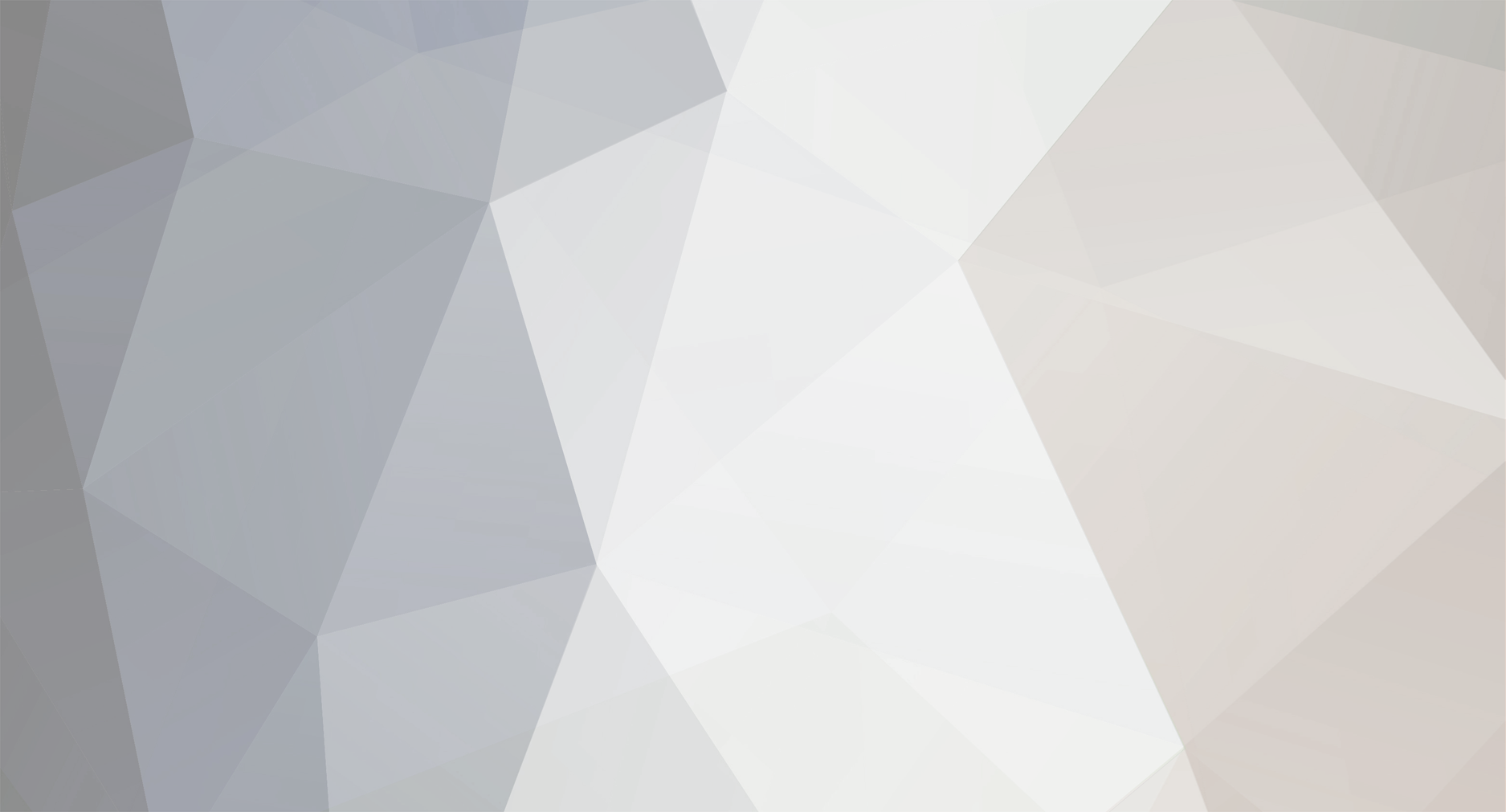
rvandivort
Members-
Posts
249 -
Joined
-
Last visited
Content Type
Profiles
Forums
Blogs
Events
Gallery
Downloads
Store
Everything posted by rvandivort
-
Oops..hy35w!
-
Hey guys,I`m sure this has been done before...but, is there a BOV on ebay that has the proper outlet to go to the input of an hy36w to cut down on lag. Thanks, Roger (I`ve seen some ovals and horns---want a tube for a vacuum line fitting). Or other manufacturer?
-
Rotating hy35w for wastegate actuator
rvandivort replied to rvandivort's topic in Turbo / Supercharger
I mean we have the Vband stuff on the exhaust--Don`t have that. I have a 5 bolt. Please explain this stuff. -
Rotating hy35w for wastegate actuator
rvandivort replied to rvandivort's topic in Turbo / Supercharger
OOPS, The wastegate is STAINLESS STEEL!!! The brazing thing does not work. It grabbed into the lever, but not the pin. So, I am having friend Tig weld it (stainless steel job). I wonder about the different models of Holset. I have a 02 model. 2400 dodge. It has mystified Me ,seeing all the different ways of approaching the problem. I am assuming there was a big change the next year . -
Rotating hy35w for wastegate actuator
rvandivort replied to rvandivort's topic in Turbo / Supercharger
My reference to grinding the puck refers to grinding the edge..and not much.Furthermore,I had a heavy ruster, and all above refers to that situation. Thanks for all your help, Roger -
Rotating hy35w for wastegate actuator
rvandivort replied to rvandivort's topic in Turbo / Supercharger
I`m going to Leavenworth tomorrow to get the wastegate lever welded. I could send it to You then. -
Rotating hy35w for wastegate actuator
rvandivort replied to rvandivort's topic in Turbo / Supercharger
Cold Fusion, How `bout splitting the cost? I still have the shipping box. -
Rotating hy35w for wastegate actuator
rvandivort replied to rvandivort's topic in Turbo / Supercharger
Actually,(for nc chris) had to order a rather large internal snap ring remover--15 1/2"--off of ebay. Cost Me about 67$ w/shipping. Worked in about 3 minutes with removal of the exhaust end and bumping out of the exhaust section. The pin was gone (thru corrosion ?), so no grinding was necessary. I`m wondering about the necessity to remove the wastegate actuater bracket now, as it looks like it it might have worked. But, a piece of aluminum strap will work with a half hours fabrication..or less. So.. Does anybody need a 15 1/2" internal snap ring tool good for 6"? Thanks, Roger -
Rotating hy35w for wastegate actuator
rvandivort replied to rvandivort's topic in Turbo / Supercharger
Another thing I ran into was binding on the the waste gate puck. Sometimes it would close and other times not. I ballpeened the two sections together. That didn`t totally work...so I mildly beveled the bottom of the puck with a diegrinder--eliminating obstruction on the lever end. That worked. -
Rotating hy35w for wastegate actuator
rvandivort replied to rvandivort's topic in Turbo / Supercharger
Thank you Chris! Will do that tomorrow. Maybe I`ll be able to drop it in by the end of the week. -
Rotating hy35w for wastegate actuator
rvandivort replied to rvandivort's topic in Turbo / Supercharger
First, forgive the above blather--it ran an 18.96 in LS/A. I did smoke the tires with that supper granny on the early Hydromatics! Today I finally separated the two sections with the help of jeffer949,nc chris, and datman. I realized You separate it..not turn it(like duh!). Anyway, after sawsalling 1/4 plus down and using a air hammer...I had no separation. I was very impressed with the used bimetal blade-it went further than I wanted! I bought a maap/oxygen torch from Lowes, heated it,then air hammered it for a minute (the groove). It separated! Now, I don`t know whether it was the heat or the constant soaking in penetrating oil that did it. The separation showed a flange about a half an inch going horizontally toward the exhaust turbine. This would stabilize an overcut into the original groove( I did cut into it a bit). It did require a little bit of adjustment to free the exhaust turbine from binding or squeaking..but as soon as total contact was achieved..yeah! I don`t know if if this freezing thing is normal, but that`s how I did it. Now..My question is.... after rotating the exhaust portion...how bout the intake? The intake is toward the block and not enough to preclude a double 90. The snap ring on the intake looks like the next step. Thanks again, Roger -
Rotating hy35w for wastegate actuator
rvandivort replied to rvandivort's topic in Turbo / Supercharger
There is no shop in the area that would do anthing differently than I am doing. It is the mating space between that is important. As long as it is 2mm..no problem.I have been rebuilding engines since 1965. Not every year of course. But, being in building construction for 40 years and doing all the mechanical stuff---as well as building a street stocker( 68 chevelle) from the ground up I know the pitfalls. My first rebuild engine was a 53 Hudson twin H power 308 flathead six--Nascar champ in 53. I am a risk taker! -
Rotating hy35w for wastegate actuator
rvandivort replied to rvandivort's topic in Turbo / Supercharger
I am only going as far as "break point". I am taking a few thousands of an inch off both sides of the flange. The worst that could happen is break thru..not likely. Milling the two ends and a shim would take care of that. Ran an air hammer and heat on it today..still no break. Still would like to know how much meat I have to work with. By the way, if the worst happened, what socket do You use to remove the turbine assembly? It is a star thing..not sure what would work on that. -
Rotating hy35w for wastegate actuator
rvandivort replied to rvandivort's topic in Turbo / Supercharger
Jeffers, I don`t intend to go all the way. Just enough to get a breakaway. What I need to know now is the thickness of the flange ,so I don`t go so far as to cock it. This thing is fightin Me!! Thanks for Your help. Roger..about ready to put it in.....frustration!!! -
Rotating hy35w for wastegate actuator
rvandivort replied to rvandivort's topic in Turbo / Supercharger
Thanks datman, I decided to not do the zip files because of cost. Do You have a pdf on this? I have cut a 1/4 inch groove around with a bimetal sawsall blade, and am soaking it with penetrating oil. I have been hitting it with a plastic headed hammer any place I can. Thanks to jeffers, and others with the dowel thing I stopped believing I could just rotate the thing and everything would be alright. This thing is stuck like somebody used epoxy on it. But, after 6 years?! what would You expect? Going to try again tomorrow with the heat. If that doesn`t work..more cutting. What is the size of the flange. In other words, I`m into it for 1/4 inch--how far is it to the end? Thanks again, Roger -
Rotating hy35w for wastegate actuator
rvandivort replied to rvandivort's topic in Turbo / Supercharger
So far no luck. The thing is stuck together with no willingness to part. Have done WD over a week and 15 minutes of heating with a propane torch. Tried heating on the wastegate a month ago..ended up knocking it out with a homemade punch. Next step will be a sawsall with a hacksaw type blade. This is isolated from intake and exhaust, so no problem? Stop Me if I`m wrong. Thanks, Roger -
holset HY35 silencer ring......my thoughts
rvandivort replied to big-phil's topic in Turbo / Supercharger
Sorry..not to be an idiot here...but, what is a silencer ring? Others might want to know. Thanks -
Rotating hy35w for wastegate actuator
rvandivort replied to rvandivort's topic in Turbo / Supercharger
Thanks Guys. Guess I`ll get another propane tank and go at it. NCchris,does the hy35w have the same dowel? And where is it? I have the vband totally removed. Ahh , see a flanged out thing at the four o`clock position (or 8 O`C from the connector depending on how you`re looking at it.Unfortunately, I have no reference point after pulling the v band:(Where in relation to the oil inlet, outlet would it be? Thanks,Roger -
Hi! Saw a post 8 months ago about this. Thought it said removing the v band and then rotating it, and then aligning it with a t3 actuator to a fabricated bracket on the intake manifold would do it. Rather than going back on an intensive searce again--and the fact that the thing is rusted together (mucho WD40 used so far), any advise on this? Am about ready to get a 24" pipe wrench and a vise and break open the thing. Any experience would be appreciated. Thanks a lot, Roger
-
Got Mine yesterday. How long have You used it? It`s an air compressor regulator. Adjustment screw with a spring and a ball. I guess anything that could be wrong with it is the quality of the spring steel. For 15$?!?!
-
Hey Challenger! This thang work? Bought it anyway. Thanks for the spacer advice. Skilsaw with an abrasive blade..1 minute. 60 minutes with a die grinder and 4 bits. Have to find a better way of doing this, but it`s done. Thanks again, Roger