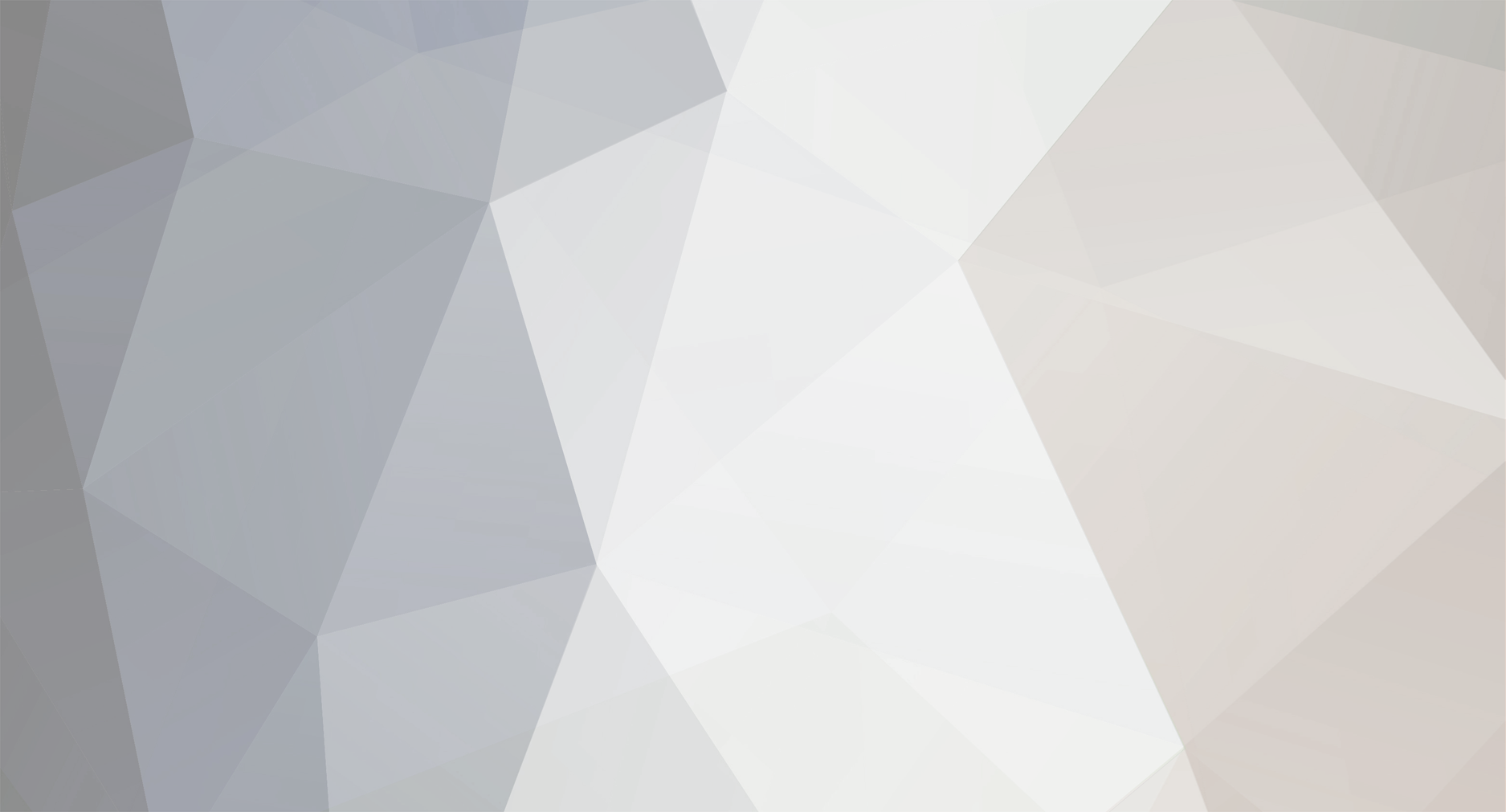
Pop N Wood
-
Posts
3012 -
Joined
-
Last visited
-
Days Won
5
Content Type
Profiles
Forums
Blogs
Events
Gallery
Downloads
Store
Posts posted by Pop N Wood
-
-
Thats a terrible price given everything that is missing and the fact that is the least desirable year of LS1.
Look at the price of the complete unit from a 2000 trans am in this ad
-
About half way down the page on the left is a link that you are looking for
A new, uncracked dash on a 240 is worth about $1000. Straight bumpers are pricey too. Check the rust carefully, especially on the underside. If all of that is good, than the car is well worth $4K. If you have any skills as a mechanic than the condition of the engine is almost immaterial. You could pick up a spare on this site for a few hundred bucks. It is the condtion of the body's that really determine the worth.
-
I still don't see them being the issue here, I mean, if the front member had been reinforced, would it have happened at all?
Well, possibly yes again. If you repeatedly bend a piece of metal back and forth it gets work hardened. That makes it brittle and prone to cracking. The solid mount is what caused the crossmember to get hard and crack. Solid mounting the rear would have help limit the motion and possibly prevented the front from going.
But regular inspections might have discovered the degradation before such a catastrophic failure.
-
the solid mount and urethane bushings were not the issue (as they are still intact), it was a lack of reinforcement of the stock front support.
Well, no, they are the issue. Something has to flex, and by using a solid front mount and flexible rear mount means the flexure HAD to happen in the steel of that almost 40 year old cross member.
I would be willing to bet if you magnafluxed any of your other crossmembers you will find some level of stress cracks on at least some of them.
Actually you are getting to the level of performance where normal rules no longer apply. JohnC once posted the preventive maintenance he did on his race car between each race and on a yearly basis. Might be a good idea to do something similar with the beast you have.
On the up side this answers the question we had on another thread about whether the diff is subject to twisting along the car centerline.
I wonder if you had a functioning arrestor strap if it would have saved the back of your diff.
-
That should be effective. Maybe not the 100% pristine engineering solution, but some times you have to work with what you have.
-
I had an old car that use to do that and it was valve guides. Oil leaks down around the valves and fouls the plugs while it sits overnight, then takes a little while to burn the plugs clean when it gets started. On my V8 it as the rear most plugs that fouled since the engine tilt caused them to be the lowest.
The correct fix is to get a head job. On some cars it is possible to replace the valve seals without pulling the head.
A short term work around is to try some hotter plugs. A good parts store should be able to help you get the hotter plugs. Also make sure the rest of the ignition is in good shape.
-
I'll be using motor plates (because I want full length headers) so my engine wont be as low as the JTR setup. I hope the new lower front diff position wont cause me any problems.
Thanks again,
Chris
It shouldn't. Lowering the nose of the diff changes the tilt. You will then need to tilt the engine to match. Getting the diff more "level" allowed me to sit the motor more level giving me more tranny to ground clearance.
If your motor is really high, then you may need some more backwards tilt on the engine to let the top of the tranny clear the tunnel. If that happens, you can put some washers on the mustache bar mounts to lower the rear of the diff thus getting the angle of the engine and diff to match.
-
Do the HybridZ DIY version
http://alteredz.com/Headlight_Relay_pg1.htm
There are tons of supporting threads where others have done something similar.
-
Yeah. Use the stock GM computer and either have someone reprogram it or get HPTUNER and a laptop to reprogram it yourself. That is what everyone else does.
-
Z Gads!! That's impressive! Expensive too.
Looks like you were still running the original R180 cross piece that came with your 72. The later R200 pieces are significantly heavier. There also looks to be significant rust on the inside of that piece.
What type of tires were you running? How long have you had the solid front mount and how many launches do you figure it had on it? We have had a lot of threads about fatique cracking with a solid front mount and flexible rear mount.
Sounds like time to do the Ron Tyler front diff support.
Maybe Ron was right about that 1/4 plate......
-
If you only have one spring gone bad, then wouldn't the back firing be limited to that one bore of the one carb?
-
All I can say is there goes the neighborhood.
Now we have to worry about a bunch of rich mofo's throwing money around to try and impress each other and driving the price of our hobby out of reach.
On second thought, now that I have looked at the pics I don't think we have to worry about this one selling for an excessive price.
-
-
I think the oil in the intake is being overstated.
From what I have read on LS1tech, it doesn't affect everybody. Only some cars are bothered by it, and it is less common on the later engines vs. the earlier ones.
Worst case just take the PCV off and put open breathers on it. The other day I found a nice valley cover with built in K&N filter for $60.
-
Sounds like something shorted out DOWNSTREAM from the ballast resistor causing excess current through the resistor.
Really, you should be able to jumper over the ballast resistor and the car will run fine until the points get pitted to the point of no longer working.
You need to be careful, because whatever is shorted may have been the cause of your fusible link/alternator going out in the first place. Fix the short before you burn up another alternator.
-
I would use something other than carb cleaner.
That stuff is too nasty.
-
Damn and I was just envying those nice, straight bumpers in the earlier pics.
-
You don't need more than 20 amps for the welders you are looking at.
Just go to Homers and get a receptacle that matches the plug on the welder.
I have a 50 amp plug receptacle on my 30 amp welder circuit. As long as the breaker is matched to the wiring size you are safe. Just don't go the other way around.
-
Sound simple. Get Georgia insurance.
-
The type of plug doesn't really tell you how much amperage the circuit is rated for. In a perfect world it should, but people take short cuts.
Find the breakers that control the two plugs you showed. They should have separate breakers since all 220V outlets need a dedicated breaker each. That should tell you what amperage that circuit will handle. Keep in mind the amperage rating of a circuit is determined by the size of the wire and not type of outlet. If you need a bigger breaker, you may need bigger wire.
You can alway change out the plug outlet to match you welder, but make absolutely sure the wiring matches the breaker size.
Also you shouldn't have to up size the breakers. The MM175 in the first link says it only needs 19.5 amps of line current. If that is accurate, you should be good to go with only a 20 amp circuit. Go to the Miller web site and pull up the owners manual for that particular unit to see what it recommends. But couldn't hurt to go 30 amp. A 30 amp circuit needs 10 guage wire.
That being said, unless you are planing on taking the welder to a buddy's garage, get the 220V unit. They draw much less line current and won't dim your house lights like a 110V unit can.
-
-
That is why I cut and pasted the entire head installation procedure.
I wasn't sure what "GM P/N 12346139" was. Thought it might be lube, but turns out it is brake cleaner. But when searching for that info I found this snippit from a Helms manual
http://www.ls2.com/boggs/torques/headboltinstructions.htm
It specifically states the M11 bolts, which are fastened with angle gauge, must be set dry.
I guess the moral of the story is to always read the manual.
-
I always thought the flap on the back of a Blazer was to prevent the rear window from getting dirty.
I thought it was so exhaust fumes wouldn't get sucked up into an open back window.
-
Head bolts 101, NEVER
EVER
should ANY head bolt on ANY engine from ANY manufacturer be torqued dry. PERIOD!
That is not what the GM service manual says for a 2002 Camaro engine::
-----------------------------------------------------------------------
Clean the engine block cylinder head bolt holes, if required. Thread repair tool J 42385-107 may be used to clean the threads of old threadlocking material.
Spray cleaner GM P/N 12346139, P/N 12377981, (Canadian P/N 10953463), or equivalent into the hole.
Clean the cylinder head bolt holes with compressed air.
Check the cylinder head locating pins for proper installation.
Install the NEW cylinder head gasket onto the locating pins.
Important
when properly installed, the tab on the left cylinder head gasket will be located left of center, or closer to the front of the engine, and the words "This Side Up", and the engine displacement, will be visible.
Inspect the gasket for proper installation.
Install the cylinder head onto the locating pins and the gasket.
Install the NEW cylinder head bolts.
Notice
Use the correct fastener in the correct location. Replacement fasteners must be the correct part number for that application. Fasteners requiring replacement or fasteners requiring the use of thread locking compound or sealant are identified in the service procedure. Do not use paints, lubricants, or corrosion inhibitors on fasteners or fastener joint surfaces unless specified. These coatings affect fastener torque and joint clamping force and may damage the fastener. Use the correct tightening sequence and specifications when installing fasteners in order to avoid damage to parts and systems.
Tighten the cylinder head bolts. Tighten
Tighten the M11 cylinder head bolts (1-10) a first pass in sequence to 30 N·m (22 lb ft).
Tighten the M11 cylinder head bolts (1-10) a second pass in sequence to 90 degrees using the J 36660-A .
Tighten the M11 cylinder head bolts (1-8) to 90 degrees and the M11 cylinder head bolts (9 and 10) to 50 degrees a final pass in sequence using J 36660-A .
Tighten the M8 cylinder head bolts (11-15) to 30 N·m (22 lb ft). Begin with the center bolt (11) and alternating side-to-side, work outward tightening all of the bolts.
Welder Power
in Fabrication / Welding
Posted
It can be difficult to diagnose when one phase of a three phase system goes out. I could tell you stories from when I worked in a nuc plant, but they are pretty boring.