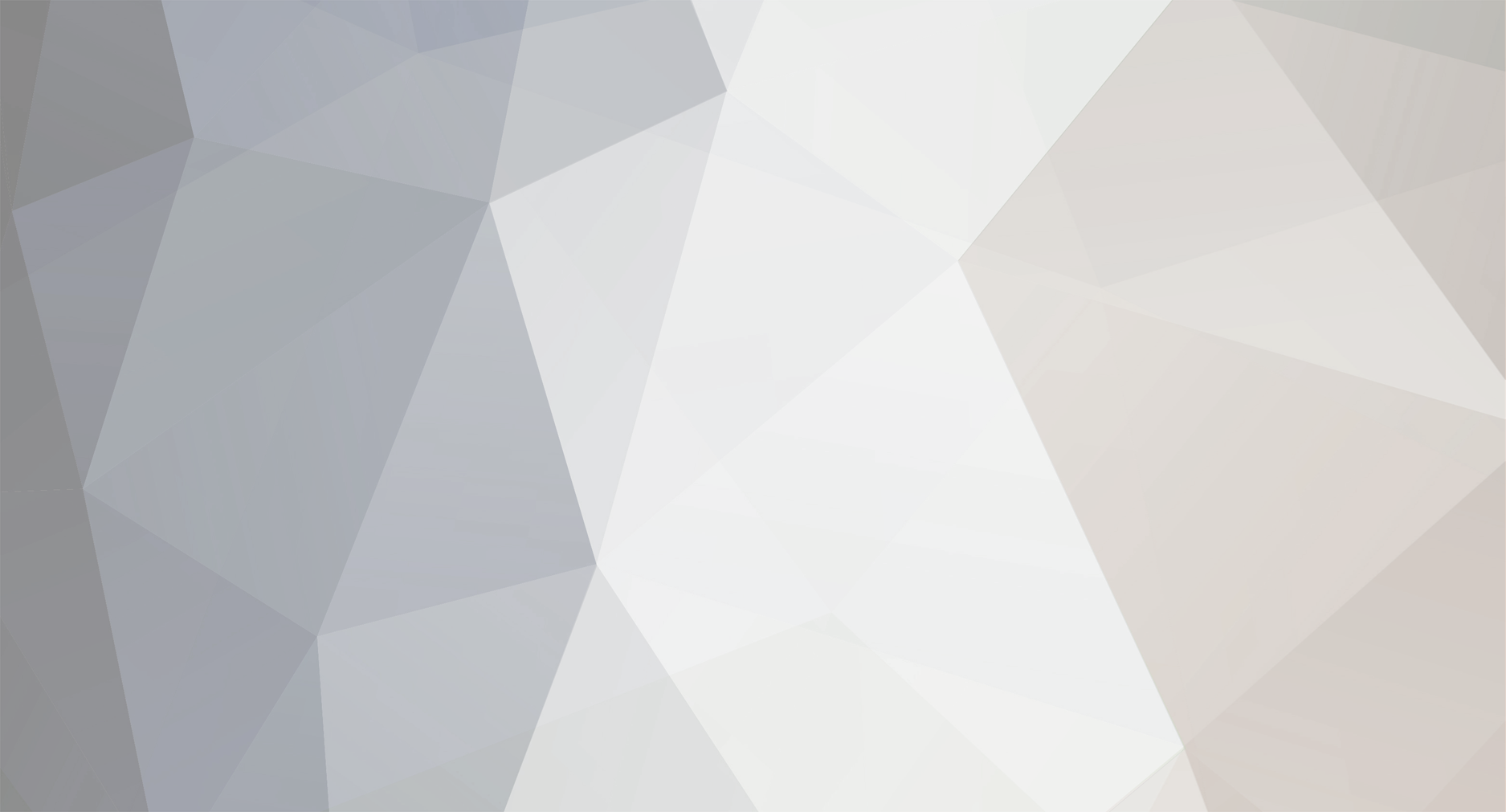
Mike C
Members-
Posts
2067 -
Joined
-
Last visited
Content Type
Profiles
Forums
Blogs
Events
Gallery
Downloads
Store
Everything posted by Mike C
-
For a little motor, the Dart SR torquer is probably the way to go. Or a set of Corvette L98 aluminum heads if you want an aluminum head.
-
Installed 3.7 diff.with torsen LSD ,tires spin easier?
Mike C replied to tomcraft's topic in Drivetrain
Increased torque from the 3.73 although not a lot. Were the rams horns 2" exit or 2 1/2"? If they were 2, you could see quite a bit more power from 2500 rpm up with the shorty headers. -
They are cable activated and mount to the floor with 3 bolts, so it should be pretty easy. But integrating it with the console could prove problematic. If you want a GM shifter, the 2nd gen F-body "slap stick" is a much more reliable gear changer.
-
Is this a complete 3.70 LSD center section or are you swapping into another housing at the same time you are rebuilding? Or changing gear sets for that matter? Trouble shooting an anomaly is always a hassle. My process for doing pinion bearings is to always measure the installed height of the pinion so you can check height on reassembly. Obviously without a depth checker you can't do that, or if you have already taken it apart, so next... Now that it has been reassembled and we find an issue this is where I would start: Step 1: Disassemble. The whole thing unfortunately. You need to make sure there is neither a burr or piece of trash caught between the pinion depth setting shim and bearing or any of the races in the housing. While it is apart cross check all bearing and race part #'s and visually compare the old and new bearings just in case. Step 2: Reassemble pinion gear, bearing, and depth shim. With the original pinion depth shim cleaned & deburred, re-assemble pinion bearing and shim onto the gear. Make sure bearing is pressed all the way down and is even all the way around. Step 3: Inspect and clean/deburr housing where the pinion bearing cups install. Re-install bearing cups. Make sure all cups are fully seated and square in their respective bores. Step 4: Finish reassembly of pinion with all existing parts and see how tight the assembly is. From the centerline of the pinion, a 10" long bar with a 1 lb weight on it should NOT rotate the pinion, but on a 13" bar will. You should be able to rig something up, just snug up on it until you get there, that will be just over 10 inch pounds. Beam type inch pound wrench is available for about $30. It's kind of surprising how much 10 inch pounds is. Step 5: Now that you have preload set, you can check for play using your dial indicator by pushing and pulling on the pinion and checking total movement. This will give you a starting point for adjusting shims if needed. Step 6:And this is a little out of the normal order as before I finish shimming and adjusting the pinion I would- Step 7: Put the carrier back in and check for backlash. Once again, backlash is something I measure before I take it apart so I can compare on reassembly. If you skipped that, then we are measuring to see how close it is to spec. If it specs, now time to run a gear pattern. If the pattern looks good (and check it with the pinion loaded somehow to really squeeze out the marking compound) pull the carrier and finish adjusting the pinion bearing preload through trial and error shimming. Step 8: If pattern is whacked, then you have to look at some pictures and figure out what spec has changed. If it is pinion depth, somehow you need to verify what the correct depth would be. I don't remember how/if Nissan marks the pinion head to show depth or if it is assembled without any markings ala GM. This will require getting a pinion depth checker if you have depth info. Summit and Jegs both have house brands for about $100. Step 9 and Beyond: Once we know the pinion depth is right, we can move side shims to adjust backlash. This can all be quite the pain with assembling and disassembling the whole thing, but at least the carrier shims are not BEHIND the bearings like on Dana axles. Good luck and I hope this makes sense. I have read it and read it looking for inconsistencies in my descriptions, but they might be there!
-
I have a 12mm R200 from an '85 Turbo car in my 240. Swapped in using '78 R200 stub shafts, so the short answer is yes.
-
My driveshaft came from Wenco. Don't remember exactly what I paid, $250? But it came with the 1310 chevy joint and Neapco adapter on the back and the NISSAN T5 yoke on the front. But the first one was wrong, and they acknowledged they screwed up and had a UPS call tag out to me and a replacement on the way ASAP. I will do business with them again as price is one thing, but how they respond when a mistake is made is something else.
-
I tried this when I swapped a ZX 5 speed into my 240. It did NOT work with the transmissions I had. The distance from the pivot to the ball the plastic piece fits on that goes in the tranny was different. The 4 speed shifter would not engage all the gears. First thing I did was heat and bend a 5 speed shifter to the shape of the 4 speed shifter. But the ball barely came out of the console! Talk about short throw... I wound up cutting the 5 speed pivot off and TIG welding it to the 4 speed handle. Now I have a T5 with a Hurst shifter. :thumbs up:
-
Not sure exactly which parts are interchangeable, but the Nissan T5, Ford T5, and Camaro T5 all have the shifter mounted much further to the rear. Shouldn't be too hard to find a grenaded non-WC Ford trans for experimentation. Mustang and Nissan use same shifter setup.
-
Yes. But I would just get a complete diff from a ZX and install the Quaife. That way you don't have to mess with the pinion depth variable when changing housings.
-
Yup, like Jon said, all you need to change are the side shafts and the input flange, unless you have a limited slip from the donor, then you need to ditch the finned cover. I put an '85 in my 240 for the 12mm ring gear bolts.
-
Great buy. Goes to show that you can score a deal if you can wait. Throw some pics up.
-
How far does the slave cyl move on a t5 transmisson?
Mike C replied to FiveSeventyZee's topic in Drivetrain
Did this just start or has it always been that way? If it just started you probably have a leak. If you just got it running for the first time, it could be all sorts of things. -
You think I could TIG with this power source???
Mike C replied to BURLEIGH's topic in Fabrication / Welding
Stop. Don't buy any equipment. Start by reading this and buy the Miller Student Guide package. http://www.millerwelds.com/products/helpmechoose/selection-guide.html http://www.millerwelds.com/resources/tools/basket.php?action=A&id=211630&qty=1 Best $25 you could ever spend with explanations of process, instructions, weld calculators, and catalogs. -
Interesting, and not a clue. But my experience with shifters for the OEM 4 speed, the early and late 5 speeds was that there were different lengths and bends to not only the shifter handle part, but the length of the pivot is also different and there were several variations so you need the exact handle or it won't shift into some of the gears. I wound up using the 5 speed shifter cut off right above the pivot and welding my 4 speed handle to it and what I would recommend that you do. My first attempt at 5 speed shifters was to heat and bend a ZX shifter, but it made the handle so short that the ball was just barely above the console!
-
You think I could TIG with this power source???
Mike C replied to BURLEIGH's topic in Fabrication / Welding
That's for you to decide IMO. You can get a used Syncrowave 200 for $1200-$1500 reasonably easy if you can wait awhile. You can get a new Hobart Tigmate for $1500 or as you mentioned, any number of others. I'd start out by saving $ and if I came across what appeared to be a real deal on an older Miller/Lincoln/Hobart/ESAB/Airco/Heliarc I'd buy it and practice with that. You can sell it for what you paid for it usually when you are ready to upgrade. -
You think I could TIG with this power source???
Mike C replied to BURLEIGH's topic in Fabrication / Welding
You might be able to find a Thermal Arc Dragster. I Googled real quick and didn't find any for less than $650? It is an 80 amp inverter type DC stick box with scratch start TIG optional. I bought a closeout from Sears a couple of years ago for $269 complete with the TIG package except the gas bottle. They used to be on eBay for $450 all the time brand new. Here is what looks like the replacement, less than $300 but you will need to add a TIG torch, flowmeter, and gas bottle: http://www.brweldingsupplies.com/shop/products/thermal-arc-95s-95-amp-dc-stick-tig-welder-w1003202.cfm EDIT: Here it is on eBay, $410 with free shipping. http://cgi.ebay.com/THERMAL-ARC-95-S-TIG-STICK-WELDER-PKG-W1003203_W0QQitemZ230398803026QQcmdZViewItemQQptZBI_Welders?hash=item35a4d6bc52 -
You think I could TIG with this power source???
Mike C replied to BURLEIGH's topic in Fabrication / Welding
The Spoolmate 200 is a constant voltage machine to run the spool gun, ie a MIG welder. You need a constant current machine to TIG. -
How does everyone get air cleaners under the hood?
Mike C replied to FiveSeventyZee's topic in Gen I & II Chevy V8 Tech Board
The lowest profile air cleaner base I have seen is the Chevrolet factory base. Get them from the aftermarker for about $50, $80 for bottom and top with a paper element. Eventually the triangle type foam filter winds up melting down the carb from a backfire... -
TO bearing itself is the same, but at least three different collars that slip into the bearing, and possibly three different clutch forks as well. You have to match the collar to the clutch and fork you are using.
-
As I and many others have found the hardway, there are different clutch/throwout collar combos. At least three different collar heights found int 240, 280, and 280zx turbo depending on the clutch. There are at least 2 if not three different throwout forks. You need to use the parts for the clutch you have, and not the trans. If you changed the clutch, use the 5 speed parts, if you kept your early clutch, use the 4 speed parts.
-
Not sure on a Z32, but the earlier cars have several different height bearing collars. Also a couple of different throwout arms. I have issues with my T5 swap still and need to pull it again, but my short term fix was a smaller bore slave from a 240sx. 5/8 I think? While most replacements are 3/4? This gives me just enough disengagement to make it driveable until I pull the trans again. I sucked it up and bought a 280ZX turbo collar and throwout arm to make sure it doesn't have to come out again. At least for that...
-
You can modify the stock distributor to get more mechanical advance. This will allow you to keep a much more reasonable initial advance to aid starting. I'm lazy, so I bought a Mallory L6 dual point without vacuum advance which is extremely adjustable. I bought the Unilite conversion for it as well, but have not put it in yet, as the dual points run pretty good, at least relative to carb jetting... Buying the dual point and then adding the unilite conversion was WAY cheaper than just buying the Unilite distributor. I think I paid $190 from Summit for the distributor and then $80 for the Unilite. Some due diligence on the 'net will show you how to modify the weight mechanism for more mechanical advance and how to lighten either the weights or spring tension to change the rate at which the advance comes in. A file and/or some brazing along with some general knowledge will do it. A dial-back timing light helps a ton in determing what the total advance # is and how fast it comes in.
-
I had a bad brake booster in my car. The vacuum leak gave a similar "throttle on braking" response. You may want to check your booster and line. SOme have an inline check valve that might help.
-
I'd like to see pics as well. But whatever you do, don't mix and match pinion gears with ring gears. That will result in a bunch of wasted gears in no time.
-
I re-used mine.