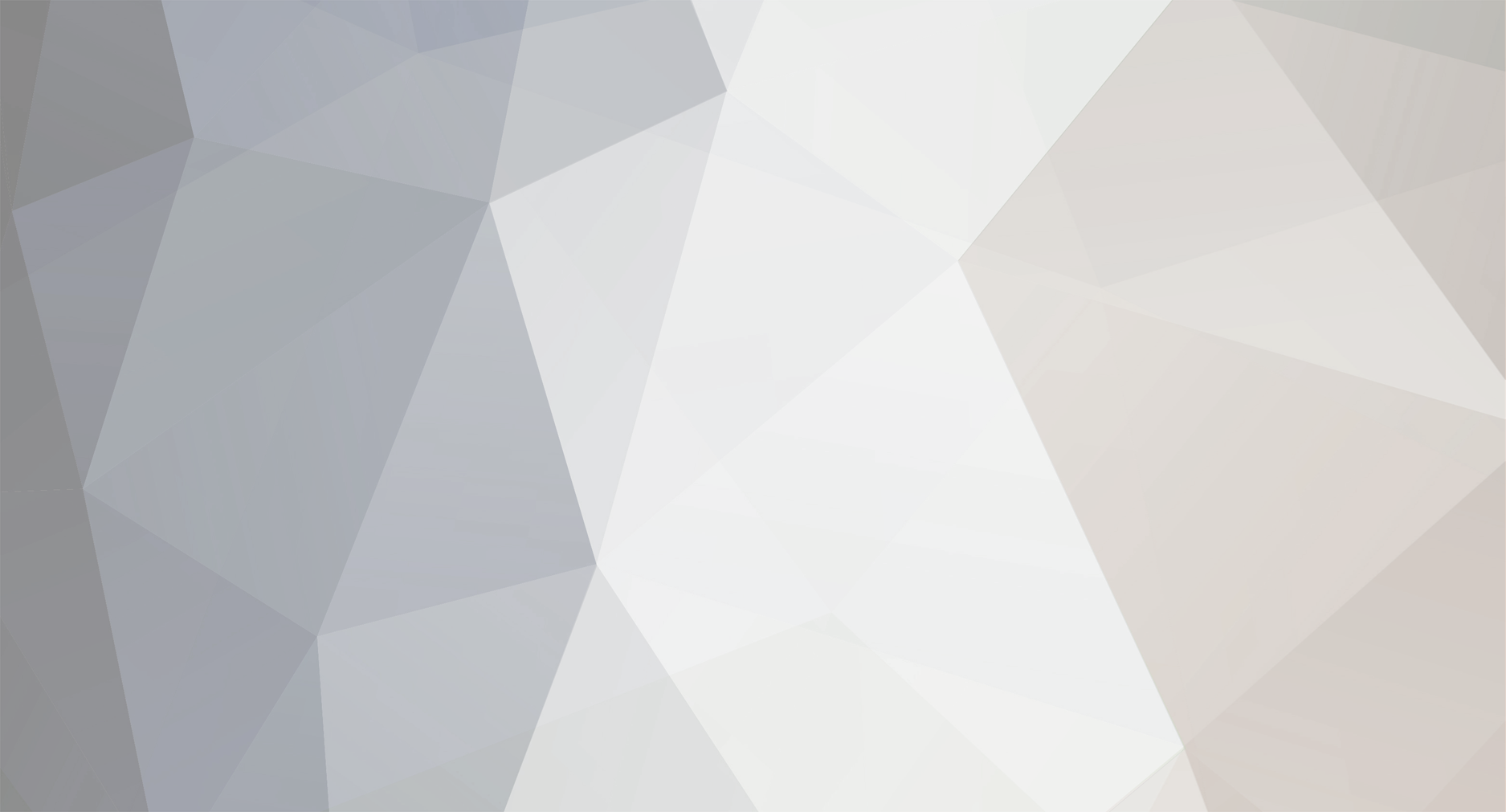
rejracer
Donating Members-
Posts
422 -
Joined
-
Last visited
-
Days Won
2
Content Type
Profiles
Forums
Blogs
Events
Gallery
Downloads
Store
Everything posted by rejracer
-
As Cygnusx indicated, this would be fine if you used short bolts. I'd use a washer between the chain and the deck. You could use the stock head bolts if you use something rigid in between the bolts instead of the chain. Class 8.8 bolts would be fine for this. Class 10.9 is the strongest, but not needed in this application.
-
Master cylinder no booster
rejracer replied to AIShelby's topic in Brakes, Wheels, Suspension and Chassis
It sounds like the system is not adjusted correctly, or the brake booster is bad? I had to replace my brake booster and MC about 2 years ago, I am very happy with the stock setup. I had the larger MC in there and when it failed I went back to stock. I prefer the feel of stock vs the larger because it give me better control and more feedback when on the brakes. -
I did the 280z tach when i upgraded to electronic ignition. Has worked ever since, I did the mod in 1995.
-
If you still have your 280 tach which you already converted, you can mount the 280 tach guts in the 240 housing. This is what I did when I converted my 72 to electronic ignition. As I recall it was a bolt in affair, but at worse you have to drill one hole in the back of the 240 housing to clear the tach signal input lug. You still have the 280?
-
Alex, there is a new FAQ's section FAQ is Frequently Asked Question, don't know if you use the acronym over there or not. Overheating can be addressed, it's in the FAQ section.
-
Oddman, I found dimensions for the larger fan, but not the smaller on Rock Auto. I have the mounting geometry for the smaller fan, that I pulled off one of Bill's fans for a shroud I designed. It's fairly easy to fab it up like Bill did, as I recall he did this before I had gathered the dimensions. -Robert
-
Protect the threads by putting lug nuts on them and torque them down a bit. When using impact guns don't use extensions and even avoid deep well sockets if you can. Both reduce the amount of momentary torque that gets transferred to the nut. An extension acts as a torsion spring (even impact extensions) and to a lesser degree deep well sockets. Of course make sure you are using heavy impact sockets as well.
-
Does the 280ZX have a proportioning valve?
rejracer replied to PhilbertZ's topic in S130 Series - 280ZX
Pulling from left to right cannot be caused by brake lines as the pressure will be equal between the left and right sides. If it was the brakes causing the issue it would have to be calipers, pads or rotors. Glad you found the problem. -
Rear disk rotor question
rejracer replied to GOTHALOSISM's topic in Brakes, Wheels, Suspension and Chassis
If you are going to 5 lug, I would choose a different setup. The 280zx rear brakes in my opinion are not worth the effort if you still incur the cost of machining the axle and rotors. I am currently running the 280zx caliper/rotor with early maxima brackets. -
Higher efficiency cylinder head by grooving?
rejracer replied to mutantZ's topic in Miscellaneous Tech
I step away for a few days and.... Tony/John, Your pointa are not lost. I've heard everything you have said, and agree with it. Thank you. What I have not seen is what type of testing B&S did. I simply do not have the data. I don't know if they did the same crude cuts in the head / piston, or even if they tested it on OHV engines. I am sure their goals are different than mine. Part of my posts are just thinking in text, please don't take this as being in denial of the known shortcomings, or pushing views. rsicard, I don't know where you are going with the patent theft, as it's totally irrelevant to the technical discussion. I am trying to have a technical discussion to better understand the combustion process, not get into a business ethics debate. My emotional attachment to the grooves is nil, so if they work, great, if not, I'm not phased a bit. Back to the grooves, no power gain at WOT, just mid range power gains at the cost of emissions. If there is additional data please include it, otherwise I know what the grooves do per the real testing data I found. My only question at this point is if the grooves can be modified to get power gains at WOT. Once again, if no data suggests it's possible, I'm not going to cut up one of my P90's to find out. As much as I would love to develop a new combustion chamber design that increases power, I still have to live in reality, and that is I don't have the means, knowledge, or tools. I will say that what the OEM's have done in the past 10 years is inspiring. Cars just keep getting better. -
Higher efficiency cylinder head by grooving?
rejracer replied to mutantZ's topic in Miscellaneous Tech
The chamber design could also affect the results. I would agree with what John is saying, if a combustion chamber is already optimized in other ways, how much would the grooves affect combustion. What I believe the test prove, is that under circumstances the grooves yield a significant increase in power. Problem is it's not WOT. For a street engine I see a benefit. I would again agree with John, this is for cruising. In all the implementations I've seen of these grooves, I would describe it as a garage hack based on the work I've seen done. In my opinion the implementations done with a hand file are half baked ideas. To me there is little to no thought put into what it is the designer is trying to get the gasses to do inside the chamber. All descriptions I've seen are along the lines of "increases turbulence", which is just vague. It strikes me as "lets do something and hope it works", instead of a well thought out design. I suspect that if the there was a more elaborate design, that there could be benefits even at WOT. As of now, that's just my theory. There were a couple of problems with the tests though. And I think it was in the favor of the grooved head. First, the average RPM's were not the same. The grooved head was run at a slightly lower RPM, about 50 RPM's. With a fixed throttle position, I believe this would be in the grooved head's favor. Also, not all the TPS readings were the same. This too could skew the results. I don't think it accounts for 17% at moderate loads, but I would expect the real number to be somewhat lower. Also this test did not compensate for the loss of compression. The loss of compression I believe would lower the power output on the grooved head. So the tests are not perfect, just the best I've seen on the net. John, keep in mind that not all of us are using this in a track only car, so a loss of compression may not be as big of a priority as it is on your engine. Cooler running at part throttle has a anti detonation benefit for when you do intermittently get in on it. Since most street cars are low duty cycle, there may be an indirect benefit at WOT, as you may be able to run a tad more timing, or up the boost. Come to think of it, EGT's were lower, I don't know if that means the combustion chamber would be cooler as well. The grooved head was using less fuel based on the injector pulse width, so it may be a higher percentage of less fuel being consumed in the chamber. I assume that would mean lower chamber temps as you have the same mass of air being heated by less fuel burning, but I could be wrong. It could be that the more complete combustion happening in the chamber means higher temps. Make this a road race or track car, and that benefit is no longer there, or against you if it raises chamber temps. That's my thoughts on this for a while. I need to analyze the test data some more, and scour the corners of the net for objective power testing. -Robert -
Higher efficiency cylinder head by grooving?
rejracer replied to mutantZ's topic in Miscellaneous Tech
Here is some test data: Click here for test data In summary at part throttle or lower RPM there is a net loss of torque. At higher loads and RPM's there is a gain. Now get this: The largest improvement I found in the document was a 17% increase in torque output. There may be higher. This was tested on a Geo Metro engine, 2 heads were re-manufactured to stock specs, one of them modfied with the Singh Grooves. Does this qualify as legit test data? 260Det, Yes it's very reasonable to consider it. I've seen some of the pics on the net, all I can say is I'm surprised some of those cars run after they are done. One thing concerning the testing is that even the above test data, the compression on the engine is lower than on the stock head. I would like to see another test where the chambers are welded up a bit in an area that is not going to alter the turbulence at all, just even up the compression ratio. I think the loss of compression may be lowering the torque output at lower RPM's. To what degree remains the question. -Robert -
Higher efficiency cylinder head by grooving?
rejracer replied to mutantZ's topic in Miscellaneous Tech
I don't know how well it will, it looked somewhat small. But the VG chamber design looks like it may respond better to this than an L series. I do think it will help the burn rate, but I just want to be clear this mod alone is not going to yield a 20% power increase. I would be pleased if it got 1.5% more power over a well set up high quench design. A tad more over a open chamber head, assuming you swapped to a closed chamber head, yet left CR the same. I would also like to make clear I am not trying to step on anyone's toes on this, I'm just making the point that the idea has merit, just like a standard wedge head and turbulence. -
Higher efficiency cylinder head by grooving?
rejracer replied to mutantZ's topic in Miscellaneous Tech
I think there is a wee bit of misunderstanding here. My 20% comment was misunderstood. The 20% I am referring to is basically the power to be had without changing the intake or exhaust manifolds or porting the head. 20% is doable without porting or manifolds. That was my point. Are you reading what I wrote? How did you get 325hp from an engine that was originally designed for 170 or so hp? I am assuming you modified the airflow of the engine, combustion chambers, timing and fuel system. This guy is just talking about modifying the combustion chambers and fuel system. If you are approaching a 100% increase, why do you doubt if this guy is doing a few mods and gaining what he describes as increased torque, lower temperatures, and smoother running. I'm scratching my head as to why this is unbelievable. Perhaps I should have elaborated. I was reading up on this before I posted and here is a quote from his website: (and other websites) "After this simple design change ~ Obsolete Side Valve Engines which feature large quench areas have shown reductions of up to 42.5 % in fuel consumption" "I undertook to carry out modifications on a side valve Briggs and Stratton engine - as side valves display the largest squish areas in comparison to over head valve OHV designs" -Somender Singh He is saying 20-42.5% reduction in fuel consumption, but gives no numbers that I have seen concerning a % power increase. Side Valve Engines are more commonly known as flat heads here in the US. Getting 20% more efficiency out of engine design that is approximately 100 years old is not an impressive feat. Thus my comment above. Now my bad, I said gain 20% right after increase in power. I did not mean to imply a 20% increase in power from the Singh groves. I meant 20% increase in power is attainable by increasing combustion efficiency, which includes introducing turbulence, raising compression and retuning. In the real world this could mean welding up the chambers (or using a P90/P79/MN47/E31 or early E88), fitting flatop pistons, and running Megasquirt, Wolf, Haltec, and tuning it. If doing that many mods on an otherwise stock engine then 20% is not unrealistic. While that's a lengthy list of car manufactures, the relevant engine manufacturer has been omitted: Briggs & Stratton. If you've read up on Singh's work, then it's clear that he came to his conclusions by modifying what we consider a lawn mower engine. Some of my comments were in context to his work, others were applying what he was doing to a more modern engine design. Realize he lives in India. When I was there in 2007 it was explained to me "keep in mind when dealing with us (Indian workers) that 20 years ago, we did not know what a color television was". This was told to us by one of the more educated and affluent managers there. He was part of a higher caste. Mr. Singh is modifying engines that they actually use over there in transportation. Makes me want to modify my 8hp briggs that's on my Tote Goat. I never stated or implied that if you cut grooves in your L-series head that you will get 20% more power. I did however say that if you modify the chambers, increase compression, and tune it, 20% is not unrealistic. Since you are already at nearly 100% increase, you've accomplished what Mr. Singh was aiming at concerning combustion efficiency and then some. Albeit the comparison is apples to oranges, regardless, principles applied. My quotes above stand. So to restate my original intent: Any design change that increases the rate of burn in the chamber will yield more power when properly tuned for. Singh grooves may be one means of achieving that, as is quench, as is swirl, as is multipoint ignition, as is getting the ideal fuel mixture for the chamber it's being burned in. Lastly the OP's link had the quote: "He claims that his invention makes an engine cleaner, quieter and colder than its internal-combustion cousins around the world—while using up to 20 percent less gas." -- (Popular Science; Sep 24, 2004) I've never seen a claim where he states a % increase in power, rather a % reduction in fuel consumption. I said 20% power, but that was not related directly to Singh's work, nor was it the grooves alone. So to restate what I've restated: This discussion is focused on combustion efficiency, how it affects power, and how Singh Groves can be used to increase it. Leon / 74Adam, Do you have anything to add concerning the topic at hand? I did get a laugh out of that one, but do get sucked into the vortex! Just come with understanding of what the originator is and is not claiming, and how it relates to a "modern" engine. Did I just call an L-series modern? Most of the skepticism in this thread is caused from assuming Mr. Singh is claiming the grooves increase power by themselves, or assuming (and not understanding) what I actually wrote. rsicard, Thank you for posting thoughtful content. You are right, ideal grove placement would be dependent on chamber design and layout. 260DET, In a non turbulent open chamber the flame front expands outward from the spark plug in a more or less spherical shape. This is not exactly true due to the result of the compression stroke, it's more like a disc. The gas inside this sphere is in process of or has already combusted. The pressure inside the sphere is the same or very close to the pressure in the rest of the chamber, but the density is far less due to the increase in temperature. This means that the area outside the flame front is slightly gaining in temperature (as a result in the pressure increase), but greatly increasing in density. Turbulence is attempting to deform the natural spherical flame front. When the flame front is deformed the ratio of flame front surface area to volume unburnt gasses in the chamber increases. Simply stated this is just an attempt to expose unburnt gasses to the flame front. This is why multiple grooves are being reported as yielding results. I think what is happening is the groves make a column of gas and thrust it into the flame front, which causes an equal volume of the burnt gasses to be thrust in an opposite direction away from the groove. Instead of a standard quench area expelling a flat sheet of gas, the groves are attempting to expel a column of gas. This column of gas having a bit more volume and mass is able to penetrate the flame front further than a more consistent sheet. If I could get a dual plug head with one spark plug where it is in the L series, and another located at the opposite side of the chamber, I think that would be an ideal physical layout. For an experiment I have been thinking about for a few years. I would do a splayed timing offset between the two plugs. I would ignite the open side of the chamber first. As the piston is moving up the flame front is expanding and compressing the unburnt gasses to the opposite side of the chamber. The gasses think they are safe, but little to they know the other plug is about to fire, and it does, say 5* BTDC. This second ignition event increases the turbulence by rapidly propelling the unburnt gasses in the quench area. Groves or not I believe this would be increasing turbulence in the chamber. But with the grooves the velocity of the gasses in the groove area is greater as the quench effect is forcing the gasses to lesser pressure areas of the chamber. Where I disagree with Mr. Singh is the 70 thousandths rule. Make the piston to deck clearance as small as possible overall, but do more elaborate grooves to channel as much of the mass of gas to increase the flow from the quench area to open portion of the chamber. The goal is: 1. Force as much of the gas to the other side of the chamber as possible 2. Evacuate as much of the gas from the quench area. 3. Increase the flame front surface area to unburnt gas volume ratio So now another event happens, we reach TDC. As much of the gas that is going to get evacuated from the quench area has been evacuated, and the piston starts it's downward travel. The quench area's volume delta is increasing much more rapidly than the rest of the chamber, as a result it's localized pressure is dropping faster. Remember when we forced out the gasses through the grooves. That action caused unburnt gasses to flow in the opposite direction. I would place the grooves so that these unburnt gasses would be as close to the quench pads. Now that the volume of the quench pad area is increasing and the pressure dropping, the hope is that it would pull the unburnt gasses into this area, and hopefully there is still a remainder of the combustion process to support the burning of these gasses. The goal is to have the largest flame front surface area in relation to the volume of unburnt gasses, so the combustion process completes in less degrees of crankshaft rotation. Anyhow that's my theory on how this would work based on my understanding of what's happening in a combustion chamber. If any of you wish to refute it, please do so intelligently. I'd like to learn so I can more more fully understand how design affects the combustion process. -
Higher efficiency cylinder head by grooving?
rejracer replied to mutantZ's topic in Miscellaneous Tech
His point was that a turbulent combustion chamber causes the same effect as multi point ignition. I would agree with this. Anything that will speed up the burn rate in a combustion chamber is better for power, assuming the engine is tuned for it. If we can get the burn rate up, timing can be delayed the proper amount and we are left with greater mechanical leverage as the crank is closer to 90* when peak cylinder pressure is achieved. Not to mention less cylinder pressure while compressing. This nets out to an increase in power. In my opinion 20% is not unrealistic. Keep in mind that the engine he was working on it's basic design is roughly a century old. Do note, that just cutting grooves in a set of heads and running it without tuning it accordingly is not the right approach as it's not complete. He also stated that the compression was raised. There is efficiency increase with just the compression gain. So removing your cylinder head and taking your die grinder to it will get 20%? I don't think so. Raise the compression, modify the combustion chambers, and re-tune it? Now your talking. -
Pressure test? Use a welding tank and the proper regulator. Any welding gas mix will work, Argon, Co2/argon, or tri mix. No Oxy as Tony said. I am certified scuba for open water, altitude and nitrox. Even compressed air (~21% oxy) is safe. I would not try it with nitrox, which is up to 40% oxy. My dad's buddys have converted A/C compressors for air compressors. They run power tools off their jeeps. Also never play with oxygen in any concentration, it is a very unforgiving gas. Co2, and nitrogen give physical warning signs, no such luxury with oxygen.
-
Doubtful as vacuum leaks will be most noticeable at low rpm, much less so at high. Regardless it needs to be fixed. Problem you describe sounds like fuel starvation. Starvation can be in a couple of different things. 1. fuel level in bowl is getting low due to inadequate inlet flow. Check bowl, float, needle and seat, and brass filter at carb (if equipped). 2. fuel system is dirty / clogged not allowing enough flow from bowl to jet orifice. Check flex line from bowl to jet, cleanliness of jet. If you were checking fuel pressure after fuel pump then pre pump filter and pump are fine, problem lies between fuel pressure and jet orifice. Hitting a wall can also happen from jets being to far down like when the choke is on, but that would be noticeable in terms of running rich.
-
Their ability to correctly id the cars is pathetic. They had it listed as a 260z, and the 72 240 was listed as a 280z.
-
I went back today and counted the number of turns on the driveline to make the output flange turn once. It was just past 3.5 turns. I would have pulled it if it were 3.364's.
-
shouldered bolts for hub spacers???
rejracer replied to piston's topic in Brakes, Wheels, Suspension and Chassis
The spacers should be centering on the hub, and the spacer should have a raised area in the middle to center the rotor on the spacer. With that said, I get my bolts at one of 4 locations: 1. Local ACE hardware in Roseville, CA. They have an excellent selection stocked by midwest fasteners. 2. McMaster Carr 3. Bolt Depot 4. Fastenal. When I did my Toyota vented upgrade, I assembled the parts off the car. I got 2 pieces of wood and set the rotors on them, I then loosly hung the hub from it then slowly gave each bolt a half turn each working my way around until it was snug, then torque to spec. This was my best attempt at the time to get it centered. I later pulled the brakes off as I did not like the front to rear bias. Do be aware that the OEM does not rely on the bolts to center the rotor to the hub. -
thanks Drax, I've been reading it. i understand the helmholtz principle, now trying to understand the math behind it... You posted some good info there, I'm still trying to digest it.
-
Thanks Leon, this particular project is not going the ITB route, as it's whole purpose is to explore different designs. I agree with everything you are saying, just looking for the supporting math to design a runner, rather to design a proper velocity stack for a given flow / pressure at a certain rpm range. I've not found what I need just yet. So far, the design has been based on packaging needs, not really on proper design of the diameters of the runners.
-
As mentioned in the PM, Nylon standoffs would do the trick. If you are concerned about the strength of the standoffs, maybe try making a rear plate out of Plexiglass that centers the rear of the gauge to the housing. If you wanted to be really fancy, Secure the electrical connections with brass standoffs, then on the brass standoffs mount the plexiglass centering ring, then behind the plexiglass plate use Nylon standoffs connected to the brass standoffs, or use brass standoffs connected to the plexiglass plate using different fasteners (not connected to the other brass standoffs. In Ascii art it would look like the following: 1 2 3 |---------- | | |--|--| | | | |--|--| | | | |--|--| | | |---------- 1 is the rear housing 2 is the plexiglass plate 3 is the back side of the gauge. Would this solve the problem at hand? I think the trick becomes finding standoffs with the right threads for compatibility with the gauges Edit: The ascii art looks well in the editor window, but not using the web browser. copy and paste into a an editor that uses a monospace font.