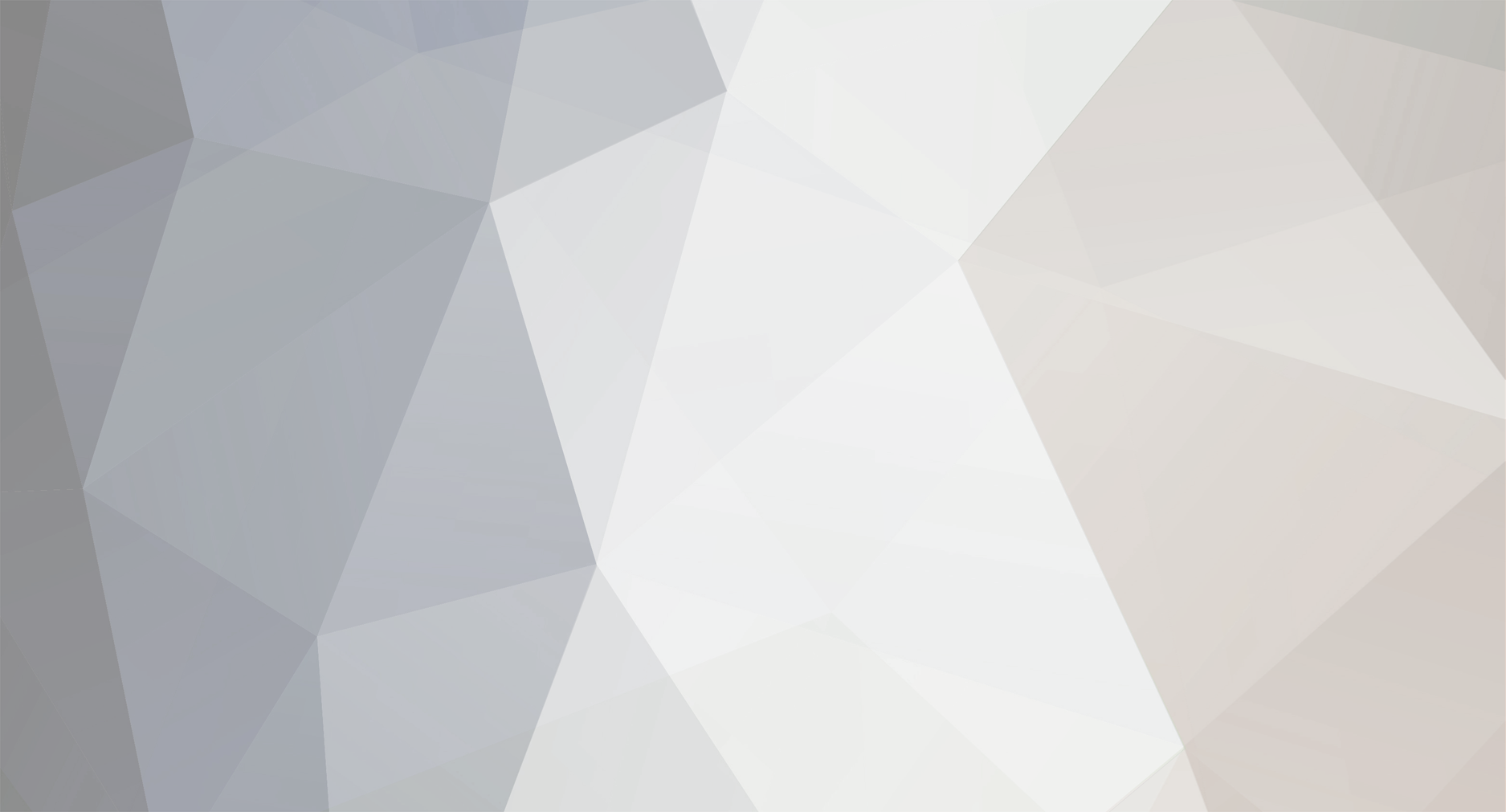
rsicard
Members-
Posts
889 -
Joined
-
Last visited
Content Type
Profiles
Forums
Blogs
Events
Gallery
Downloads
Store
Everything posted by rsicard
-
Alainburon: How does one locate Rockford CV's? Are they on the Internet or is there an address and phone number? Please advise. Thanks.
-
Its either lack of fuel or lack of ignition. Temporarily plumb in a fuel pressure gauge into the regulated pressure portion of the EFI system. If when it cuts out there may be a small temporary rise in fuel pressure if there is a commanded cut from the ECU. If there is a significant fuel pressure drop then fix same. The most suspect sensors in the EFI system would be the TPS or MAP. MAF, CLT, O2, IAT won't cause this symptom. The only other possibility is the ignition system or wiring for it or wiring for the EFI system.
-
Pull the spark plugs one at a time to see which ones are sooty from a rich fuel mixture. Check the regulated fuel pressure on the fuel rail to the injectors if most of the spark plugs are sooty. Pull and inspect the fuel injectors on the cylinders that show sooty spark plugs. Likely if the fuel pressure at the rail is OK, some or most of the injectors may be faulty. Check the TPS, MAP, Coolant Temp, MAF etc sensors for proper output to the ECU. Add a can of Seafoam to the gas tank at fill up to help clean the fuel injection system.
-
Fist check for grounds on the burnt wires. Bypass the ammeter by inserting a heavy gauge wire from the battery post on the starter and the armature post on the alternator with the negative battery post removed. Then momentarily touch the negative battery cable to the negative post of the battery to see how much of a spark it emits. If it does not spark too badly then hook up same to the battery and test other circuits.
-
What led you to the black connector on the passenger side?
-
Michael: You are very accurate in your assessment " Well, not outright crap, but the best cylinder head design in the world won't compensate for incorrect timing or a carburetor that pukes fuel." All of which you have said is true. After having rebuilt and driven a Chev Big Block with modified factory fuel injection, they like 40 degrees + advance for ignition timing. That in itself should tell the story of the inefficiency of that engine design. The fellow that designed by the small block back in mid 1950s had a design that was WELL AHEAD of its time. The only thing really improved is the cylinder head designs and advent of multi-port fuel injection which GM screwed up until the LT-1 came about with very precise ignition and fuel injection timing.
-
Michael has good advice. Just raising compression is just one aspect of trying to obtain better engine performance. Buy and study books by David Vizard and you may be ahead of the game. First concentrate on getting the body structure and systems in proper good order. Get it running and driving before working on the engine for more performance. Later year 350 engines were machined by CNC systems and should be more exact dimensions. Before building a performance 350 get a really good block as the foundation for making REAL power. No core shift and adequate cylinder wall thickness. Displacement for displacement the Gen I, Gen II, Gen III and Gen IV are all very similar in power for the same power enhancements. The Gen I has the most amount of cheap performance parts available.
-
Question about 280z 5 speed tranny
rsicard replied to nissanboy85's topic in S30 Series - 240z, 260z, 280z
Need to take the transmission out and get it to a COMPETENT manual transmission shot to have it repaired. The rubber boot should fill the opening in the hump and not be able to see the road. May not be the proper boot for the vehicle. Depends on if it was moded to add the 5 speed trans. -
Mike: Horsepower at best is 240 if the displacement is 350 cu in. With many parts missing it will be expensive to buy the parts to rebuild.
-
Christine: I am really trying to think of how to resolve this issue. I must trust what you are telling me is accurate and must be VERY DETAILED. The more detailed the better with MUCH CLARITY. Need to establish a baseline from which to proceed. Next, please disassemble one of the front or rear turn signal lights to get at the bulb socket. With the running lights OFF, check for +12 volts on all three of the bulb contacts. The sleeve and two terminals at the bottom of the socket. In the elder years of the Datsun, the hot side +12 volts was routed from the fuse panel to the bulb. Then the return or ground side was switched on and off. This was the electrical design theme at the time of the 1971 Datsun 240Z that I know for sure as I have one. Not so sure about the 1979 models. That is why I need you to test for same to see if the electrical design theme carried over to the later years. Not so serious as it the reverse of the American Automobile electrical system designs which switch the positive side. Just 6 of one and half-dozen of the other. If Datsun carried through the electrical design theme from older models, then the combo switch needs to assert a ground to the bulbs through the turn signal switch then back through the common turn signal flasher which is nothing more than a normally closed thermal switch that when has sufficient current through it heats up and opens up momentarily then cools down an closes the circuit once more to light the turn signal bulbs. I hope the forgoing has provided some info for you. Look forward to hear from you as to the constant voltage on the turn signal bulbs with the headlights and running lights TURNED OFF.
-
How was the following verified? "There's absolutely no power getting to any of the signals when the turn signals are engaged, but there is power when hazards are engaged." Was a voltmeter used at the bulb socket to verify that +12 volts was present? From the wiring diagram it appears that +12 volts for these lights comes from the fuse panel. It therefore appears that the turn signal switch supplies a ground/return to the other side of the bulb sockets. With all the other lights that are not working it would seem that a ground/return is missing for these. Supply a temporary GOOD ground to the chassis from the switches to see if some lights come on. This assumes the wiring from the bulb socket to the cabin switches are OK. Electrical continuity from the bulb socket to the cabin switches can be checked with a Multi-Meter and long wire to the bulb socket.
-
Any more progress on the situation?
-
The 280ZX wiring diagram shows maybe two different types of flashers for turn signal and emergency and therefore may not be swappable. Also the wiring for turn signal may also go through the emergency flasher enable switch. Therefore there are two suspect switches. The turn signal switch and emergency flasher switch. The wiring diagram is complex and not well represented. +12 volts can be checked for at the tail-lights turn signal etc. If +12 volts is not present then there is a bad fuse or wiring or connector.
-
OK, if the forward and aft turn signal lights it is likely the turn signal switch or the turn signal flasher. On the 240 and 260Z's there are two flashers, one for turn signals and one for emergency flashers. Not sure of the location of these two but they are likely identical. Find both and swap them if they are identical and see if the problem stays the same or goes to the emergency flasher system. If the latter is true, then replace the flasher for the emergency flasher system. If it remains with the turn signals then it is likely the turn signal switch or wiring. Try there and post the results.
-
Christine: To answer your questions: 1) yes 2) yes, bad turn signal switch, or bad fuse, bad wire, bad wire connection. First it would nice to know exactly which model and year the automobile is. Typically the 240 and 260 Z's by design had heavy current flowing through the headlight and turn signal light switches. In order to fix the design, heavy current relays need to be installed in the headlight circuit. Then the headlight switch can be allowed to control these relays with a MUCH smaller amount of current and preserve the integrity of the headlight switch. On the 240Z and maybe the 260Z, the left and right headlights receive +12 volts from individual fuses. This inherently is a good design. The headlight switch on the stalk on the steering column switches the low or ground side of the circuit. This is still OK except it switches HEAVY CURRENT which is NOT GOOD. First thing is to trouble shoot the problem to see if +12 volts is getting to the headlights. Once that is determined to be good, move on to the ground or return side of the circuit. Temporarily grounding the return side of one of the headlights and then the headlight lights up says the column stalk switch is defective. These can be either repaired if not extensively damaged or replaced. But after replacement of same install the additional relays through which the heavy current will flow rather than the stalk switch. If there are any further questions, please do not hesitate to ask.
-
Looked at the Megasquirt schematic. There is a LED hooked up to the Micro Processor that indicates pulses out for Injector drivers but this is WAY UPSTREAM from the injector drivers. If this LED is pulsing on and off then use the Oscope to trace pulse signals from the Micro Processor to the injector drivers. If all is well there, double check the wiring to the injectors.
-
Need to determine why there is no Pulse output on the injector lines. Put 15 ohm loads on each injector output and I think the other side of the resistor goes to +14 volts supply. Then check with Oscilloscope for pulse outputs on the injector lines from the ECU. Don't understand why using the low impedance injectors??? Adding resistors make NO SENSE at all with LOW IMPEDANCE injectors. That just lessens the current to the injectors. I am puzzled and have 38+ years in electronics and a background in EFI.
-
For the rear lighting, do a really good inspection of the rear wiring to determine its condition. Likely it may be reusable. My intention is to use as much as the original yet strengthening the weak spots. Those are the headlight, turn signal and running light switches. These switches will be the biggest obstacle to installing a new harness. I purchase a new expanded fuse panel and relays to handle the heavy current used by the headlights. The turn signal and running lights will be replaced with replacement LED bulbs. This will require replacing the two flashers with three terminal types that will work with LED bulbs. The LED bulbs will use MUCH LESS current such that the existing original wiring will be more than sufficient. Just need to eliminate the design deficiencies of the original with modern parts and practices. In other words, fix only what needs fixing.
-
When is come to rebuilt switches, you can do this yourself if you are CAREFUL. Mark the wires before disconnecting the stalk switches on the steering column such that there is no doubt when putting same back together. Then find a good workspace and CAREFULLY open one switch at a time and clean same. When cleaned smear silicon grease onto the switch portion and close back up. Do this to the other switches. The headlight relay kit is available from www.motorsportauto.com/products.html. May not need to replace heavy-current wires behind the dash so long as they are not damaged. Strong suggestion: Just inspect for a good ground/return electrical path back to the battery negative. Make certain there is a heavy-gauge wire between battery negative and the body/frame for a GOOD return path from all cabin circuits back to the battery negative. With all of this you should do just fine. If there are any further questions, don't hesitate to ask.
-
I think what John is saying is the body and frame are the ground or return side of the circuits. The connections between the different electrical components and the body/frame are all dependent upon how good the electrical connection is back to the negative post of the battery. If there is a weak (connections) or inadequate gauge wire from the negative post of the battery to the body/frame, then ALL the electrical circuits that use the body/frame as the return path back to the negative post of the battery will be electrically WEAK. Using properly sized wire, per circuit current carrying requirements, will ensure there is GOOD electrical performance for those circuits. Good grounds/circuit returns are the other 1/2 of the circuit. A POOR return path make a POOR electrical circuit. Same is true for the positive side of the circuit. Not relying on the body/frame ensures a good circuit for the ground/return side. When gathering together grounds to a central point, the return path to the negative post of the battery needs to be even heavier gauge wire to carry ALL the current of all the circuits tied to it.
-
Poor grounds will become heater wires, like toaster elements, at their weakest points. When replacing them use the next gauge heavier wire and make them all come to a common point. Then use a heavy gauge wire from the common point back to the negative post of the battery. Then get a kit for the headlights which includes relays to take the heavy current off of the headlight switch on the column and transfer that heavy current load to the new relays in the kit. Then get the turn signal and headlight switches rebuilt. The same should be done for ALL the heavy current wires routed behind the dash. Also inspect the back side of the fuse panel for any poor connection and clean them up and resin core solder any poor connections there.
-
From 1975 to 1981 semiconductors made significant improvements. Yet the basics of EFI remain much the same.
-
Your Z is as good as it can be as is. Not much to be gained with a LSx or 2JZ, just more headaches. What year did you purchase the Modern Motorsports stub axles. Did the same and they are REALLY BEEFY. Also using the same R200 CLSD with 3.7 ratio. Only improvement might be beefed up 4L60E with steering wheel paddle shifters versus the 700R4. Other than that newer AFR COMPETITION heads might be a little bit better. Your Z is really 90%+ optimized right now.
-
Tony: You are quite accurate. "Japan Electronic Control System Co., Ltd. ("JECS") was formed in June 1973.[1] It was a joint venture between Robert Bosch GmbH, Nissan Motor Co. and Diesel Kiki Co., Ltd.. It enabled Nissan to use Bosch's engine control technology, and gave Bosch access to the Japanese market. JECS later expanded to manufacture many other automotive parts besides EFI systems."