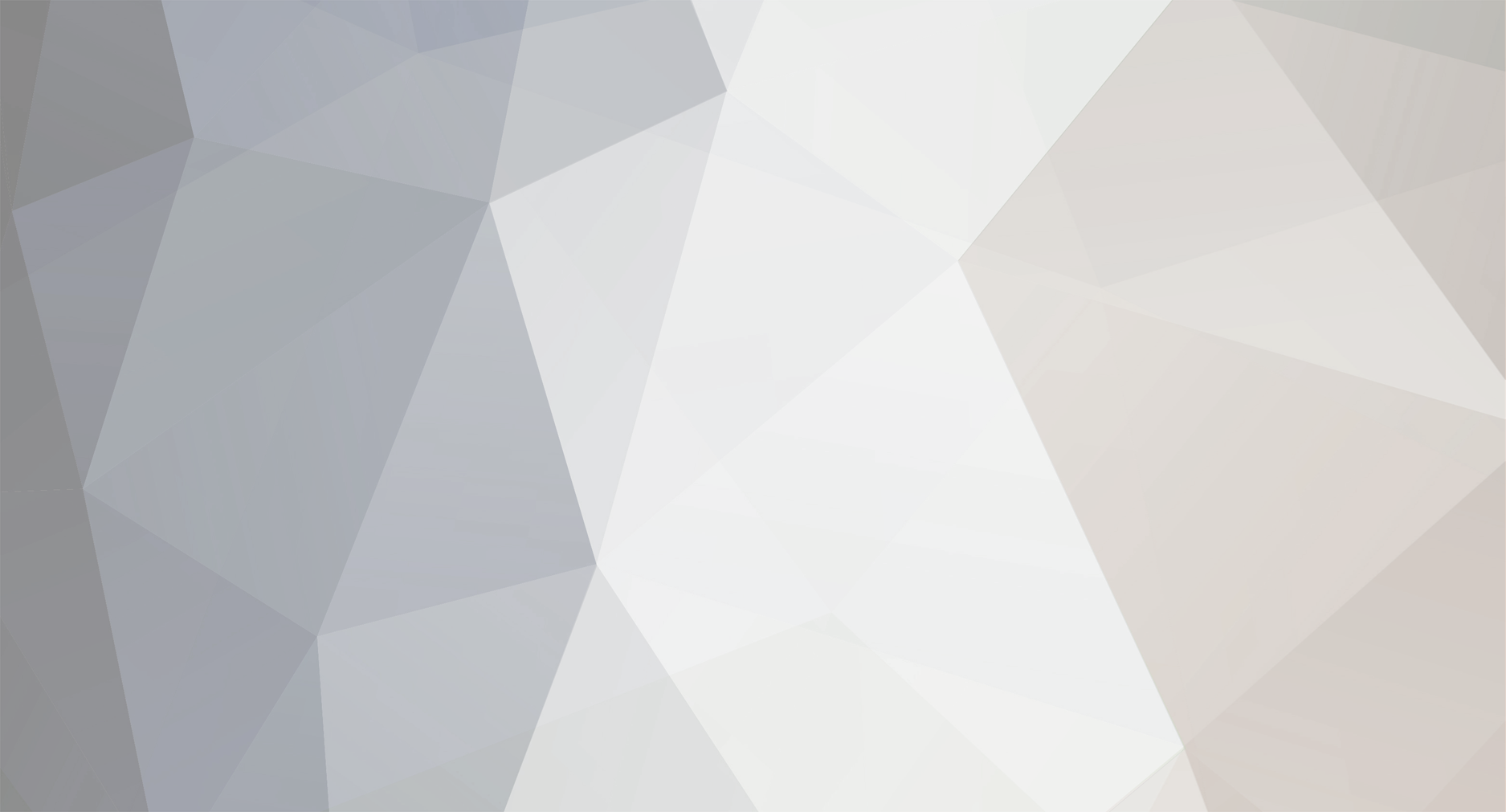
DrSideways
Members-
Posts
110 -
Joined
-
Last visited
Content Type
Profiles
Forums
Blogs
Events
Gallery
Downloads
Store
Everything posted by DrSideways
-
I finally got some photos of mine up on my FB page. http://www.facebook.com/?sk=messages&tid=1303216999374#!/photo.php?fbid=1518476613897&set=a.1515300014484.74951.1593979432 It is about as simple as it gets. The tach is the only gauge with wires. The high roll cage cross bar holds the top and two tabs welded onto the steering column holds the bottom. I used some rubber vulcanized mounts with a stud on one side and a threaded hole on the dash side. I used an aluminum panel. If I had to do it again it probably would be a carbon part. Hope this helps, Alan Yes it is for sale.
-
Wheel wells and skirts
DrSideways replied to heavy85's topic in Windtunnel Test Results and Analysis
+10 to what John said. It looks like you want to do 1/4 mile racing. Really with any competition you need to focus on the large gains first. The stock Z Car is VERY dirty on the bottom. It has a REAL big frontal air intake. Taking care of these first and then look at the rest. Any air into the engine bay needs to get out.. Less in = less that needs to be evacuated..... Any air over the top of the car needs to be smooth flowing. The ends of the car air flow need to have sharp edges for the sir the break free from. Not that I would EVER condone ANY rules encroachment:)but some creative quarter panel end work work.... may just may enhance some air flow. Not that I would do any such thing..... Sounds easy doesn't it??? Focus on keeping the car low and not letting air under there in the first place. Watch some old (for some of us;)Warren Johnson down track vids on how the car gets lower as it goes down track. Hope this helps, Alan -
Glad you got a good deal. Try and find some ZEP 45. It is a spray lube with Teflon. Give the runners a good spray twice a year and you can pass this on to your kids. Alan
-
Depending on whether they have roller bearing slides. Pre 1985 I would say they won't have sliders. Post 1985 most top line boxes had roller bearing sliders. Guys at the dealer had boxes in this style as early as 1982. The top and bottom would have been stacked. From what I remember not counting the side cabinet these would have cost about $2k or so in 1983. Hope that helps. Alan
-
Try Perry here: http://www.skidmarkracing.net/ Alan
-
Try Todd @ http://www.wolfcreekracing.com/ Alan
-
This link gave a 404 file not found page. Click ME for the HybridZ Rules and Guidelines. Thanks, Alan
-
Where to buy Rota RB-R Wheels?
DrSideways replied to Meaty69Maro's topic in Brakes, Wheels, Suspension and Chassis
Try the Wheeldude.com. He was very quick to an inquiry I had yesterday. I used the message box deal he has. The email got bounced back for some reason. The message box work fine. Hope this helps, Alan -
Even the good stuff breaks
DrSideways replied to mark's topic in Brakes, Wheels, Suspension and Chassis
Do you have a better mouse trap? Would normalizing the welds help? I don't think Dave or his welder does this. I asked one time. Alan -
Even the good stuff breaks
DrSideways replied to mark's topic in Brakes, Wheels, Suspension and Chassis
Alan, Christ, Now I will need to worry about what is wearing out on the Red Bird, while I'm hauling it down to road. Afraid so. It isn't as bad when you are going 2-3 hours. Some roads are better than other too. Two days @ 10 hours each and I would want to leave time to nut and bolt things. No different than running my car on a Friday & Saturday. Sunday morning is spent flushing the brake fluid and tightening things up. I also ran my shocks back to soft and tied the car down using wheel bonnets. John C. may have something to say about tie downs and shock wear/damage. Then we would be getting off track a bit, but good to cover none the less. Alan -
Even the good stuff breaks
DrSideways replied to mark's topic in Brakes, Wheels, Suspension and Chassis
Glad to throw some light on the deal. It is so easy to overlook stuff that is "working" when there is generally a list of stuff that isn't. Although it is more work, a duty cycle type of operation can help overcome this type of issue. A lot of formula guys also use an hour meter to help. The one thing that doesn't count is trailer time. I have seen cars have all kinds of loose stuff after long tow trips. If this was easy everyone would do it. Just think of the mess that would be:) Alan -
Even the good stuff breaks
DrSideways replied to mark's topic in Brakes, Wheels, Suspension and Chassis
On formula cars with significantly less weight but same materials, the control arms and other suspension components are magnafluxed at least once a year. With more weight and a curb or two... In the "Prepare To Win" by Carroll Smith he would only use Krylon spray pain on them for easier strip down and checking between each race weekend. Alan -
I did some more thinking on this. Your car is pretty low. The spring rates are not real stiff. Then there are the Tokico shocks. Are they the shorter units? If not, might they be bottoming out and taking the spring out of the equation? Those can be at their limit anyway under some less than extreme conditions. Autocross on a slick lot can be some of the toughest conditions. So to test this out just raise the car back up to something just less than stock ride height. Realign and re-scale the car. Go to an event and see how it does. This would be an inexpensive way to test. Keep us posted, Alan
-
A larger front bar will help to keep the inside rear on the road surface too. When installing a 1"+ front bar I always weld a plate to the bottom of the frame rail. This covers the bolt holes and runs about 5"-6" fore to aft with the center between the original holes. The width of the plate is just a bit less than the width of the rail. Then I weld a 4"x$' plate to that. The extra width sticks out to the inside of the rails. This is where I bolt the sway bar brackets. I think the plates were 3/16" thick. John C. may comment on that. The larger bar can rip the threaded inserts right out of the frame. Of course that won't happen while in the paddock. Back in the day I ran a Suspension Techniques 1" front bar and 7/8" rear bar with a lot of success. Your mileage may vary. Alan
-
Car vomits oily stuff out the exhaust
DrSideways replied to Blitz21's topic in Trouble Shooting / General Engine
Whoops, didn't the FI, just the '73 in your sig. It still sounds overly rich. FI engines do have cold start devices. You might look at the function of those items and check general state of tune. Don't sit. Just go. It can warm up away from your "spot". Alan -
Car vomits oily stuff out the exhaust
DrSideways replied to Blitz21's topic in Trouble Shooting / General Engine
Sounds like it is running pretty rich. Are you using the choke for cold start? If so try and start without that. Also don't rev the engine while sitting there. Crank up and move along. Does your tail pipe extension point straight out or down. Don't point it down. Hope that helps. Alan -
The HRP deal would be the Easy button. Another thing you might look at is a carbon fiber panel. It only needs to be around 24" - 28" long. I dictated width by fitting the Autometer Tach over the steering column. My roll cage cross bar goes straight across the car just under the door level. So the tach fits between the two. I can snap a photo tomorrow while at the shop if you like. Simple is better. I have seen some dashes get out of control. No need to go across the car, or to be bottom of the windshield. Less is more...... Alan
-
safety wire for brake rotor bolts
DrSideways replied to bjhines's topic in Brakes, Wheels, Suspension and Chassis
In your photo post the pic on the right I will refer to. The lower bolt @ about 5:30 in the pic .... The wire that is going around the bolt head should be going around the other side of the head. As you are running the wire this will tighten that loop against the side of the bolt head. As you bring it around to meet the wire coming out of the hole I always run the "looped" wire under the one coming right out of its hole. When you put in your 1 - 11/2 twists it stays put and firm. Then you can attach the safety wire pliers and continue to the next hole. Actually I think I was looking at your work wrong. Upside down kind of. Other than getting the loops tighter it looks correct. If I was going to wire the the bolts from that side then I would run the wire as I was talking about. If I was standing on the top side of the table then your direction is fine. Confused yet? Tighten the loops and back to regular programing:) Alan -
safety wire for brake rotor bolts
DrSideways replied to bjhines's topic in Brakes, Wheels, Suspension and Chassis
Twisting the wire on the part that goes around the bolt head is incorrect. That part should go around the opposite side of what you have there J.M. That way the wire that goes around the bolt naturally gets in tension while twisting for the next run. Some safety wire pliers and some Duck Bill pliers can help with this job. When you first stick the wire through the hole and do the first twist you can take your duck bills and give it a twist or two and then put on the twist pliers. Make sure and put the wire coming out of the side closest to the next hole over the one that comes around the fastener head. This keeps that "wrap around wire" down and not popping over the fastener head. Before you get to the next hole, hold up and make sure to not add an extra twist. This puts slack in the run. John C. is right about not holding the fastener in, but to keep it from working loose. Loose safety wire doesn't do much more than nothing. If the fasteners work loose just a bit vibration will still cause damage. Still better than falling off, but not optimal. Something worth picking up is a "Standard Aircraft Workers Manual" by Fletcher Aircraft. More than just safety wire:) Like always there is more to it than it looks like. You can also get the hat bolts pre-drilled from several race oriented hardware places. Hope that helps, Alan -
At CMP with the 13 inch floating rotor set up
DrSideways replied to mark's topic in Brakes, Wheels, Suspension and Chassis
You should drill the hat to rotor bolts for safety wire. If one of those backs out it goes to machining on the caliper mount. There is no tee-shirt involved when that happens. Alan -
bre and zg flares do not exist... (pic request)
DrSideways replied to crazyoctopus's topic in Body Kits & Paint
Glad to help. My wheels are 16"10 with 0 offset. Alan -
bre and zg flares do not exist... (pic request)
DrSideways replied to crazyoctopus's topic in Body Kits & Paint
You can look here: http://www.triadzclub.com/index.asp?inc=giles This is a 280 with flares close to what you are looking for. Also has the BRE front spoiler. Mark Ulrich also has a similar setup here: http://www.triadzclub.com/z/events/past/2003/03kershaw/IMG_1039.jpg http://www.triadzclub.com/z/events/past/2004/vir04/IMG_1297.jpg Hope that helps, Alan