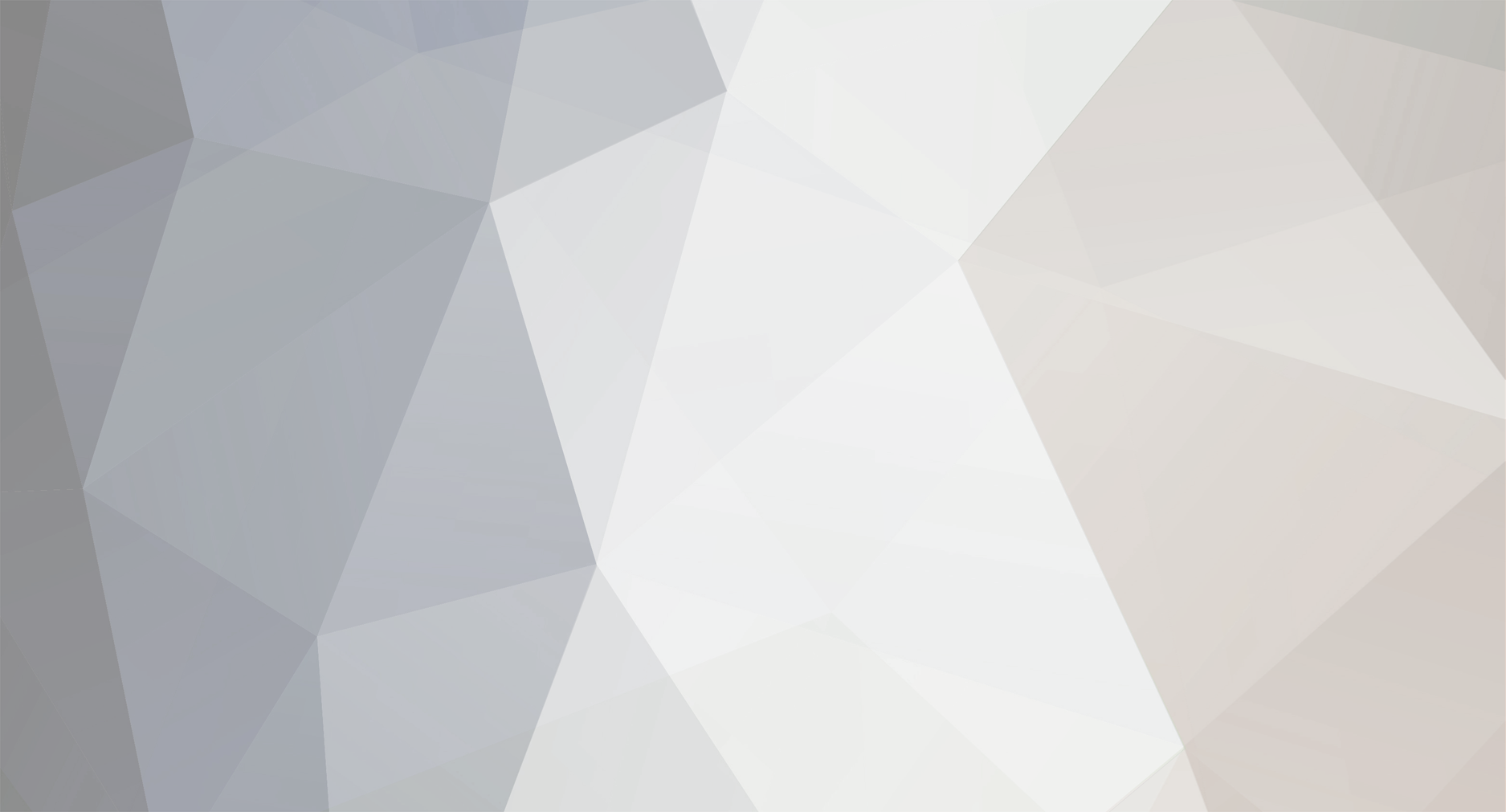
WizardBlack
Donating Members-
Posts
1444 -
Joined
-
Last visited
-
Days Won
2
Content Type
Profiles
Forums
Blogs
Events
Gallery
Downloads
Store
Everything posted by WizardBlack
-
I have used some that did and some that didn't. You'd just have to tweak it a bit. Perhaps placement isn't ideal. Always try to put it right up close to the TB.
-
LOL. Well I never really was much of a fan for the 'linearized' theory or using PV=nRT. I have tuned dozens and dozens of turbo cars with standalones with direct access to pulsewidth. They never make a very good linear ramp IMHO. A good place to start? Yes, but they need more work. Likewise, most of the maps you see on here don't sport very close to 100% VE all across the map. They SHOULD, though, if that theory were true. Like I said, the very high vacuum areas are always much lower which goes to show it doesn't work like that. The nature of turbo cars affects part of it, plus powerband, head porting, cams, etc. etc. Basically any part of the powerplant that isn't 'plain vanilla' design. I don't think any of us (nor the Datsun engineers) are going for that...
-
Here is a direct copy and paste from Megamanual under Tuning; almost halfway down on that page: PW = REQ_FUEL * VE(kpa,rpm) * MAP * E + accel + Injector_open_time You know, I thought the same thing about using 100 ms for Required Fuel as long as the ECU can handle the extra digit in the size of the number until I saw that MAP is indeed used as a variable; or so it says. It certainly wouldn't be much of a 'volumetric efficiency' if it didn't take pressure into account already.
-
I am just wondering if anyone has gotten rid of the old fueling formula currently used by Megasquirt: PW(fuel) = Req.Fuel x MAP/(100kpa) x VE/(100%) + E and simply switched to a fuel map where you tune the pulsewidth directly like most standalones. I know it can't be any harder on the processor (actually quite a bit less calculation) and it is certainly easier for anyone who has tuned many standalones. You could still use the handy power and engine size calculator to fill in starting numbers and simply reconfig them to plug pulsewidth in directly. I mean, you can take someone's VE table and get their 'required fuel' number and actually calculate it in a spreadsheet such as excel (or even better, the free and compatible alternative). Any thoughts? I'd be down for it.
-
I bought a Chrysler T&C 3.8L coilpack from the local Autozone. It is nice as it has four bolt holes through it and it's flat on the back. The connector protrudes up through the top just like the pins for each cylinder. It looks just like the one that BRAAP was using. It is also labelled. I wanted to make a note that it doesn't work quite the same way as the other coilpacks some are using. They mention a firing order of ACBACB for the EDIS pack. This doesn't correlate to labelling the three coils A, B and C on the coilpack, however. The best I can tell you is the firing order of the engine (the coilpack came off of) is incremental (1,2,3,4,5,6) so just look at the molded-in cylinder numbers on the coil and compare it to the outputs of the EDIS pack and the Datsun firing order (1,5,3,6,2,4) to reason your way through it. It came out differently than I expected. Perhaps the 'Dodge coil pack' pinout (on a sticky in here) is swapped from the T&C connector (same look of the connector, however, so I doubt it). Anyways, I wanted to drop a heads up to anyone trying to get their MS running with EDIS and this type of coilpack. I used a combo of some updated info about EDIS (rising edge) along with Datman's map with an updated 'required fuel' of 17 ms to get it to fire on my '77 with the stock N/A injectors (all other fuel system parts were stock, too). It fired on first try.
-
I'm pretty sure many of you misunderstood his question. He is not interested in a P90a head nor the hydro lifters. He wants to know if the solid lifters are the same between P90 and N47. Anyhoo, I think he got his answer.
-
You should be able to find it somewhere in the tune/datalog. If you are datalogging the pulsewidth change that means something in the map or a loose sensor is TELLING it to change. If it was some sort of electrical problem with the injectors it would NOT show up in the logs. The logs show what MS thinks it should be running. Recheck all sensors that have an effect. This includes coolant, MAP, TPS, IAT, etc. etc. Try datalogging everything with the key on and engine off. Walk around and jiggle the sensors, the wiring, the grounds, etc.
-
I am pretty sure that all the solid lifter heads use the same solid lifters.
-
Just as a semi-relevant 'cost effective' solution... I have heard of old timer mechanics (on old-timer cars) use a flattened-out cardboard cereal box for a replacement head gasket.
-
Yeah, it could be spark blowout. Too much gap or weak/faulty/poorly grounded coil, etc. I have also seen some maps be too violent in the changes from one field to the next cause an issue or one field isn't way too low on timing or fuel (not tuned yet) that will cause a hysteresis like that. I do notice a very rapid change of fuel pulsewidth. Any way to get the sample rate higher?
-
Any maps or datalogs to post? Are you sure you guys have hot start enrichment on? The few maps I got off of the 'map thread' didn't have it enabled. There were numbers, but the whole ASE system was shut off by an option at the top of the screen. Hot restart requires a decent chunk of fuel and usually not a lot of extra timing (if any; but I've seen quite a bit added by some). Mark
-
Well that expansion ratio (.000069/F) sure makes a lot more sense but I've run and re-run the ratio I came up with from sources using Kelvin. Perhaps I just ain't thinking right.
-
You'd want to use a gear and slide system on the runner setup and bi-directional motor with a worm drive gear on it. That way it's not under as much load and won't have to be working when sitting in a particular state (such as just cruising where most cars spend most of the time).
-
Widebands will work darn near anywhere except in the first 6" after the turbo. They will heat themselves up and be ready before about any engine is ready for closed-loop operation. The only downside to long distance mounting might be a very very slight reaction issue. I've never noticed a problem either tuning or watching the car hum along in closed loop with such a situation. Mark
-
See my above comments in this color.
-
I used to have a TEC III so I'll take a stab at this. It's actually pretty straightforward, but they make it sound more confusing than it needs to be: IOT-Injector Offset Time. This is specified in milliseconds. Whatever this number is is added EVERYWHERE and at ALL TIMES. It is intended to be used to specify an injector response time. Every injector needs a certain amount of time to respond to the "open" command. This is the injector offset time or injector response time, etc. It is usually around 0.7 to 1.25 milliseconds depending on the manufacture of your specific injectors. If you already have a map and you want to change the IOT, you must change the entire base fuel map in the opposite direction by the equal amount to have no change in the map. If it's zero (or whatever) and your car runs fine; leave it be. It doesn't HAVE to accurately reflect the injector pulsewidth; just know that the computer is always adding this amount to the calculated pulsewidth to adapt for the injector's time to respond. TOG-Time on for One Gamma. Specified in milliseconds. Another questionable naming example. They later changed this to UAP; User Adjustable Pulsewidth. Essentially, they try to make use of a "horsepower calculator" when you first set up a new map with all your relevant details to figure out what amount of fuel is going to be required in all situations assuming 100% Volumetric Efficiency. As such, when you plug in a value for TOG, this is the pulsewidth injected at 5.0 volts on the MAP sensor when you leave '100' in the VE table at that rpm and load point. It comes from a rather simplified (IMHO) thought process that an engine flowing twice the air pressure requires twice the fuel. As such they suggest that you should just be able to specify a ratio between load and pulsewidth. Twice the load, twice the pulsewidth. That's what the TOG is; the ratio. You simply tweak it from there with the 'VE Table'. As an example, a common N/A engine is going to use at most, say, 8 ms of fuel in any situation. This will probably be around peak torque and max load (100kpa). This is the TOG number. If this is the case, at 50 kpa it will inject 4ms unless you tweak it with the VE table. It will inject 6ms at 75 kpa, 2ms at 25 kpa and 0ms at 0kpa, etc. You get the idea. The TOG number is the other point needed to determine a fuel 'slope' if you graphed fuel pulsewidth versus load (MAP). The other point is 0ms for 0kpa. TOG is the number at max load. You should determine this as best you can with their 'calculator'. Next, look up the injector response time for your injectors (or estimate) at normal voltage and plug this in for IOT. From there, you get the car warmed up however you can and proceed to tune the VE table with the enrichment maps zeroed. Use a coolant temp and an air temp correction map from another vehicle (even another type of ECU is fine) and make sure they are yielding ZERO % adjustment to the fuel pulsewidth (FPW) at normal conditions. They can add fuel for colder and subtract for hotter, etc. than normal but they shouldn't be doing anything at normal cruising, etc. Once the VE table is right you can go back and do acceleration enrichment, warmup enrichment and startup enrichment, etc (probably in that order). Last step is to turn on EGO correction and keep it's range of authority at +/- 10% or less and do a lot of datalogging. I personally don't like to use TPS/MAP blending and go for straight MAP unless you have a funky ported-to-all-heck N/A car with some lopey cams. You may find a little bit of TPS based fuel accelration is needed to tweak that last bit of drivability, though. By the point you need to mess with that you should have a little bit better feel for the car. I hope that helps. I kinda taught myself most of it, too. The TEC computers are a bit different from most ECU's. They probably have the most in common with the megasquirt. I will keep an eye on the thread or send me a PM if I can be of help. Mark
-
I know it's been a while since my thermodynamics, so how on earth did you come up with that direct relationship? My research showed a different ratio of expansion, but the injectors themselves probably have negative effects from the heat. It may actually be more; quite a bit more maybe? The Coeff. of Volumetric Expansion for gasoline (950 x10^-6 xK^-1) shows an increase of ~21% for gasoline for a 22 degree Celcius (or K) change in temp. (check my math; that doesn't feel right but it does expand 4X faster than water) A rough estimate on anticipating the change in resistance of the copper windings of an injector comes out to about an 8.7% rise (.393% * dT Celcius) in resistance. Considering these are low impedance and probably coupled with a ballast pack, that is probably only a third of the total resistance the ECU sees. This would raise the total resistance by ~2.9%. Given that voltage is pretty much constant, this would drop the current seen by the injectors. I can't really say how that will affect the pulsewidth. And before anyone decides to me, I am just throwing that out there to spur the conversation. Mark
-
'The AFM is your friend" from www.atlanticz.ca in the tech section will tell you how to test the AFM with a multimeter. Even so, it can be tricky to test it.
-
Remote style turbo setup, size piping question
WizardBlack replied to LamboZ's topic in Turbo / Supercharger
Straight answer. Measure the perimeter of the opening of a T3 flange and calculate what diameter piping has the same perimeter. Then fab up your pipe how you need it and have a machine shop press the pipe into the flange and weld it. The beginning and ending of this adapter pipe is going to both be a T3 flange so you know precisely what pipe you need. The alternative is to use same area, but I prefer perimeter for smooth transition. -
Hmm, probably need some more detail. Try going to atlanticz.ca and getting the EFI bible to do some diagnostics. I will tell you that the 280Z doesn't have a normal throttle position sensor with varying voltage. It has an open/close circuit to indicate at very low or closed throttle and another open/close circuit to indicate >~60% throttle (WOT). If you get it to bog at a very specific throttle range ONLY at 2500 rpm then it could be that it's not kicking into the WOT switch or out of the closed switch fast enough and going somewhat lean, etc. It could be a lot of other things, though, since you didn't indicate that you had actually tried anything before posting.
-
Ah OK. That'd count as block sanding then.
-
If I understand correctly, for EDIS it is now realized that Ignition Input Capture should be changed to 'Rising Edge'. Your map posted a few months ago doesn't reflect that and I'd suggest anyone considering using your map as a basis should look into that.
-
I wouldn't buy the "low thread count" junk they sell at auto parts stores for anything critical anyways. Painless Wiring sells extremely nice stuff.
-
IMHO that really would not have done anything for you unless you used a pretty stiff block to to block sand. Otherwise you simply have smooth u-shaped rockers (or they could have been).