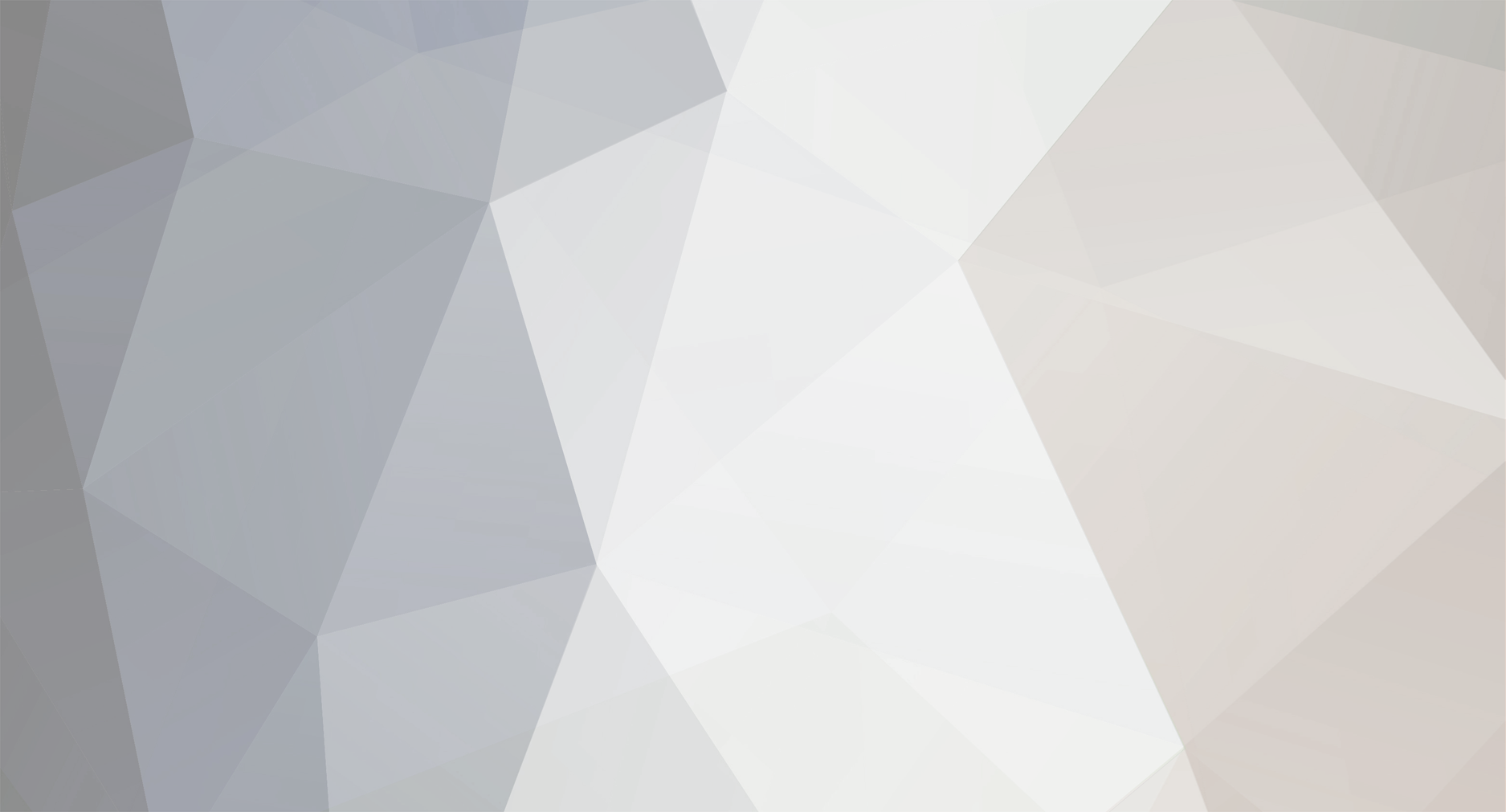
Mike C
Members-
Posts
2067 -
Joined
-
Last visited
Content Type
Profiles
Forums
Blogs
Events
Gallery
Downloads
Store
Everything posted by Mike C
-
That does not work. The gears are ground to a specific helical size and run in on a machine to make a matched set. You might be able to swap pinion gears that are the same ratio but most likely the whine would be unbearable, but you can't change just one gear to change gear ratio.
-
I know I had at least 1 R200 with a square flange. I think it was an '85 12mm from a turbo car. I swapped a '78 flange from the 10mm I had in the car when I put the precison gear LSD in. Both of those are Long nose however, so not sure if that helps you or not.
-
I had issues with my Centerforce II pressure plate releasing and learned that it may nbe just small differences, but the throwout arm and collar had different part #'s than either of the other clutch setups for S30 cars. The early 5/8" slave is no longer made, just the 3/4" and I was not getting enough throw from my clutch. I found a 240SX 5/8" slave that gave me enough length to disengage the clutch. The T5 trans from the turbo cars has a removeable bellhousing unlike the Nissan trans so make sure you've got that. I had a custom driveshaft made with a Nissan yoke on the trans end and the 1310 Chevrolet joint with Neapco adapter for the R200 in the back of my car. I used the Hurst Competition Plus shifter for '83-'91 Mustang GT. I think the T5 is the best swap trans because it has the deepest first gear and the highest overdrive. My car a highway monster with 3.54 gears.
-
Yes. At least on my car (Stock diameter Suspension Techniques springs) and a zero offset 16x7 wheel there isn't hardly any clearance to the spring. With coilovers you might not need the spacer, but with stock diameter springs I think you will. And if you've lowered it, those 8.5" rims are going to probably cause some woes...
-
Rebuilding Driveshaft for T5 with R200 in a Series 1 240Z
Mike C replied to SuperSamuri's topic in Drivetrain
The factory driveshaft has the u-joints swaged into place. If it could be disassembled (and with a big enough press, you could) it still wouldn't have grooves cut for the retainer clips. In my own experience, drivelines don't make any noise. Vibration maybe, but not noise. Because of the IRS arrangement, u-joint wear isn't much of a deal with a Z. At least not with any of the 3 cars I have owned and the 100,000 plus miles I have driven a 240 so most likely the sound is from either transmission bearings or the R200 as mentioned. I had my driveshaft made by a company in Californio, Wenco. The guy I dealt with was very knowledgeable. I did the Nissan u-joint in the front, but a 1310 in the rear and the Neapco adapter to bolt to my R200. As I mentioned in another thread, he suggested a Chrysler Torqueflite trans yoke with the OD reduced to the Nissan seal diameter and you could run 1310 joints in both ends. With several thousand miles on my T5 swap I still consider it to be the best of all world's for the Z as far as transmissions go. The same deep first gear as the early 4 speeds and the more overdrive than even the late ZX 5 speed. -
I had my driveshaft custom made by a company in California called Wenco. The rear was the done with the NEAPCO adapter to use the Chevy 1310 size joint but I went with a new Nissan T5 front. He said he could reduce the OD of a Chrysler Torqueflite input shaft which had the right spline count but the wrong seal diameter and I could run 1310 joints in both ends. Knowing that, you could bore the tailshaft out to take a bushing the size of the Torqueflite input shaft, or you could have the TF shaft reduced in diameter to match the "worn" bushing in the Nissan housing. Seems you could also cut the bushing out (slowly and carefully!) and then press the new one in DIY.
-
It is a limited slip of some sort with the 2 piece case based on the seam on the ring gear flange. It looksl like it has helical gears like a Torsen to me. I've never seen a ring gear that didn't have anything stamped on it, so rotate it around and look for markings where that yellow paint mark is now. Otherwise, with the the cover off, count the teeth on the pinion gear and count the teeth on the ring gear. Divide the pinion into the ring and that's your gear ratio.
-
LT1 T56 on an early block Flywheel question
Mike C replied to rayaapp2's topic in Gen I & II Chevy V8 Tech Board
Counter weight issue. Two piece cranks have a counterweight on the flywheel flange. The one piece crank is perfectly round and the flywheel is not zero balanced. -
I have a T5 in my car as well as an '85 12mm R200 in my car and I swapped on the flange from a '78 R200. I then used the Neapco adaptor the V8 guys used and had a new driveshaft made with the Nissan front yoke and the 1310 Chevrolet sized rear joint. The guy I spoke with said a Torqueflite had the same spline count/diameter but outside diameter too big. They could turn it down to Nissan seal size so you could run 1310 joints in both ends. If my car made more than 200 hp that's the route I would have taken. Wenco in California made my shaft FWIW.
-
Difference in trans length is a great idea, but I would put it all together then measure for the driveshaft before getting it modified.
-
240Z chassis + 280ZX 5 spd Trans + STI R180 Diff = What Driveshaft?
Mike C replied to GreenState's topic in Drivetrain
I swapped a ZX 5 speed into my 240 with the R180 and used the stock driveshaft. I'm not familiar with the Subi R180, but it's a long nose as well, correct? Seems like a chance it will work. I had a shaft made for my Nissan T5 and 12mm R200 swap. It has a new Nissan yoke on the front and I used a 1310 rear joint on the NEAPCO adapter. It was about $250 as well. Came from WENCO. -
You should be able to get a differential shim set for similar size bearings from something common and have it work fine. Most likely a Dana 30 or Dana 35 but possibly a Dana 44. You just need to know the OD of the bearing race for the carrier bearing, and the OD of the pinion shaft bearing and ID of the pinion shaft and you could cross reference. Once the diff is apart, it would be easy to find at a drivetrain shop or even calling somebody like Randy's Ring & Pinion to order. The Dana info is all over the web. A very early 12 bolt diff shim set ('65 passenger car) might be ideal for carrier shims, but I haven't had an R200 apart in a long time to remember exactly. When I did my Precision Gear LSD, I didn't disturb the pinion depth. I checked backlash before and after using the stock shims and it didn't move so I didn't need any additional shims. I have a ton left over from doing 4x4 gear installs, but didn't write down or compare at that time what would be best for the R200.
-
Cool. I have one of those I use for jeep tires. It's a bitch to get the tube in a 6.00 16" tire, but having it bolted to the floor really lets you get some leverage on it! Big radials fall on the wheel like you mentioned.
-
Ideas for bench repair fixture for r180 or r200 diff
Mike C replied to RebekahsZ's topic in Drivetrain
Not at all. The 3/16" 3" angle was bolted to the diff mount bolt holes. The 2" square tube was welded perpendicular to the angle and stuck out about 10". I then used long bolts and steel plate to clamp the tube down to my grate top welding table. Didn't want to go anywhere and hung off side of table with pinion pointed down and top of ring gear about chest height. -
Ideas for bench repair fixture for r180 or r200 diff
Mike C replied to RebekahsZ's topic in Drivetrain
I made one out of 3" 3/16 angle and 2" 14 ga square tube. Clamped the tube to my workbench and bolted the diff with the pinion nut down. This let you work on the guts and made it easy to take back off the bench. Had a pic on here years ago when my LSD install post was new. No idea where that was hosted or what happened to those pics anymore! -
I know we have been discussing this on PM, but figured I would post some here. The universal pinion depth gauges will work universally. (Ha Ha!) but they lack any documentation on what specs/dimensions would be for an R200. You might have to use different pointers or extensions on the dial indicator to get where you need to go. The universal gauge uses the measurement from the cap mating surface to the bottom of the bearing bore minus the radius of the bearing race to establish where the centerline of the axle is in relation to the cap mating surface. Once you know that, you can measure from the mating surface to the pinion head to figure what dimensions you are working with. But those companies don't want to support something out of the box for their $100 tool which I understand. But in the case of replacing just a carrier, their should be no need to adjust the pinion depth. This is also true when replacing the bearings as they are so precisely made that the pinion depth will be the same as originally set. In the case of your diff, do we know if it was quiet before you performed the swap? I had a 4.56 12 bolt in a Camaro that made a ton of noise and it turned out to be carrier bearings and not the gears. In that case the noise changed based on how much load was on the axle in a turn. In the end the pattern is the ultimate determinate of whether the gears are setup correctly, but this can be a slow and arduouse process to get there.
-
This is the most used reference that I know of for the T5 and here they discuss the basic history of the WC and non-WC, years and applications. http://www.5speeds.com/t5/index.html
-
I have a Nissan T5 in my '72 240z. I did NOT modify the hole. I have a Hurst Competition Plus Mustang T5 and I bought the shortest pullback shifter handle in the catalog. I then bent it about 10 degrees to the driver's side in my press. It is high compared to where the stock shifter was, but I like it. It's up and close to the wheel ala NASCAR.
-
Unless you have some torque limiting device on the impact, stay away. Even the, you can warp the carrier because of uneven torquing of the ring gear. Use the vise to retain the carrier, and use the torque wrench to EVENLY apply force around the ring gear. Do it in stages. Slip the gear on if it's not already and snug a bolt. Continue adding bolts and just snugging them. Then up the torque to 30# or so, then 60#, and then max.
-
My experience with the stock T5 shaft was same as above. Cannot be shortened because both ends are bottlenecked. I had WENCO http://www.wencodriveshafts.com/ build me a new one and was quite happy with their service. I have since bought another driveshaft from them. I used a new Nissan size slip yoke in the front and had the 1310 U-joint and NEAPCO flange put on the rear. He would have put a MOPAR slip yoke on the front after reducing the OD to fit the seal on the Nissan T5 I think for $100 bucks? Then you could have 1310 joints on both ends. But I'm not making enough power to justify it.
-
The current LS motors are Vortec, but the '96-98 truck motor was also a Vortec. The non-LS Vortec motor is just a one piece rear seal first gen small block. This is an important distinction... Search on the 'net for putting Muncie behind LS motor, tons of info out there.
-
Get the counter shaft bearing stabilizer ring and don't speed shift. Stay away from really big sticky tires and it should hold up.
-
I have the GMPP intake although I have not actually bolted it on the motor yet... But just knowing that the biggest issue the Vortec motors had was the intake gaskets failed, I wouldn't consider running one if it did bolt up. As usual, YMMV.
-
When I swapped mine in, I measured backlash before I pulled the open diff out, put the LSD in, measured backlash, and it was the same. I was going to try the early (65 only, maybe 66?) Chevrolet shims for the 12 bolt. This was before they switched to the cast shims. The steel shims were thinner but looks like they would work for the 200. Don't remember where I got them, though.
-
The L98 aluminum heads didn't get the revised intake pattern the iron bolts head did if I recall correctly. They weren't the greatest flowing head as mentioned, but they are more than adequate for the TPI with stock runners. Some bowl work on the heads along with a port matching of the intake and exhaust should work pretty well. If your TPI is from a 305, get 350 throttle body and injectors. I think the Comp 260 cam would be a fair choice. (210 @ .050). My buddies '74 'vette convertible has a TPI 305 in it he swapped in back in '88. It has a Summit flat tappet cam, headers, and an Edelbrock intake base. Still has the iron heads. With 3.07 gears and the TH700 in ran 13.97 in Houston. That's at 3600# plus driver...