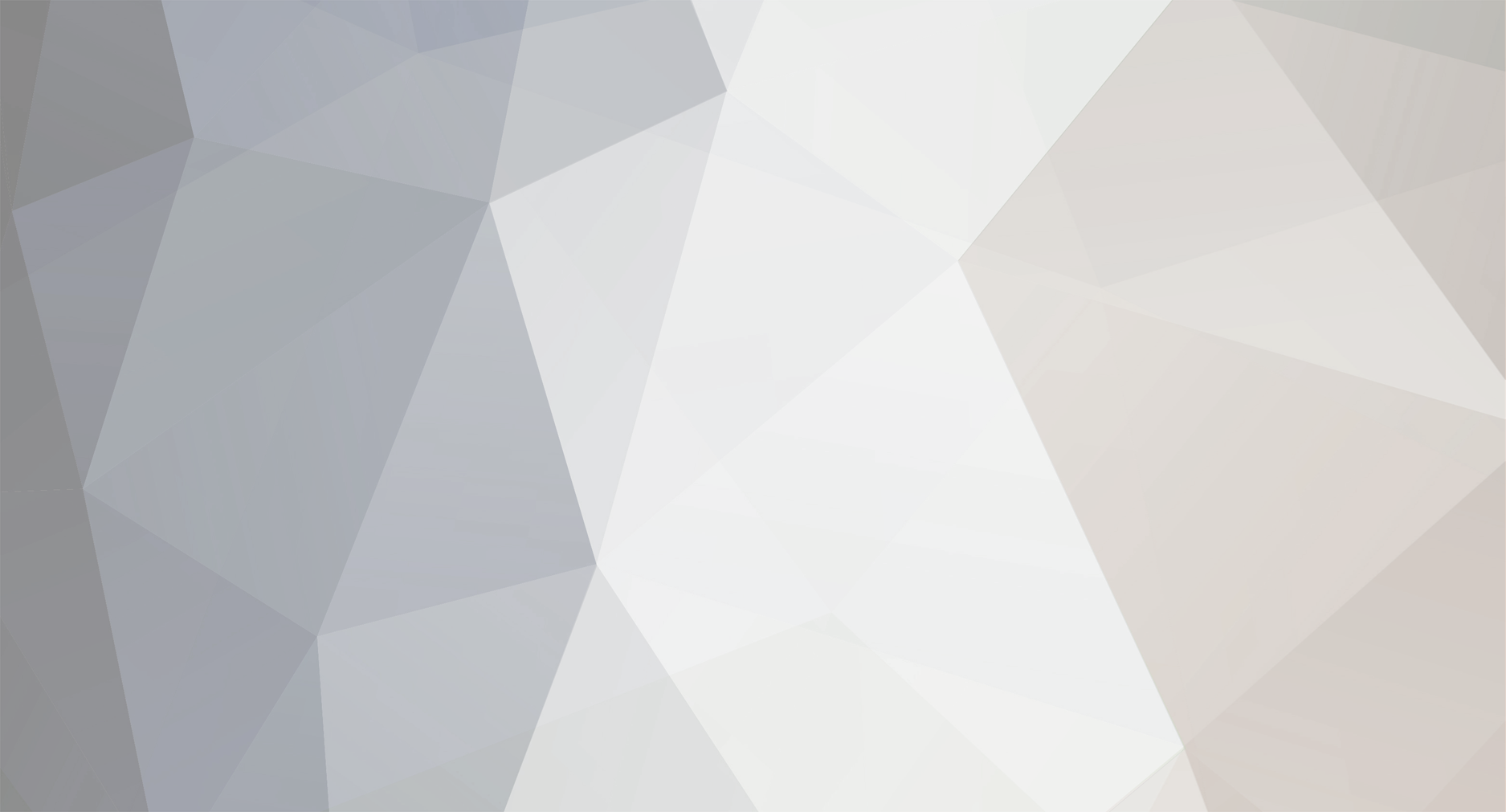
Ironhead
Members-
Posts
529 -
Joined
-
Last visited
-
Days Won
18
Content Type
Profiles
Forums
Blogs
Events
Gallery
Downloads
Store
Everything posted by Ironhead
-
ANOTHER Datsun Z/LS3/T56 Swap Thread
Ironhead replied to Ironhead's topic in S30 Series - 240z, 260z, 280z
All I have really done the past couple of weeks is work on installing the radiator and plumbing the coolant and oil lines. The radiator is a Ron Davis unit. He said he already had a template for a Datsun Z/LS swap radiator. I told him I wanted the biggest radiator that would fit, just to hopefully prevent any future cooling problems. I should have been careful what I asked for. The radiator does fit, but it has to be installed absolutely perfectly or it hits the frame rails, or the fill cap hits the underside of the hood. And the hose fitting interferes with my passenger side strut tower brace which had to be "clearanced". I finally got the radiator installed, but it took a lot of fiddling. It clears the frame rails by less than 1/8" on each side. If I was doing this all over again, I would have passed on using AN hose and fittings for the radiator hoses. The AN20 fittings are just too bulky and expensive. They eat up too much of the available room between the front of the engine and the radiator fans. I got everything to go in, for the time being at least, but I am rapidly running out of space in the engine compartment. The oil lines were a similar drill, trying to route them so they use up as little space as possible and allow as much clearance as possible for the exhaust. Thanks for looking. -
ANOTHER Datsun Z/LS3/T56 Swap Thread
Ironhead replied to Ironhead's topic in S30 Series - 240z, 260z, 280z
So, in this thread: https://forums.hybridz.org/topic/129738-someone-please-refresh-my-memory/ I was inquiring as to whether or not I could remove the horn brackets, as I forgot what they were for. When others confirmed they were for the horns....they were destined to be gone...because they are in the way of my oil cooler plumbing. So I figured, easy job, good access, just three spotwelds on each bracket....I'll just drill them out then remove the brackets. That way I can save them if for some lame reason I decide I need them after all. No sign of trouble ahead. Well, I dunno, something about spot-welding relatively thick steel or something. My spot weld drill-out bit got partway through the metal, then hit a patch so hard it might as well have been glass. Seriously, the bit would just spin without removing any metal whatsoever. I tried a different bit, same result. And, there was way too much metal remaining to just pry or otherwise force them off. So, all that remained was to grind the damn things off. I hate grinding metal...you know...loud, makes a mess that gets everywhere, that sort of thing. But what else could I do? Funny how jobs that appear easy often wind up being a serious PITA. I know all you fellow car dorks understand.... PSA: If you find yourself having to do something like this, I found that a 36 grit flapper disc removes metal MUCH faster than a grinding stone. I would have assumed the reverse. Sorry for the rant/tangent. -
What I did/will do was this: I drilled drain holes in the low spots of the Bad Dog rails, directly below where the OEM rails had the drain holes. Then I sprayed the inside of the Bad Dog rails with epoxy prior to fitting them. That should leave only the weld areas to have bare metal. This might be a bit anal, but I am going to use a small brush with Rust Bullet or a similar product to get the cracks and crevices from the outside around the welds, where epoxy won't spray in well. Then a coat of epoxy, and seam seal the cracks on top of the epoxy. Then paint/undercoat. Then do the insides of the rails with Eastwood inner frame paint. Then, if I feel really anal, SEM cavity wax on top of that. MIght be a bit much...but none of these steps are particularly expensive or time consuming...figured I might as well do all I can to prevent future problems. As was stated earlier, these cars have so much layered metal and moisture traps, it's a wonder they haven't all rotted away to nothing. I have noticed in many places though, that the factory spot welds were done right through the factory yellowish primer. It looks nothing like standard weld-through primer, so I have wondered what sort of formula it was. I have very little faith in rattle can weld-through primer. Even though it is "weld through", it is so darn fragile I think on balance you are better off just using epoxy and cleaning it off the small areas that need welding. There is no perfect answer. So I probably won't drive the car in the rain....LOL
-
Someone PLEASE refresh my memory.....
Ironhead replied to Ironhead's topic in S30 Series - 240z, 260z, 280z
Thanks guys, you rock! Now I am going to ditch them without hesitation.... Kind of surprising really. Those are heavy metal brackets with dual M8 threads on each. Seems like overkill to mount horns.... -
Someone PLEASE refresh my memory.....
Ironhead replied to Ironhead's topic in S30 Series - 240z, 260z, 280z
It looks factory...standard spotwelds and M8 weld nuts. I too perused the 'net and could not find them on other cars... Screw it....I'm takin them off. If it turns out to be a mistake it'll be easy enough to replace them. Thanks much for the input. -
My car has been apart for so long I cannot remember... My car is a '74 260z. What attaches to the bracket I have circled in the photo? There is an identical one on the other side. They are sort of in my way, and I was about to remove them, but I can't remember what they do... Can anyone with a decent memory or an intact car help me out? Thanks!
-
Thoughts on T3 'Rear Power Braces'?
Ironhead replied to artishard116's topic in Brakes, Wheels, Suspension and Chassis
I honestly think these parts are pure bling....which is ok....but I don't see any performance improvement they would provide at all.... It seems to me there would be more benefit if they designed a part that tied together the rear control arm bushings, since they sit out somewhat cantilevered away from the body, I could see where there would be relative movement between them when loads are introduced. Even then, the benefit would be minimal, since the TTT conversion already has the "dog bone" tying them together. It would primarily be lateral movement rather than fore and aft movement, and these TTT parts seem designed only to address the fore and aft. As someone else mentioned, the control arm bushing mounts are tied pretty solidly together fore and aft by the control arms themselves. I think TTT knows that if they crank out cool, machined, anodized aluminum parts that bolt right into place, people are going to buy them just for the bling alone....without really thinking through whether there will be actual performance benefit. IMHO, these parts are a perfect example of that. I could see some appeal if the replacement front cross-member was at least designed to facilitate a dual exhaust....but it isn't. -
Sirpents 260Z / C32 AMG Powered RS30 - Australia
Ironhead replied to Sirpent's topic in S30 Series - 240z, 260z, 280z
Fantastic work on a very ambitious project! Glad you are back in shape to continue. -
ANOTHER Datsun Z/LS3/T56 Swap Thread
Ironhead replied to Ironhead's topic in S30 Series - 240z, 260z, 280z
Just the latest (and hopefully last) iteration of my FPR install and plumbing. -
ANOTHER Datsun Z/LS3/T56 Swap Thread
Ironhead replied to Ironhead's topic in S30 Series - 240z, 260z, 280z
I got the transmission installed in the car. I am using the Hoke cross-member and tranny mount, but since I have the car stripped I figured it made more sense to weld in the support plates rather than use the bolt in Hoke units. So I cut new ones out of .25" steel and welded them in. As posted earlier, my plan was to use the Sikky shifter, since the T56 Magnum tranny I am using apparently moves the shifter further forward that with the standard T56 the Hoke kit was designed for. The problem that developed with this plan was that I really did not like the feel of the Sikky shifter. It added a lot of slop and "vagueness" to the shift linkage, and I did not want to build a car that (to my tastes) shifted poorly. So I decided come hell or high water I was going to use the Tremec shifter. This involved welding up the OEM shifter cutout, and cutting a new one for the Tremec shifter. Not a big deal, but I am also going to have to modify my (completed, I thought) dash structure which would now interfere with the shifter. If I am honest with myself, I think I was just trying to dodge the additional work and that the Sikky shifter would save me from it. I also found that I had to further lower my steering rack, in order for it to clear the oil pan. With the tranny installed and bolted up, I found that the engine sat in a more level attitude than I expected, which pivoted the front of the engine back down onto the steering rack. So I will have to further space down the tie rods as well. I know the long shift lever evokes a school bus and won't win any style points, but I prefer having the shifter as close as reasonably possible to the steering wheel. This shift lever accomplishes that, as well as angling backward to make up for the slightly-too-far-forward shifter pivot. I think I did the right thing not using the Sikky shifter, I cannot believe how nicely the setup shifts with the stock Tremec shifter. It is silky smooth and very precise. I am just pissed off that I spent the money on the shifter that I won't be using. Since I installed it I cannot really in good conscience return it....it no longer looks perfect and new. Thanks for looking. -
ANOTHER Datsun Z/LS3/T56 Swap Thread
Ironhead replied to Ironhead's topic in S30 Series - 240z, 260z, 280z
I'm using the Bosch Motorsport mount that New Zed linked a few posts ago, just because I already had one on my BMW and it was easy to pull off for mock-up. The Radium one looks better though....just because it comes set up with AN6 ORB threaded ports. The Bosch one has M14 threads, but adapters to AN6 are easy to find. Boy though, Radium is sure ripping people off with their price on the Bosch 3 and 4 bar FPRs. I just bought a 4 bar from Pelican Parts and it was less than half what Radium is charging. The only possible issue, is the Bosch FPR is really small, so small it is kind of disconcerting compared to most of the aftermarket ones. I worry that it might not handle the fuel flow of my engine/fuel pump combo. But this same Bosch FPR was used on the 2001-2003 Audi S6, which was a fairly high HP car, so hopefully it is up to the task. If not, it will be a simple matter to switch to a higher flow unit, without significantly re-designing my plumbing setup. I don't think there are specifically problems with Aeromotive FPRs so much as that the aftermarket ones in general are not designed and made to the standards of the OEM ones. Newzed is right on the money with that as far as I have seen. Plus all the aftermarket ones are adjustable, which IMHO adds another unneeded variable. I have read of several high end automotive tuners who won't tune cars with adjustable FPRs, just because there is really no need for adjustable fuel pressure, and they have found that the adjustable FPRs are much less reliable. Fuel pressure problems can quickly kill a highly tuned engine....from going lean and detonating. I just did some more reading....these Bosch FPRs are rated to "reflow" up to 220 LPH...and my Bosch 044 pump is rated to deliver 220 LPH at 4 bar. So, I should be good, considering it won't generally be sending back all the fuel the pump is providing, at least not unless the engine isn't running. Apparently if the FPR has too little capacity, you will see a rise in fuel pressure beyond what it is rated at. This wouldn't be catastrophic, like going lean might be. I will just have to monitor fuel pressure for a bit once it is all up and running, to make sure all is good. -
ANOTHER Datsun Z/LS3/T56 Swap Thread
Ironhead replied to Ironhead's topic in S30 Series - 240z, 260z, 280z
My fuel pump is a done deal. The cell has an integral trap door reservoir and the ubiquitous Bosch 044 pump. I don't know the specs exactly, but I know that pump will handle far more power than I will ever have in this car. Honestly my intent is to leave the LS3 stock....LOL....I know, I know, famous last words. But I have done my share of messing with modified engines, and wanting a break from that is one of the main reasons I went LS3 in the first place. The problem with highly modified engines....yeah they go fast....but they need good gas....and the biggest problem for me is that no matter how much time you put into it, you can never get a perfect tune. I don't mean at WOT....that's easy....I mean part throttle and idle and all that. My current plan: I borrowed the Bosch FPR adapter off my BMW for fit up. I am going to "Y" the AN8 fuel supply line from the cell into two AN6 lines, one going into each fuel rail. The FPR adapter will mount to one of the heads and will be plumbed between the two fuel rails. It will use a Bosch 078133534C 4 Bar (58 PSI) FPR for an Audi S8 (and numerous other Audis). Then an AN6 return line back to the fuel cell. This might be a bit of overkill, but at least I know I won't have to re-do it all down the road. Thanks again to all for the input. Very helpful. -
ANOTHER Datsun Z/LS3/T56 Swap Thread
Ironhead replied to Ironhead's topic in S30 Series - 240z, 260z, 280z
Brakes are already plumbed....without hard lines. Honestly what sold me on that decision....I saw photos of one of the recent cars used in the German DTM series. These are arguably the most advanced and technically sophisticated racing cars on the planet (rules are much less restrictive than F1). This DTM car's brakes were 100% plumbed with braided teflon hose. So I figured if there was a performance penalty, it must be minor.... But this has been a great source of insight about FPR plumbing. I am pretty much convinced it is worth the slight increase in complexity and plumbing to put the FPR close to the fuel rails, so that is my current plan. I know from my past experience that what Newzed says is dead on: If you can find a way to implement them, OEM style FPRs are much more effective than all the assorted aftermarket ones, which are pretty much all the same. I had to return a car I owned in the past to a "closer to stock" setup in order to pass smog here in California. I had been using an aftermarket FPR, and was just living with fluctuating fuel pressure. Well, to pass smog, I returned to the stock FPR. It held the pressure dead on, right where it was supposed to be. Go figure...... -
ANOTHER Datsun Z/LS3/T56 Swap Thread
Ironhead replied to Ironhead's topic in S30 Series - 240z, 260z, 280z
Yeah, that's the setup I have on my BMW. With it you can use nearly any fixed pressure Bosch FPR. I am looking at Audi FPRs, because they use a Bosch 4.0 Bar which is about 58 PSI, should be perfect for LS3. The only hassle with that Bosch Motorsport stuff is that you generally have to order it from the UK. For some reason no one in the USA seems to stock any of it. -
ANOTHER Datsun Z/LS3/T56 Swap Thread
Ironhead replied to Ironhead's topic in S30 Series - 240z, 260z, 280z
I have a track car with a very buzzy four cylinder engine. I can tell you that I tried Aeromotive FPRs (2) on that engine. The vibration killed them both, very, very quickly...like within 5K miles, and I started to get completely erratic pressure. Switched to a Bosch Motorsport FPR....trouble free ever since. One thing that is really annoying to me about all the aftermarket FPRs....they are all adjustable. The only reasons I can think of for an adjustable FPR: 1. Your injectors are near max duty cycle and simply upping the fuel pressure is quicker and easier and cheaper than buying bigger injectors. 2. It is much cheaper for the manufacturer to sell one "adjustable" FPR than market different models with different pressures. I have found that fixed pressure FPRs hold a steady pressure much better than the adjustable ones. -
ANOTHER Datsun Z/LS3/T56 Swap Thread
Ironhead replied to Ironhead's topic in S30 Series - 240z, 260z, 280z
I don't think it is specific to the FPR....these aftermarket FPRs are all the same. Just a rubber or teflon diaphram and a spring. If it is adjustable, a screw to adjust the spring tension. That's it... I spent some time reading various internet debates about FPR before or after the fuel rails. Some of them highlight the levels of idiocy that can be found on the internet, others almost echoed discussions of religion. Pretty entertaining... Having said that, the largest consensus was that FPR after the fuel rails was "best", but they never said exactly why. Just like the Aeromotive link....it says "after" is "optimal" but it doesn't say why. It also says that mounting it before the fuel rails would work. Well, if it will work, why are they clearly discouraging it? Everyone who had actually tried mounting the FPR before the rails said that it worked fine. So I don't know what to think. The only difference I can imagine it making would be fuel temperature. But even that is not cut and dried. With a returnless setup, the fuel would spend more time in the rails near the engine (I think). But with the return setup, the fuel would make two long trips to the engine and back in fuel pipes directly over the exhaust. With the setup I am pondering currently, the FPR and return line are in a "cool" location. So I don't know what I am going to do. Just like with the brakes, I am leaning toward skipping the hard lines and just using flexible braided hose the whole way. I hate working with hard lines, I find the flared ends more prone to leak than hose fittings, and the only real advantage I see to them is a bit less cost and bulk. Actually I am not even sure hard lines cost less, because I always screw up so much of the tubing during the bending process and have to trash it....LOL Thanks for the imput, greatly appreciated. -
ANOTHER Datsun Z/LS3/T56 Swap Thread
Ironhead replied to Ironhead's topic in S30 Series - 240z, 260z, 280z
I thought about that. It's certainly possible. Whether it would be a significant/measurable benefit is another question. I figure the fuel is probably fairly warm with either option. It still has to make its way to the engine through a fuel line generally directly above the exhaust. I have to believe that a braided hose with a teflon or rubber liner would transmit much less heat to the fuel than the standard hard steel fuel line would. The only other reasonable option would be to run the fuel line through the interior of the car, which I don't want to do. It seems like when the fuel is atomized as it squirts out the injector, it would almost instantly take on the temperature of the incoming air....or close to it. The injected fuel volume is so small compared to the air volume. But there is no doubt that warm fuel would make a warmer intake charge than cold fuel would. I think I am just going to opt for the simplest setup though. -
ANOTHER Datsun Z/LS3/T56 Swap Thread
Ironhead replied to Ironhead's topic in S30 Series - 240z, 260z, 280z
I've been trying to get the fuel lines finished through the trans tunnel so I can install the transmission. I assumed all along that I would be running a supply and return line from the engine to the fuel cell, just because every fuel injected car I have ever dealt with worked like that. But I learned that most LSX powered cars have the fuel filter and fuel pressure regulator mounted together at the rear of the car, with only a supply line going to the engine. This seems like the cleanest, simplest approach, and frankly I don't really understand why other cars generally do not plumb it this way....? So I was looking for someplace around the rear differential to mount the FPR, and thought why even run a return line that long? So I mounted the FPR right on top of the fuel cell, with perhaps a 10" long return line. Then one supply line will go from the fuel cell enclosure through the floor of the car and up to the engine through the trans tunnel. I cannot think of any reason why this won't work....but if anyone here can please speak up. -
ANOTHER Datsun Z/LS3/T56 Swap Thread
Ironhead replied to Ironhead's topic in S30 Series - 240z, 260z, 280z
Dave, I really don't know the significance of the badging. All I know is that I wanted the GM gearing, ordered it from Summit, and they call it a "Super Magnum". I have the shifter installed now and I was screwing around to see how the shifting felt. It seems like it shifts nicely, but you can definitely tell this is a beefy tranny with a lot of torque capacity. It is not a "flick of the wrist" style transmission. I did get the 4" setback version. I think I might install a longer shift lever though. As I mentioned, I am not really a fan of "short shifters", and I tend to like a taller lever that is closer to the steering wheel anyway. I will wait on see how it feels when it's in the car. I am just trying to finish running the fuel line through the trans tunnel then the tranny is going in. -
ANOTHER Datsun Z/LS3/T56 Swap Thread
Ironhead replied to Ironhead's topic in S30 Series - 240z, 260z, 280z
The problem is that my tranny is the T56 "Super Magnum"....and it uses a six bolt flange for the shifter rather than the four bolt flange on the regular T56...like in the GTO. I realized this because Sikky sells different shifter kits for the T56 Magnum/Super Magnum than for the standard T56. This is the one for the standard T56: This one is for the T56 Magnum: You can see that they are not interchangable, so I knew the GTO shifter would not work in my case. After pondering this for a while, I wound up just ordering the Sikky shifter. All the other potential solutions I could come up with were either very complex or marginal from a functional standpoint. Thanks for the input guys. -
I belong to a specialized BMW site as well, and the posts there have slowed way, way down from their peak around 2006-2007. I have been told it is because most participants have shifted to FB. I don't know if that is true or not, since I have nothing to do with FB, and never will.
-
ANOTHER Datsun Z/LS3/T56 Swap Thread
Ironhead replied to Ironhead's topic in S30 Series - 240z, 260z, 280z
I got the oil tank bolted in. Clearances are tight, particularly between some of the fittings and the rear coil, but I think it is enough unless a motor mount fails or something. This is the drain at the bottom of the tank. Hopefully will make things easy at oil change time: Most of my experience in the past tinkering with engines has been on four cylinder motors, and I am continually surprised how much heavier all this V8 stuff is. Most of the steel flywheels I looked at weighed in the 35# range, which seems really heavy. So, I went with a 12# aluminum one. There were so many clutches available for LSX engines, it is kind of mind boggling. I ended up going with this one from Centerforce, because it had good reviews for the sort of use I have in mind. Also, because it was orange. But I think that goes without saying. Here again, this clutch was so damn heavy it made me wonder why I bothered with a lightweight flywheel: I am getting the transmission ready to go in. I removed the weird (to me anyway) GM hook-ups for the hydraulic line to the clutch slave, and just used standard AN4 fittings and hose. I also rigged it up for a remote bleeder valve, so I don't have to crawl under the car and work my fat hands into the trans tunnel to bleed the clutch. Small bit of work now should make things easier down the road. Only other "development"....I took some measurements and found the shift lever on the T56 is going to be about 4" too far forward to protrude through the stock opening in the trans tunnel. I don't know why I was assuming this would just line up perfectly (why would it?), but I think I was. I have no real problem welding up the existing opening and moving it forward, but that is going to put the shift lever very close to the dash, and probably also a bit too far forward ergonomically speaking. So I did a bit of searching and found this: https://www.sikky.com/product/t56-magnum-4-shifter-relocation-kit/ I am generally not really a fan of "short shifters", but aside from being a bit overpriced, it seems like this would otherwise solve my issue. Anybody here used one of these, or heard anything about them? Thanks for looking. -
ANOTHER Datsun Z/LS3/T56 Swap Thread
Ironhead replied to Ironhead's topic in S30 Series - 240z, 260z, 280z
I do have a Braille, but sadly it doesn't quite fit. It might have worked if I went with a really small Braille, but I wanted one that would reliably start the car....and it is a bit too large to fit in the space left over. I planned all along to put the battery in the rear next to the fuel cell anyway. I am probably going to run the wiring harness through the firewall in the area just outboard of the oil tank. -
ANOTHER Datsun Z/LS3/T56 Swap Thread
Ironhead replied to Ironhead's topic in S30 Series - 240z, 260z, 280z
LOL...Yup....I have my seat slammed on the floor....as far back as it can go (until the sloping roof starts to take away the headroom), and my pedals adjusted as close to the firewall as possible. I mean, after all this, I fit Ok, even with a helmet on....but there is NO spare room. -
ANOTHER Datsun Z/LS3/T56 Swap Thread
Ironhead replied to Ironhead's topic in S30 Series - 240z, 260z, 280z
Nothing can ever be simple.... I knew it might be a bit of a challenge mounting the oil tank. A lot of track cars mount it in the passenger compartment, which I didn't want to do...for many reasons. I ordered a smallish tank (1.5 gallon) and figured it would fit somewhere in the engine compartment. But it really didn't. It "might" have fit between the radiator and front of the engine on the driver's side, but I can't be sure as I do not yet have a radiator. It would be close at best, and kind of lame in terms of weight distribution and all that (not that a gallon and a half of oil is all that heavy). So the only decent solution seemed to be more cutting/grinding/welding. I made sort of a "perch" for it below the OEM battery location. My plan is to install a bulkhead fitting in the drain hole at the bottom of the tank, to protrude through a hole in the bottom of the "perch"....to make it easy to drain the oil when needed. The bottom plate is .10" so it should easily support the tank's weight, and then I will just use one mounting bracket to hold it against the firewall. Mocking everything up it seems like this will work.