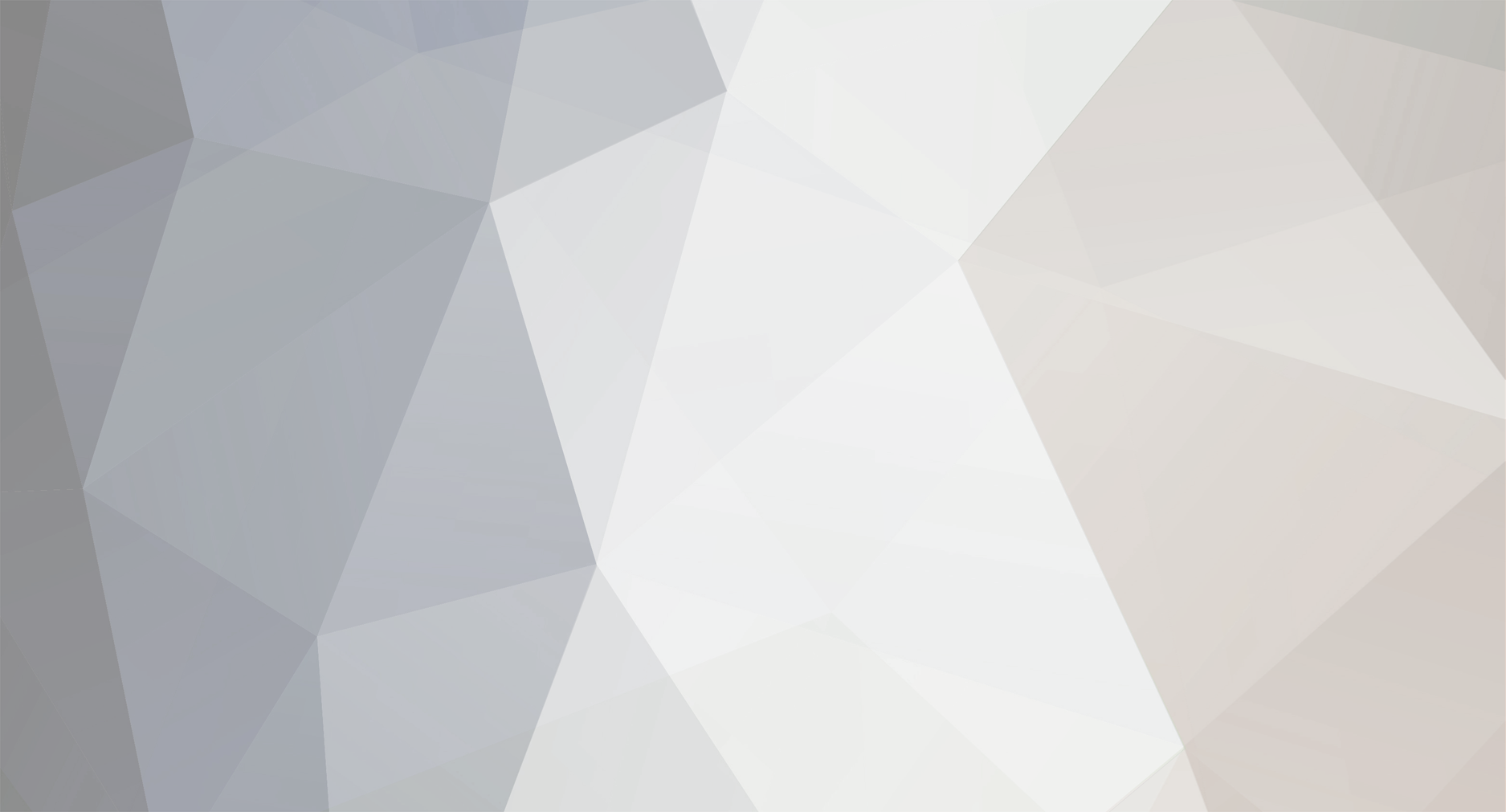
Dat73z
Members-
Posts
838 -
Joined
-
Last visited
-
Days Won
8
Content Type
Profiles
Forums
Blogs
Events
Gallery
Downloads
Store
Everything posted by Dat73z
-
I had a 30 min window this PM so I made a new line for the block coolant feed. Hopefully I'll have an hour or so this evening to wrap up the Tstat line as well.
-
This AM I started draining the coolant down and started back in on bracket fab. I think for the throttle cable I'm going to route it just in the space between the surge tank and heat shield. Hopefully with the new stainless cable and heat sheathing there will be no melting from the turbo heat in that location. Later today my Bossa Design water pump should come in, and my new Borg Warner Tstat on Mon so trying to get everything ready for that. Always something to do.
-
Today I was able to measure and trim the heatshield material. It was quite challenging to do as it is 321 stainless with an internal ceramic liner/air gap. Supposedly it can withstand 1800F continuous and 2000F+ intermittent. I hope it works to reflect and redirect the heat rising off the turbo into the carbs. The whole sheet needed to be unfolded, the cuts made precisely with overlap, and the overlap then folded back over. I haven't folded it back over yet as I'll need to punch a few holes in the stainless and fold those edges over for the vacuum lines, throttle cable, and mounting brackets. I decided to make this a multi-piece heatshield which will be assembled on the car as it was the only way to be able to snake it all in with the surge tank installed.
-
After more fitup and consideration for serviceability it is becoming clear that the heat shield dimensions will be critical. The surge tank must be bolted on before the heat shield otherwise there is no way to access all of the surge tank fasteners. I have some designs in mind, hopefully I can get to a final template later today and keep moving forward.
-
Thanks @rossman, always appreciate your insights. My AN fittings come in today and I get today off so hopefully I can get that back together. This morning I received notice that my heatshield material may be delivered early so I started templating things up. I think I'm going to fabricate some brackets to hang the heatshield off carbs 1 and 3 since carb 2 holds the throttle cable for which I'll need to make a new bracket for that as well to move the throttle cable away from the turbo. As always, everything on this setup is ridiculously tight with considerations to clear everything and serviceability. I've also attached a pic of the radiant turbo heat carnage on the throttle cable. I'm hoping the stainless cable, relocated away, and heat wrapped will be ok but we will see. I thought I was done with fabrication but I have to remind myself that just a couple months ago the car was in pieces on jackstands with no driveline. Just need to keep pressing forward and developing/improving the setup.
-
@rossman also I'd like to try the lower rad hose area as you suggested but I want to try the block first. Mainly because I don't want to run a line under the oil pan but I'll do it if the block feed strategy doesn't work.
-
@rossman a minute or two after shutdown the boiling from the CHRA starts. I think my issue is actually how I have my lines routed. You can see in the pic I drew on above, my turbo coolant line runs from the pass side, over the hot turbo and into the side closest to the DS shock tower. The return is lower on the opposite side. At shutdown the hot turbo heat rising into that line isn't helping either I'm sure and I think with the way that line is routed, instead of pulling cool water from the PS side it's boiling back over to the heater core branch... I'm going to swap around the lines with one feeding from the block, and the other from the DS shock tower side back to the tstat housing first. Just waiting for parts as usual. For the heat soak I've decided to go all out on it. This AM I safety wired in the vband shield. I also ordered some of this to fabricate a large heatshield under the carbs: https://www.heatshieldproducts.com/inferno-shield I will also do a brushless ducted fan or two to run after shutdown, similar to how I've seen some triple carb guys in Japan/tropical environments do to deal with the heat
-
I went for another long shakedown drive yesterday for an hour or so of mixed driving between traffic and high speed running. It is apparent one of the pitfalls of these setups is the extreme turbo heat. I noticed the plastic Lokar throttle cable I had recycled from my other build began melting from the radiant heat of the turbo. Also after long duration high speed running, if I don't open my hood at shutdown the fuel will boil in the carbs. I've ordered a stainless lokar cable and will relocate it away from the turbo along with additional heat sleeving and shielding plates under the carbs.
-
After a nice long drive, I'm still getting the coffee maker turbo boiling. I have some AN fittings coming in tomorrow so I'll need to wait on those to make the new lines. I'm really pleased though with how smooth the car is running now. Every time I take it out I've been refining the tune a bit more. I'm hoping it'll be ready for dyno tuning in a few weeks.
-
Early this morning I pulled vacuum on the system and held it at -25inHg for a couple hours. I have now both pressure tested and vacuum tested my system and am confident there are no leaks. I then filled the coolant via vacuum with the nose of the car elevated maybe 2 feet so the filler neck/coolant source was above the tstat housing. I reused the coolant + water wetter that I drained as it looks absolutely clean. I don't think I will ever traditionally fill a cooling system again if I can help it. Absolutely no mess and filled the system within 5 minutes. I will take the car out for a nice long drive over lunch to establish a baseline before making further changes to the cooling system.
-
As Loctite 567 has a cure time of 24 hours I've had some time to carefully look everything over and think things through a bit more. My CHRA has a slight clock to it upwards towards the DS maybe 5 degrees or so. I don't get boiling at all during running, but at shutdown, when there is no longer water pump pressure to force flow in the system the hot CHRA begins to boil the coolant which can result in localized steam pockets. Ideally, if the coolant has a gradual sloped return up with adequate delta T to promote thermal siphon this should not occur. At least that's what I think is going on based on a few hours of research. So I think ideally, the coolant lines in the turbo will need to be swapped around. Since I have everything set up modularly with AN fittings, I'm going to run down the following: 1. System as-is full vacuum test/fill see of it was an air pocket/lock issue and ensure there are absolutely no other leaks in the system to set the baseline 2. Block feed 3. Lower rad hose feed 4. Swap lines around, block feed 5. Swap lines around, lower rad hose feed I'm still not sure if this is really an issue, but I may as well take this as an opportunity to learn while optimizing the system. I think this should keep me busy this next few days.
-
@Zetsaz Yeah, probably the most annoying thing is there's no good way to fix it without pulling everything apart again. Oh well, a problem for another day 😂
-
Over lunch I removed the block drain and installed the adapter fitting. I'm going to first attempt the block feed location before trying the water pump outlet. Mainly for convenience of routing. Hopefully I'll have some time later tonight to fabricate the hose. I'm curious how the coolant vacuum test/fill setup will work out. I'm pretty oldschool and have traditionally filled and burped cooling systems my entire life.
-
It's turning into another crazy week so I had to break jacking the car up into 2 days lol. This morning I got up early and got the car in the air to prepare coolant draining. I also did an undercarriage inspection since I've covered a few hundred street miles. Everything looks good except the typical rear cap seal seepage. Pretty annoying but it's minor enough that I can live with it for now. Usually I replace those seals myself even if someone else did them as they're tricky to get right. In this case I sent it but as is tradition with that strategy I'll need to rework it at some point 😂. I snugged up the pan a bit more and will keep pressing forward.
-
Yes the L24 in your 240z is a 2.4 liter inline 6. I would recommend fabricating an actual shroud with an air space. The mishimoto has an inward ledge from the rear face to the actual core, something like 0.25" iirc. If you use a flat plate, consider how you would allow air to bypass at speed. Some people use a rubber flap such that when the car is sitting in traffic the flap gets sealed closed by the pressure of the fans on drawing air from the front of the rad. At speed the flaps open up for less air obstruction through the rad. I have fabricated a couple shrouds/iterations for the Mishimoto actually, here is an example I made using twin spal 12 pullers. If I ran it I would've added some flaps or louvers as I mentioned above. Either way start with a basic sketch and measurements, all of the items you linked had them then do some cardboard templating, all the basic fabrication stuff
-
Some good news, my 1/2 BSPT to -6an block fitting came in early today so tonight I'm going to install it and try out my new Harbor Freight vacuum bleeder. I think the strategy will be one change at a time. It will be another iterative and annoying development process, but hopefully one that gets me to a resolution.
-
If you mount a single 16 you may run into issues in terms of overall assembly thickness. The Mishimoto 2 core is a hair over 2.75" off the rad support. The fan you linked is a hair over 3.25" (~3.27"), and the shroud is 2 5/8" deep at the top. So your total assembly thickness would be 8.625" best case assuming all of the mounting is perfect, there are no dimensional tolerance issues, and your car isn't tweaked. The Water Pump pulley face is roughly 5.5" off the core support. You may be able to make it work, but the fan would not be mounted in the center of the rad. Edit: I assumed you had an L-series. I think the 8-9" measurement for the assembly is about right. If you are swapped, take a measurement from the core support and compare. I've seen SR20's and others which have much more room than the L6.
-
This morning I got up early and started taking some measurements for the AC system since it seems I may be waiting a while for parts...as is typical these days. I think I have most of the components for the AC so I can start cutting some shapes and welding up the compressor bracketry. I intentionally fabricated everything around where the AC components would go since I know my wife at least needs a heater and AC lol. The condensor I have fits perfectly between the intercoole/rad/oil cooler. I also already ran the integrated wiring for the AC when I reloomed the harness. I visited a friend this past week to borrow some OER jets and saw they had a really cool kick up/down solenoid on their triple Mikunis. I'm going to do some more research and see how I could implement this as my idle does drop a couple hundred rpms, esp with both efans going, probably more with an AC compressor running
-
Since I'm still waiting on cooling system parts and jets, I decided to try my hand at soldering and drilling jets. I successfully got the car to 11-12 afrs across the board. More tuning to be done but it's decently drivable now and at a baseline where I'm comfortable with boosting. Tomorrow I'm going to tune a bit more after work and put the surge tank on.
-
After a couple hundred miles of street driving it was time to check the torque on everything again since everything was redone. So far so good, only my vbands were loose due to thermal cycling/relaxation. I torqued them back up and will check again in another few hundred miles. At that point I'll safety wire them in along with installing the inconel vband shields. I should probably wipe the whole system down with acetone again too but I think that's just the ocd getting to me...it's an exhaust so it'll get banged up and stained.
-
Still waiting for parts so I continued tuning this AM. Things are finally looking up after all the new build drama. I was able to borrow a box of OER jets and the engine is running smooth at idle 11-12afrs and off idle but falls flat on it's face above 2-3k rpms pig rich 10afrs. A few years ago I put 36mm venturis into my 47 OERs thinking I was going to run it on my 2.5l turbo motor. When I moved, the 3.2 stroker was a last minute decision since I didn't want to put the spare engines and all of the stroker parts I had into storage. When I removed the main jet stack, the car cruised around at 12-13afrs. With the 36mm venturis on the pilots and my mains are coming online at 1.5krpms which is crazy but seems to make sense since the carbs are choked down to the lowest end of the range for 47s so the signal is much stronger. I'm going to borrow some mains jets from my other buddy today and if I can get the afrs at 11 across the board to start then I'll throw the surge tank on and start boosting/tuning from there. Really hoping I can get there this weekend 😁
-
It's really faint to hear but at 2 and 6s you can hear the movement of the coolant as it cools the turbo post shutdown. 20220729_190052.mp4