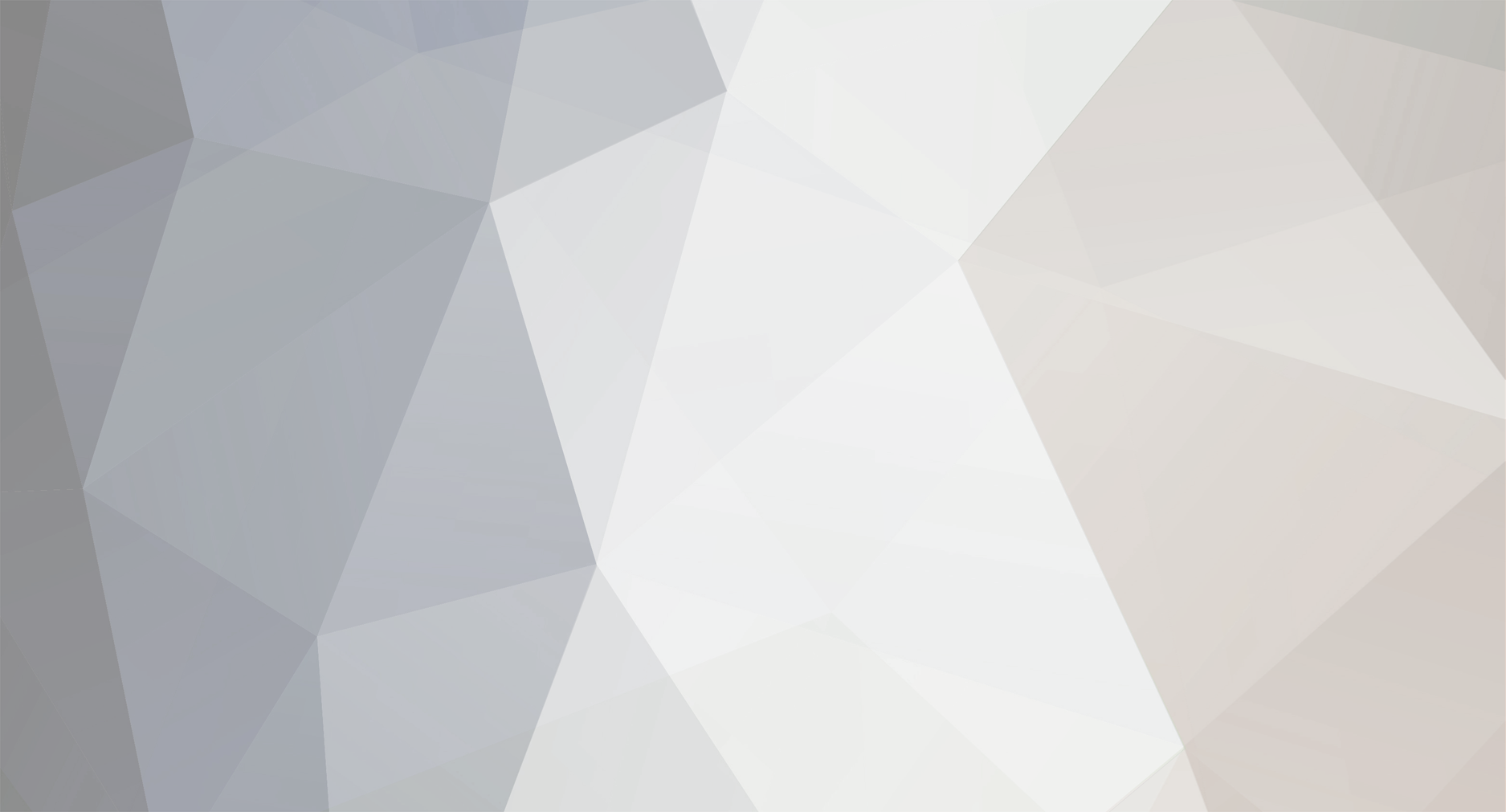
Dat73z
Members-
Posts
838 -
Joined
-
Last visited
-
Days Won
8
Content Type
Profiles
Forums
Blogs
Events
Gallery
Downloads
Store
Everything posted by Dat73z
-
This morning I continued with organizing the harness accessories. Eventually I want to fabricate some power/ground busses and a relay panel behind the dash, but I didn't want to get into all of that for this phase of the build. I think I need to get some round head allen hardware for the terminals as the bolt heads press against the terminal covers. A minor nickel and dime annoyance
-
Out of time tonight but I managed to get the harness organized up to the breakouts for battery accessories. Originally I was going to integrate all harnesses into one but I've decided to keep the fan and headlight harnesses separate for serviceability. I was also pleased to find my routing and mounting choices for the oil cooler lines and intercooler piping made working in the area a breeze. Really hoping I can get through this in a couple more evenings because leaning over the fender and crawling around is killing my back
-
This evening I started back in on shaping the harness. I replaced a few more connectors with OE crimp style. I think this will take a few hundred zip ties, but the harness seems to be holding the bends I want. I really dislike wiring generally but I'm trying to stay motivated on this part of the build
-
Tonight I had a few minutes to keep working the harness and got it mostly routed around the coolers. I think it's been almost a decade since I've owned this Z. When I purchased the car the PO was feeling under the fenders and told me there was a spare key hidden somewhere but he couldn't find it. Lost over 30+ years but I guess I finally found it
-
This morning I got up early and kept working the harness before heading out for Father's day. I forgot that I had made some custom horn brackets for PIAA horns as the turbo cooler packaging now takes up the space for the OE horns. The brackets I originally prototyped out of AL. The final version I made is 1/16 SS plate for rigidity. The brackets postion the horns to clear the intercooler and valence with a gap, and also helps to locate/support the harness behind so a multipurpose bracket
-
Had 15 mins after dinner and sorted the ignition system. I managed to pull the curves down that the engine ran on during the dyno. I think at 9-10psi it was at 350hp and trq. The curves are fairly typical for this type of setup including the map advance off load, the only difference really is the map section for boost retard. I also came to the realization that technically I could put some fuel in, fire the car up, and go for a drive right now. After all of that though I'm going to stay the course and finish this off right. Tomorrow I'm going to keep working the harness and prepare it for looming. I should also probably get the paperwork in for the tags and insurance. I haven't checked 240z prices lately but I'm going to assume I should increase my coverage anyways after all of this.
-
And I am an idiot. Shortly after my last post I realized my headlight relays were on the negative terminal. One circuit left to go which is ignition. Hopefully I can get that done tonight
-
This evening I was able to work on the harness a bit more. I'm down to the last 3 circuits which need to be addressed before I start tidying things up: 1. Fan Controller - forgot a ground whoops 2. Ignition system - it seems the green/white wire which I thought had 12v ign has nothing so I'll splice into the black/white upstream 3. Headlights - no idea yet, I can hear my headlight relays clicking but I'm only getting like 0.03v Starter and everything else including the radio and power antenna work. Really brings me back to when I used to drive this car every day. Hopefully again soon 20220618_180145.mp4
-
This morning I got most of the harness routing complete and tested. Wiring is probably one of the easiest but least enjoyable build aspects for me, next to sanding and bodywork. I rerouted the harness through some grommets on the valence support as the cooler packaging now takes up the original harness area. I think the strategy will be to zip tie every few inches to hold the shape of the harness/bends. Then when I pull it back out to loom, snip the zip ties as I get to them with the harness tape
-
Thanks @AydinZ71 I think I actually have something similar left over from when I set up my tig machine. I seem to recall it was RV cable or something. Tonight I made some battery cables and hooked up the major circuits in the car. So far so good and no smoke so the gremlins get to stay in my car 😁. Originally the cables were supposed to be temporary but I may just run them. I took an old set of cables I had and cut the tired ends off on a bandsaw. Then I hydraulic crimped some autozone special lugs on the ends and protected them with marine style heat shrink. It's been a few months since I started this but I've already cleaned up the harness and replaced all the connectors and crimp connections. Next steps are to test each circuit and ensure I'm happy with the layout in the car. Then pull it all out to loom. 20220617_203734.mp4
-
I used leftover silicone hose, clamps, and a barb fitting from when I was doing the turbo vacuum lines to plumb in the overflow tank. I forgot that I had ordered some new battery terminals as they were delayed for a few months due to supply chain but they came in earlier this week and also fit perfectly under my terminal boots. I'll take this as a sign to start back in on the wiring. I rebuilt the harness a bit with all new connectors and a dedicated 12v feed to the fuel pump. With all of the hard parts in place I'm going to work on finalizing the re-routing of the rad support area wires around the cooler packaging + looming
-
Tonight I wrapped up the bead rolling. It's been a really busy week but 15 mins here and there is bringing this to the finish line. This weekend I'm going to set mechanical tdc and on the distributor. Also see what base map Rebello ran the engine in on the dyno with
-
Yeah I was surprised to find that OE's basically run some improved worm clamps for even clamping pressure. I priced out Murray clamps and it's 1-200$ just for that, and HD clamps are like $100 each! Maybe someday in the future. I tested the tbolt clamps on my hot side piping and the movement is constrained to 1/4 or 1/3rd of what I had in the vid above when I'm really yanking on it. I'm basically at the point of having everything back together enough for a first startup so this will do for now.
-
So after a lot of reading on IC charge piping design, it seems: 1. A bit of flex is good. Setups with bracing can crack out the AL welds for brackets and this is a known issue even for mass produced intercooler pipe kits/hardpipe upgrades. 2. If bracketing and using silicone couplers, care should be taken to ensure that the bracket and chosen pivot point(s) doesn't create more issues with hose blowoff. 3. There are other coupler options available similar to vband clamps but can be fairly expensive and adds fabrication time. Some are able to flex, others have no flex. 4. If using silicone couplers, use high quality parts including at least tbolt clamps. By design, tbolt clamps do not provide even clamping force and can go out of round. There are other more expensive clamp options as well such as Murray clamps which are similar to what OEs use but with a constant tension mechanism. The best clamps have even tension and will not break or loosen resulting in boost leaks. I'm leaning towards no bracing and running the tbolt clamps I have to keep moving forward. It seems all of the other options are basically more $ and time for an incrementally better result. Open to suggestions if anyone has thoughts, here is the worst case movement I get with no clamps on the hot side. The cold side is fairly constrained and short. 20220615_202353.mp4
-
This evening I got my hot side piping mostly finalized. I was waiting to complete the rad fitup before final trimming and I'm glad I did. The final clearances came out just about right. I did the final cuts to the charge piping on the bandsaw then using my new clean hose cutting skills trimmed the silicone coupler down a bit. The pipe needs to come back out one more time for bead rolling and maybe refinishing. Unfortunately during the past couple of years when I was moving around and couldn't work on the car I carried the piping with me with every move instead of putting it in storage with everything else so it has some nicks and scratches. Not sure if I want to put the time into that right now. I am also considering fabricating and welding in some bracing for the charge piping that bolts to the head but I need to do some more research on the pros/cons of that. I've seen a lot of turbo builds that run without it and some that do
-
With the radiator change fiasco out of the way I started back in on final trimming of the intercooler piping over lunch. Because everything is so tight on this setup I've really been trying to be considerate of serviceability, even something as simple as trimming tube. For the cold side I sectioned the run to give just enough clearance to swing out of the way of the upper rad hose. Otherwise I'd need to drain the coolant down and remove the upper rad hose to work on this section in the future. I need to do some final adjustments and bead roll the ends.
-
Last night I finalized the rad positioning. I was able to raise it 1/4" which left me somewhere between 1/4-1/2" spacing between my chosen rad cap and the hood bulge. It is now hopefully not coming out again for fitup. I also trimmed the coolant hoses to fit and installed the hose clamps. I can't remember why I decided to use the OE style clamps as there are better styles available but I think it was because I was sending a batch of parts out to zinc plate anyways and I already had them. On cutting the hose I have always struggled with making clean cuts so for this build I decided to change that and attempt to make clean cuts.
-
And after more measurement and mockup with what I have on hand it turns out the 240z hose with a 90 from the 280z hose at the bottom with the AL coupler I made will work. It's not perfect but the closest point is to the fans. I figure when the fans engage or driving the hose will tend to move back towards the firewall instead of towards the fans. I wonder if my aftermarket 280z hose is a lot different than the OE 280z hose as the 240z OE hose runs a lot further forward to the rad before bending down. But I'm only $14 into it and I guess in the future I can just order a 240z hose, a 90 elbow, and reuse the coupler I made. I was kind of hoping I could use order a 280z hose in the future to trim but if anyone has pics of the OE 280z hose in their car please let me know.
-
Nice! I tend to geek out on details when I'm working but when I'm doing my own projects my brain is 99% unplugged which is also why I tend to go through a bunch of revisions and whoopsies 😅. I'm in the SF Bay but formerly LA/OC. Tonight I started fitting up the lower rad hose. I started by trimming the 280z hose 2" in the vertical plane and added the coupler I made. Then I realized the assembly is way too close for comfort to the oil cooler lines and alternator fan. The Wizard cooling radiator is much larger than the Mishimoto unit. I have a few options here I believe. I'm going to start by trimming the 280z hose a bit more to see if I can pull the vertical portion of the hose away from the oil cooler lines/alternator and towards the rad. If that fails, I have some scrap AL tube and I was thinking of hardlining the entire run and having just 2 rubber or silicone couplers at either end. The 240z hose is just dimensionally wrong due to the increased size of the rad. I feel like every time I do anything on this car a bunch of custom fabrication is required but the build goes on
-
The ultimate Z car strut solution (possibly?)
Dat73z replied to clarkspeed's topic in Brakes, Wheels, Suspension and Chassis
Doesn't Tein already have a solution like this? I recall maybe 15 years ago I got a ride from a mutual friend who had a Tein coilover setup on his Lexus GS. He was able to adjust the rebound from a Tein module on the dash Edit: Found an older article on it https://motoiq.com/tein-edfc-active-controller-suspension-tuning-at-its-best/ -
@Zetsaz Here's a better shot of the clearances. I think I recall the mishimoto is slightly smaller so you might be able to tuck it in even tighter
-
@Zetsaz yeah it fits pretty good, pretty happy with how it came out 👌 It is a champion 2"×10". I got the idea off some posters on FB. The guy who sent some installed pics had a slightly diff mounting config and what looked like the larger 2"x13" bottle
-
Final weekend update on the turbo build. Just wrapped up the coolant overflow mounting. I was thinking to do some aesthetically interesting things to the bracket but ultimately kept it simple with radiused edges and a brushed finish mainly because I kept getting distracted so function over form. Hopefully my radiator cap comes in early next week so I can do the final adjustments to the cooler packaging and move forward with final assembly. Next week there are a couple of non turbo related items I need to address but I think the objective will be to get the engine ready for the first fireup.
-
💯 I would've saved hours, probably days if I had purchased the correct raw materials upfront. Good info on the various alloys...I'm actually a degreed and licensed engineer with a background in mechanical/materials but I'm only practicing electrical now. If it hasn't been apparent I've sort of just been sending it on this build in my spare time and mostly whatever I have on hand 😂 In terms of tig welding there are lots of affordable machines out there now. I started on mig as well and besides the additional and to me at least annoying prep/positioning that goes into a quality weld I prefer tig. You get a lot more control. If it's in the budget maybe get a cheapo tig machine and make some stuff. It's not difficult to do some functional welds and with your background in mig think you'll pick it up really quickly. Worst case your welds look like 💩 and you grind it down like you would with the mig lol
-
Thanks @AydinZ71. Honesty I'm not sure the alloy. I had a bunch left over from my wife's garden...reinforcement for some planter boxes I made and hangers for flowers. So I used all the scrap AL to create all the custom brackets I used for this build. It doesn't sand or weld very well at all and putting a uniform brushed finish on it was a pita. It's also like 1/8" thick so I'm limited to hacksaw or bandsaw for cutting and it doesn't like to bend at all. I honestly can't even remember where I got it, probably Home Depot or Lowes.