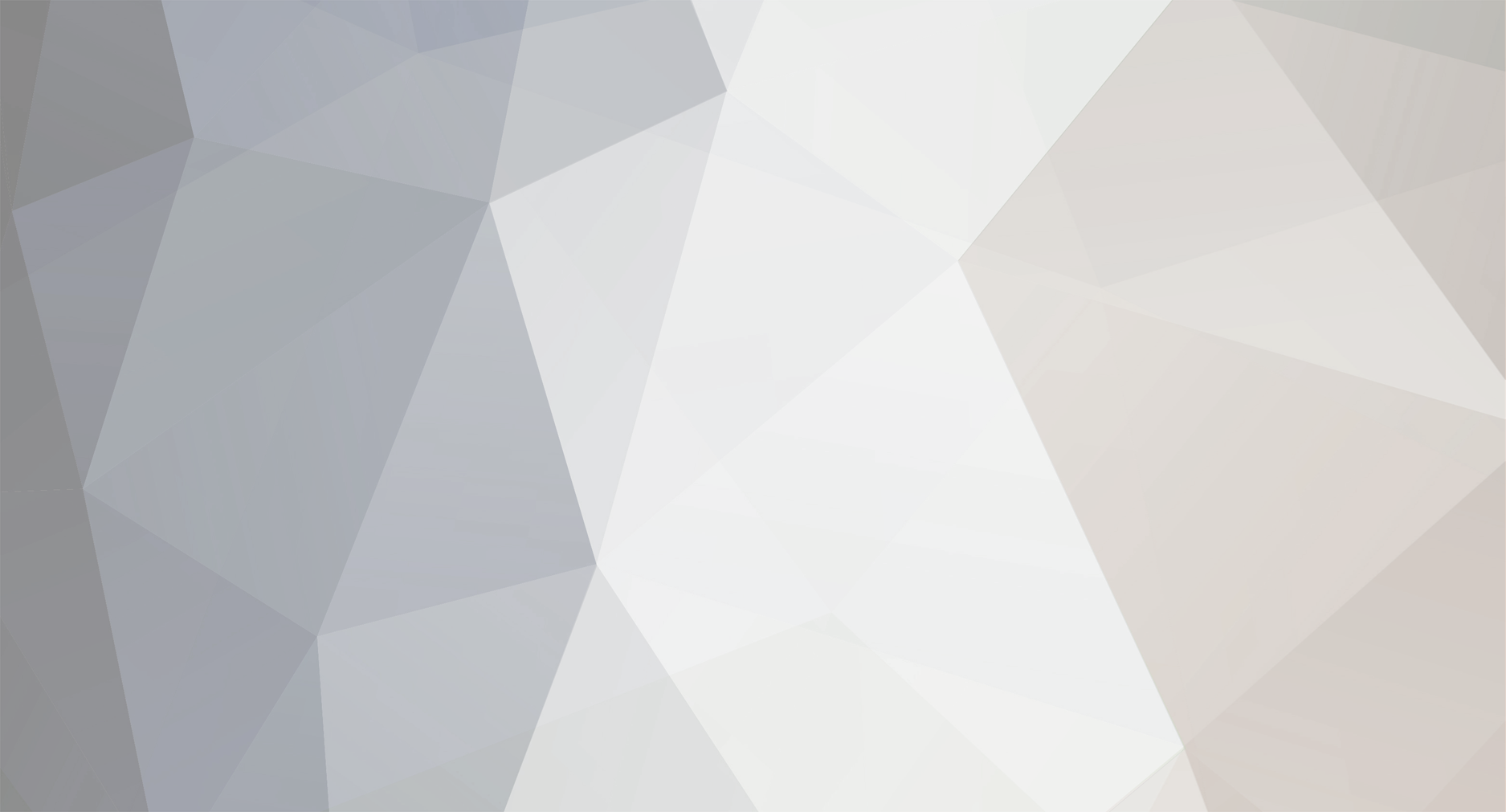
Dat73z
Members-
Posts
840 -
Joined
-
Last visited
-
Days Won
8
Content Type
Profiles
Forums
Blogs
Events
Gallery
Downloads
Store
Everything posted by Dat73z
-
💯 I would've saved hours, probably days if I had purchased the correct raw materials upfront. Good info on the various alloys...I'm actually a degreed and licensed engineer with a background in mechanical/materials but I'm only practicing electrical now. If it hasn't been apparent I've sort of just been sending it on this build in my spare time and mostly whatever I have on hand 😂 In terms of tig welding there are lots of affordable machines out there now. I started on mig as well and besides the additional and to me at least annoying prep/positioning that goes into a quality weld I prefer tig. You get a lot more control. If it's in the budget maybe get a cheapo tig machine and make some stuff. It's not difficult to do some functional welds and with your background in mig think you'll pick it up really quickly. Worst case your welds look like 💩 and you grind it down like you would with the mig lol
-
Thanks @AydinZ71. Honesty I'm not sure the alloy. I had a bunch left over from my wife's garden...reinforcement for some planter boxes I made and hangers for flowers. So I used all the scrap AL to create all the custom brackets I used for this build. It doesn't sand or weld very well at all and putting a uniform brushed finish on it was a pita. It's also like 1/8" thick so I'm limited to hacksaw or bandsaw for cutting and it doesn't like to bend at all. I honestly can't even remember where I got it, probably Home Depot or Lowes.
-
Yeah I found that out the hard way when I pulled the windshield and the previous glass co gouged and siliconed the entire windshield frame resulting in rust. Oh well, it's been repaired. This morning I woke up early to keep working the bracket a bit and make it look a bit nicer. I'm going to radius the edges a bit and maybe add some design elements like speed holes before calling it good. I also realized by cutting close with the bandsaw and trying to save some sanding time I created a bunch of extra work for myself blocking out the gouges for a brushed finish. I'm not a professional fabricator so I guess this will be a lesson paid for in extra time
-
Started in on mounting the overflow tank. I've been going back and forth on where to mount it given everything is so tight but it seems next to the rad will have to do for now. I started with some scrap AL from the garden which I also used to fabricate all of the other brackets on the car. After some trimming I think I have something that will work. The charge piping will barely clear beside, and the AC lines should have just enough room to run below.
-
I should probably also mention eventially I want to do all stainless hardline in front of the rad support for the oil cooler and AC, like how I did my fuel lines. For now I ran the SS braided to get me back on the road as I already had the AN fittings and hose. The 10AN SS tube and bending tools I don't have and are quite expensive
-
@AydinZ71 I agree less fittings, less chance for leaks. SS braided line really doesn't like tight radius bends, and it will eat through anything around it. I wanted to keep my cooler packaging as tight as possible along with my hood springs since this will also be a street car. I also couldn't move the oil cooler any further to the DS as I'm going to be running AC and my condenser barely fits in that spot, but it fits. I also wanted to run SS Braided and not nylon braided or pushlok. So it's a compromise from all perspectives. If I was building a turbo racecar I'd omit the hood springs entirely and move the intercooler forward and at an angle along with boxing on the entire frontend. Move the oil cooler further to the center and forward. That would gain the clearance to run some large swooping bends with the SS braided line and also make things easier to work on.
-
This past couple of days I've been busy working on some welding projects for other parts of the car but I managed to make some progress on the turbo build. The Wizard Cooling mounting tabs are off. After some test fitting I slotted the holes and bolted the rad in. I may raise it a couple of mm for additional clearance of the charge piping as well but I've been waiting on my radiator cap to come in to ensure it won't hit the hood with the additional height. Things are getting really tight. I found a 280z hose has the right bends but needs to be trimmed maybe 1" so I created a coupler from some scrap AL tube. It was good practice on cutting, grinding, annealing, and bead rolling. Hopefully I'll have enough time to fabricate a bracket for the coolant overflow can as well but we'll see how the weekend goes.
-
Is your clutch and slave system fully bled out and the clutch fork spring bringing the ToB and collar back to rest fully disengage the ToB from the pressure plate? Residual pressure in the system could cause the ToB to ride the pressure plate. I believe on the s30s the ToB should not be riding the pressure plate and that's how I measured it out on the clutch + ToB assemblies on my setup which is not OE (there are a couple mm of free play before ToB to pressure plate engagement) but maybe others can chime in as well. I would lean towards pulling the trans and replacing the ToB. Also ensuring all of the measurements are correct. I think you're fairly limited in what you can do with the trans in the car. I have seen clutch forks which have a hole and threaded bolt through it for adjustment but mine have always been the dimple and socket type
-
Haven't had much time to work on the build this week but got a more few parts in for final fitup. For the hot side pipe I wasn't happy with the original routing so after some measuring I added an angled coupler to gain clearance and clean up the run. Just waiting for a few more parts to come in and mock up which is mainly the coolant overflow before I slot the radiator mounting holes and finalize the position. Sounds crazy given how large the s30 engine bay is but things are really tight and since I work on my own car I've been trying to be thoughtful of how things are mounted as to be serviceable
-
Nice clean build. Arizona Z car sells a 15/16" master cylinder if you're looking for a complete solution
-
One item I installed earlier in the week for the turbo build were new engine mounts. I was searching for a moderate (e.g. non-solid) option for a while and couldn't find anything that I was satisfied with so I kept my good condition OE mounts and travel limiters originally. Recently Milkfab Engineering came out with a set of 40-50 shore D mounts which is a similar durometer to mounts I've run in my other street/track dual duty vehicles in the past that I've been happy with. I've run harder mounts in the past and personally don't care at all for all of the cabin vibrations for a street car. I was really impressed with the build quality and the alignment/installation was actually easier than the OE mounts due to the stud design. I like how the design takes into account the full stack height of the OE assembly (mount + travel limiter). They came with good instructions along with torque specs and Andrew @ Milkfab was also super quick to respond with any Qs. Pretty excited to see how these will perform
-
So far this weekend I haven't done much on the Z due to being distracted on a bunch of house projects. I've actually been waking up at 4 or 5 AM on some days just to get an hour or so in on the build before the day takes over. I did manage to wrap up the clutch lines, fill, and bleed everything out. It's nice to have working brake, gas, and now clutch pedals again, feels like progress is actually being made. First impressions of the OS Giken twin plate is the pedal is much stiffer than the Exedy 240mm I had before but definitely not as stuff as some of the clutches I've run on other cars. Definitely within range of what I'd consider streetable personally but driving and holding ability will tell the full story. If I can find a couple of hours today I'd like to at least final mount the radiator in position so I can move forward with the final looming of the wiring harness 20220605_084524.mp4
-
This evening I started unboxing and mocking up some of the parts that came in while I was gone. One large item was the custom 3" core Wizard Cooling radiator. It is definitely a quality piece. Test fitting in the car it barely clears everything, but it clears. I was also able to reuse my twin spal 12" fans. Unfortunately the mounting holes to the chassis are slightly off so I'll need to oval the holes in the rad brackets out slightly. Not a big deal, but another mini project for this weekend. I also threw the downpipe back in with the o2 sensor so I could start back in on welding up the exhaust bracing. I found it interesting how the inconel shielding was done. Originally I thought they would stop at the flex, but they covered everything in multiple pieces which allows the flex to flex as it should. They also including vband shields that I'll safety wire on later. I also got a bunch of other mini projects wrapped up around the car but trying to keep this thread focused on the turbo blowthrough L setup
-
For the first batch of machined parts I had some SS braided line separators made which were more legitimate than the zip ties I had prior. These also add support to the lines to keep them from moving around and eating everything around them.
-
Been a while since the last update but I had to take a 2 week break from the build for a nice vacation. Before heading out it was a frenzy of parts prep and fabrication before sending a bunch of parts and drawings off to have a few items machined and worked on while I was away. I've just received back my downpipe from inconel shielding and some parts from zinc coating. At this point I'm just waiting for a few items for final assembly. Hopefully I'll be back on the road this month if nothing else gets delayed
-
One year later I got the windshield glass back in. I used the vintage rubber seal and it fit perfectly all around with no gaps like I've seen on other cars. I still need to install the corner and bottom small trim pieces but I don't think that will be an issue with this seal, it's really pliable. Hopefully this helps someone
-
240z SCCA vintage race car, restoration
Dat73z replied to AydinZ71's topic in S30 Series - 240z, 260z, 280z
Are you limited by rules on tire sizes and/or how wide you can go? Looks great. Almost looks like you could fit those tires by trimming your existing sheet metal without flares -
The price seems pretty steep. Bear in mind headlight buckets and trim rings will vary in dimensional tolerances. I wouldn't worry too much about the seals, your headlight bucket area isn't airtight anyways. Use some common foam rubber type adhesive seal. The typical non-trim ring headlight covers just use a strip of channeled rubber around. For the mounting some people just ditch the OE type mounting hardware and run rivnuts. For an outward OE look you can get the oval head type screws as well although I doubt most would notice. Here's a pic of my later ones while I was waiting for paint to dry Edit: just took a look at their page and btw not sure what they mean by "fits more flush". Honestly the fit looks worse from their pics than the later versions on a well matched headlight bucket. On 3 different headlight buckets my headlight cover trim fits completely differently but I guess that's just how our cars and parts were made back then
-
A musician's therapist (The $300 Z)
Dat73z replied to Zetsaz's topic in S30 Series - 240z, 260z, 280z
After more than a few dozen trips to the hardware store over the years I finally bit the bullet and started doing large orders from belmetric. I think I probably saved $$$ overall compared to Home Depot/lowes/Ace/Fastenal even after shipping. They usually have the correct lengths and thread pitches I need although the head/nut sizes are usually different 👍 -
Only when I've needed to have the part sit flush with the surface, and I can't counterbore the part have I gone through the hassle of welding nuts. For something like flares, you'll probably be running some fender welting right? As indicated above imo I'd rather due rivnuts here as you can easily remove them with a countersink etc. and replace if they get damaged
-
A musician's therapist (The $300 Z)
Dat73z replied to Zetsaz's topic in S30 Series - 240z, 260z, 280z
Dude that is so sick! Looks like it pulls hard Yeah def check the spring. Also not sure if you'll run into this but with the ultimate internal wastegate my engine was seeing boost creep on the dyno so the port on the hot side got hogged out and I took out a bit more just to be sure. What're you running for your rear end? 3.54? By creep I mean with a 10lb spring it was getting up to 15+ by redline I believe but on a 3.2 -
Yeah I don't know why but I really struggled with drilling the o2 sensor hole so I definitely don't envy 2. The SS tube is ridiculous. I first tried a milwaukee hole saw and the blades flattened out and only scratched the surface within seconds. I ended up using a high quality carbide burr at high speed to wallow out the hole
-
It's been a busy month so far but I managed to squeeze a few hours into this build. Unfortunately most of the past couple weeks was spent wrapping up rust repair welding, bodywork, and paint. On the turbo build it sounds like my zinc coated parts are done, custom radiator is done, and some random brackets I had machined are done. So final assembly when those come in. Also welded on my o2 bung and will be sending the downpipe off for inconel shielding tomorrow. Little by little, day by day
-
A musician's therapist (The $300 Z)
Dat73z replied to Zetsaz's topic in S30 Series - 240z, 260z, 280z
@Zetsaz I'm sure it'll be a lot of fun once you get it all sorted. You have some good mods and the compression to crank the boost 😁. Post up some videos once you get it dialed in!