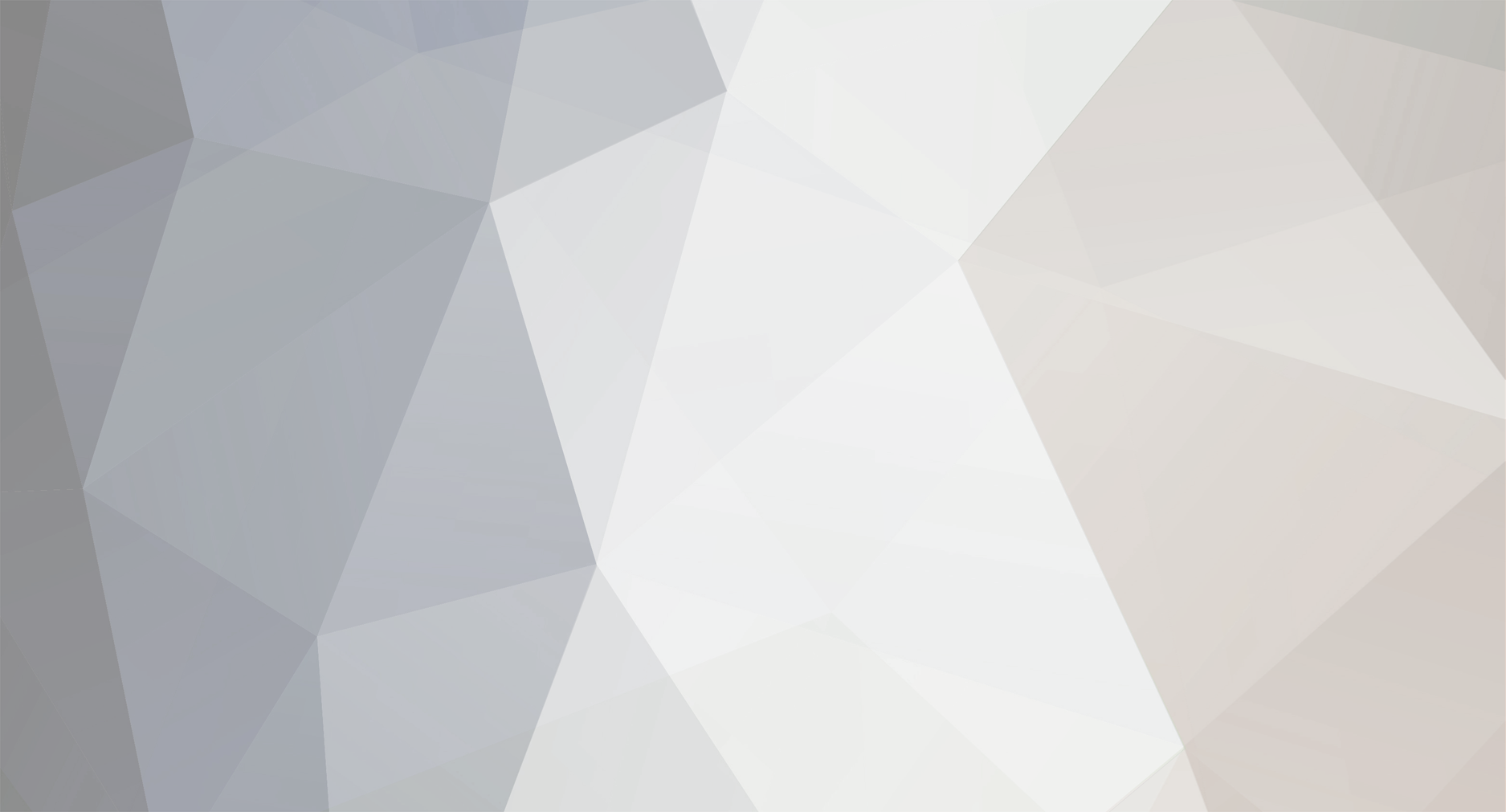
Ironhead
Members-
Posts
529 -
Joined
-
Last visited
-
Days Won
18
Content Type
Profiles
Forums
Blogs
Events
Gallery
Downloads
Store
Everything posted by Ironhead
-
Do you remember seeing a small hole in the upper driver's side corner of the windshield frame? I am not referring to the drain holes on the lower frame...this would be a smaller hole, maybe 1/8" in diameter.... My car has such a hole, and I do not know if it is supposed to be there for some reason (can't imagine what) or if maybe it was made when my car was media blasted or something. Debating whether to leave it or fill it with seam sealer before putting in the windshield.... Like I said, I cannot imagine the purpose of this hole, but it looks pretty much perfectly round like it is supposed to be there. Thanks!
-
ANOTHER Datsun Z/LS3/T56 Swap Thread
Ironhead replied to Ironhead's topic in S30 Series - 240z, 260z, 280z
It is very smelly when first applied, but I think that is primarily the carrier fluid which quickly evaporates.... After a few days I cannot really detect an odor to it, but keep in mind this is all in my shop which is full of various smelly chemicals. -
ANOTHER Datsun Z/LS3/T56 Swap Thread
Ironhead replied to Ironhead's topic in S30 Series - 240z, 260z, 280z
Since we all know how much Datsuns like to rust, I used no less than seven cans of 3M Cavity Wax and completely douched every blind spot on the car with the stuff. Primarily inside all the frame rails, and the rockers. I am also going to do the doors when I retrieve them out of storage. It spent a couple of days dripping wax. Then, after giving the car a week for the two-stage paint to harden a bit (it has remained very warm here) I carefully began final (I hope) assembly. No real rhyme or reason to it, other than trying to get all the difficult access bits attached while the car is still largely stripped. Very rewarding to have finally reached this point. Thanks for looking. -
I too just followed the SCCA rules. In my case 1.5"/.120" wall tubing, and .100" for all the reinforcing plates. IIRC those specs are good up to 2800# car. I sure as hell hope my car doesn't wind up heavier than that....but it could I guess.
-
I know the factory Porsche 935s had an aluminum roll cage, but again, they were raced long ago. I wonder if the ones still participating in vintage racing have been retrofitted with steel cages...?
-
I pondered the same thing, wondering if the floor is an adequately sturdy mount for seats. If you think about it, a seat is most likely to break free in a crash if the impact occurs from the rear. Then the entire weight of the driver will be slammed into the seatback, and the harness will do little/nothing to keep the driver/seat in place. In a frontal impact, nearly all of the driver's momentum will be captured by the harness with very little strain on the seat. Same with a roll-over. A side impact will be somewhere in between. This was my reasoning for installing a seat-back brace, this one specifically: https://www.bkauto.com/R_9020_Seat_Brace_Fixed_Back_Composite_Seats_p/r-9020.htm It bolts to brackets welded to the harness bar. Other than that, I welded seat mounts from square tubing that tie fairly securely into the frame rails, which really is the only significant source of strength in the floor pan.
-
280Z build w/ LS3 and 2015 Mustang spindles/8.8
Ironhead replied to 280Z-LS3's topic in Gen III & IV Chevy V8Z Tech Board
Great work! I'm sitting here kicking myself for not just going with the Ford diff from the beginning. Too late now. If it breaks I will go Ford then. -
I imagine most of you have already seen them....but there are black and white photos floating around detailing the cage design on one of the later BRE Datsun Zs from back in the day. A couple of things that stood out about them. For one, they didn't "stitch weld" the OEM joints, they ran solid beads down the entire sheet metal joints. The other thing that surprised me was that they used a hell of a lot of tubing. My conclusion was that they were much more concerned with rigidity than weight, although I cannot tell from the photos if the tubing is chrome moly or mild steel. The design would make entry and exit of the car difficult, to the point that it would be pretty much just like leaving the doors closed and climbing in/out of the window. This was a long time ago, and I imagine cage design has advanced since then. I suspect they could have had virtually identical rigidity with fewer tubes. But, on the other hand they were certainly successful cars in their day.
-
ANOTHER Datsun Z/LS3/T56 Swap Thread
Ironhead replied to Ironhead's topic in S30 Series - 240z, 260z, 280z
Finished the painting. I am definitely ready to move on to something else: -
I just wanted to weigh in....I too consider McMaster-Carr to be the best retailer on the planet.
-
280Z build w/ LS3 and 2015 Mustang spindles/8.8
Ironhead replied to 280Z-LS3's topic in Gen III & IV Chevy V8Z Tech Board
For some reason, both those colors look metallic to me. They aren't? -
Boy is this the truth. I did it, and just remembering doing it gives me PTSD. Actually I would rank the entire stitch welding process, if one is fairly thorough about it, as very high on the PITA scale. Probably the thing I hated doing most on my car. Of course, it isn't the welding, it's removing the paint/primer/seam sealer so you can weld it.
-
ANOTHER Datsun Z/LS3/T56 Swap Thread
Ironhead replied to Ironhead's topic in S30 Series - 240z, 260z, 280z
I am (currently) using the GM oil pump, and Gary Armstrong of ARE told me exactly the same thing. I was unsure if he was trying to sell me on a dry sump pump with a pressure stage, or was speaking the truth. It was moot anyway, I might have bitten but a larger pump would simply not fit in my application without HUGE modifications. What is the upgrade you refer to? -
I don't know honestly what is "correct practice" (you will get a bunch of opinions) but I did stitch weld this area, for whatever that's worth (not much). There are many informed, intelligent car fabricators who will say that stitch welding itself is a waste of time. At the end of the day you will have to do what seems correct (and worth the effort) to you.
-
ANOTHER Datsun Z/LS3/T56 Swap Thread
Ironhead replied to Ironhead's topic in S30 Series - 240z, 260z, 280z
I actually hadn't heard that. I'll have to look into it. So far the LS3 is bone stock except for changes I made to the oiling system. It's funny, I have tinkered for years with assorted Japanese and German inline engines, but I have no experience whatsoever with US pushrod V-8s. -
ANOTHER Datsun Z/LS3/T56 Swap Thread
Ironhead replied to Ironhead's topic in S30 Series - 240z, 260z, 280z
Bit of prep work involved to paint a 45 year old car. -
ANOTHER Datsun Z/LS3/T56 Swap Thread
Ironhead replied to Ironhead's topic in S30 Series - 240z, 260z, 280z
Some places are simply impossible. Like the top of the cage where it sits 1/16" from the roof. After I lowered it to weld all the joints, I sprayed the top bars with epoxy before raising it again and welding it in place. So at least they should be protected from corrosion. As far as the color coat, the most I "might" have gotten on top of the bars is a dry gritty dusting which would not offer much in terms of corrosion protection. In areas where there is just a limit on what is possible, all you can do is your best and live with it. -
ANOTHER Datsun Z/LS3/T56 Swap Thread
Ironhead replied to Ironhead's topic in S30 Series - 240z, 260z, 280z
It does where I did my part, but all the weird angles painting the cage and what not left me with overspray/rough spots in places. I honestly don't know how that could be completely avoided, so I am just moving forward and not worrying about it. Thanks for the comments. -
280Z build w/ LS3 and 2015 Mustang spindles/8.8
Ironhead replied to 280Z-LS3's topic in Gen III & IV Chevy V8Z Tech Board
The Lizard Skin sound control is heavy. You pick up a gallon can of that stuff and you swear it is made of lead. I would agree it is "easy" to install, but the prep beforehand (masking) is an absolute MoFo. I used right around two gallons doing the whole car. It also doesn't make the car "quiet"....it just changes the general ambiance from that of a tin can to more of a fiberglass can...if that makes sense. -
ANOTHER Datsun Z/LS3/T56 Swap Thread
Ironhead replied to Ironhead's topic in S30 Series - 240z, 260z, 280z
Been scrambling the past few weeks trying to get the shell painted before the weather turns cold.... Started by masking off exterior areas that are going to be done in base/clear: Then sprayed gray epoxy over everything and started working on seam sealing. I sealed pretty much everything, while making sure to keep drain/vent holes open so that if water does find its way in, it can drain/evaporate. If anyone is looking for a seam sealer, I messed with a few of the 2K products and settled on SEM 39777. It is flowable, and can be brushed into tight areas, but is not so liquid that it wants to run everywhere. And being a 2K product, once it cures in about 15 minutes, it is impervious to just about everything. The only thing it is not good for is filling larger gaps, for that I used 3M 08308. After that, a coat of white epoxy (changed colors to help with coverage, and because single stage green will go right on top). I painted all this in one day to stay within all the re-coat windows. It doesn't look like that big of a job, but my ass was kicked when I was done and I think I had epoxy coming out of my ass... Next step was single stage green (Delfleet DSS) which in the photos has already been masked for the application of Lizard Skin and Raptor Liner. The masking needs to be exhaustive, because these products are thick enough to completely fill in small threaded holes and such, so they ALL had to be masked. PITA. Next, Lizard Skin sound deadener (two coats) was sprayed in pretty much all of the interior, followed by two coats of Lizard Skin temp control on the firewall and trans tunnel. Neither of these products are particularly durable, so everything was covered with a thick coat of Raptor Liner. I also did the door bars with Raptor Liner since they will constantly be getting climbed over, and I wasn't sure how long straight paint would last. I also sprayed Raptor Liner in the fender wells, and on the bottom of the floor pans. This is where everything stands now. The remaining "gray" areas will be painted in base/clear, after another buttload of masking. Confident I will finish though, before weather turns too cold... Thanks for looking. -
280Z build w/ LS3 and 2015 Mustang spindles/8.8
Ironhead replied to 280Z-LS3's topic in Gen III & IV Chevy V8Z Tech Board
I've been pondering all this for the length of the build. I haven't treated anything yet, as I am still finishing painting.... First of all, I have one of those spray guns with the spray head at the end of a 14" wand, so I can get paint in some pretty tight places. The problem is, since it doesn't run into cracks and crevices, I figure it is still only marginally effective. You aren't going to get serious rust problems on most open sections of unpainted sheet metal...you would just get surface rust. Problems start in the lower pinch welds and other places where water can just accumulate and remain there. How can you possibly treat those areas other than using wax? So, the only conclusion I keep coming to is cavity wax, smell or no smell. There are several places where spraying paint simply isn't an option, and cavity wax is about the only solution on the market. I am aware of the Eastwood "inner frame rail" paint, but it has pretty mediocre reviews, and I don't see how it can possibly be as effective as cavity wax. For example, I am positive I burned any finish off the inside of the frame rails while welding on the Bad Dog rails. I don't see how that can be covered except by a runny product like the cavity wax. I know OEM repair specs call for the application of cavity wax in all sorts of places that could vent into the passenger compartment, so I imagine (hope?) that the smell fades after some reasonable period of time.... Regarding the Tamco Mono Coat, I agree with you. I read about it, and they make the point of saying it is "nothing like POR-15", but in every way, is sounds exactly like POR-15....LOL. I'm sure there are only a limited number of chemistry solutions for a reasonable price for problems like treating rusted metal. I wager Rust Bullet is pretty much the same stuff as well. I've overcoated nearly all of the Rust Bullet I used, first with epoxy, then seam sealer, then epoxy again, single stage paint, Lizard Skin, Raptor liner. I haven't encountered any problems with lifting or incompatibilities. -
280Z build w/ LS3 and 2015 Mustang spindles/8.8
Ironhead replied to 280Z-LS3's topic in Gen III & IV Chevy V8Z Tech Board
It is a tedious process, isn't it? Frustrating and repetitive as hell... What worked best for me was to attack the visible seam sealer with a wire wheel in a grinder, then switch to an assortment of dental picks and small screw drivers, and if none of that worked, I burned it out. I still wound up with a lot of contaminated welds to deal with. You also have to be very careful down the road when prepping the chassis for painting to make sure all the bare metal is protected from rust with epoxy and seam sealer. Otherwise the process of stitch welding can introduce a lot of new paths to corrosion. Looks like you are doing a good job with it. -
Apex Engineered: My evolving experience
Ironhead replied to BoulderCharles's topic in Non Tech Board
Agreed, and it certainly isn't just machined parts. I hate to outsource anything, because often as not their quoted ETA is utterly meaningless at best, a deliberate lie at worst, and they pretend to not understand how anyone could feel the time taken to complete a job even matters. I'm currently seven weeks in waiting for a mountain of parts to be powder coated, and I thought the quoted ETA of three weeks was a bit long in the first place... Not car related, but I was once quoted three weeks by a gunsmith for a hunting rifle to be re-barreled. Wound up taking the guy 14 months...no communication, no apologies, nothing. When I picked the gun up, he just short of shrugged about it and said "yup" when I asked him if he realized it took well over a year.... Most of these sorts of flakey establishments tend to stay in business, so there must be some customers out there who genuinely don't care how long it takes. -
A musician's therapist (The $300 Z)
Ironhead replied to Zetsaz's topic in S30 Series - 240z, 260z, 280z
It's funny, after I bought my car and was stripping it down, I found some PO had put Dynamat on both sides of the trans tunnel. That stuff was so hard to remove, I find myself scared to use it. -
Yeah, I got nothing. That's better prep than I did. Definitely disconcerting.