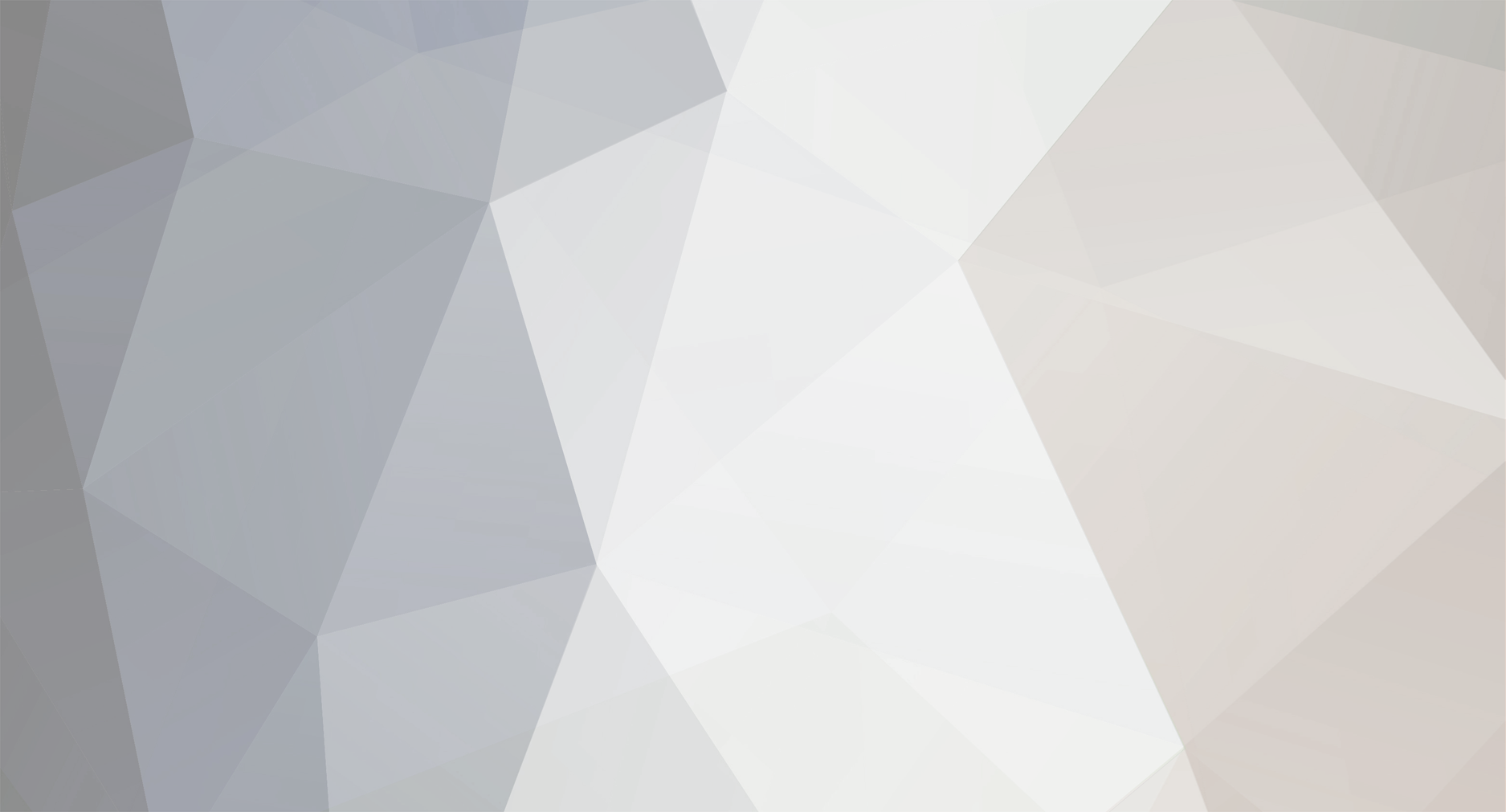
Jolane
Members-
Posts
351 -
Joined
-
Last visited
Content Type
Profiles
Forums
Blogs
Events
Gallery
Downloads
Store
Everything posted by Jolane
-
I used a chip (hex driver?) to isolate my processor I/O from the driver chips. This also allowed me to "step-up" the signal voltage from 3.3V (uP) to the 5V required for the coil driver. I assume that the driver in the LS1 coils requires a TTL level input, which I believe is spec'd at higher than 3.3V. The interface chip I used was very inexpensive and easy to use. The opto-isolator was also serendipitous in that I needed to invert my signals during start-up to avoid firing all the coils initially (uP initialized with all pins high state). Joshua
-
13" rotors and Outlaw 4000 calipers
Jolane replied to blueovalz's topic in Brakes, Wheels, Suspension and Chassis
Blue, That looks like it fills the wheel nicely. Question though; why weld the caliper bracket to the spindle mount? Seems like the 2 bolts would have been just fine. Is the spindle very weldable stuff (as in strong)? Steel? Cast Iron? Joshua -
rear poly bushings on outboard end of CA
Jolane replied to blueovalz's topic in Brakes, Wheels, Suspension and Chassis
Holesaws work great too. I built some monster jack stands last fall and used one 7/8" holesaw to cut 28 holes in 1/4" thick steel tube, and the bit still looks excellent. Just slow down the cut, use cutting fluid, clear the chips often, and it works well. Joshua -
rear poly bushings on outboard end of CA
Jolane replied to blueovalz's topic in Brakes, Wheels, Suspension and Chassis
-
Sam, a couple comments that I hope you don't mind in this thread. First, it seems that you really need a digital scope for this project. I used mine to measure the crankshaft speed directly from crankshaft sensor while the engine was running. I did this while the engine was running stock, so my system wasn't controlling it. This helped verify that my measurements were good enough. The crankshaft sensor I was using, along with a 4 position trigger wheel, provided excellent positional repeatability. I then had to find the accuracy and introduce an offset bias to correct for any machining errors (not a big deal). My uController had no problem keeping up with the input. Have you looked at or modeled the scheme for controlling the coils? This is a big deal on a V8 compared to a single cylinder. I provided my scheme in my paper. It was harder than I had expected though. You have to provide enough time for the coil to charge, and also advance the firing when the RPM goes up. This becomes more difficult as the RPM increases. I was using a waste-fire scheme, so I only had to control 4 coils. With 8 coils, the problem will be worse because you will want to charge 2 or more coils at the same time. I would recommend modeling this if you haven't already, and understand this better. The beauty of an engine is that it doesn't require the absolute best in timing accuracy, cinluding EFI. The system is actually rather slow compared to many other systems in the world. Building a great control system shouldn't be too difficult. The EFI should be the easy part because it doesn't require accurate timing at all (when I say accurate, I am talking nS). You probably would never see the difference in engine performance if your timing was off by even 1/2 a degree. Besides, the more precise the system, the better it must be tuned and calibrated, otherwise it is just extra information going to waste. In effect, ask yourself what you going to do with it, and why is it important? Does NI offer a student discount? It seems like you are set on using an NI board. I would strongly suggest looking at a uController, perhaps in parallel. They are used for applications like this daily. I am not trying to be a critic at all. I am very interested in your project actually. Please keep the updates coming. Hopefully this post doesn't come off differently. One thing engineers need to learn is what is good enough? Anything more usually costs more time, money, reliability, support, etc... Figure out the problem, what it requires, then solve it. Good Luck, Joshua EDIT: I meant to add that these sorts of project are VERY time consuming. They also eat a lot of money. My project ended up costing me ~$5K+ including a scope and a few iterations of the hardware. This was for the ignition only, and didn't include donated parts/materials/etc...
-
No Kidding...This would be completely awesome! I am not so sure that the market could support it though (especially considering Dynacorn is only producing bodies as engines/trannies/etc are readily available). Joshua
-
I also broke my big toe on my left foot...and it no longer bends now AT ALL at the outer joint. It was pinned back together for a month as I slammed it into very hard dirt riding my dirt bike. I also chattered the rest of my foot in the process. Anyways, it no longer bends, and sometimes that is bad (like when playing soccer, trying on new shoes, rock climbing, etc). Good luck with yours! Joshua
-
Why not just use a mixed signal processor? Everything can be done with very few components in this manner. As to why they are aren't used more often...I guess they really aren't needed. You don't need 1/500th degree resolution on the crankshaft. Engines are systems that can tolerate less resolution. Reliability is much more important. I believe Ford (or was it GM, I can't remember now) uses the Motorola 6811 based systems with 2MHz processor speeds. With efficient code writing (say in Assembly, or even machine language), the greter speeds are not required. There are many tricks that can be played also during processing to reduce the latency times. Hopefully you have a scope and signal generator to run this on before using a real engine. I found that my digital scope was a life saver in checking the timing sequences. Good luck, Joshua
-
Belt-driving and a rotary encoder (going where no one has gone)
Jolane replied to 280Z28's topic in Ignition and Electrical
Besides the timing issues, I am not sure how well that encoder will hold up to a side load and RPM induced from the belt tension. Further, that is an optical encoder, which means if any dirt, moisture, grime, etc get in there, it may not like that much! I would reconsider using a hall effect sensor, they are much better for dirty environments. I will PM you about getting that paper to you. Joshua -
Belt-driving and a rotary encoder (going where no one has gone)
Jolane replied to 280Z28's topic in Ignition and Electrical
I guess I still don't see the reason to have such a high resolution encoder. I built an DIS system from scratch 2 years ago for my Master's project. I used a 4 "tooth" wheel on the crank, and a camshaft sensor. It used an 8051 based ucontroller. It was interrupt based of course, and used a lookup table with a custom word size to control coil charging and delay. I would be happy to send you my paper on the system if you are interested. It did have some unique bits to it that might be helpful (such as how to chargeand fire a coil reliably). If you are not interested, no problem! Good Luck, that is a big project with demanding timing requirements. Joshua -
That's the method I used actually. I put new floors in, then put the stock frame rails in, then a piece of 1 X 3 tubing. I cut a clearance out for the stock frame rails and fit it over. I ran it back to the rear of the floor, then from there fabricated plates to connect to the subframe. I used the same 1X3 tubing, cut it down so it was ~1" tall, and ran two pieces from the tranny tunnel to the rocker, and attached my seats to those. Up front I plated the stock frame rails on bottom, inside engine bay, and top up to the sway bar mounts. I built a new crossmember and welded that in solid, and welded my engine mounts directly to the plated frame rails. Overall maybe I gained 50 punds (complete WAG), but feel like it is nicer and strong. I also welded in two strut braces to the firewall (1 1/4" x .065 tubing), and bolted in a brace across the engine bay. I just want to tie in my SFC to the rocker better. My main hoop is connected similar to Jon's, although I built a platform for the tube to land on, and boxed it in. My main hoop fit VERY tight to the inner panel. Joshua
-
I have a TKO600 in my 72. It does not seem wide up on top compared to the tranny tunnel, although I am moving my lines out of the tunnel anyways. The car is down to bare metal going through a complete build, so I can't comment on the shifting, noise, etc. It fit fine though in my application... Joshua
-
rear poly bushings on outboard end of CA
Jolane replied to blueovalz's topic in Brakes, Wheels, Suspension and Chassis
Thanks for the explanation Jon. I am trying to figure out which method I should use for my street car. I had a feeling this really applied more to a track car. Good luck and let us know how it goes (and which method you use). Joshua -
Belt-driving and a rotary encoder (going where no one has gone)
Jolane replied to 280Z28's topic in Ignition and Electrical
That seems like an aweful lot of teeth for a crank sensor. Are you building your own system? If not, what system are you planning on running? It seems like a belt drive would be a VERY bad idea since it can stretch/etc. You need something diffinitivly aligned with your crank. Do you a tertiary as well, or are you using a cam sensor also? Joshua -
Belt-driving and a rotary encoder (going where no one has gone)
Jolane replied to 280Z28's topic in Ignition and Electrical
I don't have any idea what you are doing...but what about using a non-contact sensor instead? Hall effect sensors work nice for this sort of thing. I used a gear tooth sensor to sense steel blocks in an aluminum wheel (crank shaft sensor). This may not have the accuracy you want though...just brainstorming. Joshua -
rear poly bushings on outboard end of CA
Jolane replied to blueovalz's topic in Brakes, Wheels, Suspension and Chassis
Blue, I vote to change the tubing to thick steel for that method. There is a lot of forces there, so the metal needs to be thick and strong. Basically, this makes it look like the MM design. In fact, replace the Heim's with the stock car bushing assemblies (I don't know what they are called, but have a "bolt" welded to a tube" and it would basically be the same thing. I hadn't considered modifying my rear LCA's before this thread. Now maybe I will consider it. Since this is a street car, anyone think I need the adjustment at the wheels, or would the center adjuster (like Blueoval's) work fine? I have no appreciation how much the toe can be off stock. Joshua -
rear poly bushings on outboard end of CA
Jolane replied to blueovalz's topic in Brakes, Wheels, Suspension and Chassis
-
rear poly bushings on outboard end of CA
Jolane replied to blueovalz's topic in Brakes, Wheels, Suspension and Chassis
-
rear poly bushings on outboard end of CA
Jolane replied to blueovalz's topic in Brakes, Wheels, Suspension and Chassis
Cary, Yeah, I guess that would do a good job at strengthening the arm. I would recommend capping the ends of the tube as well. By toe adjuster, do mean inboard behind the diff instead of adjusting everything in the LCA's (I think it is BlueOvalZ who has a nice setup like this)? This method does shift the wheel in the wheel housing though due to the moment of the LCA. If this is not what you mean, I guess I don't see how you could make the adjustment. I guess in the end, how often will this be adjusted anyways once set-up? I assume it is set it and forget it, but I don't race cars... Joshua -
rear poly bushings on outboard end of CA
Jolane replied to blueovalz's topic in Brakes, Wheels, Suspension and Chassis
Cary, I think I understand what you are saying, but what would a tube buy you over just a flat plate on the end? It might even be possible to modify a stock arm to look like the Modern-Motorsports arms at the ends. Seems like you could put a 3/8" or so plate on the end and double nut the heim. I have not seen a MM arm in person, so I have no idea what thickness they are. I also don't know if this would be a good method or not, but something else to consider. Personally I like the threaded tube ends, although adjustment does require taking things apart first... Joshua -
Are the waves the kind that pop when you push from the other side (oil canning)? I have this on my rear hatch. If I put a shim between the skin and the internal support in the middle of the lower panel, it disappears and looks great. Maybe this would work for you. As for the doors, I have no idea. I went and found better doors for mine to avoid having to do the body work required (I don't feel comfortable just filling lows with bondo and moving on, especially if it is oil canned). This is also the problem with my hood...I will probably get a composite one to replace it. I wish I could be more help...and look forward to more experienced replies... Joshua
-
rear poly bushings on outboard end of CA
Jolane replied to blueovalz's topic in Brakes, Wheels, Suspension and Chassis
I cut my front LCA of the same as you have done on the rear. I then stuck the threaded tube end into the square section, and formed (with a hammer) the square tubing over the tube end and welded it all up. I had to cut a Vee to go from square to round in the LCA, but no big deal. This acts like a plug weld on the side of the tube end as well. ou could do something similar for your tube ends. Bending the steel is easy, especially with a torch (I did not have one at the time). Another option isweld the tube end into a short stub round tube, and use a hole saw or die grinder to cut a hole into the LCA to mount it and weld it tight. I would still lean towards forming the metal over the tube, instaed of just capping off the ends of square sections. If you want to cap the ends, at least wrap the caps over the top and bottom of the LCA, and be judicous in where and how you weld it. I used TIG to weld mine up, ensuring good penetration and control...MIG would work fine if you are comfortable with your setup and know how good your weld is after welding (I am afraid there are a lot of people who think their MIG welds are great, when in reality they are weak and cold). Joshua -
Those bumpers don't look too bad either. The back looks slightly bent on the top, but front looks nice...
-
Damaged rear end - want to shave it clean - where to start?
Jolane replied to Hugh's topic in Body Kits & Paint
-
Please Critique My Welds(4th day Welding)
Jolane replied to JustinOlson's topic in Fabrication / Welding
Not to completely disagree with SHO-Z, but I think walking the cup is very common in the pipe field, but not usually recommended for general TIG welding. I only say this because I have read about both methods, and heard the debate back and forth about which is better and why. My impression was that walking the cup was really a trick used when pipes line up perfectly, and it can really help for out of position welds in this situation. It should also result in a very consistent weld. For corner joints and the such though, I have not seen it recommended. I agree with everyone else, your welds are looking pretty good for the amount of time you have been welding. The only major problem I see is undercut. As someone else mentioned, undercut is bad. This can be caused by not enough filler, too hot, too slow, washing the toes with the torch, etc. I would recommend cutting across the weld and look at the penetration. Keep practicing and you will be making great welds in no time! Joshua