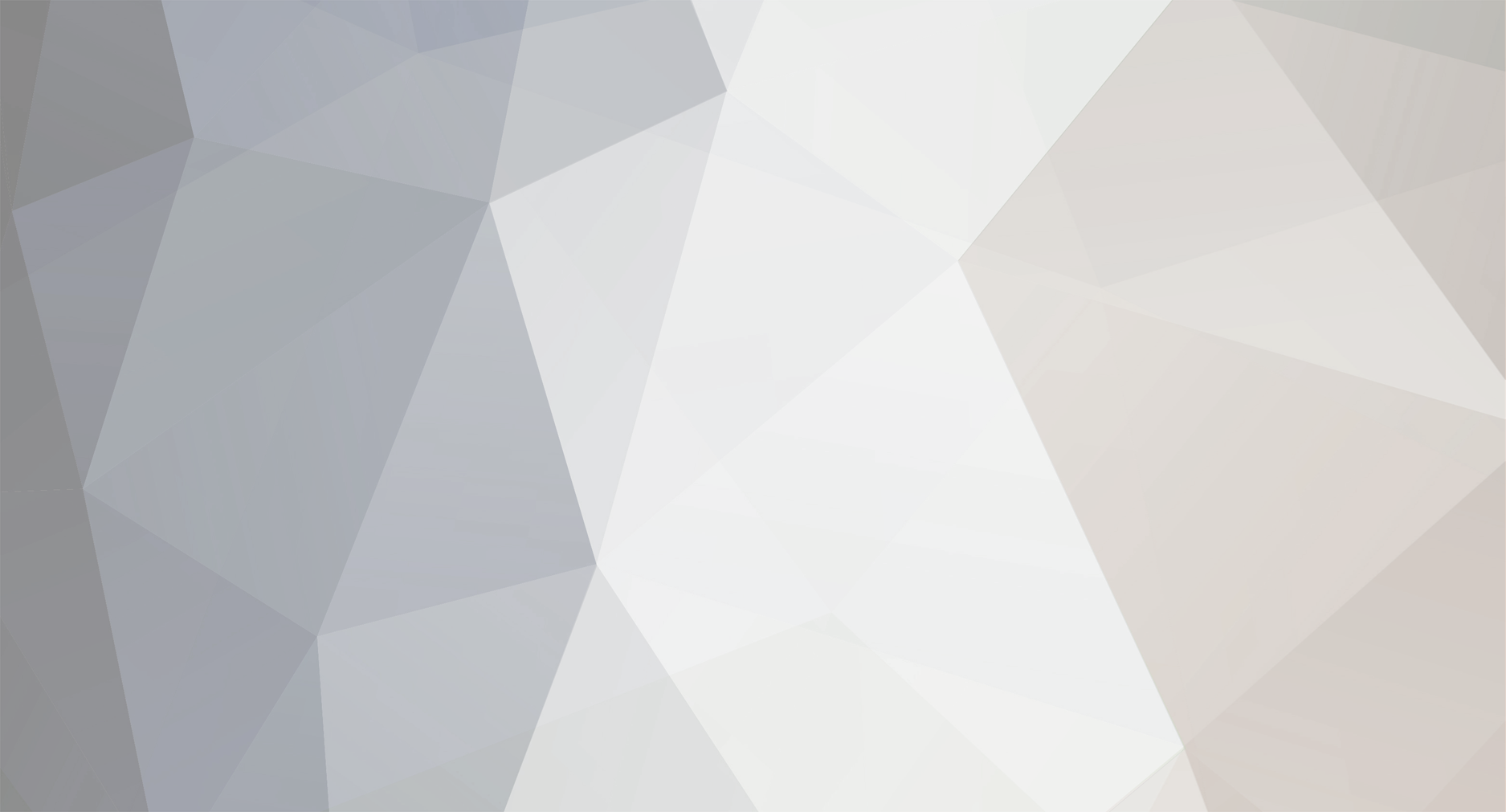
Jolane
Members-
Posts
351 -
Joined
-
Last visited
Content Type
Profiles
Forums
Blogs
Events
Gallery
Downloads
Store
Everything posted by Jolane
-
Looking for a certain style of engine mount...
Jolane replied to Jolane's topic in Gen I & II Chevy V8 Tech Board
Wow, thanks guys! I appreciate the pictures as well! I did not realize som many cars use mounts like this. I was told today by a co-worker that his BMW has similar mounts as well. That Corvette mounts might work the best. All I want is a plain mount. I was actually thinking about using a T/C rod bushings. It would be bolt through (safety), cheap, and easy to implement as well. Decisions, decisions... Thanks Again! Joshua -
Guys, I think I have seen this style of engine mount before, but don't know what it is out of. It was round, and had a stud sticking out of the top. The cylinder was basically all rubber, and it was mounted vertical. The bottom was mounted to the frame (or crossmember), and the engine mount attached to the top. I thought it was for a Toyota, maybe a Supra, but honestly can't remember. Maybe I am making the whole thing up, or maybe it was custom. I know that the circle track guys (like IMCA division), use aluminum versions of what I am referring to. Of course this makes the engine solid mounted, not what I am after. Can someone place this part? Thanks for your help, Joshua
-
Jackhammer, I will try posting pictures sometime. I don't even know how to quote someone though right now. I just can't figure out where to insert the negative so it will display on the screen (j/k). Anyway, I really do like your approach. If I had a brake, I would have done something very similar. It is tough though working in a small garage with, essentially, hand tools. I can't even get the engine out of the engine bay because the chassis is stripped of suspension, so it can't roll, and the engine hoist cannot move foward but 6" (step in garage). Anyways, I think in the end we both end up with something very similar. I considered running mine all the way forward, but I started with pretty good frame rails (just a little bent on the right side). I figure that if I reinforce everything to the strut towers minimum, it should be nice and strong. The front end is just to hold the headlights, etc (exaggerating a bit, but basically it is just added weight for me). I actually worked on the car today, and got my custom crossmember welded into the car (finally, after about 6 months of having it built). That came out nice, now onto the engine mounts (for the third try). Joshua
-
Thanks for the info Cary. Used in tension, now that is starting to sound nice and strong. You have that right about the twisting seen by a bushing. That is the downside. I am not really sure how much twisting a standard bushing can take, and maybe that is a bigger problem. What if is can't take a lot, then the TC rod gets twisted, which can be bad. I will most likely just use beefed up TC rod for my project with a poly compressed bushing and a stock rubber tension bushing. Eventually I want to build another 240 (my '70), and at that point I think I might do a true A-arm on it. The plan for that car includes cutting the front end off at the firewall also, and building a full tube frame front end. I think this would make it easier to use an A-arm front end. Even with my beefed up frame rails, I am not sure I would trust an A-arm for my current project. Wouldn't an A-arm be the best here. It could be easily tilted for better anti-dive, allow wider tires and/or sharper turning radius, robust, etc? Seems like this would be ideal, nd could potientally save space as well. Just need some stout frame rails. Maybe just go Mustang II front end, no more strut towers, even more space. Thanks for the discussion, Joshua
-
Stiffen and strengthen! HOW?
Jolane replied to cremmenga's topic in Brakes, Wheels, Suspension and Chassis
Before someone else tells you in a meaner way... Please use the search function olong the top. Search from sub frame connectors, frame reinforcement, etc. Good Luck, Joshua -
Cary, I do realize that the loads are largely compression given that the car is rear wheel drive, and braking and accel loads are all compressive on the TC. Backing up is the only major loading conditions I can think of, and how much can that really be considering the speeds. I would assume that cornering also exhibits loads on the T/C rod, but can't quantify that reasonably. Most of the cornering load goes into the LCA. The loading of a rack end seems to come primarily from tire scrub or bumps. I have seens cars hit curbs and totally mangle the A-arms, spindles, etc, but the rack end still holds together. I wish there was a clean way to rubber mount the T/C rod. I realize that this defeats the purpose of using the rod end (stability, lack of excess deflection, etc). I have also been thinking along the lines of using a standard poly bushing in a configuration similar to a track bar (panhard rod). The back of may cars have these as well to control the fore/aft wheel motion, like a drag link. This would require modifying the T/C cup, but I would think the gain is worth it. It could create more room for headers, starter, etc while limiting transmitted vibration. It wouldn't be too hard to implement either if your already working on that area anyways (which I am). I just really want a street method that doesn't have me breaking T/C rods later. Something robust, more accurate handling, vibration "free", etc. Joshua
-
Jackhammer, That is almost exactly what I did, except I did not use Baddog subframe connectors. I plated my front frame rails with individual flat pieces since I did not want to get them bent, plus it is easier to fit them. I have been working with the engine hanging betweent he frame rails (from a cherry picker)! I think the end result is very similar. I also "spot welded" my parts in place using plug welds. The corners are fully welded and ground and appear to be on bent piece. I used 14 gauge HR for this. Finally, I only ran my pieces past the sway bar mounts, and not up to the rad mount due to the shape of the rails and how they taper. I personally think the weight is worth it, especially considering how rusted the rail can be inside (unknown), and how I am mounting the engine. Thanks for the pictures! Your work looks good! Joshua
-
Tube80z, Do you have information on the strength of a rack end? I cannot image a rating for these things since it seems like most of the loading is rather low compared to a TC rod. I was thinking along he lines of using a GM draglink from the front axles of a truck. This would require some changes to the TC mount. I could imagine bolting the rod end through the frame rails (this is hard to explain, so I will stop there). In the end, my car is for the street, so I just want a robust TC rod and minimal road vibration. I am thinking of a custom TC rod but then use the poly front and stock rubber rear bushings in the stock cups. By making a TC rod I would like to increase the diameter of the stud going through the bushings (modify the bushings ID). Joshua
-
I am also very interested in this. First hand experience would also be greatly appreciated. Joshua
-
Maybe I am weak, but that block is rather heavy. I would get someone to help you, maybe two if possible. I put my block on my engine stand by myself, and it was a royal pain (did I mention heavy) trying to get the pipes lines up and inserted. Please be careful if you do it yourself! Joshua
-
DJ Paul, I looks like you cut out the frame rail section, and are replacing it. My frame rails were solid, so I simply plated them with 14 gauge sheet hot rolled. The existing rails are still under the new plating. The reason for the plating is to displace the loads from the engine mounts and crossmember. The stock sheetmetal is so thin, I did not trust it, especially after welding it. I think the absolute best thing to do, for me anyways, would be to cut the front of the car off and fabricate a complete tube chassis up front, but that will be for another car one day. Joshua
-
I have not seen those Baddog pieces before. That was basically what I did to my 240Z last winter using 1x3 steel tubing. I cut a section out so it could go over the existing frame rail (which was actually a brand new piece I put on after replacing the floorpans). I then put a piece at each end to tie it into the frame rails front and rear. The front also was a channel that capped the existing framerail. I just finished plating the front frame rails this weekend with 14 gauge, bottom, sides, and top. I will be welding in a custom crossmember within a few weeks, then welding the ending mounts to the framerails. This is a lot of work, and wish I could have used an OTS part. Nice looking parts Baddog! Joshua
-
Oh, I see. I spoke with Bubba as well way before ordering my TKO-600. He was okay on the phone, but did not instill confidence. Eventually I may look into getting a G-force T5, but for the weight difference, maybe not. I know what you are saying about the blowproof bell housings. They are HEAVY! I would rather loose that weight, but also want to keep my feet if an accident did occur. I guess this is the downside of high HP AND safety. Joshua
-
I also have one, it is in the car, but the car is on stands stripped to the metal. Can't say I will drive it before 2007 at this point. It fits nicely though, and the shifter comes out in a decent location. Joshua Mike, I thought you were going with the G-Force T5. What happened? I tried to follow that thread, but maybe I missed something along the way. Last I heard, there was another vendor for the gearsets.
-
That machine has gotten great reviews, and is supposed to be an awesome machine. The price is great also for what it is! I have a Dynasty 200DX (Miller's inverter AC/DC tig) and it is very nice also, just ~$1000 more for an equivalent setup. That TA is definitely worth the money though. As for torches, you can put basically any commercial torch on it, air or water cooled. The standard that comes with it is a 17-series aircooled I believe. No problem finding parts for it. Joshua
-
Any idea on whether it can be thinned with Lacquer, MEK, or other? I have some that is just a little too thick, but would like to use it. I tried some on a clean piece of steel, and was not all that impressed with the finish or the durability. Maybe I should have let it rust a little. Maybe the stuff is just a little too thick. Joshua
-
why IM NOT a big fan of two post lift designs
Jolane replied to grumpyvette's topic in Trouble Shooting / General Engine
I have used 2 post lifts with both smaller cars (280ZX) and larger trucks (1500 Ram, Nissan King Cab D21, 3/4 Ton Chevy and Ford, etc). I have felt safe using all of the lifts with all of these vehicles, but it does require triple checking the pad placements before lifting high. My brother got to see a co-worker drop a Jeep Wrangler from ~3 feet in the air. I guess it bounced real nice! When I build a shop, I would like a 2 post lift and a frame table. I would build the frame table so it could also act as a 4 post lift. The 2 post though will be my main lift. Joshua -
Did anyone watch the other video right below the S2000? It is a Suzuki Samari like thing hauling butt on two wheels. Now that was impressive! Joshua
-
My GF's 2001 Honda Accord was parked in our driveway (not very steep, but inclined none the less) in 1st gear without the parking brake set. On a cold winter night it seemed to have rolled back into the street. The engine is fine, it was in First Gear. I guess the engine compression bled down due to the changing air temperature in the cylinders. That was a little scary, luckily didn't hit my car! I do not plan on using any brake kit that does not have a manual parking brake on my build. Joshua
-
Another TT383 Chevy Race Video
Jolane replied to Turbo Meister's topic in Gen I & II Chevy V8 Tech Board
Wow, nice run! I too enjoy seeing your videos. Thank you. BTW, your video quality is really nice! I could watch it at half screen (full is 21", 1600x1200) and it looked excellent! What camera are you using to create the video so smooth without pixelation? Joshua -
I also have Forza. I have never played GT, but I definitely like Forza. It seemed a little slow at first (not very arcade like), but I have gotten used to that and like the realism. Joshua
-
Are you getting any spares with the bike, that can be brought back by riding the bike? Personally, I would opt. for #2. To be honest, if you can't afford the extra $150, maybe a bike is not a good option in the first place. They are expensive, especially when considering maintenance, tires, gear, etc. It is a sure bet, and will make the trip more enjoyable. Joshua
-
I also own both, and have used the plate for my current 383 project into the 240Z. I had my tranny attached also, and did not find it difficult to use compared to the leveler. I personally don't like the leveler much due to its tendancy to twist the engine. I also did not want the chains going over the valve covers. The plate is simple, holds well (using ARP bolts into an AirGap intake), and keeps the engine level (horizontal). An aside, when I needed a way to get the car up my drive way (no drive train, but inclined driveway), I bought another plate and bolted it to the floor in my garage, and use it as an anchor for my come along. Works very well like that also. I am not saying that one is better than the other, merely that I like the plate more for my situation. Joshua
-
Just to comment on the Mig's that also act as TIG power supplies. I believe, and correct me if I am wrong, that they output DC TIG only, no AC, so no aluminum. I definitely would like to have a big MIG though with Pulse on Pulse, what awesome welds those put out! Joshua
-
Congrats! I personally have a Dynasty 200DX in my garage. I chose it for a few reasons: 1. It is portable, very portable! 2. I can stick weld on 110V if need be. 3. I only had a 50A 220V plug available. 4. I wanted to be able to use a plug (30A) that was not super expensive. 5. Reputation. I wanted a machine more capable than I. 6. It takes up little space, and uses little electricity when in use. I really like it, and feel I made the right decision. It was a little spendy, but for my application, I could not have lived with a larger traditional machine. I have used the pulser before, but an typically welding stuff that does not need it. The high frequency on the other hand is awesome! It makes a huge difference when I go from 60 HZ up to 150HZ (or whatever). It definitely helps shape the arc. I have never used a traditional machine (this is my first TIG), so I don't know how they really differ otherwise. BTW, the T/A 185 is about the same price, maybe a little cheaper, than the Syncro 180. It has gotten great reviews, and seems to be an excellent machine, incase you are considering an inverter. It does not run off 110V though, only 220V. The price includes the regulator, foot pedal, torch, etc... Joshua