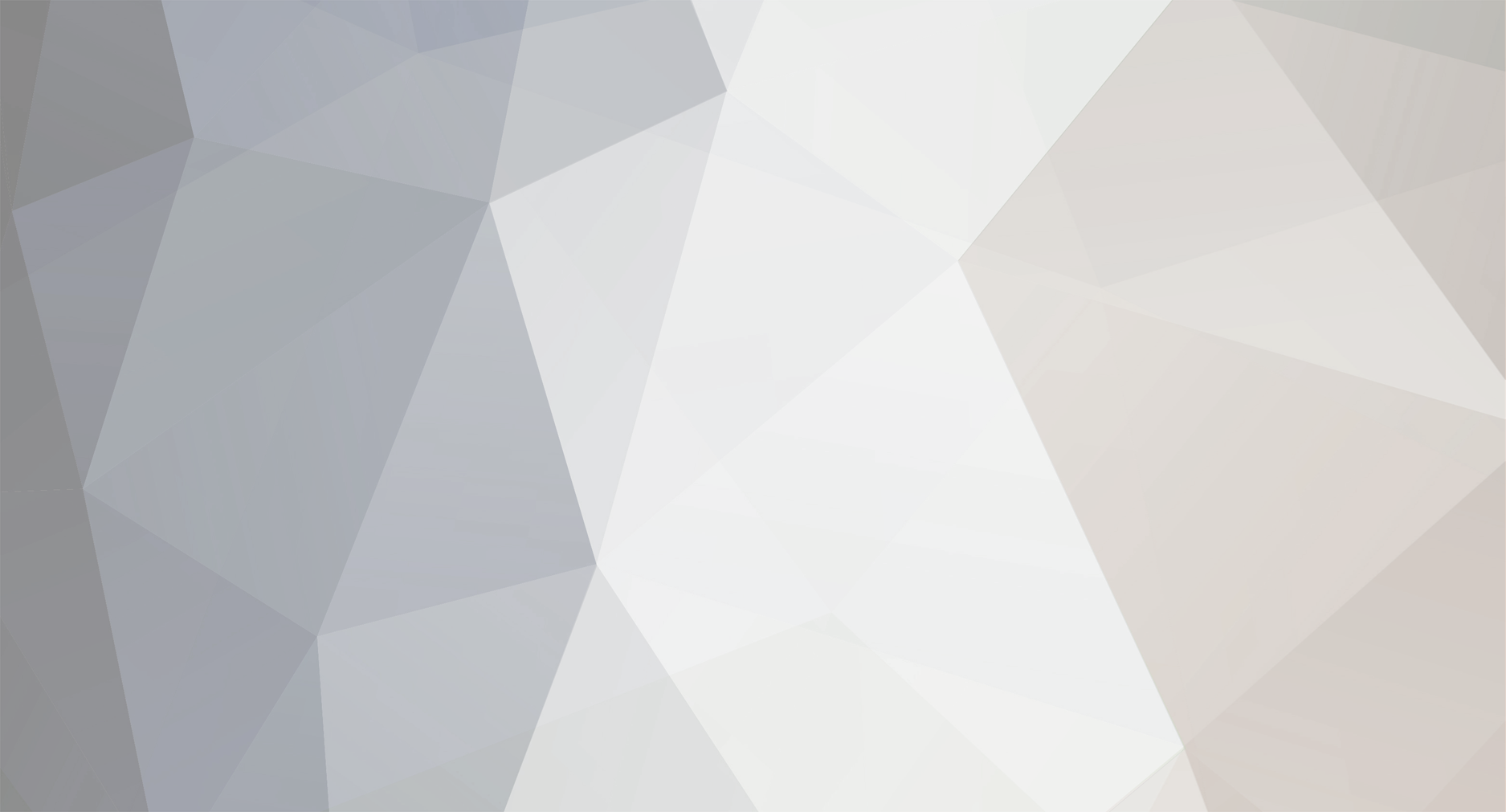
jeffp
Members-
Posts
595 -
Joined
-
Last visited
Content Type
Profiles
Forums
Blogs
Events
Gallery
Downloads
Store
Everything posted by jeffp
-
I ran 500hp at the flywheel with a TO4E and no NOS. hp @ wheel 413hp torque 475 foot pounds. Is that enough for you? I also have installed a new turbo and ran the car up to 27 psi of boost, much more power then 23 psi of boost.
-
ACT clutch just about on the way out... alternatives?
jeffp replied to a topic in Miscellaneous Tech
I bought my unit from Dymamic Motor Sports for 252.00 (CF DF unit) I did not like their unit myself, I had problems with hitting the flywheel bolts, on a stock flywheel. I can tell you that you will NOT get much more then 280 foot pounds of torque out of that unit new old or otherwise. My unit had about 5K on it and it gave out at that torque on the dyno. Give Robin a call at superior friction and see what he can do for you. (408) 436-1485 tell him Jeff Priddy with the 280zx sent you. hope that helps -
I used the stage 5 turbine wheel and machined the turbine housing to fit the larger wheel. I ran my car to 500hp and the spool was very good 23psi @ 3000 rpm, instant boost. the curve was so quick the car was almost uncontrolable at times, but it was fun.
-
I would really quiz those guys on the gear sets they are installing and how strong they are. When I was looking for a good tranny, i found a company in UK that was already doing a T5 upgrade, but they were a little unsure about the strength of the unit wil slicks. That is what made me say no go for them. They also have the dog ear type gera sets and the syncro gear sets. I wonder if this is what Gforce is using??????????????????????/
-
Before you take off much more of the bearing what you really need to do is to make sure the bearing edges are tight against the block. You may be dealing with a situation of the sides of the thrust bearing being bent out slightly. So if you make the bearing fit and then start running the car using the clutch and that stuff, you just may find yourself with to much end play in the crank, and I dont need to go into what that will cause. If you have a spare crank, install that part and use a block of wood on the end of the crank and tap(hit) it with a hammer to make double sure the bearing is cradeling the block correctly.
-
What are the pros/cons of building a turbo stroker motor?
jeffp replied to mrcheeze36's topic in Turbo / Supercharger
First off some of you guys are putting down very respectable numbers with your setups. I built the stroker really for one reason, I HATED the doggy bottom end under non boost conditions. I thought the really sucked off the line, it drove me nuts. That was my reason for a stroker. I dont believe the 89mm pistons are a good idea with a turbo engine, the 88mm pistons would be the biggest I would ever recommend for a turbo application, for the reasons stated above. I also increased the static compression to 8.5:1 for better power off boost and so I could fudge on the turbo somewhat. The one thing I have noted on my engine and setup was when I could build boost. My second turbo would build bost @ 3K not a ramp up, but instantly when you mashed the gas pedal 20psi of boost, the car was almost uncontrolable. This new turbo, although it spools slower( at least with no tuning, and it needs tuning bad) but the transition is much smoother and I can control the car much better now. The rod stroke ratio in my opinion was not sufficient with the 240 rods,at least for longevity, so I had custom length rods made for the engine. so that was my reasoning, and it has turned out well for me. My last dyno turned out 471 foot pounds of torque, and the turbo was out of air, so I went bigger. We will see what happens with the new program, 72Lb injectors and a turbo that can push 35psi at a much higher flow rate then my last unit. -
anybody know whats the most HP out of a Turbo L28ET?
jeffp replied to a topic in Turbo / Supercharger
First off, I did build my bottom end to be bullet proof. I did not want to try to build 500hp on stock cast pistons that had 200K on them and were sucking oil (about a quart per tank or 400 miles) Second, I wanted to build the bottom to last a good long time, and get a little more mechanical leverage with the longer rods. Then I finished it up with ARP studs in the head and the mains. 22psi on pump gas, you are really asking for trouble. You will have to really retard the timing, richen up the mixture to even attempt it. 400RWHP is not as easy as some may think. you will need to run at least 22psi of boost on a stock bottom end to even get close to that figure. Myself, I would not try it on pump gas, detonation on stock pistons are not a good combination. Anyway, good luck in your efforts, and you know, I have had guys telling me I could not do this or that all of my life. So go for it, just keep your head about you and you will reach your goals. -
Hi everyone, I have received the pipes, and have completed all of the other parts. I am getting boxes made Monday for all of the stuff for shipping. I must say I am very surprised at the lack of communication regarding my emails to all of you. Anyway, they are completed and waiting for boxes. I will mail everyone when they finish up the packing boxes.
-
search function being down really sucking... info on JWT ECU
jeffp replied to a topic in Turbo / Supercharger
I am running most of what lockjaw has on his car. He bought my turbo from me my last upgrade. I was able to pull 413 hp and 473 foot pounds of torque on the dyno my last run with the system. The car moves, no question about it. I get very good gas mileage @ 30-32 mpg and the drivability is very good in town and racing. I like the system because it is still the Nissan unit and it produces power. You use the stock harness (turbo) and make the changes to the fuel pump relay wiring(the stock 280 ECUfed 12 volts to the relay, the 300 feeds GROUND) you will need 7 ohm resistors in line (series) with the injector wires from the ECU and switch #2 and #5 injector wires for better performance (clark said most guys dont notice the difference but that is the correct thing to do) The ford MAF is 4 wires, 12 volts, 2 grounds and one sensor output wire. (They have the MAF connector for about 10.00) You need the 300 chopper wheel installed to tell the ECU where #1 TDC happens, the 280 chopper doesnot have the ability to do that. So they really have a complete package for 350 hp and 450 hp(I was able to get 500Hp at the crank) New developments here the last week: I have been working with Clark on a 72Lb program for the system, yes that is correct 720cc injectors. I got the flow data on the MAF and Clark is working on the program. THAT FOLKS, will push my car to 600hp at the flywheel easy, no problems. The ford MAF will scale to 1500CFM, plenty to run that kind of hp. So that is what is going on with the upgraded system. I have instralled a turbo that can push about 35psi of boost, that is aboput 10 psi more then my old turbo, so if I can run 35psi of boost, we are looking at more then 600Hp. So that is what is happening. -
Rising rate fuel regulators and turbos
jeffp replied to silicone boy's topic in Turbo / Supercharger
I have some input on this issue. First of all I have a reply to this answer::::A RRFPR is often just a bandaid, or a "shotgun" fix for a problem more directly solved by a good EFI system. I disagree, I am sure you can program dutycycle to compensate for the fuel pressure, but WHY? You need to keep in mind the pressure drop/increase in the intake manifold. You just cant make calculations easily for flow bsaed on duty cycle. The injector flow is a closed loop system, meanint that idf you have negative pressure in the intake, the injector will flow more fuel when you have pressure in the intake you will flow less fuel from the injector because of the pressure differential at the outlet of the injector. So using a 1:1 pressure regulator, takes the flow rart differential out of the equation for fuel flow. 1 pound of boost will get one more pound of pressure in the system, no matter if you are at vacuum in the intake or at 20psi of pressure in the manifold. The variables required, and fuel flow tables required to meter those changes are way more then the current systems are able to handle in my opinion. The tuning would be a nightmare. EVERY CAR you see out there has a pressure regulator on it, and every car will have some sort of regulator on it based on manifold pressure. RISING RATE REGULATORS are ment for POSITIVE manifold pressure above 14.7 psi or at the manifold 0psi manifold pressure. You are more then welcome to try a program tune without a vacuum activated pressure regulator, but you wil have to change your program every time you increase, or decrease altitude, because as you know, the pressure @ 5000 feet is nuch less dense then at sea level.anyway -
A real test of the difference a fuel pump makes (dyno)
jeffp replied to a topic in Turbo / Supercharger
First and formost that thing that needs to be cleared up is the requirement for a larger capacity fuel pump. I have done mucho research on this topic with my ca, completed accurate testing of the system for my application, but this info applies to all fuel pumps. Guessing when it comes to fuel pumps can be a VERY expensive guess. In order to determine if you need a new pump, you really should take the time to see just what your pump will do. You know how much the injectors will flow @ 3 BAR so that will be your flow rate of the pump minimum. The next variable is the fuel pressure. NOTE: a stock turbo fuel pump will crowbar @ 65psi meaning it will NEVER provide more then 65psi of pressure, so @ 3 bar (44.1psi) you will only be able to boost the car to 20 psi and the pressure will not rise anymore. Then you have the fuel requirements @ 65psi. For your injectors you will need 1554cc's of fuel per minute. So if the pump can run that kind of fuel delivery you are in there. Injector size is also the determining factor as to how much hp the engine will be able of producing. I will refer you to RC engineering for flow rates and hp ratings of the injectors http://www.rceng.com/technical.htm#WORKSHEET When you find out how much flow is needed to get the desired hp from the engine, then it is just a matter of seting up your system and testing it (not while running the car). Start with the static psi (3bar or 4bar) add in the boost pressure (using a rising rate fuel pressure regulator) the rate should be 1:1 on the regulator. so 43-44 psi plus the boost of 20 will give you 64psi. Then plug in the formula for the injector size to match the desired hp. for my car at 600hp 72lb/hr injectors @ 35psi of boost=79psi of fuel pressure the injector required will be 600cc/min to get 600hp, so the total flow of the system I will need is 3600cc's a minute from the fuel pump/lines/and rail. To do a quicky real time test on your system what you will do is hook up a fuel pressure gauge to the system (feed side of the rail) and test the car under boost. The fuel pressure should rise 1 pound for every pound of boost. The gauge should NEVER lose pressure under boost through out the rpm range. If you do see a pressure drop in the gauge under boost you need a bigger fuel pump, no question about it. Had you tested the system BEFORE you went and bought a fuel pump, you would have found that the stock Nissan pump was within operating requirements of the system and injectors. I guess what I am getting at here is that all of this stuff is just simple math, there really is no guess work to the equation. Just plug in the numbers and see what you get. Then after you understand the requirements of the system, test it on the car real time with all of the system components installed and see if you get the correct fuel from the system. Just going on the advice of someone for me in my case was not good enough, why, well because I have not found ANYONE that has done the real time in life testing of my system, and even if they did, I still would test my own car and system, you NEVER know is something is screwy on your own car for some reason. Come to find out, the 280ZXT system has a 4psi drop across the system from the fuel pump outlet, to the fuel rail. There is some restriction either in the fuel damper, or the line in some place is not the correct diameter(either through the bends, ir a ding in the line(it's the bends in the line) or the damper is the constriction. Well according to the data on paper I should be able to run X amount, but try running 4psi of pressure low @ 30psi of boost one answer BOOM! So My recommendation for anyone is to FIRST test the system before you buy anything. Save yourself the headache, the question of is it good enough and should I buy this or that. FUEL delivery components are NOT cheap, and replacing a component based on what who ever said will do this or that is just not good effective design, or rationalation for your particular situation. -
I guess the first thing I need to clarify would be the application of the bars and their relative location. The other thing theat needs to be realixed is the hp and torque of the engine installed in the car. I ran my car for a long time without a strut bar and I was running a good amount of torque and hp. The biggest problem I had with the car was the suspension and its components of the car rather then body flex. The strut rods were a big improvement, and the control arm bushings as well. I noticed more improvement then from just about anything else I did with the front, and a good 1 1/8" sway bar and good shocks and springs. Those upgrades did more for the car then a top strut tower brace will ever do for the car. if you go to the side of the tower(at least on my car) and press the side of the tower say 4" down on the tower, you can see the metal flex as you push on it, not very strong, it will flex, and dent with any significant force applied to it. The cowl is seemingly stronger, but tap it with a hammer and you will dent it easily. So that is the reason for my comments. Really if you want to REALLY strengthen the chassis of the car, then build an engine plate, attach brackets to the cross member bolts, attach a bar to the plate from the strut tower TOP. Then you have the foundation to link the front to the rear. That setup is really strong and will stop body flex. I agree, adding the bars do look good, but a bar to the radiator support will only support the radiator, not a big issue there with flex. I dont know, I'm not trying to be critical or rain on someones party, but I figure if I am going to go to that extent with the car, I may as well do a complete job, and make it fully functional for my time effort and money. anyway, sorry if I offended anyone.
-
most of the auto alternators will not supply enough current to operate the system at idle. so give it a littl gas and get it to about 1500 or so and try it again.
-
I have looked at your setups and have only one question: WHY?????????? installing an adjustable bar that way on a zx or any z for that matter does very little. I have personally taken the time to look at the structural improvements of such an install and have determined it to be a waste of money. The metal on the cowl is to thin, and the position of the bar to the side of the strut tower is to thin to make it worth anything. If you want some real stregnth, then do this. First off mount the bar to the strut bolts on top of the tower, then install a bar flat stock C channel would be very nice across the front of the cowl of the engine compartment. That will give you some strength. installing an adjustable bar on the hood latch is a total waste of time, the metal there is so thin it will not provide any stress relief or securing of the tower to ant significant amount to make it worth the effort.
-
I bought mine through Stillen. I like the part, but it has no degree marks, and yes the hole for the dowel pin is in the wrong spot. I drilled mine to get it closer. The part works well, and it has not slipped at all. The one thing I did not like was the star washers, when you tighten and losen up the nuts a few times, the star washer destroys the nut. I did a mod to mine and used a flair type nut and that has worked out well, I did have to modify the washer so I could get a socket on the nuts. I used a degree wheel on my cam the second time I had it apart and it was off about two crnk degrees, maybe because of chain stretch, maybe not. I would not say it is easy to make adjustments with, but for me it was the best way. I did it while I had the oil pan off the car, and made sure to make the crank degree tab was totally correct to make it easier next time. I like the part, but not having the drgree notches makes it a pain in the butt.
-
First question: >One thing I did with mine was make the tranny mount solid as well, and thus reinforce the stiffness of the unibody, but I had to use a 5-point system (front of engine, back of engine, and tranny) to make this effective. A 3-point mounting system (motor and tranny) would not be as effective in this regard but I would hazard a guess that it would be an improvement in adding regidity over the OEM rubber mountings. For myself, I did not want to go with the solid tranny mount to try to stiffen up the car. For me going that way puts to much strain on the tranny tail ahaft. I did not want to run the risk of breaking the tranny, or bell housing etc etc. I wanted a little flex in the tranny area when I really get on it. As it is the tranny moves very little and that is good for me. I did use the stock rubber mount, but installed the poly bushings in the cross member. That has worked out well for me. I mounted my engine with solid engine mounts and have not had any problems with them in the least. They have not loosened up either, bolts or mounts. The vibration, well it is not bad at all, in fact I like the way the car feels when I give it gas, beefy, and at idle there are no problems with vibration either. I went this way because of the close tolerances of my intercoolr pipes, fuel rail, and just about everything else LOL. So for me, I say go for it, and consider my thoughts on the solid tranny mount.
-
since you have tried the rich problems, try this. clamp off the return line of the fuel injection and try to start the car. Let someone else try to start it, or get one of those starter switches gizmoes and hook it to the starter to engauge the starter. Turn the car to on, clamp off the return line and hit the starter. See if it starts that way, and if it does, then you just may be way to lean for some reason. use pliers with tape around the teeth so you dont mess up the rubber FI hose in the process. hope that helps.
-
I looked at the various sprockets out there and the HKS was the winner for me. Te MSA sprocket has all the adjusting holes nd I did not like that idea of preset adjustments. The AZ acar sprocket looked like it was susceptable to coming lose. I got the HKS sprocket and an able to adjust any degree + or- 15 degrees. The down side is you need a degree wheel to do the timing. So you will need to know the lobe centers, and @ what lift the figures were taken at. Then its just a matter of setup of the degree wheel (easier said then done) and dialing in the cam. Then if you take the time to dial in the timing tab on the damper it is easier the next time to do the job. Cam timing is not to hard and you know when it is wrong. I think one tooth is like 19 degrees or so, way to much timing for any cam.
-
I have the turbo manifold, and you are correct, to polish it is alot of work. But if you decided to take on the job, the first thing I would suggest is a good abbrasive wheel to start. The wheel will remove most of the unevenness of the metal. There will be hard to reach places, so sand paper will work there. Then after it is smooth, go at it with some 400 grit wet sand paper, and wet sand it, then 600 grit and so on until you are ready to use polishing compound on it. Lots of work there, but if you want it bad enough, you can do it.
-
I did alot of mods to get the car to this point, and I am looking for a little more to about 600Hp. I have been working on that one for some time and do hope to get the fuel management to push it to 600hp.
-
I have 2 90 degree bends in my DP and the car is running 500hp. The back pressure at the inlet of the turbo is 1:1 so 25psi of boost gets me 25psi of back pressure at the turbo inlet. I dont thing the bends make that much difference in a mandrel system, in fact if you look at the bend radious and picture the air moving over the inner and outer radious, you wil find that it makes the air swirl around the radious, then into the second bend the swirl addes to the flow through the bend. anyway, I have 500hp and very low back pressure in my system and that works for me.
-
I spoke to Frank and was informed that they should be ready by the second week of Jan. That was the last I spoke to him. I do have the cats and mufflers ready to go. I am waiting for the DP to have my box guy make custom boxes so nothing will get dinged or damaged in the shipping, a added cost, but worth it I think.
-
I have that header on my webpage, along with the header I got for my car. I was trying to get some sales of the part with innovator Z but it never got started. That is an equil length header and from what I have been able to learn it works very well. The cost was about 1850.00 for the part.
-
I have been working on a custom 3" downpipe it feels like forever. I was able to get 15 guys that wanted it, and the 2 1/2" flange to go with it. So NOT all of us are doing the "group buy thing" just to steal everyones money. Look under my posts and see how long it has taken to get this thing going, and not becuse of me, but getting everyone to get their money in and answer all of the questions then work with the bender, the box builder, buy the cats amd mufflers, it's just been a pain in the butt to say the least. I still haven't cashed everyones money orders yet and have invested 950.00 of my own money on cats and mufflers. So I hope that gives you some hope for the froup buy thing as I am all over it, well as fast as I can be.
-
Having done all that you have done to your car and more, the labor costs can eat you alive. I decided long ago that if I was going to do these mods I was going to do them myself. So that is what I did. Bandsaw= 195.00 welder= 290.00+150 for the gauges and controller. So with that in my garage I was ready to do work. I went with mandrel bent pipes in steel, no to heavy, and 10.00 for each u bend. I needed 3 ubends and 1 jbend to complete the job. all total on thwe second set of pipes was about 250.00 with a new coupler and powdercoating. I saved tons of money, but I spent it elseware. My first proto exhaust cost me about 450.00 and then I had it made mandrel bent at Bassani Exhaust. That cost alot but it was worth it. So it is not cheap to have this stuff done. I have tried to do most of the work myself, I cant imagine how much more I would have paid for all the work. So yes it was expensive, but that is what you will pay to have someone do your work for you, sucks yea, but that is what you can expect. Lastly, if you want to see what the turbo will do for you, I am bnot to sure of the turbo, but remove the line from the compressor housing, plug the holes(or the hoses) and get the waste gate actuator signal after the throttle plate, like with one of the fittings on the intake, tee it and you will get you boost back. Just keep an eye on the boost creep and all that stuff. That will get the boost back up for you. Or you could go with a controller and control the boost that way. anyhow, hang in there, your car will get to where you want it to, I'm just not sure about your wallet, or my wallet for my little project LOL