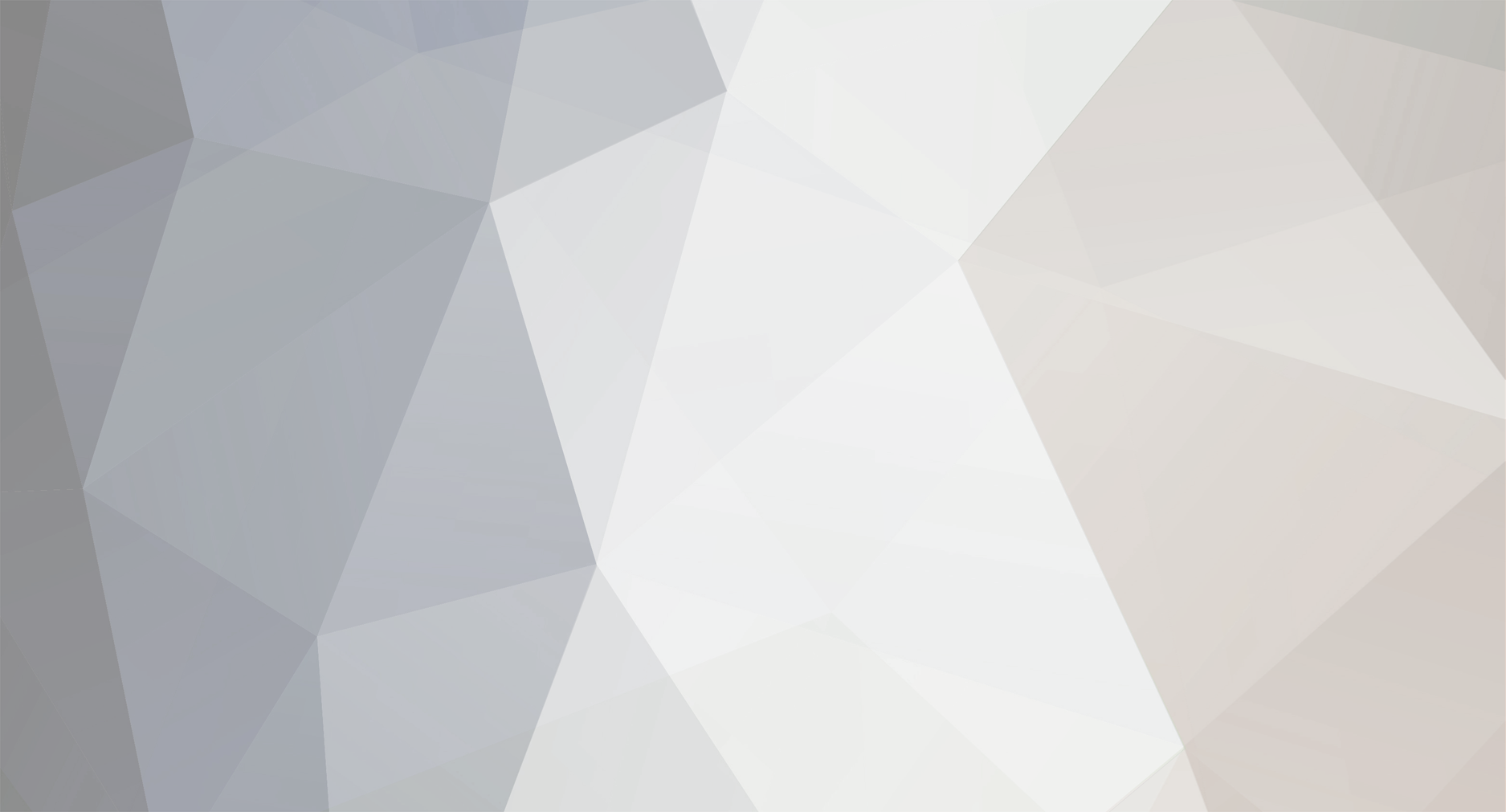
jeffp
Members-
Posts
595 -
Joined
-
Last visited
Content Type
Profiles
Forums
Blogs
Events
Gallery
Downloads
Store
Everything posted by jeffp
-
I took a look at their page and it sounds good. I don't really have anything to worry about though. All I need to read was that the system uses a 2 Kw alternator and knew automatically they were going in the oposite direction. Same principle, but totally different hardware and electronics. I was talking last night with my engineering buddy again about it and he has a basic design going for it. @KW what a joke, the alternator would be about half the size of the engine LOL to funny.
-
You may have something there with the chain being to long. BUT, the FIRST thing you need to do is establish if you can acheive the correct cam timing with the current setup. I realize Nissan tried to make it easy, and to be honest, I NEVER paid any attention to the lighter links on the chain as it really means nothing to me. The important thing you need to check is the cam position to the piston. Meaning, if the cam is specified to open @ 10 degrees BTDC, then make sure, no mater the length of the chain, make sure with the degree wheel the cam starts opening @ 10 degrees. Then you can atend to the slack in the chain issue. Make sure that when the chain is taught, by turning it with the crank, that the right side chain guide is not making any contact with the chain, or at least, VERY little. The chain guide introducing an angle in the chain by rubbing it, WILL change the cam timing, and after it runs some the chain will rub itself to where it wants to be, but you will again have to adjust the cam timing. So if you can getthe cam timing correct with the timing holes then you can then make adjustments to the left side chain guide by like you said elongating the mounting holes. The tensioner, you can also do the same thing to to move the piston back into the holder. I would first start with a Nissan part, just to be sure, but the degree wheel and cam timing will verify wether the chain will work.
-
I guess the very best way to see what is happening is to put an oscope on the motor b+ line and ground, to see if there is noise coming from the motor. I was looking at about 150millivolts of noise coming off the motor. For the majority of the electronics out there that noise floor will kill the operation at some point. When you stop to think that a standard radio picks up a signal from the air in the 113-120Db range(about .3 millivolts) one can reconize the problem quickly. You know, the more I work with the Nissan ECU the more respect I have for the unit. I think they did an excellent job on the box and most people, myself included introduce problems with all the new fancy crap that is being marketed. I havent had the chance to do any further work on the car here the last few days, between being sick, and the computer for the wife dieing I have been a little busy. Got to keep the wife happy, besides she gets on MSN for a long time that gives me time to do the car thing in the garage LOL. Is it the signal wire from the msd that is picking up rf? What if it is run alone? The MSD box is a noise maker period! I would like to take the time and tear one apart to see just how they made the unit. Coming from a radio background I reconized the noise the thing produced from day one. I just decided to deal with it by not dealing with it. I did not want to start screwing with their product, but yes the 6A makes noise. I did not have problems with it interfearing with the ECU, but it can be as simple as running their wires differently that will make it screw with the ECU. I would go back to stock and see what you get, and go from there. I like you also got new cap/rotor, but I have not installed them yet. I will get this thing resolved this weekend.
-
Good numbers Tim, I want to commend you on a job well done. So how does the car feel? How is the tranny and clutch holding up? half shafts and the like, or were you the one that went with the R230? Hell I cant remember now it has been so long. I tried to get my car tuned, but it did not work out the way I wanted it to, had some very uncommon problems with the car, oh well I got my stuff together now, I just have to wait to have it tuned again. Everything was looking good @ *psi on pump gas, but it misfired @ 5K oh well it's almost there. I was just glad to get the car out of the garage again, it was a year again this time. Dema did your cam, I had them do a cam for me as well. Good grind, but I was able to see some grinding errors from the grinder. I am running an ISKY part now and it appears to be a good setup. I will get the car done here in a few days, it's just been a little busy here, and man I feel like crap right now, really takes away from motivation after a full days work. Anyway, glad to see those numbers, I think you can get more then that, the question then AGAIN becomes, can the rest of the car and drive train handle the power? I noticed a very significant change in the requirements to push the rest of the car any further. Anyway, you should have some good fun drives.
-
I got to talking about my new Accel coil today with a few engineering buddy's at work and wanted their take on the size of the part in comparison to the electrical specifications. The convential coil configuration would dictate a much larger part then the part I have. We talked about how it would be possible to make a coil with it's electrical properties in this size. Ok so where is this going, well Karl and I got to talking about coils and a design that AGAIN was developed a few hundred years ago by Tesla, now aint that interesting. We went through a configuration of a coil that would literally knock the crap out of you, have much more efficiency then the standard coil configuration. Very col stuff, very cool indeed. Then I thought, well Tony has been harping on the concept of electrically controlling an engine and you know who I am speaking of. So I posed my thoughts to Karl on the matter, and since the new coil design is so much more efficient in regard to the delta factors. I felt that a relay configured the same way would be much more efficient in opening and closing a plunger, and not only that it would be able to handle a heavier mass because of the electromagnetic properties would also follow the response time to actuate a plunger. Now Karl's little brain is going right to town on that idea, and in fact has alreday come up with a design that he believes will have that abilities to control something like the weight of a valve, along with a return spring, in the event of loss of power to the coil, that would slam the valve shut, you know avoid hitting a piston. So Karl is getting some materials to test his design, so we will see here in short order what he comes up with. He thanked me for being such an ******* to mention the possibilities of electronically operating a valve in this fashion and how that then could be applied to the internal combustion engine. The efficiency of such an engine, in my opinion would increase by a factor of about 25% or more depending on the application. I also did mention to him that I know of a controller that could provide as much as 35 Amps to operate the relay, and that could be controlled on a per degree or greater of resolution. ree ree ree he is off to McFadden dale for some test supplies LOL, kinda like Tonie's evil twin brother does to me LLLLLLLLLLLLLLLLLLLLL.
-
After re reading your last sentence a couple of times, I think I was able to interpret your point and understood it as follows... The roller bearings, by design and function, will allow the two moving parts to function with one another, (as compared to the flat wiping surface of say Datsun L-series tappets), at given loads with less heat being developed even with the roller bearings smaller overall contact area, and as such there is, overall, less heat generated which reduces the demands made on the oiling system overall. Did that make sense? If that is what you said, yes, I agree 100%. So with the reduced heat, and friction being applied to the entire rotating assembly of the topend, one then can create a new design and operation Characteristic of the overall performance of the camshaft in relation to opening closing the valve. The opening event then can be much more agressive, that will yield the engine increased flow per degree of piston orientation, or pisition to Top Dead Center on the intake stroke. This will in effect increase the cylinder filling of the desired air/fuel mixture. This will also increase the volumetric efficiency of the engine as the pumping action of the piston, and the inertia of the incoming air/fuel will aid filling as the pressure differential between the cylinder and outside air equilizes. Now just as the inertia of the incoming charge gets to or beyond the pressure of the outside world, hopefully greater then the pressure outside, the valve then SLAMS shut to capture the excessive filling and reverse pressure differential (more pressure in the cylinder then the outside world). What you have now done is to increase the efficiency of the pump, much in the same way that a tunnel ram does on say a SB ford or chevy, this is very good. The exhaust pumping action then reacts very similar, only what you then do there is take advantage of the exhaust gases excaping at an accellerated rate because of the very fast ramp of the valve opening. So what this then enables you to do is to open the valve very fast, expell the spent gases at a faster rate, and then GET THIS, slam the valve shut so that you can run LESS overlap on the intake/exhaust valve that will promote an LONGER BURN of the air/fuel mixture in the cylinder. So with the longer burn time, more energy then is spent with the concern of pushing the piston back down the cylinder for a longer period, measured in degrees. MORE power for the same amount of FUEL/AIR for an overall gain in again efficiency, better power, better fuel economy, LESS emissions. So in in closing what you are doing is to increase torque, increase fuel economy, decrease emissions utilizing the same quantities of air/fuel, and infact you use less fuel/air to obtain the same amount of power. Decreasing the friction, that then decreases heat, and that is what enables you to increase the ramp time of the opening and closing of the valve to a higher rate to MAINTAIN the same constant of the factors involved. You improve the pump, and aint that what all of us want to accomplish by building "performance" in the first place?
-
Lubricant -- any substance interposed between two surfaces in relative motion for the purpose of reducing the friction and/or the wear between them. Lubricity -- ability of an oil or grease to lubricate; also called film strength. Film strength -- property of a lubricant that acts to prevent scuffing or scoring of metal parts. Friction -- the resisting force encountered at the common boundary between two bodies when, under the action of an external force, one body, moves or tends to move relative to the surface of the other. Hydrodynamic lubrication -- a system of lubrication in which the shape and relative motion of the sliding surfaces causes the formation of a fluid film having sufficient pressure to separate the surfaces. Full-fluid-film lubrication -- presence of a continuous lubricating film sufficient to completely separate two surfaces, as distinct from boundary lubrication. Full-fluid-film lubrication is normally hydrodynamic lubrication, whereby the oil adheres to the moving part and is drawn into the area between the sliding surfaces, where it forms a pressure -- or hydrodynamic -- wedge. Pressure -- force per unit area, usually expressed in pounds per square inch. Ball bearing -- an antifriction rolling type bearing containing rolling elements in the form of balls. Needle bearing -- a rolling type of bearing containing rolling elements that are relatively long compared to their diameter. I guess it is all in the way you think about it. I look at the wiping action of the cam and rocker arm as friction. Oil is then used to reduce the friction between the two parts. This equates to the drag cofficient of the two surfaces, and the improvement of the drag cofficient of the two surfaces when lubrication is the applied to the two parts. Agreed that the lack of lubrication, and the pressure properties of the lubricant to seperate the two parts and act like a buffer between the two will result in damaged surfaces in short order. However, when you look at the drag cofficient and the heat produced by that drag of two parts wiping across each other to the properties of the parts to a bearing, or needle bearing you can easily see the overall improvement of the drag cofficient, and the loss in heat produced by the wiping action of the two parts. Also dont forget about the friction produced by the two parts and the overall effect on all of the parts involved. The friction equates to again drag between the two parts, as the drag is increased, the energy required to overcome the drag increases, heat is then produced and you then go into the thermal properties that will again increase the drag of the two wiping surfaces. I also agree that the significant amount of the energy is required to depress the valve spring. However the friction and oil wedge you mentioned, along with the pressure the oil provides to keep the two parts seperated is much more then you realize. If the two parts were totally seperated, then there would be no need of a hardened part in the first place. While it is understood the majority of the wear of the parts will occur at first startup, keep in mind the parts will still wear over time due to the insufficient lubricating pressure of the lubricant in the first place. You are correct, and you pose some very important points well worth considering, however overall I believe the bearing contact area from wiping part to bearing is much less due to the properties of the bearing, and the ability of the lubricating oil to provide sufficient pressure on the bearings to obtain the desired improvement in friction, less requirements of the lubricating oil. Does that sound right to you? So waht does this all mean, you can ramp up the valve much much faster and maintain the opening significantly longer at a higher lift for an overall improvement in the ability of the pump to fill to capacity by reducing the drag on the components. So what do you think?
-
The roller rocker/cam setup is ideal for the L series engines, to quote a previous post :Granted, a roller rocker has some benefits, mostly in reduced wear, and also very small reduction in friction vs the wiper style. That is the understatement of the year. MOST of the friction in the L series engine is the topend. Just in case you disagree, get a high lift setup, turn the engine and you can feel the resistance to the turning. Then disconnect the timing gear from the cam and turn the engine, Difference between night and day. Roller setups were designed to reduce friction, period! and the ability to slam open the valve at a much higher ramp rate then you could EVER get from a tappet/wiper setup to do. The cam profile is like stated before, radically different, the roler cam brings the true meaning to the phrase "BUMP STICK" Getting such a cam will require a custom billet to start with, but I need to verify that, you may be able to get by with a solid reground Nissan cam, (not gun drilled for the lobe oiler) However, even still the lobes will have to be cut in the center of the lobe with a 1/4" cutoff wheel, about .200 deep, then welded, then ground to specifications to provide the hardness required to give the acm any kind of longevity. Now these units are a 1.4:1 rocker ratio, so you will need a higher lobe lift @ the cam to get for instance a .580 lift @ the valve then if you were running the 1.5:1 rocker ratio .415 lift VS .387 lobe lift. So you are talking radical changes in just the lift, and then the overall profile of the cam as stated earlier will be so apparent even the novas nechanic would realize the difference. The question then becomes, will you have a valve stem long enough to fit the head, and still have enough length to provide for proper valve spring compression, and not get spring binding. The standard cam gear/chain length would be much different, and you would definetly have to have full adjustability of both the cam chain and the cam sprocket to correct for the valve timing and proper chain tension. You would also have to have very good external oiling, to ensure the lobe and the roller bearing got the required oil to keep the parts from wearing out in short order. So to sum up, oiling, cam hardnness, ( I once got to see a roller cam when I worked at Sig Erson cams of a cam that came from Big Daddy's car that had soft lobes that ran 2 YES 2 seconds in the car and it was trashed) timing issues, chain tensioning issues, and finally valve stem length. Remember, the rocker geometry has to such that it will NOT promote the tip of the rocker to fall off the lash pad, and spring pressure that would folow the rocker/cam profile and shut the valve properly, NO bouncing on the cam allowed! Still another parameter, like the stock rocker configuration, is that the roller HAS to be in the center of the lobe, no hanging off to one side of the lobe at all. So if you can get all of those parameters met, then I say go for it, you will have the very best setup out there, just open your wallet very wide and drop all of the money out of it LOL.
-
I think I can answer that question well enough. There are a few things we need to realize about the MSD boxes, and coils in general. The MSD coil was key for me, because I needed a higher current spark under boost conditions. I looked around for coils and the first thing I looked at was the mallory coils, why, because I use to work for them. I was well aware of the coils they produced, but I also was aware of the fact that the coil I wanted for the application was not available any longer. The MALLORY voltmaster mark 2 coil would have fit the bill without any question. At the time I could not find one, new or used. Now there is Ebay, and I found three units and bought two. Keep in mind though, I have since found out the Voltmaster coil underwent a change in the early 80's due to manufacturing costs that basicall took a bullet proof coil and turned it into a not to great of a coil. Seems they decided to change the gauge of wire used to turn the coil, and they then became failure prone, where as before they NEVER went bad. So for me MALLORY was out, because I never did like the promaster, and that line of coils. Those units were designed for the Hyfire boxes, and I know for a fact they were having reliability problems with the Hyfire boxes. Then I learned about MSD, and I took a look at what they were selling and they advertised basically the equilivant setup. The coil specs were very close to the mallory part. I then took a look at the 6A box and liked the things like multi spart the unit would do. I went with the basic ^a, I did not want rev limiting of all of the bells and whistles, but just a box that would fire the coil under high compression. Then I had a failure of the coil just about the time I installed it. The steel core around the coil was zapping me every time I touched it. Well with anyone that has had the electronics background, like me, voltage on the csteel core of the coil meant it was shorting, or arching out. I sent it back and got a new one. The one thing that did bother me about the 6A box was that it had RFI leakage, I could hear the coil firing in my radio. But I could live with that and I did until the second coil failed, and I took that unit apart, after my conversation with the customer service weannie that told me there was something wrong with my car. I found where the coil was arching out, and I could see it at night when the car was running. So I still have the 6A box, and it is still noisy, and I have run it with the voltmaster coil. When I still had problems, I decided to run strait from the power transistor, and figured if the resistance of the primary wingings of the voltmaster was to small, all that would happen is I would blow out the power transistor. Since I had three parts, I ddecided to go for it and see what happens. Guess work here, as I have yet been able to get a good part number of the transistor to use as a reference to determine just how much current it could handle. The power transistor worked. I checked the case of the transistor while the car was running to make sure it was not getting hot, which would indicate the current capabilities of the part were being taxed. The transistor was not hot so I did a run, hooked up basically stock, but with the voltmaster. The car still bucked, I turned off the electric fan and it bucked hard once, I tried it again and it was much better. I still haden't gotten the RPM's up enough since the first fire to enable the ECU to learn the engine requirements. Now Accel, makes a very hot coil, and the specifications are again VERY close to the voltmaster coil. that part has not come in yet. Accel makes some very good parts, but I never liked their configuration, at least in the case style department, so I never used their products. So those are the BIG three, and incidentally, NISSAN made some very hot coils for their turbo 300zx applications. I have not tried any of the Nissan parts. Now it seems according to a company in Ausyland, that AFTER 2003, some manufacturers have again gone back to the high tension, heavy gauge coil wire and the car coils are getting much better. I think because now we have more capacitive discharge units in just about every car now, so long to the old points type configurations. The multi spart function, well there again it is not required, and if I had the time to actually test that function, I am just about sure it does nothing for spark and the ability to ignite fuel, possibly for fuel economy under light loads, but then by that same token, they ALL OF THEM, only work to 3K RPM's and revert back to one spark per one combustion cycle. So you tell me, is it worth the $250-350 investment that I made like many others, for a multi spark system, that will not take you to redline, and has some questionable effectiveness in the first place? I will say one thing though, I also found out that Electromotive used the MSD boxes, and come to find out, when they got a new box, they tore it apart and rebuilt it to their specifications. So go figure! I think I am goingto research out that aspect of the ignition system and see what I can dig up. I am curious as to what changes they made, and if I can find out that information I will let everyone in on what was changed, and more importantly, WHY. I can tell you this, the MSD setup I was running, with stock plug gap, was prone to misfires. I had to set my plug gap to .025 to stop the misfiring, so again you tell me, was it worth the money. I say I dont think so at this point, with the testing I have done thus far. I do have some possibilities of testing the coils under extreme pressures, and I just may check that out as well, just for my own interest in the matter. So there you have it. My recommendation is, that if you don't have any problems, then leave it alone, and if you do have problems, then check out your current system and make sure it is operating correctly befor you spend your hard earned money on all the fancy boxes out there. Myself, I am sick to death of dealing with products that are advertised to do X only to find out later they will not actually do X or if they do, it is short lived. Thats my story and I'm stickin to it LOL. Have a good one guys and gals. Now I have a circuit board to make.
-
I have two problems with the car. The first was the HVC coil was arching out creating a weak spark. So that was replaced with the MALLORY coil. Second problem, and I verified its disruption with the ECU was my new, well for the most part, electric cooling fan. So between the two of them the car would not like RPM's over 5K the weak spark under boost and the fan noise introduced into the electronics. Seems I was getting some good level ov spurious voltage spikes created by the fan, and the noise level of the moter also 150-200 millivolt noise floor is at the correct frequency, that when the trigger from the distributor got to 5K the ECU lost the correct signal and then tried to trigger off of the noise from the fan, the car died at that point and it appeared to be a misfire of the system, which it was, but in a direction that made it difficult to troubleshoot. I did end up running the car like the stock ignition with the power transistor directly to the coil. I did note the loss of RFI in my stereo amplifiers, and the car seemed to run more smoothly at idle. So liking simplicity, I just may remove the MSD equipment all together, I figure if I dont need it then why use it. That just equates to one more potential failure in the future. anyway, I just thought some of you may be interested in the investigation. I have a suppression/filter circuit I have come up with that has reduced the noise floor to about 20 millivolts, well within tolerances for filtering. I think I will go ahead and make a circuit board for the components and the power cables for the fan and be done with it.
-
I was thinking about it all night, sleep thought so fun LOL. Anyway, I am going to hook the soil up directly like the stock configuration and see how it goes. I am guessing that my problems will go away. I will post my findings, you know the only reason I installed their box was for two reasons. 1) to power their HVC coil. 2) to give me the three sparks for engine speeds up to 3K RPM's I felt the additional sparks would be helpful for fuel economy.
-
I have been running the car the same as when I first installed it. The box is mounted where the A/C cooling fan was mounted. The power is run along the passenger frame rail. The trigger is run down the radiator support and to the stock location as the coil was in the car. the trigger for the box comes from the power transistor, from the stock system. This is the ECCS system like on the 300zx cars.
-
Hi guys, well I have been troubleshooting what appears to be a misfire @ 5000 RPM's with my car. I am running a MSD 6A trigger box, and I had the HVC coil on the system. I first thought it was a problem with the coil, and I believe I was correct in that find. I then started looking around for another coil because this was the second failure in about 15K miles run time on the system. I called MSD customer service and they said it was a problem with the car. I disagree with their assessment of the problem. I had a number of guys look at the car, and none of us could find what we would consider a trouble area of the high tension side of the ignition. I decided to go with the sure never die old MALLORY Volt Master Mark2 coil. I thought for sure this would cure my problems. Well it did not. I am sure the MALLORY coil has more then enough poop to fire the engine under boost. I run the car and decide to data log the situeation, and sure enough the mixture goes very lean. So now my trouble shooting is leading me to do two things. 1) replace the cap and rotor. I checked the wires and they appear to be in good order. 2) run the car like stock with a really hot coil and see what the outcome is. The question I have for all of you is, have you ever had a failure of the 6A triggering box from MSD? Any input would be appreciated.
-
I just went through a cylinder head setup myself. You may want to consider opening up the runner at the head to 1.5" that way when/if you do the porting on the head the intake will fit the head well. The diameter of the gasket should do nicely. Just a suggestion, and you can still machine the runner to size.
-
The turbo I was running with the stage 5 exhaust turbine wheel was the T3 size. The T3 wheel : Major= 2.795" Exducer= 2.437" The Gt35R turbo Major= 3.307" (according to the previous post, I dont recall what I measured) Exducer= 2.677" That I am sure of So it is easy to reconize the turbo is essentially the same, but with a bigger compressor, and turbine wheel. You will notice, the slip ration has changed little between the two. The GT35R turbo is able to flow more air, both on the compressor side and the exhaust side of the house. Now I did my testing with the TO4E turbo I ran with Very good results in back pressure. Keep in mind the exhaust turbine housing was machined to fit the bigger exhaust turbine wheel. Also unlike the exhaust turbine housing of the GT35R turbo, the exit of the TO4E turbo dumped directly out of the back of the turbo, similar to air through a strait pipe. I don’t know how well versed you are with flow through a pipe, but a strait pipe actually creates turbulence at the exit point that has to be dealt with. The turbulence will hinder a smooth flow out of the turbo, so some flow is lost with that configuration. The GT35R turbo, if you take a look at the exit of the flow starts at the exducer size, and then opens up at a nice 7 degree angle to promote flow, to feed into a 3" pipe. Thus the GT35R turbo promotes flow out of the turbo and into the exhaust system, provided you don't neck down the exhaust pipe and downpipe. So in conclusion, the GT turbo is very similar to the TO4E turbo I was running, but more efficient regarding exhaust flow, and the ability of the compressor to flow a larger amount of air on the intake side of the house. The difference between a .63 and .82 A/R housing for spool is about 600-800 rpm's best case situation. The .63 A/R housing is much more efficient at spooling the turbo at lower rpm levels then the .82 housing, but with a properly sized exhaust system you will have no problems with excessive back pressure. My engine application, well there have been some significant improvements in the exhaust flow numbers through the cylinder head. The intake numbers were unchanged for the most part, so I am able to flow much better on the exhaust, and have gotten to that mysterious 70% flow of the intake that appears to be the constant for a well breathing engine. There is no doubt in my mind this turbo will do eaxctly what I wanted it to. It was unfortunate the MSD coil went out to lunch and screwed my first dyno test and tune. However, I know of one other car that is built similar to my engine, just not as efficient, and the bottom end not as agressive in compression, and the cam not quite as agressive also, that last dyno yielded him 700 foot pounds of torque at the rear wheel. The dyno chart you posted was in fact the chart of the TO4E setup, and yes I was not very happy with the results at the higher rpm levels, in fact it appeared very similar to a stock engine. I was not to impressed with that seeing I had an after market cam I designed the grind for that should have increased the peek power rpm and topend of the engine. Only after I pulled the engine down did I begin to find out why. Seems I had a head gasket leak in between 2 and 3 cylinders, that at the time I thought was unseated rings because it was a new build. That leakage explained why the engine, although was making twice the power appeared to be down in power. The second thing I have come to realize was the cam and the way I was running it. The cam timing was retarded to get some lowend power, and in addition to that the valve lash at the time was incorrect causing the cam profile to change significantly to the point that it made essentially the same power curve as a stock cam would. I realized this when I decided to degree the cam, in stead of using the stock timing marks that most builders use to set up their L series cam. The stock Nissan marks on the cam sprocket and the can back plate. When I degreed the cam, the lobe centers wer no where near what I specified, the opening and closing points of the cam wer way off as well. So no wonder the engine had a short peeky power band. This new build is excellent, the off boost response is excellent, and the car begins making boost at 2500 rpm's and spools very nearly as it did before, if anything a 100-200 rpm loss in spool, well within tolerances of a very well rounded street and strip car. the car picks ou the gears almost transparently to me as I shift. The transistion from no boost to full boost is excellent. I am happy with the build. Now all I have to do is to get some equipment from vendors that will do what they advertise and not go out to lunch in a short amount of time. I guess it's back to old school ignition components, the Mallory Voltmaster is definetly in order for a coil.
-
I'm not trying to have a go, I'm just curious. I'm also curious as to the 0.05" dur of your camshaft. Mine is just over stock at around 220 deg and I make max power around 6000 (I think). Advertised duration means jack ****.> That is simple, the A/R has not changed between the turbo's. My data told me that I was not making excessive back pressure @ 500hp @ 7K rpm's in fact the back pressure on the turbine was very good, some commented exceptional. What I had a paroblem with was the compressor and its ability to produce boost. I simply ran out of boost @ 23 psi and the compressor went into surge at that point, and I could see this by the pressure going from 23psi to 25psi but not able to maintain the 25psi. So the compressor was out of steam. The exhaust side was working very well at 7K rpms, back pressure was very good, it was the compressor that needed improving. I was running the stage 5 exhaust turbine. Now the exducer of the turbine was 2.448 diameter and that is the bottleneck of the exiting exhaust gases. So the gt35R turbo has the sams A/R but the compressor is bigger, able to produce in the range of 30-35psi of boost. The turbine og the turbo exducer is 68mm so the compressor is bigger, and the exhaust turbine is bigger for an overall higher flow rate then the smaller turbo. The A/R is still compressing the exhaust gases the same as before, but in effect the turbo overall is able to move more air because it is simply bigger, more air flow on both sides of the turbo. The A/R controls the speed at which the turbo will spin. A turbo with an A/R that is to large will not be able to spin the comprerssor effectively until the engine is pumping more air. The A/R that is to small will spin the turbo more effectively and sooner, but you will choke out the breathing of the engine before it reaches maximum RPM. A small A/R will be very effective and get to about 2/3rds of the rpm range, and no matter how hard or fast you stab the throttle, the engine is not going to move enough air to make the turbo boost effective, and what you begin to get is reversion back into the cylinderhead because the pressure on the exhaust is greater then the pressure of the intake. Air pressure will try to even itself out and follow the path of least resistance. so in reality, this GT35R turbo is essentially the same as the TO4E turbo, but on a larger scale.
-
I haven't gotten the dyno results from my new setup yet. The car was misfiring due to a defective MSD HVC coil. I will get the rreults here in a few weeks. data is data, I have gotten it and I know what this turbo will do. anyway, it's just a suggestion take it for what it is.
-
I have never reved past 5K now that is funny. I did the ONLY testing that I know of on the turbo and the .63 A/R housing. my test consisted of 7000 rpm's @ 23-25 psi of boost good enough for you? I never reached the crossover point. oh and BYW the engine was producing 498 hp give or take a few hp at the crank at that time. Total pain in the *** to test, but I did it before I got my third turbo for the car because I was deciding on the turbine housing A/R because I was afraid I was going to crossover with an additional 100hp. The third turbo housing was a .70 A/R part and it killed my spool, then I tried the stock .82 A/R for the gt35r turbo, same results, killed my spool. My cam came from Isky, a grind that Ron thought would work well, .585 lift intake, .540 lift exhaust 290 duration. I wont recommend a grind because there are just to many variables to get a cam in your application and have it work well. But a general recommendation is to go high lift, relatively short duration, and overlap if it is a turbo application.
-
Is There Such a thing as Too Big Of a Intercooler?
jeffp replied to t-tom's topic in Turbo / Supercharger
The idea of is there to big an intercooler, well not really, better stated is there to big a cooler for the application, yes. The intercooler will be more efficient and drop less psi of boost the bigger it is, meaning you have 15psi at the turbo outlet, and 13psi at the throttle plate, disregarding the tubing size for this exercise, you are developing 2 psi opposition to flow through the Ic, the cooler could be cooling the air charge most effectively, but because of the cooler makeup, it creates a backpressure on the turbo actual folw. So the bigger flowing cooler will have better/less pressure drop across the core, is it needed, maybe maybe not. The major consideration is size of the cooler and if you can get the thing in your car, if the cooler will not fllow efficently the CFM required for the application, will the turbo be able to overcome the flow loss to the engine to give you the flow you want. If your turbo can do that, and the cooler is still effective in cooling the air I say use the smallest unit you can to save space. Realize, that you will be very hard pressed to come up with an application that is perfect, so work to minimize the losses so that the turbo can provide enough flow in CFM for your application, and a cooler that will still cool the air over extended use. Hope that makes since. -
I am running a gt35R turbo, and one thing I noticed when I first got the engine going was that when the engine would die and it was not at idle, the turbo would still be spinning after the engine stopped. Not a bad thing, but still the turbo was spinning, and there was no oil supply because the engine oil was not being circulated. So in my opinion, make sure the engine is at idle when you shut it off, and at idle long enough so the turbo is not spinning faster then what idle will spin the turbo. That way, the turbo will not sit spinning for to long of a time after there is not an oil supply. make since? I guess one could always go electric oil pump and seperate the turbo oiling from the engine oil pumping completly to insure there is always oil to the bearings when the ignition key is on. Get a line off the oil pan and route it through the electric pump and heck you could even put a delay timer on the electric pump so that even if you turned the key off the timer would keep the pump going for a period of time and then shut down. That would be ideal.
-
Hi guys, I have just looked at your specs and I dont have as yet the complete dyno sheet on the turbo. I can tell you a few things though, you DONT want to run the .82 A/R exhaust turbine housing on the 35R turbo. The spool comes on to late for my taste. I tested that and was getting right around 3500-3600 and by 3700 could get the response I wanted. I did go with the .63 A/R housing and that is working well. Killing the power @ 7K well if you have your exhaust system good before with a 3" mandrel system you should be just fine. I tested my system back pressure and never reached crossover so if you do have a good exhaust then you will be fine. The GT housing is much better suited to run higher numbers then the older turbo's, and they now have som good vband attachments to the back of the turbo. I have not run my car up past 5K because the MSD coil I found out, only after I went to dyno the car is a piecs of crap and arching out. BTW that is the second coil I have had on the car from them and that was about 15K worth of driving. I placed a call to them regaring this issue and the cust service guy said it was my car creating the problem, which is total crap. I wont run another coil from them, I think they are crap, and I know of a number of others that have had the same results as I have had, so THEY ARE DONE! I will still keep the 6A. The turbo starts making boost in my car @ 2500 rpms, and I am looking at spool response right at 3K but I need to test some more. I kept the car cool until I got it tuned, and that blew up in my fact last test. Not to worry, things are well at hand, but being christmas and all I think the first of the year will be when it gets it's tune verified and I get the dyno numbers. I can tell you one thing though, @ 8psi of boost 5K rpm's the engine made 270hp and 290foot pounds of torque on pump gas. So this thing is going to really be a monster. I am very happy with the response of the turbo, it is very close to the TO4E I was running, so lets just see what the final results are. Dont worry about the .63 housing, go that way if you can get the turbo configured that way. When I got my turbo the .63 housing was not offered, then a year later and $600.00 for the part jethot and some special work I had what I wanted. Anyway hope that helps you out.
-
Help selecting a rod stroke ratio for a turbo build
jeffp replied to turbobluestreak's topic in Nissan L6 Forum
Well I set my engine up with a 1.75:1 ratio. I could have gone to 1.8:1 but I did not want to push the wrist pin into the oil ring. I am running an LD28 crank of 83mm stroke. The rods are 5.350" long. The engine torque ratings look a little weird when you look at the dyno graph. I made 413Hp @ 475 foot pounds of torque. Is that good enough? Generally, the longer rod will increase the torque readings, the shorter rods are for higher prm applications. So for me it was a longer rod, that enabled me to decrease the side loading on the piston and cylinder walls. Now the bore, well lets just say to bore 88mm and 89mm, the differences between the two are nominal gains if you take the time to do the calculations, and for me I opted for the stronger cylinder walls. The increases for the 89mm bore were not worth any of the down sides of going bigger. -
I have looked into this topic myself in preperation for a new system. I will be running the crank trigger setup, so the distributor is not needed. So what I did was to remove the spot in the cover for the distributor, molede the cover and welded the hole shut. Then, and here is the cool part, order, or get from a junk yard a LD28 drive gear for the oil pump. That will work very well, and you can totally remove the distributor mounting from the cover all together.
-
The fact that it doesn't burn up the wire and fuse link when the cap is in the circuit, tells you the cap is good. You can run without it. The injectors have a brown fuse link, check that. Check that you have voltage to the perspective ECU wires from the injectors. Also fo a quick check, since it is a turbo, remove the distributor and turn it, you should hear the injectors click, if not then either the ECU is bad, the distributor is bad, or you have an open fuse link. hope that helps.
-
First the intake side of the house. You will want to acheive the best flow through the system you can with the hardware you select. Keep the pressure from turbine to intake manifold as low as possible. That means the correct intercoler and pipe. You can run a little inefficient on the intake side if you have enough turbo to get to the numbers you want. The Exhaust side, the back pressure should not, if designed correctly, not reach the cut over point on the back pressure. This 2 1/2 times exhaust back pressure to intake pressure is ok, is just bull. That includes ANY turbo application, and will only serve to increase efficiency of the system in ANY application. If you plug up the pump with excessive pressure on the turbine side, there will be no place for the intake to exit after combustion, so try to keep it at least equil.